Work Orders: Definition, Benefits, Types, and How to Create One
In any large property or facility, operational efficiency hinges on the maintenance of its equipment. Work orders are critical documents that help streamline the maintenance of such equipment.
What is a work order?
Why are work orders important?
For facility and property managers, managing service requests manually or through disparate ticketing systems can lead to a torrent of unresolved issues.
Imagine this:
Crucial time-bound requests can go unnoticed, duplicate work orders clutter the system, and critical escalations could slip through the cracks. It's a scenario packed with missed deadlines and frustrated stakeholders.
Work orders help tame this chaos by bringing order to the diverse service and maintenance requests of varying priority levels.
Take the example of an educational institution where most service requests are reactive in nature. The challenge of limited workforce and budget constraints makes it difficult to manage service requests.
However, some facility managers tend to navigate this maze effortlessly. What’s their advantage?
They rely on tools like connected CMMS. It can consolidate and optimize several crucial functions like:
- Property maintenance
- Client engagement to vendor management
- Workplace management
- Asset maintenance and upkeep of the facility
It works by unifying systems, processes, and people to consolidate all facility operations in one place, and at scale.
When it comes to work order management, they aid in providing prompt acknowledgment, timely assignment, and precise closure of service requests.
Whether delivering services across multiple facilities or managing requests in resource-limited facilities and educational institutions, a connected CMMS helps transform maintenance management into a proactive, reliable process, supporting operational excellence.
A detailed understanding of work orders and how they work is necessary to leverage them to their fullest. This article will give you a complete overview of work orders, their management, and how you can use them to your advantage.
What is work order management?
Every work order follows a lifecycle beginning with identifying the problem and ends with completion and closure of the problem.
Types of work orders
Considering that each property project is distinct from another, organizations rely on different types of work orders to resolve specific issues. Some of the primary variants here include:
General work orders
These maintenance work orders include simple tasks such as equipment installation, asset removal, or even repainting a specific facility section.
The primary distinguishing factor here is that these projects are not assigned predetermined schedules and occur only when necessary.
In addition, while unforeseen asset malfunction can be construed as a general project, they fall under a completely different category due to the exact nature of the work.
Preventive maintenance
A preventive maintenance work order is a scheduled maintenance routine to address or avoid potential equipment failure.
Here are the two types of preventive maintenance:
- Reactive: Project commences upon immediate asset failure
- Predictive: Maintenance occurs at specific intervals to ensure smooth equipment functioning
Examples include monthly equipment checks, scheduled cleaning, or asset replacement.
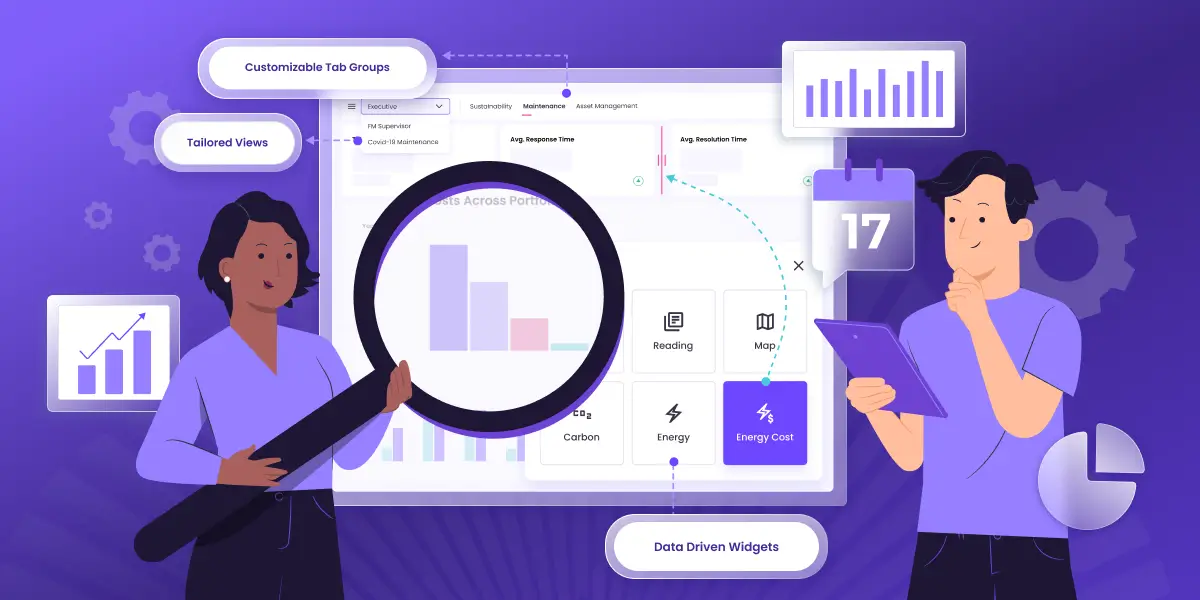
Inspection and audits
Property technicians and maintenance personnel often conduct general audits to examine the current state of operations.
