A maintenance managaement program is a combination of people, software, and systems, all working towards keeping assets and equipment efficient and reliable.
Facility maintenance departments tailor highly customized maintenance plans (like reactive, preventive, predictive, condition-based, and many more) for various equipment and asset classes.
In the past few decades, maintenance management has come a long way from being a tedious paper-based process to completely automated processes with computerized maintenance management system software (CMMS software.)
This comprehensive blog explains the meaning of maintenance management, explores its core components, compares maintenance management types, reviews modern tools, and presents a practical path to boost uptime, safety, and profitability.
What is maintenance management?
Maintenance management is the organized process of maintaining a company’s assets and resources efficiently, while controlling time and costs to maximize manufacturing productivity.
While often discussed in the context of facilities, manufacturing, and utilities, maintenance management applies wherever asset uptime and reliability are business-critical.
Maintenance management is the systematic process of planning, organizing, and controlling maintenance-related activities and upkeep of physical assets to ensure that they remain effective, safe, and cost-efficient throughout their lifecycle.
Why maintenance management matters:
- Unplanned downtime can devastate production and revenue.
- Well-managed maintenance reduces risk, controls expenses, and enhances safety.
- Maintenance and management synchronization is vital for seamless operations.
- Organizations gain a competitive edge through improved maintenance and operations efficiency.
Facility managers can’t optimize costs, maintenance decisions, or occupant experience without clear visibility.
The first step? Tracking the right KPIs. Here’s a curated list of the most impactful ones used by top-performing FMs.
Key objectives of maintenance management
Maintenance management is a vital part of operations management and plays a crucial role in operations management by ensuring assets are reliable, efficient, and cost-effective.
To achieve this, maintenance programs focus on a set of key objectives designed to maximize equipment performance. They are:
- Maximizing asset reliability:
Ensure equipment operates consistently with minimal unexpected failures, enhancing operational stability, reducing downtime, and supporting production targets.
- Cost optimization:
Strategically manage all maintenance expenses, including labor and materials, to avoid costly emergency repairs and maximize the return on maintenance investments.
- Lifecycle extension:
Implement proactive maintenance practices that preserve asset health, extending useful life and deferring expensive replacements to optimize capital utilization.
- Efficiency improvement:
Optimize maintenance workflows and resource allocation to reduce delays and redundancies, improving productivity and supporting uninterrupted operations.
- Safety and compliance:
Maintain assets to meet safety regulations and industry standards, minimizing workplace hazards and legal risks while fostering a culture of safety.
Maintenance management v/s asset management
The key difference between maintenance management and asset management is:
- Enterprise asset management (EAM) is an overarching strategy that relies on data insights to maximize the efficiency of company resources to drive operational efficiency, reduce associated costs, and increase RoI.
- In contrast, maintenance management only deals with tangible assets and focuses on keeping their performance optimal, increase equipment uptime and productive hours. It helps enterprises streamline processes for Maintenance, Repair, and Operations/Overhaul (MRO) for assets and equipment.
Frustrated by delayed repairs and complicated compliance?
Facilio streamlines assignments, tracking, and audits. See maintenance simplified.
Get a demoTypes of maintenance management
Businesses can utilize one of these four types of maintenance management techniques, either separately or in conjunction, to build an efficient and cost-effective maintenance strategy:
- Reactive maintenance (also known as corrective or breakdown maintenance)
- Preventive maintenance (also called planned preventive maintenance or preventative maintenance)
- Predictive maintenance
- Reliability-centered maintenance
Reactive maintenance (RM)
- Definition: Maintenance activities performed only after equipment has failed or broken down.
- Suitable for: Low-cost, non-critical assets where downtime does not severely impact operations or safety.
- Example: Imagine a small office fan that stops working occasionally. Since it’s inexpensive and doesn’t affect vital operations, you replace or fix it only after failure.
- Pros: Minimal initial planning; no recurring maintenance costs.
- Cons: High risk of costly, unscheduled outages; poor for essential assets.
Preventative maintenance (PM)
- Definition: Regular, scheduled maintenance performed at fixed intervals based on time, operating hours, or manufacturer recommendations.
- Suitable for: Critical equipment whose failure could cause expensive downtime, safety issues, or compliance problems.
- Example: A manufacturing plant schedules oil changes on conveyor motors every 1,000 operating hours to avoid breakdowns and maintain efficiency.
