How to Manage Inventory with CMMS
Modern CMMS systems have come a long way from legacy ones that are primarily systems of record—they stored maintenance data and reported it in a collated manner when required. In contrast, connected CMMS platforms take a modular approach to facility management, including inventory management.
Facility managers (FM) need control and readily available spare parts for uninterrupted maintenance schedules. They should always have visibility into the following: a complete catalog of assets, where they are stored, where they are ordered from, what is on order or on backorder, assets with low supply and which assets are needed for upcoming preventive and predictive maintenance. Legacy systems that do not integrate inventory management force FMs to work with disparate applications that do not interoperate, making it challenging to have portfolio-wide visibility.
An integrated CMMS enables automation of inventory management i.e. issuing of work orders once a predetermined inventory level has been reached. Maintenance operations are streamlined as asset management, work order management, compliance, and spare parts inventory management work in tandem.
Thus, FMs can move away from managing unplanned downtimes and toward scheduling preventive maintenance based on data gathered by a purpose-built IoT-driven platform like Facilio.
Let’s explore the advantages offered by a single-pane-of-glass approach to inventory management and CMMS.
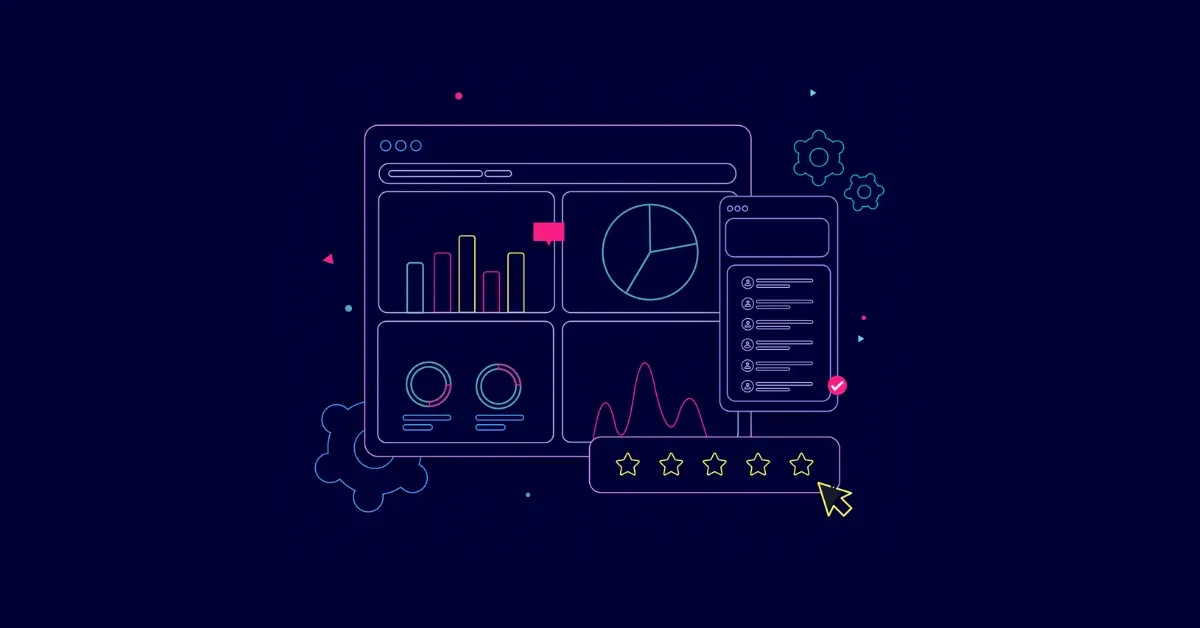
Benefits of using CMMS inventory management systems
Strategic insights into portfolio-wide performance
- Predictive analytics: By analyzing equipment performance data, CMMS inventory management systems predict maintenance needs and anticipate inventory requirements. FMs can proactively stock critical items.
- Vendor collaboration: Integrated inventory management facilitates communication with vendors. FMs can track orders and delivery status and negotiate terms—all within the same platform.
