Preventive Maintenance Scheduling: A Simple Guide
A preventive maintenance schedule is a plan for keeping your equipment, machines, and facilities in top shape.
The idea is to perform regular check-ups and maintenance tasks to avoid any unexpected equipment breakdowns or issues. This helps keep facilities humming while also prolonging equipment lifespans.
So, what kind of tasks are involved in preventive maintenance (PM)?
It could be anything from cleaning and lubricating, to replacing parts, or even updating software. The specifics will depend on the type of equipment you have and how often it's used.
Some tasks might need to be done daily, while others might only need to be done monthly or yearly. The important thing is to have a plan in place, so you know what needs to be done and when - and this is called preventive maintenance scheduling.
1.Time-based: performed at regular intervals
2. Usage-based: based on equipment usage
3. Condition-based: maintenance scheduled based on equipment condition
4. Predictive: uses advanced technologies to predict when maintenance is required
The type of PM performed on each asset depends on its needs, operational impact, repair/replacement costs, and more such factors. We'll talk more about these in the next section.
The bottom line is that any maintenance that is planned ahead of time is considered preventive maintenance.
Suggested read:
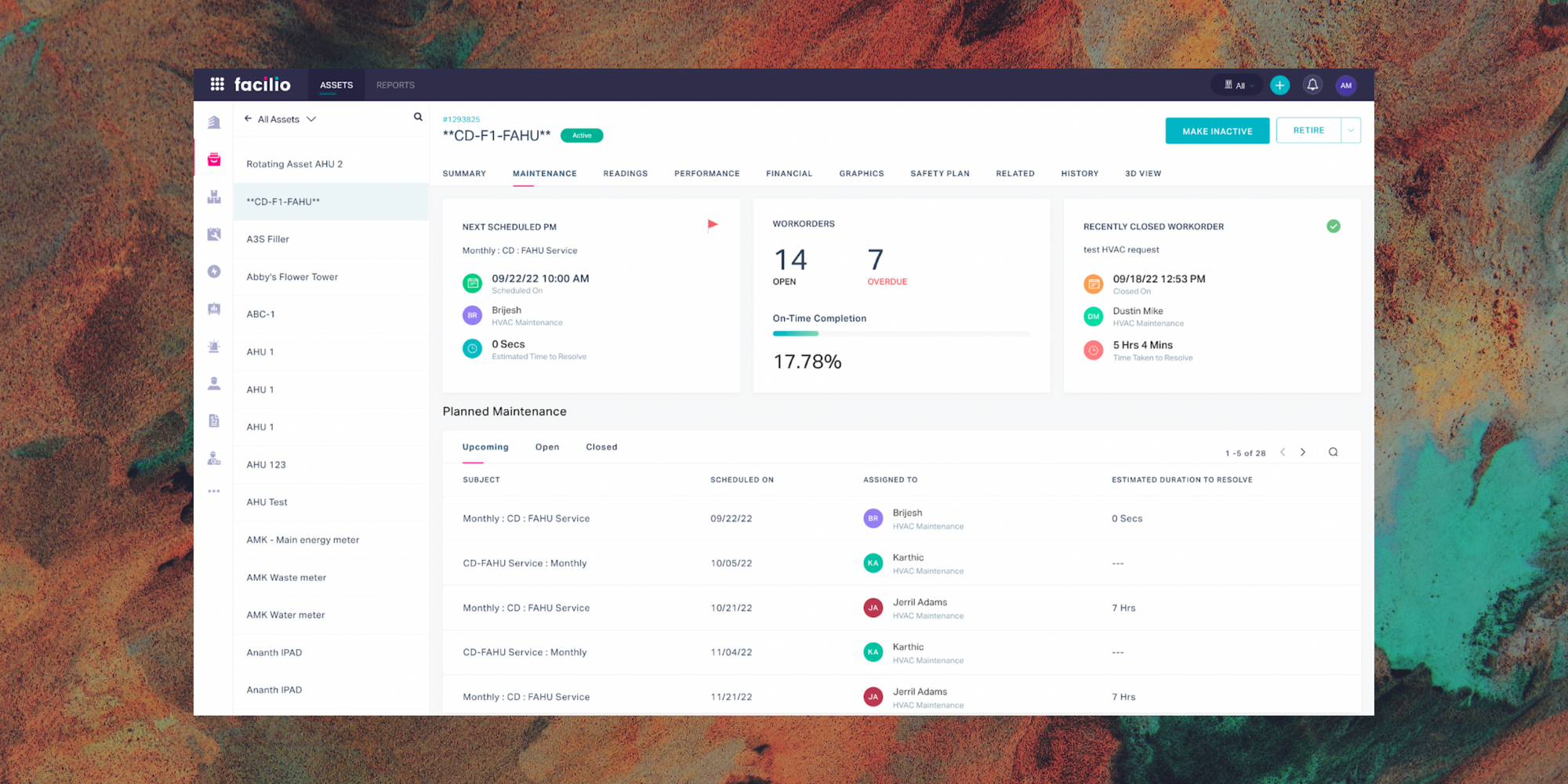
6 steps to create a preventive maintenance schedule
Here are the steps to create a preventive maintenance schedule:
- Identify the equipment that needs preventive maintenance: This includes machines, tools, vehicles, and other assets that are critical to your operations and need regular maintenance to remain in good working condition.
