Equipment Maintenance Log: Leveraging a CMMS to Eliminate Silos and Misinformation
What is an equipment maintenance log?
An equipment maintenance log (also known as an equipment maintenance form or equipment maintenance sheet) is a simple, straightforward document that records asset maintenance activities performed on a specific piece of equipment.
Equipment maintenance logs generally contain two sections: general information and maintenance actions.
The general information section includes the equipment name, model, serial number, location, purchase date, and price.
The maintenance actions list includes the maintenance date, description, and who performed it.
Learn about machine maintenance and how real-time data helps you supercharge the entire process!
How to create an equipment maintenance log
A complete picture of asset health is essential to preventing downtime, often at the root of lost revenue.
An equipment maintenance log tracks asset maintenance activities that can directly or indirectly impact business revenue.
In this article, walk through the A to Z of equipment maintenance logs, templates, and best practices.
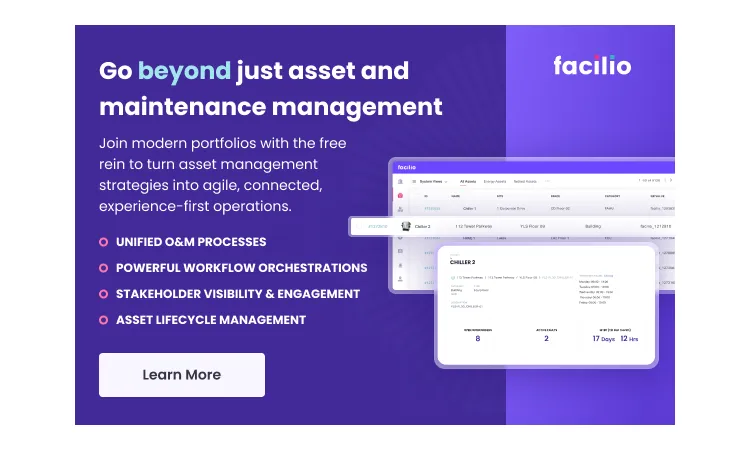
Types of maintenance logs
Depending on the use, maintenance logs can be of three kinds: schedule logs, machinery logs, and project logs.
1. Maintenance schedule logs provide a 360° view of the organization's projects and the expected project completion timeframe.
2. Machinery maintenance logs contain info on scheduled or planned maintenance activities for every equipment your company owns. These logs ensure timely machine maintenance at regular intervals.
3. Project logs are similar to maintenance schedule logs and help organizations track projects and the time to completion. They may contain maintenance tasks along with other projects.
These different maintenance logs help you document tasks across the company, optimize plant performance, and create a safe working environment.
Lear More: Equipment Maintenance Software
Why is it important to keep equipment maintenance logs?
The purpose of an equipment maintenance log is to record equipment maintenance activities to check the maintenance management process efficiency and track technicians' tasks.
Maintenance log data reveals significant failure, repair, and expenditure patterns — all key to deciding whether to replace or repair assets.
Equipment maintenance logs also show asset breakdown frequency and help optimize the preventive maintenance schedule.
Finally, these logs aid in creating specialized equipment maintenance programs, making cost-effective decisions, and boosting equipment resale value.
Benefits of equipment maintenance logs
Accurate equipment maintenance logs help companies minimize operational costs, better manage asset lifecycle, keep operators safe, and repair equipment faster.
- Save money on repairs. An equipment maintenance log lets you see assets that are no longer useful to you. As a result, you can resell the surplus to reduce inventory, save space, and cut operational expenses.
- Identify asset trends and predict downtime. Equipment maintenance logs offer critical insights into different equipment components and models. Analyzing those insights aids you in predicting downtime and making emergency asset repair decisions with speed and precision.
- Diagnose asset failure faster. Tracking asset health manually may not be feasible in large facilities that need a faster past maintenance overview for diagnosing asset issues and creating work orders. Equipment maintenance logs help them automate asset data collection and distribution among workers.
- Keep operators safe. It’s easy to miss regular equipment wear and tear, creating an unsafe environment for everyone. Equipment maintenance logs track potential issues that can quickly become major problems.
Using an automated system for equipment maintenance logs is crucial for easy information access, automating data recording, reducing paperwork, and managing maintenance records accurately.
What is destructive testing and why do you need it?
How to create an equipment maintenance log
Creating an equipment maintenance log is easy once you add the following details:
- Facility location
- Asset name and serial number
- Equipment manufacturer name and contact
- Asset maintenance technician and operator’s name
- Date of asset purchase, first use, and maintenance
- Description of asset maintenance activities
- Next scheduled maintenance date
- Additional comments and observations
Here’s the step-by-step process of creating an equipment maintenance log:
- List all equipment: Identify and develop a list of assets you want to include in the maintenance log.
- Collect equipment details: Gather equipment name, type, serial number, location, last inspection date, and maintenance activities performed.
- Create a maintenance schedule: Create a plan that includes all scheduled maintenance tasks on equipment.
- Track asset costs: Record equipment repair and replacement costs in the maintenance log.
- Maintain equipment history: Note equipment usage and malfunction from previous maintenance inspection reports.