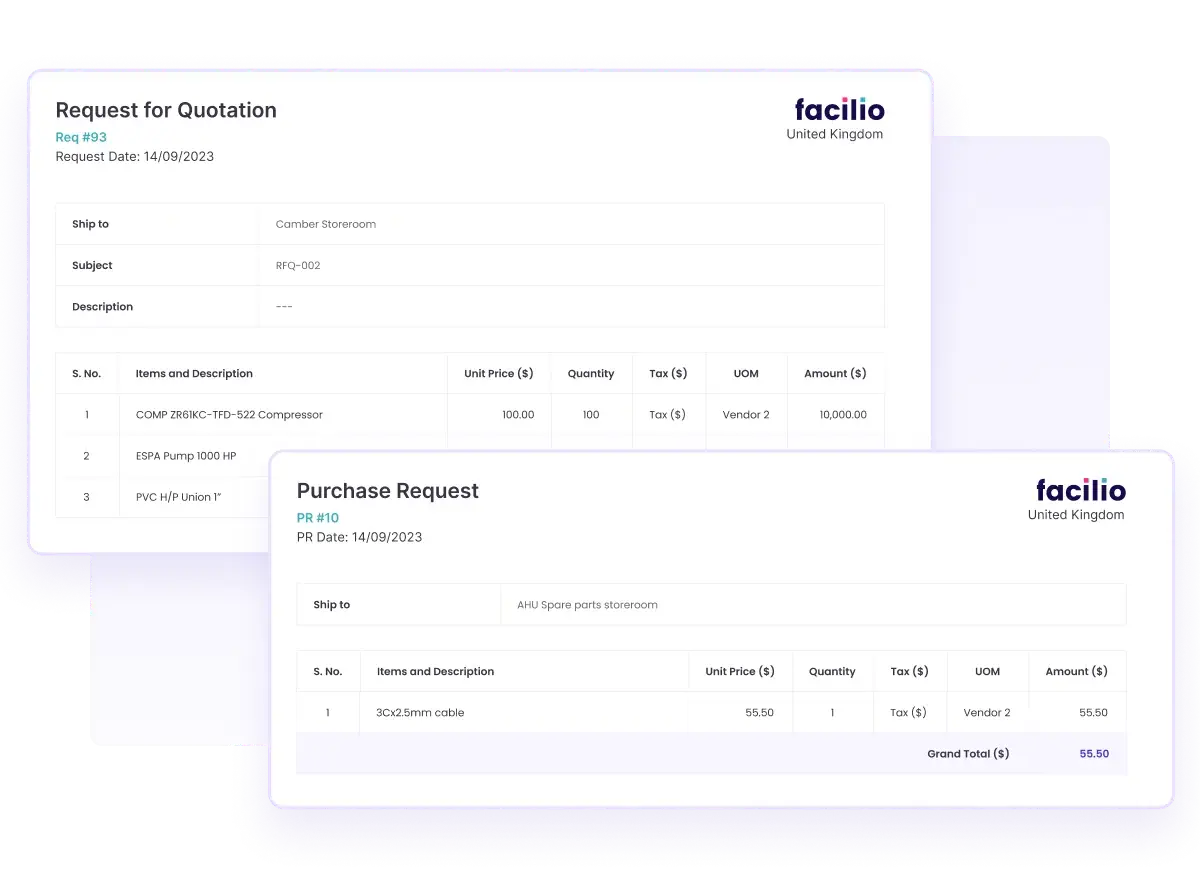
- Vendor collaboration: Integrated inventory management facilitates communication with vendors. FMs can track orders and delivery status and negotiate terms—all within the same platform.
- IoT-driven inventory insights: CMMS inventory management systems monitor inventory conditions (e.g., temperature-sensitive items). If storage conditions deviate from the norm, alerts are sent to the right stakeholders immediately.
Improved operational efficiency
You can efficiently manage assets, work orders, and inventory from a single platform. Data flows seamlessly across maintenance, procurement, and inventory functions.