- Pros: Reduces unexpected failures; prolongs asset life; good for regulatory compliance.
- Cons: Potential for over-maintenance; resource-intensive without smart scheduling.
PM maintenance schedules record the original equipment manufacturer's (OEM) recommendations on the number of operational hours after which the vehicle will need an oil change.
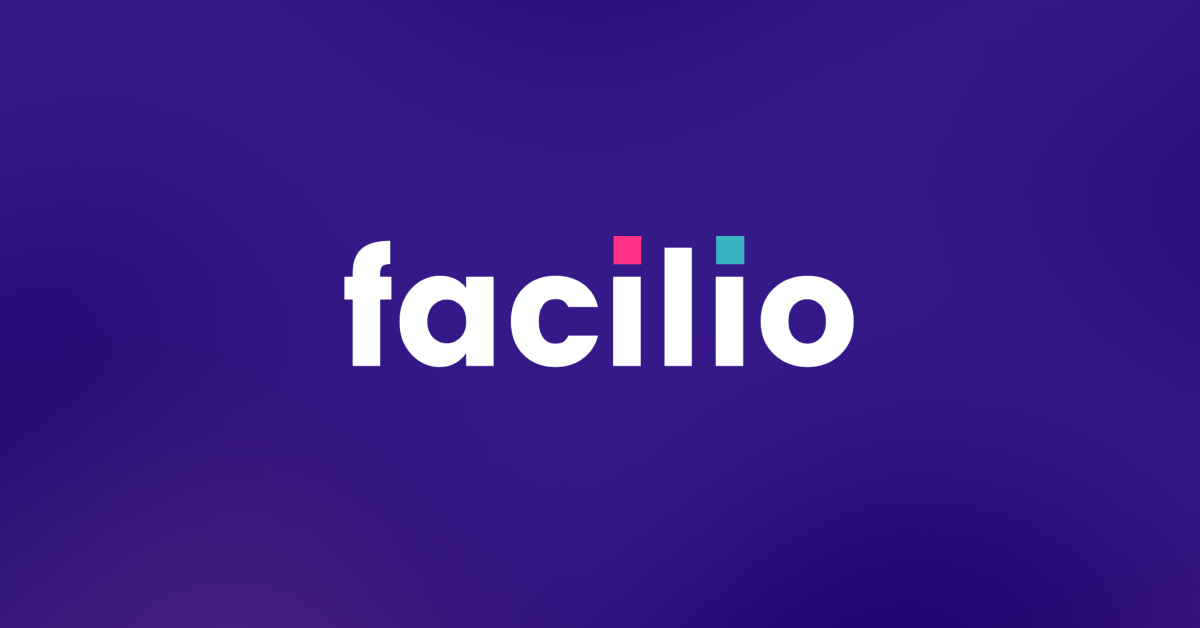
Predictive maintenance (PdM)
- Definition: Maintenance triggered by real-time data analysis from sensors that predict when a failure might occur, allowing just-in-time interventions.
- Suitable for: High-value, critical equipment where downtime is very costly, and predictive technology (IoT sensors, analytics) is available.
- Example: An oil refinery uses vibration sensors on pumps to detect early signs of wear; maintenance is scheduled only when sensor data indicate potential failure, avoiding unnecessary servicing.
- Pros: Optimized maintenance; reduces unnecessary work; improves maintenance and operations efficiency.
- Cons: Higher upfront technology investment; requires skilled staff and reliable data.
