Featured Building Operations & Maintenance
What Is A Bathtub Curve? How to Measure Asset Reliability
Most manufacturing plants and industrial facilities see failure as a function of time.
Are assets likely to fail closer to the end of their lifecycles? Not always.
The truth is that they can also fail during their useful life or even before that. So, how do you make sense of asset failure probability?
With bathtub curve — a hazard and reliability function that predicts asset failure rate. Maintenance managers and technicians also rely on maintenance management software to detect failures, identify root causes, and prevent such failures from happening.
This article walks you through bathtub curve analysis basics and how to increase an asset’s useful life or availability with it.
What is a bathtub curve?
A bathtub curve visually represents the failure rate of one or more assets by plotting their failure occurrences over time. The name bathtub comes from the curve resembling a bathtub’s longitudinal section.
A bathtub curve has three stages:
- Infant mortality period refers to the period when you start using a product for the first time.
- Normal life period starts after the initial operation period and is also known as the useful life period.
- Wear-out period refers to the time when assets start deteriorating after a certain usage period.
The bathtub graph helps you measure the reliability of assets and adopt the right run-to-failure maintenance management strategy.
Asset reliability specialists consider the bathtub curve as one of the most important graphical representations of chances of failure throughout an asset life cycle — let’s see why.
What is the purpose of a bathtub curve?
A bathtub curve is key to eliminating asset failure. Companies leverage bathtub curve analysis to set performance expectations of assets throughout their life cycle.
For example, you can use this curve to eliminate the initial failure and get rid of ‘dead on arrival’ products. Discovering defects during the initial period helps you get assets replaced under manufacturer warranty.
When assets experience failure in the normal period, that’s often because of random events. Bathtub curve analysis lets you predict those and asset breakdowns during the wear-out period as well.
These predictions help you adopt predictive maintenance techniques early on and keep assets with higher failure rates in tip-top shape.
Looking for a modern, flexible CMMS that scales with your business?
Stages of the bathtub curve
Efficient asset lifecycle management requires you to stay on top of asset failures—which you can do only if you know when assets are likely to fail.
That’s why it’s key to understand the three stages of the bathtub curve i.e. infant mortality, normal life, and wear-out period.
1. Infant Mortality Period
The early failure period or infant mortality period starts as you use a product or asset for the first time.
Common causes of asset failure at this stage include manufacturing defects, installation errors, insufficient components, design flaws, and incorrect start-up processes.
These causes often lead to a higher rate of failure during a short period—hence the name infant mortality. This period often starts with a high failure occurrence before the failure rate decreases and eventually plateaus.
So, what can you do to minimize asset failure during the infant mortality period?
Check out the common maintenance strategies to prevent infant mortality equipment failures.
- Perform preliminary tests or purging using sensors or automatic technologies. These tests will aid you to discard defective equipment or send them for repair or replacement.
- Run acceptance and reliability tests to reevaluate equipment and check replaced parts of an asset. You can also run these tests every time you change design, processes, or tools.
- Test young assets under stress using accelerated and burn-in tests. Both of these tests help you understand how assets perform in more demanding or stressful conditions than usual.
Once you run these tests, you’ll have a clear idea of whether assets are likely to fail.
The best way to prevent asset failure during infant mortality is to use reactive or breakdown maintenance — a maintenance strategy that restores normal operating conditions when assets break down. Another way is to use warranties and request asset repairs from the manufacturer.
2. Normal life period
The useful asset life or normal life period starts after the initial operation. Most assets spend the majority of their operational life in this state.
Since there’s a constant chance of failure during this time, operators also recognize this period as the constant failure rate period.
The asset failure rate at this stage is typically low yet constant. Most of these failures happen because of normal wear, human errors, overload, accidental breakdowns, or increased asset usage.
External environmental factors also influence useful asset life failures to some extent.
So, how do you deal with this?
Following a preventive maintenance checklist and operations & maintenance (O&M) manual can help perform periodic maintenance jobs.
While preventive maintenance is the most appropriate strategy for assets in this stage, you can also leverage predictive maintenance to maximize asset life.
3. Wear-out period
As assets deteriorate over time, they enter the final stage of the asset lifecycle, known as the wear-out or end-of-life period. The upward sloping of the bathtub curve at this stage is because of the increasing failure rate trend.
Not all assets reach the wear-out stage. For example, you may retire tech assets when new technology becomes available.
End-of-life failures are often predictable. Some manufacturers specify the useful life of assets and parts in their documentation.
Manufacturers sometimes design parts in a way so that they reach the wear-out period and enable facility managers to reset the bathtub curve.
Handling late-life assets becomes easier when you have a preventive maintenance plan in place. These plans help you extend assets’ useful life and ensure their reliability.
Ideally, you should revise the preventive maintenance measures as the failure rate goes up. Consider keeping the failure rate close to that of the normal life period.
Check out these preventive maintenance strategies for minimizing wear-out failures.
- Plan periodic maintenance checks for thorough asset inspection and prioritize assets that are more likely to experience wear.
- Repair what you can because preventive replacements cost less than asset replacements. Replacements sometimes come with extended warranties, making them the best way to increase assets’ useful life.
- Maintain external conditions like temperature and air humidity level to keep assets in the best working conditions.
- Use manufacturer-approved spare parts instead of unoriginal ones to increase asset life.
Suggested read: What is Facilities Condition Assessment?
How to calculate tub curve
Mean time between failures (MTBF) is a common metric used to analyze failure rate. It defines the average time gap between system breakdowns.