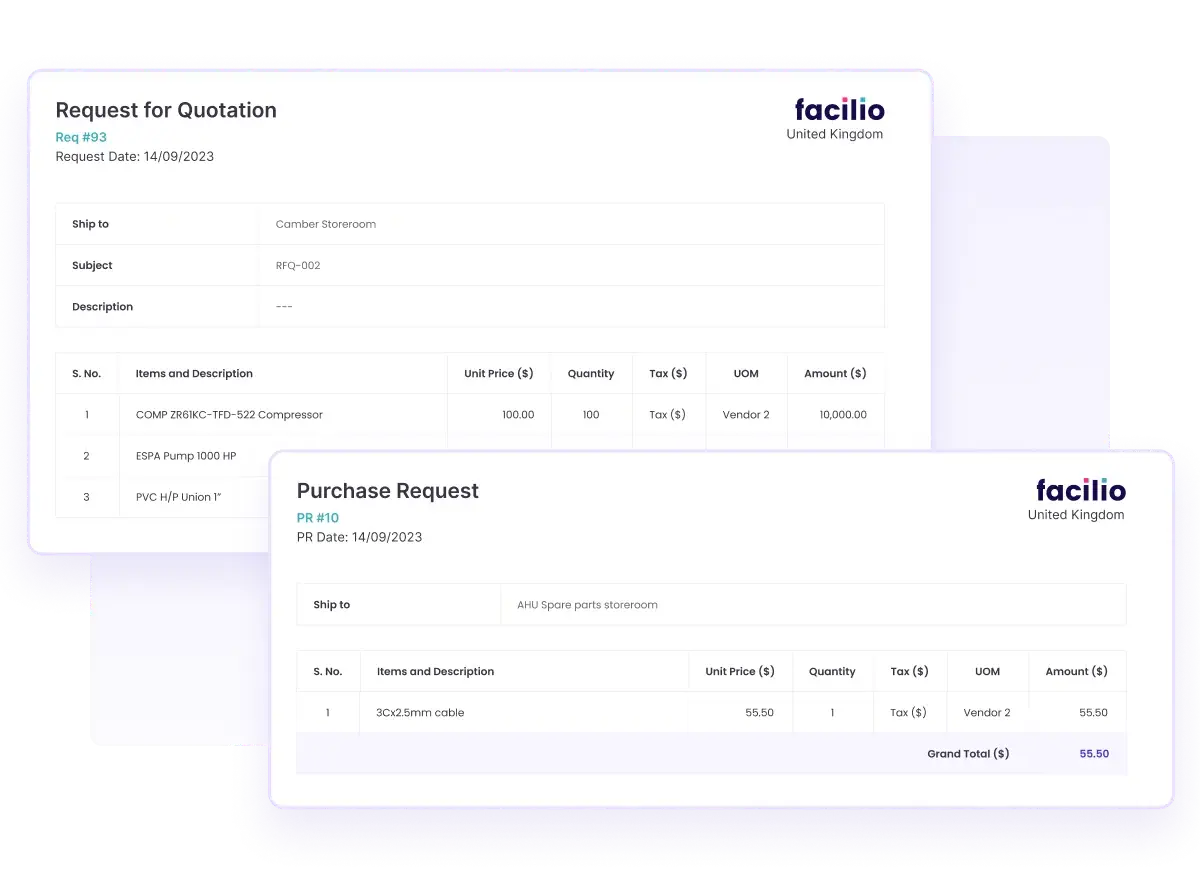
The CMMS inventory management system automatically checks inventory levels when a maintenance task requires a spare part. If stock is low, it triggers a reorder request. This automation reduces administrative overhead and prevents stockouts.
Quality control and compliance from a centralized system
CMMS inventory management systems enforce standardized processes by offering predefined workflows for various maintenance tasks, such as work order creation, approval, scheduling, execution, and closure.
These workflows are based on industry best practices and organizational requirements, guiding users through standardized processes step by step. Whether it’s replacing a pump or restocking cleaning supplies, adherence to quality standards becomes ingrained.