- Determine the tasks that need to be performed for each piece of equipment: This may include tasks such as lubrication, cleaning, calibration, and inspection packed neatly into a PM checklist.
- Establish a regular schedule for performing the maintenance tasks: This should take into account the equipment's usage, operating conditions, and O&M manual and the frequency at which each task should be performed ( daily, weekly, monthly, or annually.)
- Prioritize maintenance for important assets: Prioritize tasks based on their impact on safety, reliability, production efficiency, and business impact.
- Assign responsibility for each maintenance task to a specific individual or team: This will ensure that the tasks are completed on time and that the equipment is properly maintained.
- Record the maintenance activities in a log or database: This will allow you to track the performance of the equipment, identify trends, and make any necessary adjustments to the maintenance schedule.
- Monitor the effectiveness of the preventive maintenance program and make adjustments as needed: This may include modifying the schedule, adding new tasks, or making changes to the personnel responsible for performing the maintenance.
The key to creating an effective preventive maintenance schedule is to regularly inspect and maintain equipment to prevent potential problems from arising.
That's a lot of data to keep track of with paper or spreadsheet based processes, isn't it?
This is where a computerized maintenance management system (CMMS) steps in—turning complex PM scheduling into a streamlined, repeatable process.
How to schedule PM tasks using a CMMS?