These periodic checks occur through an inspection order.
During this work order process, a problem is identified, and a request is raised to correct it.
Afterward, managers can deploy a corrective order to isolate and solve the issue.
Emergency maintenance
Emergency maintenance work orders deal with unplanned equipment breakdowns.
This is similar to reactive maintenance and requires a log of the conducted operations to fix the problem.
For instance, ground personnel could include information regarding what caused the malfunction, the steps taken to readdress the failure, and how to prevent it from happening again.
Example of a work order
- What does a typical work order look like?
- What are its key fields?
- Who creates it? Who approves it? Who executes the job?
The work order example given below answers all those questions and more.
Work Order ID: WO-20240617-001
Date: June 12, 2024
Requested By: James Pape, Facility Manager
Department: Maintenance
Location: Building A, 3rd Floor, Room 305
Subject: The air conditioning unit in Room 305 is not cooling the room effectively. Occupants frequently report an unusual noise coming from the compressor.
Category: HVAC
Maintenance Type: Corrective
Work to be Performed:
1. Conduct a thorough examination of the air conditioning unit to identify the problem.
2. Check internal components for any damage or blockages.
3. Check and clean the air filters and ensure proper airflow.
4. Repair or replace necessary components, if necessary.
5. Test the unit to confirm it is cooling efficiently and operating quietly.
6. Document the steps taken to solve the noise problem and attach a list of any parts replaced.
Other instructions:
1. Schedule maintenance during lean hours to ensure minimal disruption to the office staff during/occupants the repair.
2. Follow all safety protocols and use appropriate personal protective equipment (PPE).
3. Ensure adherence with all regulatory compliances related to handling of refrigerants.
Priority Level: High
Vendor/In-house: In-house
Assigned To: George Hudson, HVAC Technician
Estimated Completion Date: June 14, 2024
Approval/Authorized by: Merrill T. Metcalf, Operations Manager
Lifecycle of a work order
Every work order follows a lifecycle — from its creation until closure. There are reviews and approvals that happen in between these two milestones.
Here is how a work order usually progresses from creation to resolution.
Let’s understand the lifecycle of a work order better with the example of a reactive maintenance in a rental site, assuming you are the property manager responsible for reviewing and approving work orders:
Let's better understand the lifecycle of a work order using the example of reactive maintenance for a plumbing problem.
- Identification: The maintenance manager identifies the plumbing problem.
- Creation: A work request is created describing the list of reactive maintenance activities to be done to address the plumbing problem.
- Approval: You review and approve the request, prioritizing it as high urgency.
- Assignment: The work order is assigned to a plumbing technician.
- Execution: The plumbing technician repairs the plumbing and reports back to the maintenance department for review.
- Review: Once the maintenance manager approves the work quality, you review the completed work order and ensure all steps were properly followed.
- Documentation: All actions and findings such as the cause of the plumbing problem, steps taken to fix it, and prevention measures to be taken are documented.
- Closing: The work order status is marked as complete and closed.
The role of work orders in streamlining maintenance
While most people deem efficient work order management beneficial to their facility operations, few seem to recognize it.
Here is how they help.
Work orders have a direct impact on service quality and facility management. They act as a crucial mechanism for tracking maintenance activities, ensuring timely repairs, and maintaining the overall functionality of facilities.
Labor, contract, and material cost tracking
Work orders contain detailed information about the labor and materials used for each task. They aid in tracking costs and material consumption and provide a comprehensive view of operational expenses and resource utilization.