Case study: CIT Ltd. achieved 15% fault detection and preventive maintenance
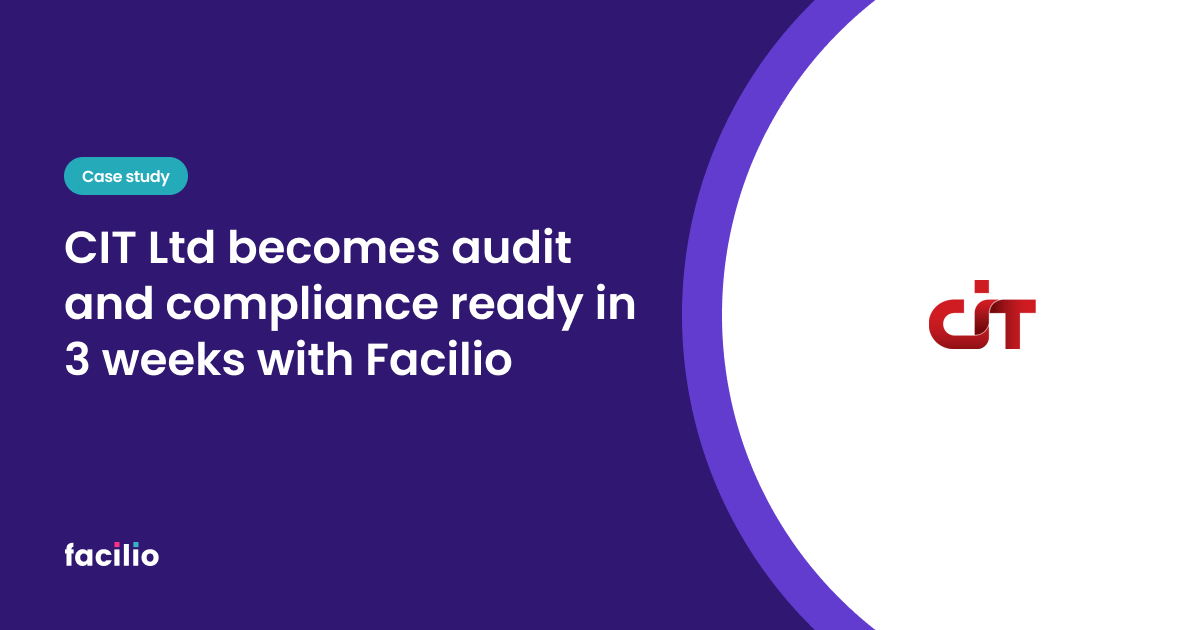
For instance, CIT Ltd., Makkah province, Saudi Arabia, recently faced specific challenges in their FM operations, which they aimed to address with Facilio. Their challenges included:
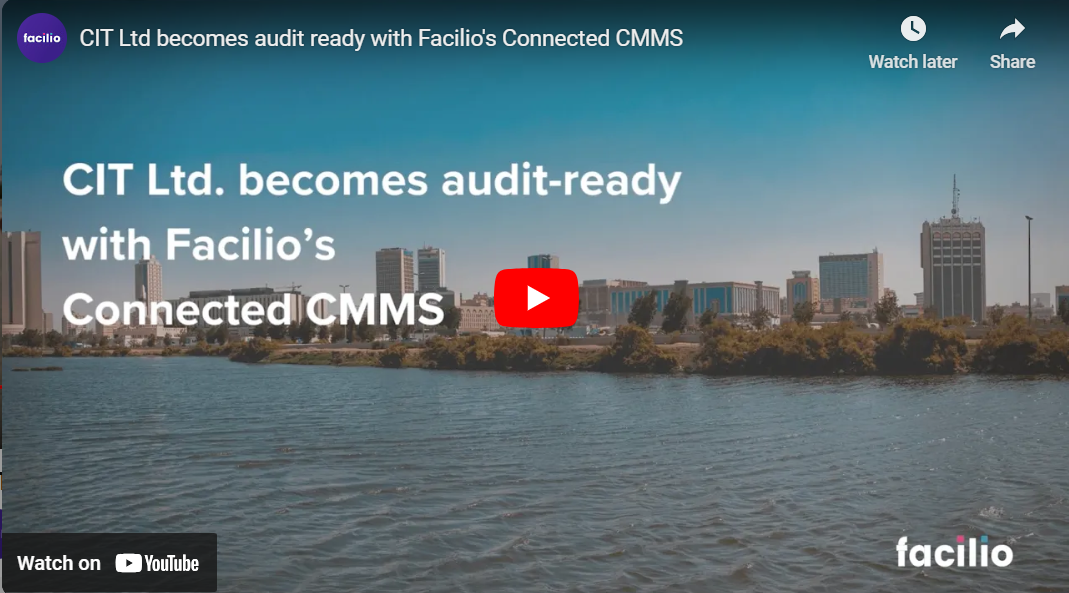
- The lack of a unified and efficient CMMS for RCU - Al Jadidah
- Difficulty in gaining a centralized view of assets and PPM activities
- Lack of visibility into daily and weekly operations, including pending work orders
- Limited insight into SLA adherence and vendor/technician KPIs
- Inability to effectively document workforce attendance for training QHSE, OSHA audits.