A CMMS is purpose-built software designed to simplify, automate, and bring structure to every aspect of maintenance operations—especially preventive maintenance scheduling.
Here's how PM scheduling works with a CMMS:
- Define the maintenance tasks, like inspections, cleaning, and part replacements.
- Input the task information into the CMMS, including details like location, who's responsible, and materials needed.
- Set up automatic reminders to make sure tasks are completed on time.
- Use the CMMS to schedule maintenance, taking into account usage, availability, and other factors.
- Keep track of progress with the CMMS and make adjustments as needed.
- Generate reports on maintenance activities to identify areas for improvement.
Benefits of preventive maintenance scheduling
There are several benefits to implementing a preventive maintenance schedule, some common ones include:
- Increased equipment reliability and availability
- Improved equipment performance
- Reduced repair costs
- Improved safety
- Enhanced customer satisfaction
Suggested read:
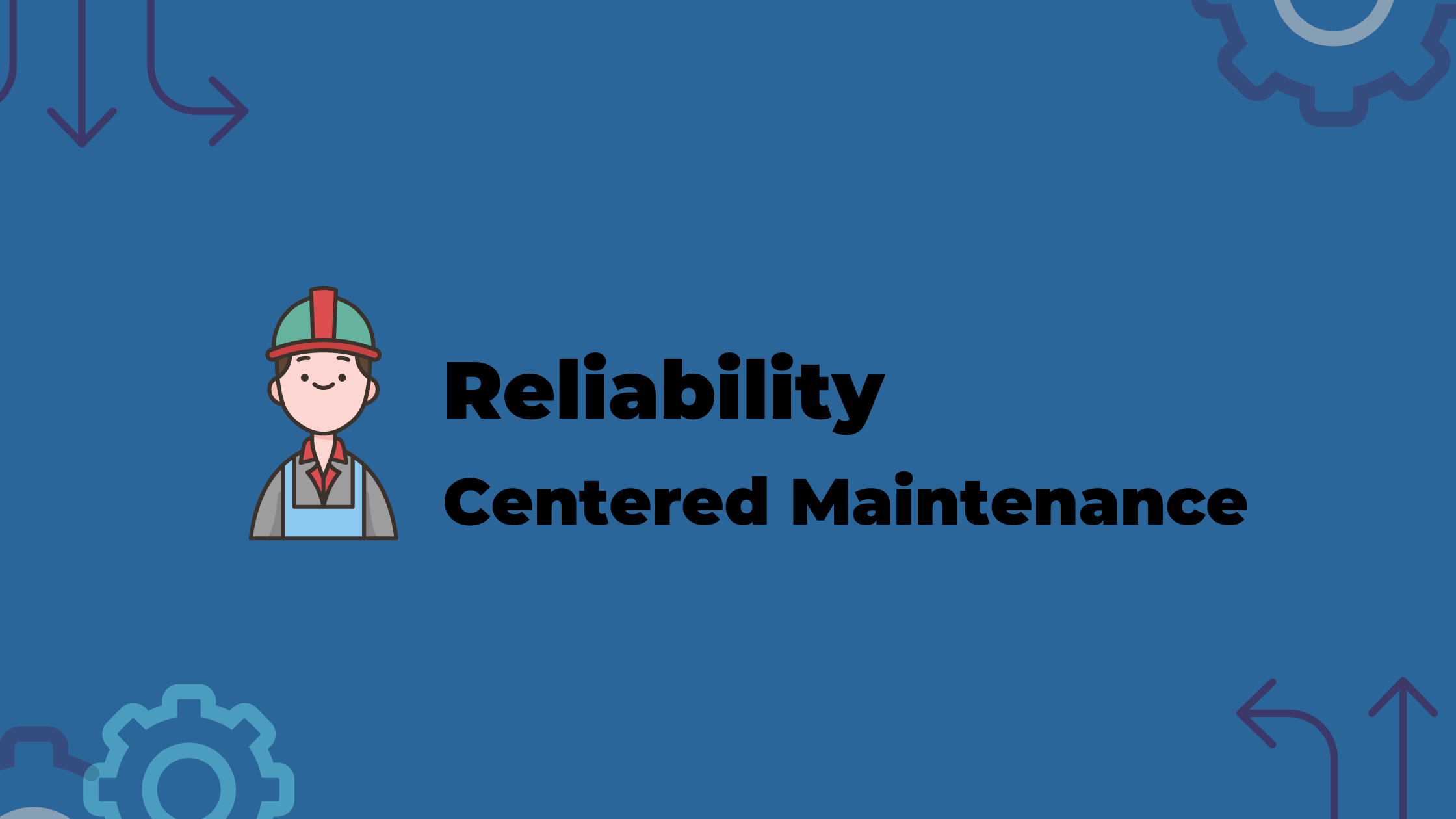
What are some examples of preventive maintenance tasks?
Anything from repairs and replacements to cleaning and lubrication can be a PM task, depending on equipment needs. Here are some examples of PM tasks:
- Lubricating moving parts on a machine to reduce friction and wear
- Cleaning and adjusting the belts and pulleys on a conveyor system
- Checking the tire pressure and tread on a company vehicle
- Calibrating a temperature gauge to ensure accurate readings
- Inspecting the condition of a machine's electrical components
- Testing the fire extinguishers and sprinkler systems in a building
Suggested read:
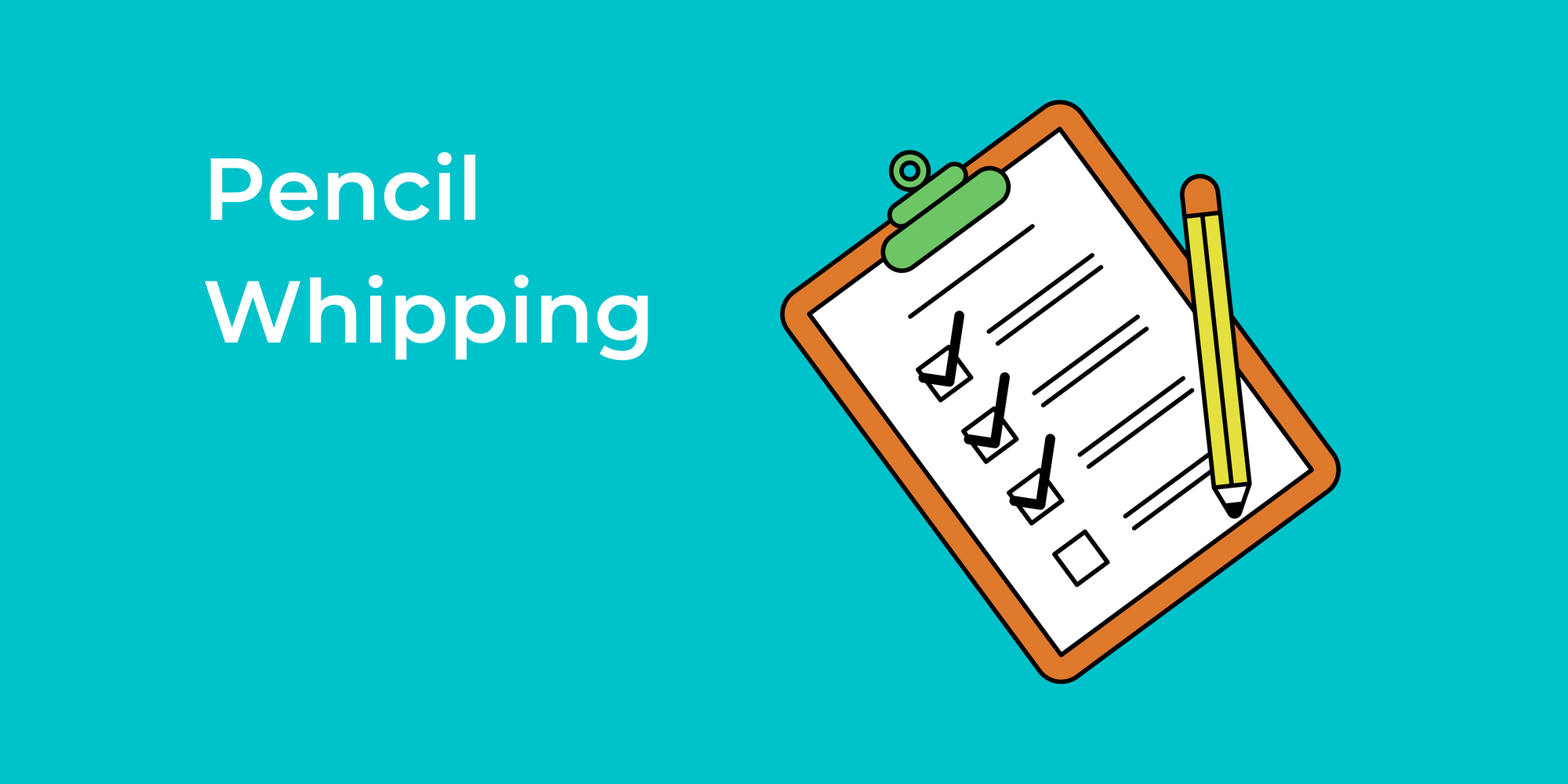
Why choosing the right CMMS is important for effective maintenance scheduling