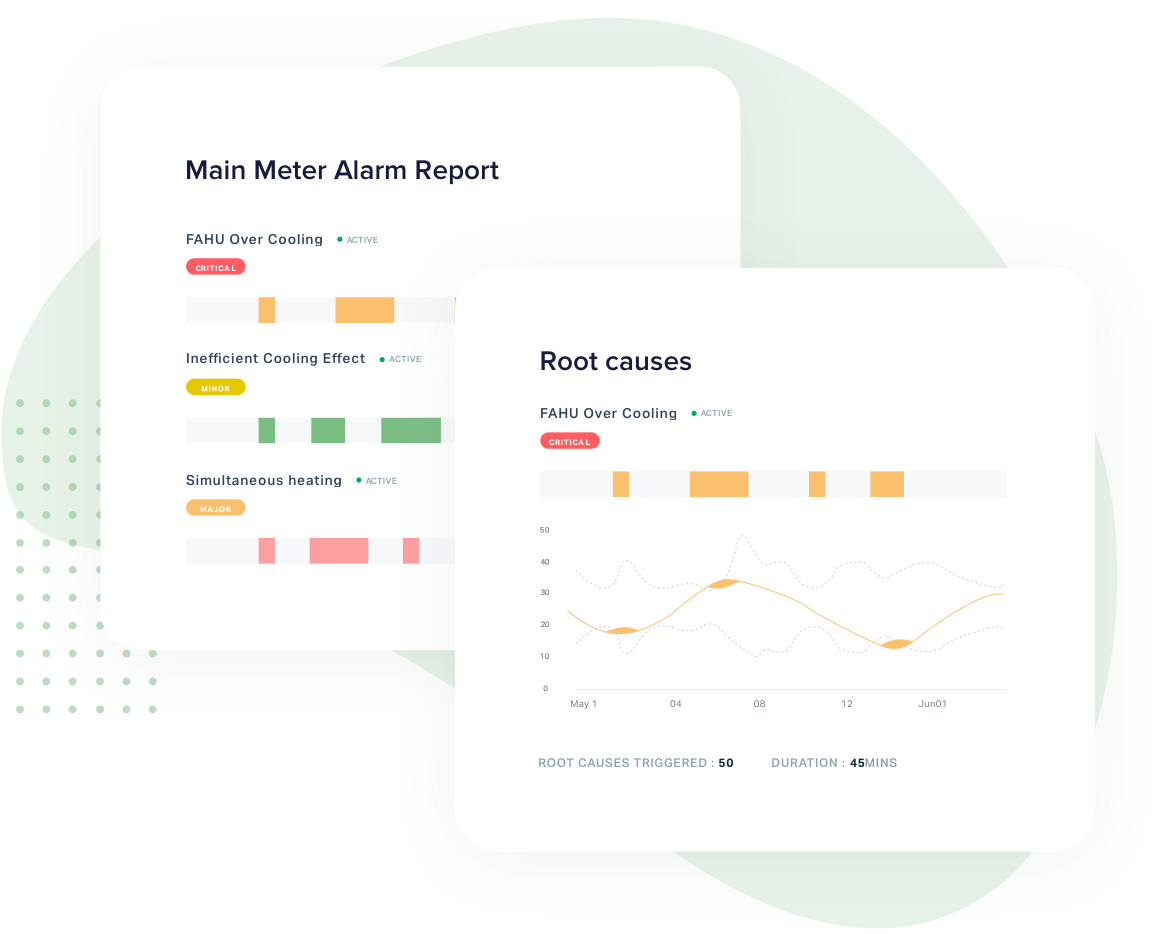
Condition-Based Maintenance (CBM)
- Definition: Maintenance is performed when specific monitored asset conditions (such as vibration, temperature, noise, or wear levels) reach predefined thresholds.
- Suitable for: Rotating machinery, HVAC systems, and vehicles, when there are reliable, measurable indicators that effectively reflect equipment health
- Example: HVAC systems equipped with temperature and airflow sensors trigger maintenance alerts only when airflow drops below an acceptable level, preventing unnecessary checks.
- Pros: Focuses resources on actual needs; prevents premature or late interventions.
- Cons: Requires monitoring equipment and analysis.
Each maintenance strategy type can be leveraged to tackle different aspects of asset failure. To implement the right strategy for your operations, it's crucial to understand the different types of maintenance and how each one contributes to overall asset reliability and efficiency.
Benefits of maintenance management
According to Finances Online, 34% of unscheduled equipment downtime is caused by aging equipment. Mechanical failure accounts for another 20%. Maintenance management, when executed effectively, can significantly reduce these risks.
Let's look at some common benefits of maintenance management in operations management:
1. Improved employee and asset productivity
In industries like manufacturing or retail, unexpected equipment failures threaten employee/occupant/facility safety, adding to a direct negative impact on the bottom line due to operational disruptions.
In the case of office spaces, improper maintenance results in insufficient lighting, uncomfortable heating, ventilation, and air conditioning (HVAC), and multiple electrical and fire hazards that disturb operations and keep employees from being as productive as they could be.
Proactive maintenance management helps identify faults and fix them before they break down, ensuring every human and machine in your facility is safe, healthy, and productive.