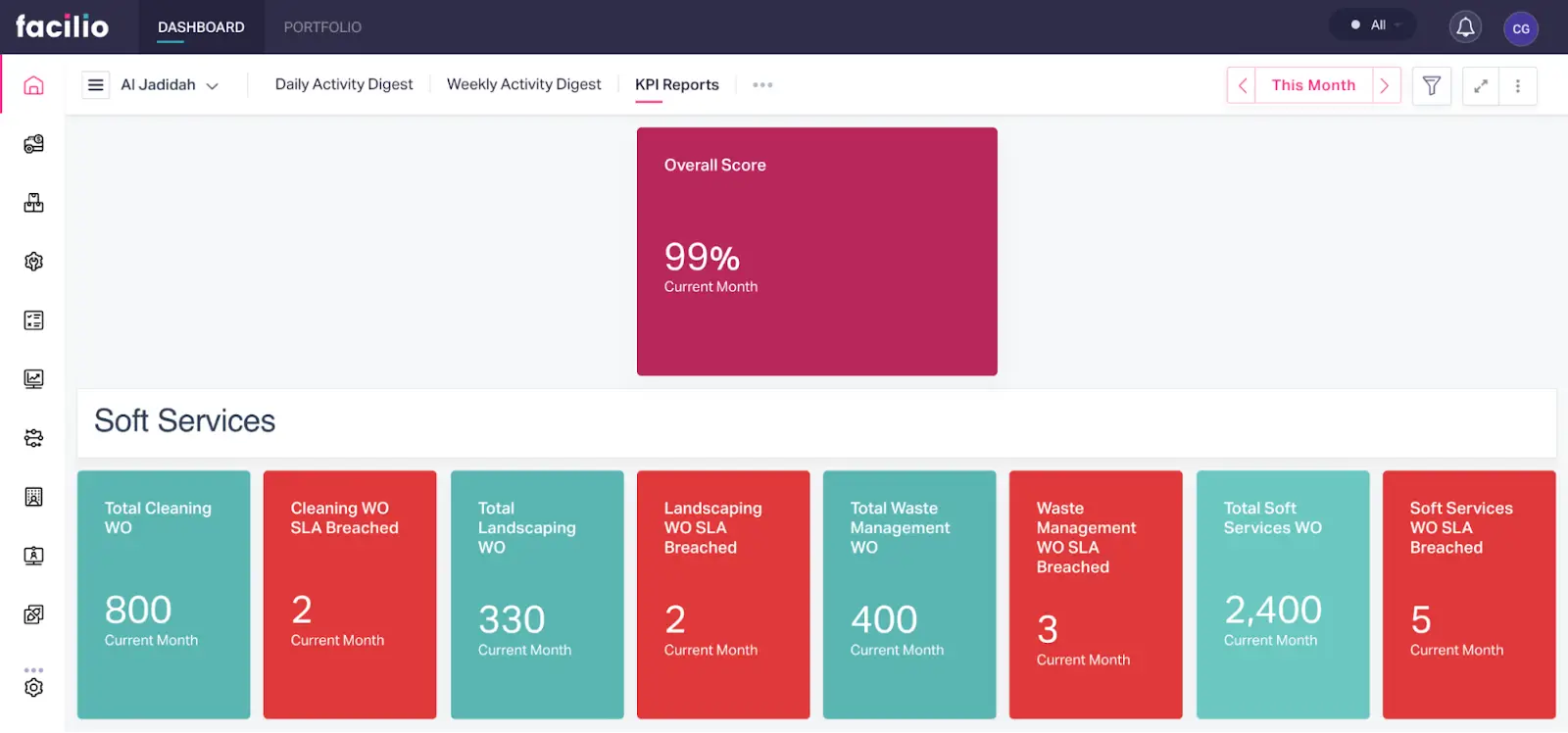
Facilio enabled them to achieve the following:
- Facilitating automated work orders and streamlining vendor management
- Reducing equipment downtime and increasing cost savings through predictive maintenance
- Optimizing training efficiency
- Providing analytical dashboards to monitor regular activities.