Equipment downtime recording
Work orders act as the documented proof of equipment downtime. They capture the exact duration and frequency of downtime which eventually leads to better understanding of equipment performance, identification of recurring issues, and planning of preventative maintenance or retro-fitting.
Integration with related modules (preventive maintenance, facility scheduling, inventory, etc.)
Work order management systems do not exist in silos. They seamlessly integrate with other facility scheduling systems, inventory management, asset management, and reporting tools. This integration ensures smooth exchange of data and efficient maintenance management.
Best practices for prioritizing and managing work orders
Task order creation is only scratching the surface. The real challenge is in prioritizing and managing them with a defined process.
Follow these best practices to make work orders for your facility operations.
Requiring a formal submission for work requests
All work orders must be formally submitted through designated channels, regardless of how they are initiated. For example, the work order discussion might have been initiated in a team meeting, but it should be formally submitted through the designated channel to reach the approver for creation and approval.
A formal submission process standardizes the whole process and ensures better work order tracking and management. You can choose between using work order templates for various scenarios or considering using an property management system with work order management to streamline the whole process.
Centralize work orders management
In the past, work orders were paper-based and were created in triplicates or quadruplicates to serve every concerned department. Although work orders are now created digitally, they still need a centralized management system to avoid confusions and miscommunications.
This centralized work order directory should be easily accessible to all relevant departments and should ideally enable them to manage specific work orders relevant to them in an autonomous fashion.
For example, property engineers can oversee electrical equipment, while department heads can issue new work orders as needed.
Prioritize work orders based on urgency
Work orders should ideally be picked upon priority so that damage can be curbed before they grow into uncontrollable situations. Mentioning the priority of the work orders helps in differentiating between which tasks need immediate attention and which can be delegated or scheduled for a later time.
For example, prioritizing a malfunctioning production conveyor belt is a high priority over a minor lighting issue in a washroom, as the former directly impacts daily operations.
Priority levels are usually defined as high, moderate, and low. Sometimes, they are also indicated by color codes like yellow, blue, green, or red, where each color denotes a specific priority level agreed internally.
Define approval timelines
Work orders are time-sensitive documents. It is necessary for the personnel creating and approving the work order to ensure timeliness to prevent delays in its completion. Excessive approval delays could delay the work order from being assigned and completed, which could subsequently lead to equipment damage.
Although approval deadlines could vary from industry to industry, for high-priority issues, such as major equipment failures, approval within an hour of work order submission is considered ideal.
This table provides a snapshot of the approval timelines can be determined:
Utilize automated scheduling tools
Work order management should be automated as much as possible to avoid errors and data updation issues. There are automated tools like CMMS or computer-aided facilities management (CAFM) systems that can help facility managers schedule and manage work orders efficiently. These tools can streamline workflows, reduce manual errors, and provide real-time updates on work order statuses.
Ensure comprehensive documentation
While the details may vary across specific organizations, some standard elements include information on:
- Equipment failure description
- Conducted maintenance tasks
- Results and efficiency of the maintenance work
- Time spent on the task
- Parts used for replacements
Training your personnel to ensure comprehensive documentation ensures that there is sufficient data to review and ensure that the work has been carried out according to prescribed standards.
Establish integration with other systems
Your work order management system cannot exist in a silo. It should seamlessly integrate with other facility management systems like inventory management systems, procurement systems, and asset management systems. It facilitates smooth data exchange and also consolidates all data in a single platform for analysis and visualization.
Following these best practices ensure that your work order management process contributes to smooth facility operations and timely maintenance across your facility.
However, to follow these best practices and to reap their benefits, your facility will need a reliable CMMS tool. In today’s mobile era, cloud-based CMMS have the upper hand over legacy systems.
Cloud-based CMMS systems vs legacy systems
Cloud-based work order management systems have started replacing them and are becoming the mainstay for several reasons.
Centralized cloud-based work order management systems go far and beyond the capabilities of spreadsheets or legacy solutions in streaming work order management.
The table below highlights the differences:
Work order management with Facilio
Facilio’s automated work order and reactive job management capabilities significantly streamline maintenance operations.