2. Reduced asset maintenance cost
Emergency maintenance activities incur high costs, especially if you require a spare part for your equipment in a run-to-failure maintenance scenario.
If it's not readily available in your inventory, the cost of shipping a spare part with fast deliveries is higher than that of standard deliveries. Also, operations are disrupted till the faulty part is replaced, inviting sizable losses for businesses.
Regular maintenance maximizes asset lifetimes by keeping them running the way manufacturers intended, reducing the chance of unexpected failures and costly downtimes.
3. Improved asset lifecycles & uptime
Facility managers (FM) and O&M teams rely on maintenance metrics KPIs and metrics like mean-time between failure (MTBF), mean-time to repair (MTR), and Remaining Useful Life (RUL) to track changes in the safety and performance of tangible assets over time.
In effective maintenance management, these metrics are tracked and analyzed using a maintenance management software to ensure each asset operates as intended, delivers maximum ROI, and reaches its full lifespan, minimizing the risk of premature replacement.
4. Better safety & compliance
Effective maintenance management plays a critical role in upholding workplace safety and regulatory compliance.
By systematically identifying and addressing hazards—such as equipment malfunctions, structural wear, or environmental risks—before they escalate, organizations significantly reduce the likelihood of accidents, legal liabilities, or non-compliance fines.
A disciplined approach to maintenance ensures that safety protocols are consistently enforced, inspections are conducted on schedule, and every asset meets the standards required by industry regulations.
5. Data-driven decisions
A mature maintenance management strategy is grounded in accurate data—collected over time through logs, inspections, and performance tracking.
This data provides valuable insight into recurring failure modes, asset performance trends, and lifecycle costs.
By analyzing these patterns, maintenance leaders can make informed decisions about repair vs. replace scenarios, maintenance schedules, and capital allocation. Ultimately, it supports a culture of continuous improvement and long-term asset optimization.
Suggested read:
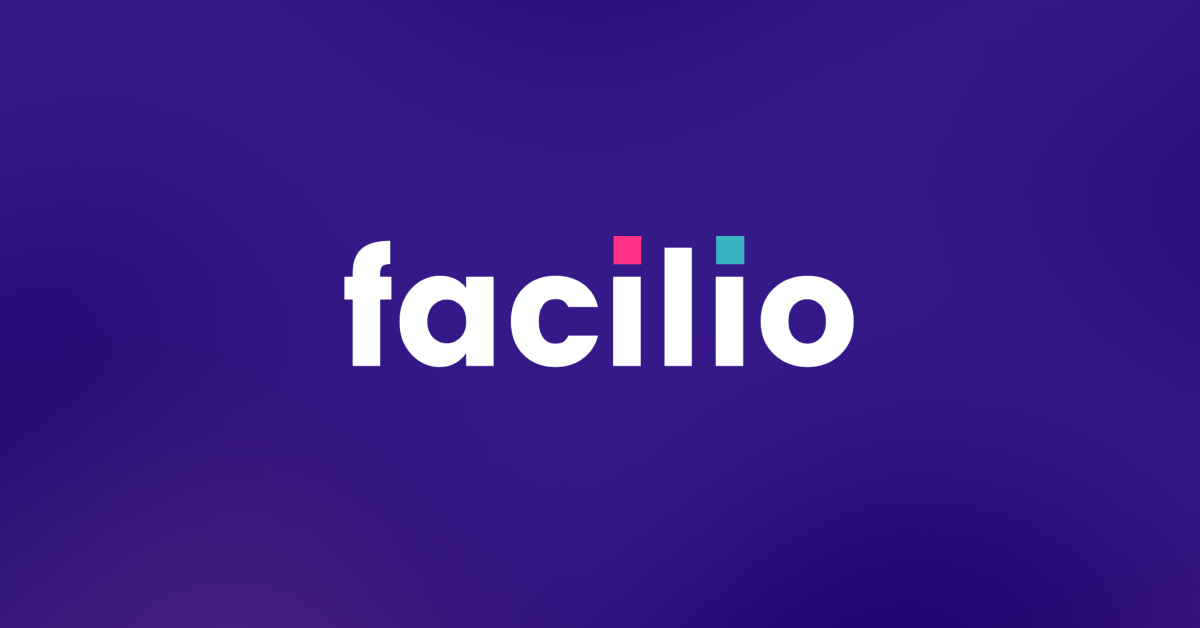
Real-world maintenance management examples by industry
Maintenance management meaning changes subtly by industry, but its core principles remain consistent.