Inventory management CMMS software also ensures compliance with safety and environmental regulations by enabling FMs to track hazardous materials, expiration dates, and certifications.
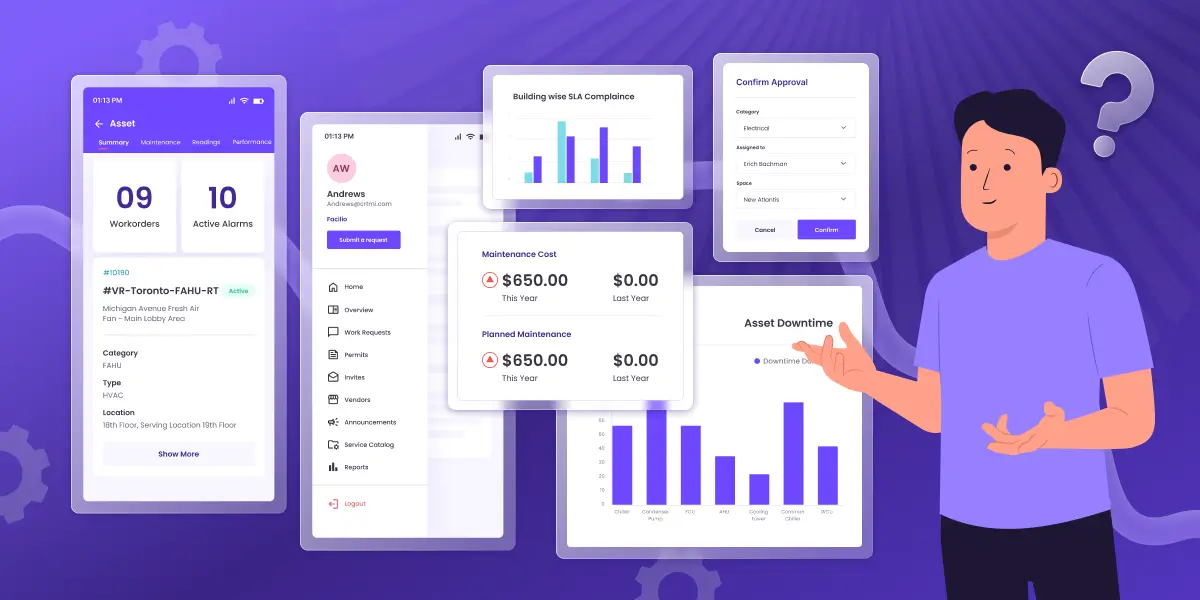
Cost optimization
- Reduced downtime: Say, a critical HVAC system fails due to a faulty sensor. With a maintenance inventory management system, FMs receive alerts about impending issues. Simultaneously, the system checks inventory for the required sensor. If unavailable, it initiates an order. Result? Minimal unplanned downtime.
- Right-sizing inventory: A CMMS inventory management system analyzes historical data to predict maintenance needs. FMs can optimize inventory levels, reducing carrying costs and freeing up capital.
- Life cycle cost management: FMs can assess the total cost of ownership for assets. A maintenance inventory management system helps decide whether to repair, replace, or retire equipment based on long-term cost implications.
Eliminate work order delays
When you use CMMS inventory management systems, all work orders are directly linked to inventory levels, ensuring that required parts are always available. This integration reduces delays, improves first-time fix rates for maintenance, and reduces close time for work orders.
Now, let’s explore some of the key features of CMMS for inventory management.
Key features of CMMS for inventory management
A connected CMMS for inventory management ensures that FMs have the necessary parts at the right price exactly when required. It includes an inventory module that catalogs all parts and tracks current quantities (such as on-hand, on-reserve, on-order, and backordered items). It also provides detailed information about the storage locations of these parts.
Some features of CMMS software that enable efficient inventory management are:
Integrated inventory management
Unlike manual tracking, CMMS inventory management systems automatically provide accurate and up-to-date information on stock levels, locations, and usage patterns.
As an admin, you can set minimum stock quantities for each type of item in the inventory, receive notifications to review work order costs, and keep your inventory data in one place.