Building a preventive maintenance schedule is just the beginning. Ensuring it works—across sites, teams, and asset types—requires a platform that delivers consistency, visibility, and automation at scale. And that all comes down to choosing the right CMMS.
A modern CMMS should let you:
- Centralize scheduling across buildings, teams, and systems
- Auto-generate PM tasks triggered by time, usage, or condition thresholds
- Assign and execute work seamlessly with mobile checklists and asset histories
- Track real-time performance metrics like PM compliance and MTBF
- Maintain full audit trails for inspections, repairs, and regulatory readiness
But not all CMMS platforms are built for today’s operational complexity.
Facilio takes preventive maintenance further—by making it dynamic, data-driven, and built to scale.
Unlike legacy tools that record tasks after completion, Facilio’s Connected CMMS continuously adapts your schedule based on asset behavior, technician bandwidth, and shifting priorities. You’re not locked into static frequencies—you’re optimizing in real time.
With Facilio, maintenance scheduling becomes a live, responsive system—helping teams reduce unnecessary work, stay proactive, and maintain control across every site they manage.
What Facilio Enables—and Why It Matters
1. Auto-scheduling based on time, usage, or condition
→ No task is missed, delayed, or duplicated—teams stay ahead of failures, not behind them.
2. Centralized calendar for all PM activities
→ One source of truth across buildings and teams—eliminates silos and last-minute confusion.
3. Technician assignments with mobile checklists
→ Faster task execution, fewer errors, and more accountability on the ground.