It's essential for any business managing physical assets, especially in a post-COVID era where safety, health, and energy compliance are critical to controlling costs and improving operational efficiency.
Here’s how different sectors apply maintenance management techniques:
Manufacturing
Manufacturing plants use predictive techniques to monitor machine health, detect failure patterns, and anticipate breakdowns. This allows maintenance teams to plan interventions without disrupting production.
Construction
Heavy machinery like cranes, drills, and concrete mixers are maintained on a regular schedule, with condition checks to catch early wear. This reduces the risk of sudden failures that could halt progress.
Commercial & Office Buildings
Systems like HVAC, elevators, and lighting are maintained based on usage patterns and occupancy data. Maintenance is scheduled during off-hours to reduce disruption. This enhances occupant comfort and safety, and lowers energy consumption.
Healthcare Facilities
Critical assets such as imaging equipment, life-support systems, and sterilizers are maintained to maximize uptime and patient safety. Maintenance strategies are aligned with compliance and accreditation standards.
Maintenance management tools & technologies
Recent advancements in maintenance management solutions, especially the rise of CMMS tools, have fundamentally reshaped how organizations manage and optimize asset performance.
What is maintenance management software?
Today’s maintenance management strategies are powered by a toolbox of advanced tech that enables teams to work smarter, faster, and with greater precision.
- CMMS platforms: A centralized digital platform that automates, tracks, and improves all key maintenance management activities, often across multiple sites or portfolios.
- IoT and Smart Sensors: Real-time monitoring for maximum predictive accuracy.
- Mobile Devices: Technicians access service histories, step-by-step guides, and update records from the field, accelerating response times.
- Data Analytics: Managers spot bottlenecks, forecast failures, and optimize schedules, all from a single dashboard.
- AI & Machine Learning: Forecast equipment failure, optimize resource scheduling.
Effective maintenance management is not just about keeping things running—it’s a strategic driver of business sustainability, efficiency, and competitiveness.
The right combination of maintenance management techniques, digital tools, and process alignment enables organizations to avoid costly downtime, extend asset lifespans, and empower teams for consistent operational excellence.
A unified maintenance management solution like a CMMS software, makes these goals achievable at scale, automating the full asset maintenance and management lifecycle for leading maintenance and operations efficiency.
FAQs
What does maintenance management mean?
Maintenance management meaning can shift slightly depending on the industry, but the foundation stays the same: it’s the process of planning, organizing, and controlling the upkeep of assets to ensure reliability, safety, and cost-efficiency throughout their lifecycle.
What are the 4 areas of maintenance management?
The four key areas of maintenance management are:
- Planning and scheduling of maintenance activities
- Execution and supervision of maintenance tasks
- Monitoring asset condition and maintenance performance
- Continuous improvement based on data and analysis
What are the types of maintenance management?
The four common maintenance management strategies are:
- Predictive maintenance: Uses condition-monitoring tools and data to forecast failures.
- Proactive maintenance: Targets root causes to stop failures before they start.
- Preventive maintenance: Scheduled tasks performed to avoid asset breakdowns.
- Reactive maintenance: Responding to equipment failures after they occur.
What does a maintenance manager do?
A maintenance manager oversees the upkeep of buildings, systems, and machinery. They plan maintenance schedules, manage technician teams, monitor compliance with safety rules, and handle maintenance budgets and spare parts inventory.
What are the basics of maintenance management?
The basics of maintenance management consist of the following steps:
- List assets and critical systems
- Define maintenance strategy and how often to perform it
- Assign teams and responsibilities
- Track tasks through work orders
- Record every maintenance action
- Use reports to improve over time
What are the 4 P’s of maintenance?
A helpful approach to maintenance includes four levels called the 4 P’s of maintenance:
- Presentation: Maintaining cleanliness and visual standards
- Protection: Preventing damage and premature wear
- Preparation: Keeping tools and systems ready to operate
- Partnership: Working together across teams to ensure smooth maintenance delivery
What are the 5 basic functions of maintenance?
The 5 core functions of maintenance management are:
- Preventive maintenance to reduce failure risk
- Corrective maintenance for fixing issues
- Inspections to catch problems early
- Support services for residents or users
- Emergency repairs for unexpected breakdowns