Vendor management made easy with a single user interface to track vendor contacts, insurance and work orders. Check out the Video below
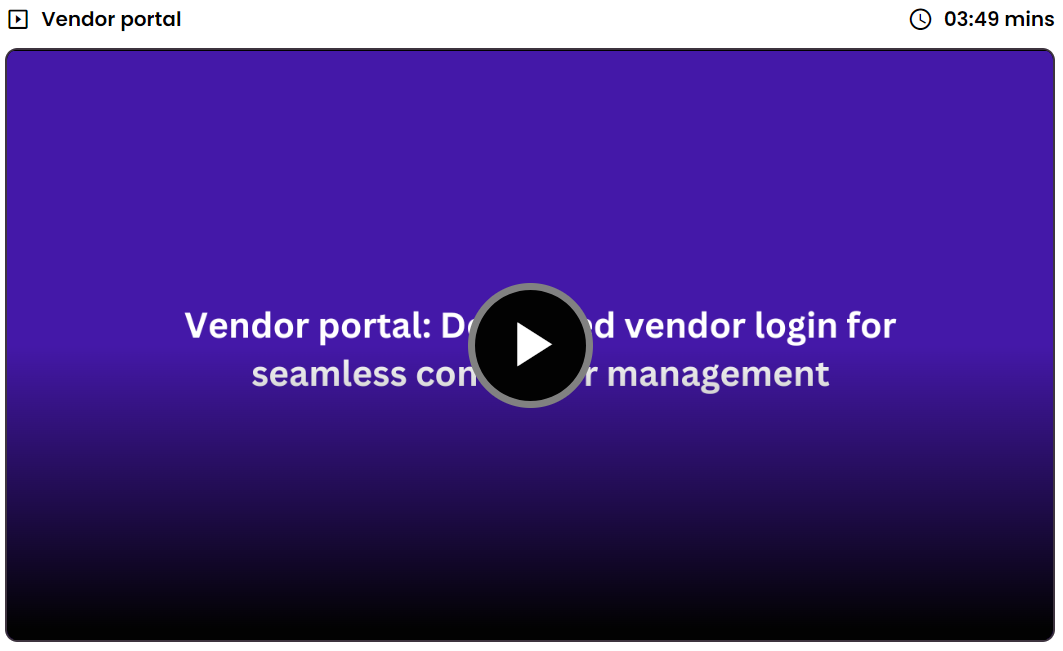
How Facilio's automated work orders and reactive job management can enhance campus maintenance
Facilio's advanced features can bring significant improvements to school and university campus maintenance operations. Here’s how Facilio can improve students/staff experience:
How Facilio's automated work orders and reactive job management can enhance campus maintenance
For any educational institution with sprawling property operations, Facilio can be a reliable tool. It streamlines work orders and ensures that campus maintenance happens in an organized manner. High-priority and urgent tasks are attended to immediately while low-priority tasks are queued and matched to relevant personnel.
Here are some of the resultant benefits;
Decrease in facility downtime and inconvenience to staff & students
Facilio centralizes incident reporting and work order management across the campus. Students and staff can raise complaints for incidents to a dedicated email.
Facilio automatically reads the email, extracts the issue details, and converts it into a work order without delay. This helps in eliminating communication gaps between maintenance teams and students/staff and aids in quick resolution of work orders.
See it in action: Support Email Configuration in Facilio
Maintaining assets with high cost efficiency in budget-strained operations
In any typical large-sized campus, the facility maintenance team is bound to receive a mix of high-priority and low-priority tasks at high volumes. Poor prioritization and unplanned resource allocation can strain resources and eventually inflate operational costs.
Facilio’s workflow manager can optimize resource allocation by automating the process of categorizing and prioritizing tasks. It ensures that urgent and high priority tasks are immediately approved and assigned, while low priority non-urgent tasks are prioritized for later.
Promoting Sustainability with Resource Efficiency
Facilio can be your reliable partner in promoting sustainability initiatives. It gives an accurate account of energy usage and also assists in timely preparation of compliance reports for sustainability reporting. Furthermore, Facilio is a cloud-based facility management platform which is easily scalable. Whether it's a large university or a small college, Facilio adapts to meet the requirements of educational institutions of any size.