You can use MTBF to find out the reliability, safety, and performance of complex assets. MTBF equals the inverse of the failure rate when the bathtub curve has a flat bottom.
MTBF can also be expressed as the sum of mean time to failure (MTTF) and mean time to repair (MTTR).
MTTF represents the total expected asset lifetime before a device or product needs replacement. Organizations calculate MTTF by tracking the total operational hours of similar assets over a period of time. This metric helps predict the useful life of non-repairable assets.
MTTR tells you the amount of time you need to repair assets and restore their functionality. It can be helpful for understanding if you’re well-equipped to asset issues. Companies generally rely on a computerized maintenance management system (CMMS) and their maintenance team to shorten MTTR.
Time to look at an example of MTBF. Imagine, one of your assets runs for 24 hours every day and has an MTBF of 3.5 million hours. Below is the failure rate calculation when the bathtub curve has a flat bottom.
MTBF = 1/failure rate
Failure rate = 1/MTBF = 1/3,500,000 hours
Failure rate = 0.000000286 failures/hour
Failure rate = 0.000286 failures/1000 hours
Failure rate = 0.0286%/1000 hours (considering total 8,760 hours in a year)
Failure rate = 0.25%/year
3.5 million hours equal 400 years. You can’t expect assets to be operational that long as they’ll wear out way before that.
However, the constant failure rate will be 0.025% per year during the normal life period. As you see, MTBF only projects normal lifetime failures and can be greater than wear-out time.
What does the bathtub curve illustrate about reliability?
A bathtub curve is an excellent tool for measuring hazard function or asset failure risk levels. It projects the failure rates of products over their lifetime.
A deeper understanding of the reasons behind failure helps you adopt the right preventive and predictive maintenance strategies.
Next, you need to decide whether to repair or replace the asset based on the root causes. Companies looking to minimize wear-out often modernize assets right before the wear-out period.
They do so because the cost of repair is often lower than the cost of new assets. These resets push assets to the infant mortality period, meaning the asset is more likely to fail.
However, these failures will decrease with time, meaning the bathtub curve cycle restarts.
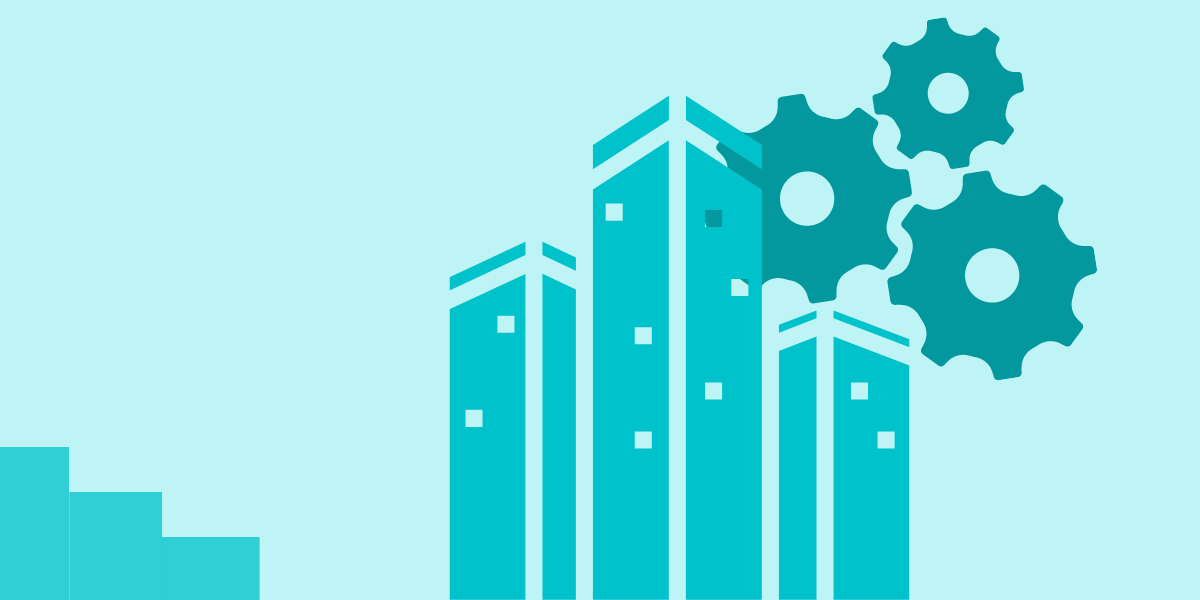
How to improve Remaining Useful Life (RUL) of an asset using bathtub curve analysis
Let’s look at the different ways in which a bathtub curve analysis helps you boost an asset’s RUL.
- Gain prognostic insights. With bathtub curve analysis, you know what assets need system inspections and advanced condition monitoring — both key to preventing asset failure.
- Manage inventory better. When you know what assets are likely to fail, you can acquire spare parts ahead of time to keep assets operational.
- Claim warranties. Bathtub curve analysis shows you what group of products are likely to experience failure over a period of time. This knowledge can be crucial for claiming warranties for expensive and critical assets.
Investigating what affects the curve and its inflection points is key to gaining operational insights. Since any formula has certain assumptions, it’s better to use innovative technologies for more accurate predictions.
Consider using a CMMS solution like Facilio to get 360-degree asset performance insights across facilities and optimize your maintenance strategy.
Schedule a demo to see how Facilio helps you optimize asset health with data-driven insights.