Asset management
CMMS inventory management systems standardize best practices and enhance quality control. Asset management within CMMS helps you identify and address issues swiftly, improving efficiency and productivity.
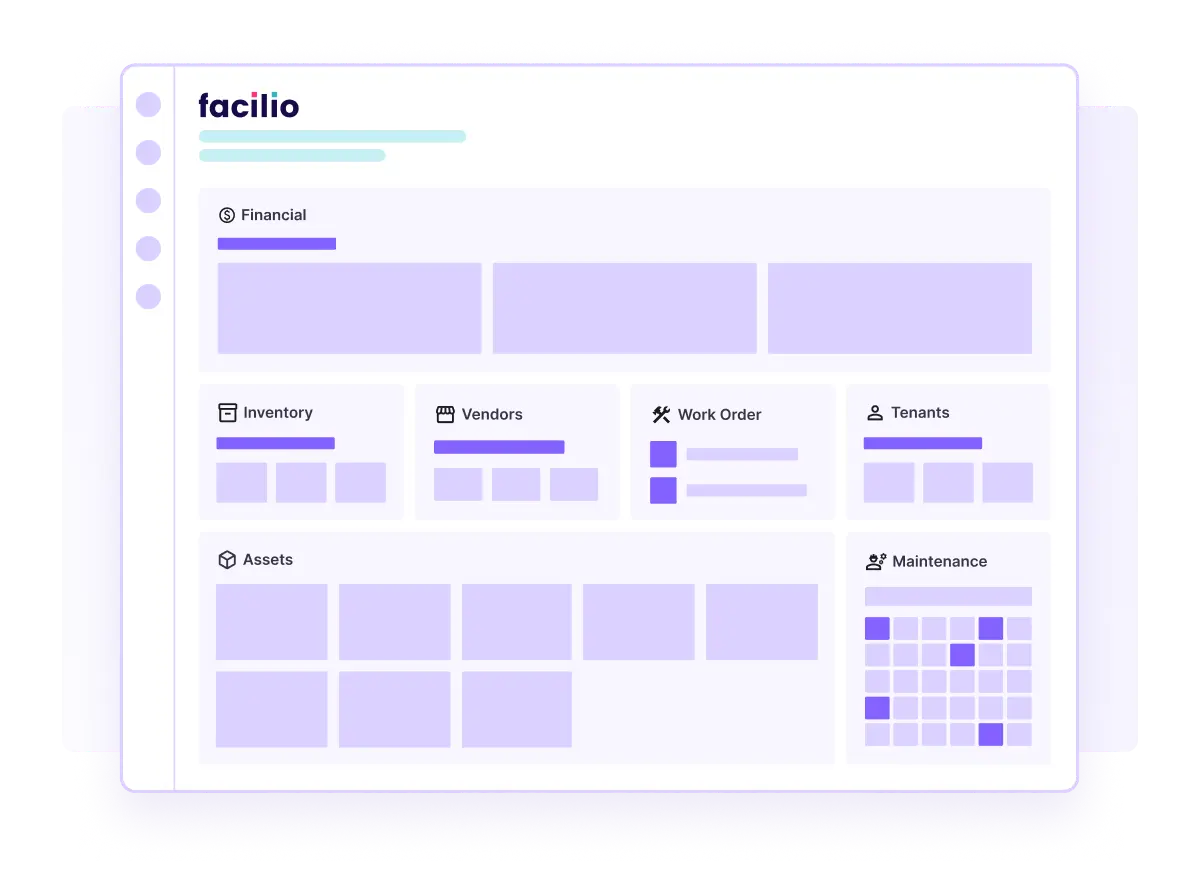
With CMMS inventory management systems, you can consolidate asset-related information within an asset registry. This repository includes crucial documentation, such as manuals, warranties, and procedures, and vital asset performance and downtime statistics.
Real-time reporting
Inventory management CMMS software gives you access to real-time data and reporting functionalities. It offers you a holistic view of inventory metrics and specific performance indicators.
Some examples of these metrics and KPIs are: inventory turnover ratio, days sales in inventory (DSI), stockout rate, order accuracy, lead time, backorder rate, fill rate, stock accuracy, work order completion rate, and inventory accuracy rate.