- Assign technician: This is the final stage, where you add maintenance technicians in equipment maintenance logs. These technicians are responsible for inspections and repairs.
These steps are key to creating an equipment maintenance log using a spreadsheet.
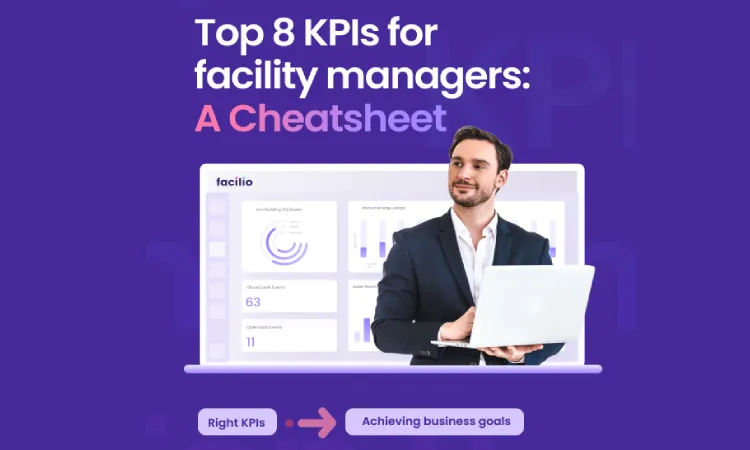
What is an equipment maintenance report?
An equipment maintenance report contains specific maintenance inspection data that offers visibility into operations and aids decision-making. These reports include the following maintenance metrics:
- Planned maintenance percentage (PPC) reveals the amount of maintenance time you use for planned maintenance tasks.
- Overall equipment effectiveness (OEE) measures the percentage of productive manufacturing time.
- Mean time to repair (MTTR) calculates the repair and testing time it takes for a broken system to be functional.
- Mean time between failure (MTBF) shows the average elapsed time between asset breakdowns.
- Preventive maintenance compliance (PMC) tells you the percentage of scheduled preventive maintenance tasks completed over some time.
How to write an equipment maintenance report
Maintenance managers follow these four steps to write equipment maintenance reports:
- Choose a reporting format. If your facility houses multiple assets, it’s best to use a template for keeping reports consistent. Smaller companies may be better off with preventive maintenance checklists.
- Identify maintenance report elements. Decide the metrics and details you want to track and include in reports.
- Create a report. Gather all equipment information based on the maintenance metrics to analyze.
- Review the report. Finally, review the report for accuracy. Consider checking it regularly to find areas that need your attention.
Now, let’s look at a few best practices for creating maintenance reports.
- Standardize data capture. Maintenance managers spend countless hours collecting and verifying data. Add to that the risk of losing paperwork or getting the wrong data. Automating data capture can end all these problems.
- Maintain a single source of truth. Inability to keep data up-to-date leaves you with data analysis, interpretation, and decision-making challenges. This is another reason maintenance departments move from spreadsheets to automated equipment maintenance management systems.
- Spend more time in decision-making. Crunching numbers manually is another headache for maintenance managers, and that’s where enterprise asset management systems can help.
Predictive Reliability: Check out this article to learn what it is, and how it is the key to improved performance!
Who is responsible for equipment maintenance?
The following departments are responsible for equipment maintenance and can help you achieve total productive maintenance.
- Operators, including plant managers, machine operators, and line supervisors.
- Inventory managers who often need to rotate assets based on facility demands.
- Health and safety officers who ensure workplace safety with processes like lockout tagout.
- Reliability engineers who analyze maintenance metrics to offer actionable insights.
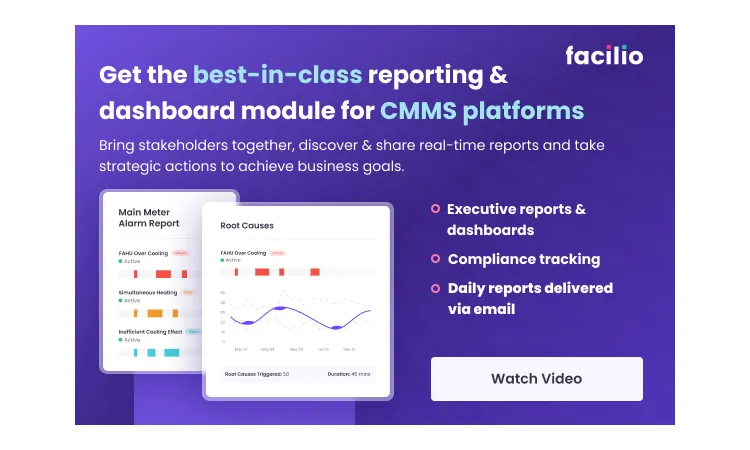
How to maintain accurate and up-to-date maintenance logs
Managing maintenance logs is no easy feat.
Typically, maintenance managers are buried in paperwork while tracking maintenance activities or servicing tasks, gathering data, analyzing data, and finding insights.
CMMS software like Facilio streamlines asset maintenance and management with automated work order creation and historical maintenance activities tracking.
Moreover, you can automatically update logs as soon as a work order closes.