4. Real-time tracking of PM compliance and work completion
→ Leaders know exactly what’s done, what’s pending, and where support is needed.
5. Dynamic adjustment of task frequency based on asset performance
→ No more over-servicing or wasting resources—PM effort is aligned with actual need.
6. Smart parts and inventory linking
→ Techs show up prepared—no delays due to missing parts or approvals.
7. Full audit trail with digital logs and timestamps
→ Built-in compliance for safety, insurance, and regulatory reporting—without extra admin effort.
8. Cross-site visibility for multi-location operations
→ Standardize schedules, spot inefficiencies, and compare performance across the portfolio
How Al Fajer Standardized Preventive Maintenance Scheduling Across 300+ Buildings
Al Fajer Group, a large facilities operator managing hundreds of buildings, made the shift from fragmented, manual scheduling to a fully digitized preventive maintenance program using Facilio’s CMMS.
Here’s what changed when Al Fajer leveraged Facilio for their miantenance management:
- 80+ preventive maintenance schedules standardized and automated across 300+ sites
- 13% increase in workforce productivity through smarter scheduling and technician enablement
- Significant reduction in unplanned outages, improving SLA compliance across high-demand assets
What made the difference wasn’t just better planning—Facilio's CMMS was a platform that brought structure, automation, and real-time visibility to preventive maintenance at scale.
Schedule for Reliability, Not Just Routine
Preventive maintenance isn’t just a best practice—it’s a strategic advantage. But to get results, teams need more than a list of tasks. They need a schedule that’s clear, consistent, and built to scale.
When every maintenance schedule is planned right, executed efficiently, and tracked automatically, maintenance stops being reactive and becomes a driver of uptime, cost control, and long-term asset health.
That’s exactly where the CMMS you choose makes all the difference.
The system you choose determines whether your team is stuck recording work after the fact—or actually driving results. Most legacy CMMS platforms were built to log activity, not lead it. They weren’t designed to automate schedules, assign tasks, or support dynamic portfolios.
Today’s facilities are fast-moving, complex, and under pressure to deliver safe, efficient, and healthy environments at scale. You need a CMMS that’s built for this reality—not yesterday’s.
Facilio’s connected CMMS is a reimagined approach to CMMS, which helps you manage preventive maintenance like clockwork, across every building, team, and system.
Ready to modernize your maintenance scheduling?
Learn how Facilio helps you turn it into a system that delivers measurable results.
Explore Facilio's Connected CMMSFAQs
1. What is a preventive maintenance schedule?
A preventive maintenance schedule is a structured plan that outlines when and how often equipment should be serviced to avoid unexpected failures.
It typically includes recurring tasks like inspections, cleanings, and part replacements triggered by time or usage.
2. What are the key aspects of a preventive maintenance schedule?
To be effective, a preventive maintenance schedule should be:
- Based on appropriate timing and frequency using equipment usage, OEM recommendations, or failure history
- Prioritized to focus on high-risk and high-impact assets that affect safety or operations
- Planned with the right resources like technicians, tools, and spare parts availability
- Aligned with daily operations to avoid disrupting production or occupant activity
- Flexible enough to adjust as asset conditions, workloads, or priorities change
3. What are the main benefits of a preventive maintenance schedule?
A structured PM schedule helps you move from reactive to reliable. These benefits directly impact cost, uptime, and safety:
- Reduced downtime: Prevents failures before they happen, keeping equipment online and operations smooth.
- Cost savings: Avoids costly emergency repairs and optimizes labor and parts usage.
- Extended equipment lifespan: Regular upkeep helps assets perform efficiently over longer cycles.
- Improved safety: Proactively addresses potential hazards, supporting a safer work environment.
- Enhanced sustainability: Reduces waste and over-servicing by maintaining only when needed.
4. How to set up a preventive maintenance schedule?
There are six key steps in setting up an effective and scalable preventive maintenance schedule:
- List all critical assets across your facility.
- Define the maintenance tasks required for each asset.
- Set service intervals based on time, usage, or asset condition.
- Assign technicians, tools, and spare parts in advance.
- Use a CMMS to automate scheduling, alerts, and task tracking.
- Review results regularly and adjust the schedule as needed.
5. What is an annual preventive maintenance (PM) schedule?
An annual PM schedule outlines all preventive maintenance tasks that need to be completed over a 12-month period. It includes recurring inspections, servicing, and replacements planned at monthly, quarterly, biannual, or yearly intervals.