You can click directly on any graph on the dashboard or filter the data you want. You can also tailor our dashboard to your specific needs based on your scope or role as a stakeholder.
This enables you to make data-driven decisions and stay relevant by adapting quickly to changing requirements in your industry.
Best Practices to Streamline Inventory Management within a CMMS
Here are some best practices for managing inventory with CMMS:
Build an equipment bill of materials
Imagine being responsible for maintaining a fleet of forklifts, you can achieve this by creating a structured blueprint. How do you do this?
You list all components such as tires, hydraulic pumps, and safety lights. Each component has a part number, detailed description, and the quantity needed. You categorize these parts into mechanical, electrical, and consumables.
Using a CMMS, you can track each part, ensuring you have the necessary components in stock for timely maintenance, reducing downtime.
Here’s a more detailed description on how to build an equipment bill of materials.
- Define the scope: Identify the equipment for which you are creating the bill of materials (BOM). Ensure that the scope is well-defined, whether it's for a single machine or an entire production line.
- Itemize components: Break down the equipment into individual components and subcomponents. For example, if you are creating a BOM for a conveyor system, list out the motor, belts, pulleys, bearings, control units, etc.
- Detail specifications: For each component, include detailed specifications such as part numbers, material specifications, manufacturer details, and quantity needed. This helps in accurate procurement and maintenance planning.
- Categorize items: Group components into logical categories such as mechanical parts, electrical parts, consumables, etc. This makes it easier to manage and locate parts.
- Create a hierarchical structure: Arrange the components in a hierarchical format, showing the relationship between assemblies and sub-assemblies.
Identify all parts systematically
Implement a systematic labeling and cataloging system for all inventory items. For facility managers in manufacturing, every part used in production, from screws to large machine components, is labeled with a barcode.
Staff use handheld scanners to log parts in and out of the inventory system, ensuring real-time tracking and reducing the chances of errors or misplaced items.
Here are some practices for systematically identifying parts.
- Use standardized naming conventions: Develop a naming convention that is consistent and easy to understand. This should include abbreviations and codes that represent different categories and types of parts.
- Barcode systems: Integrate barcode or QR code systems to tag each part. This allows for quick scanning and tracking within your inventory management system.
- Inventory software integration: Ensure that your inventory management software can capture and utilize the standardized names and barcodes for easy tracking and retrieval of parts.
- Training: Train your staff on the new naming conventions and barcode systems to ensure everyone understands and uses the system correctly.
Implement a defect control system
One of the best examples of the significant implementation of a defect control system can be seen in factories that use sensors on their production line machines.
These sensors send data to a predictive analytics system. The system analyzes the data to predict when a machine part is likely to fail.
When prediction has been made, maintenance teams receive alerts and can replace parts during scheduled downtimes, avoiding unexpected breakdowns.
To effectively implement a defect control system, consider the following:
- Develop and adhere to preventive maintenance schedules for regular checks and servicing of equipment.
- Use predictive analytics tools to analyze data from equipment sensors and predict potential failures before they occur.
- Schedule regular inspections by qualified personnel to identify and address any emerging issues.
- Create a clear reporting mechanism for defects that includes digital forms or mobile apps to report and track issues.
Streamline the work order process
Consider using a CMMS inventory management system to digitize your work order management processes and automate task assignment, scheduling, and tracking.
Here are some tips on how to do this:
- Digital work orders: where tasks can be created, assigned, and tracked electronically.
- Automated task assignment: based on technician availability and expertise.
- Integrated communication tools: to facilitate real-time updates and collaboration.
- Reporting mechanisms: to track the progress and completion of work orders, helping in resource allocation and improving response times.
Centralize spare parts
A logistics company for instance can centralize all spare parts for its fleet of delivery trucks in one warehouse. Using a CMMS, they can track inventory levels in real time.
When a truck needs a new part, the maintenance team can quickly check availability and request the part, ensuring minimal downtime.
You can achieve centralization by:
- Real-time inventory levels: to avoid stock outs or overstocking.
- Streamlined procurement: to reorder parts when inventory levels fall below a certain threshold.
- Visibility and access: to check availability and request parts as needed.
Assign locations to parts
Allocate designated storage locations for each inventory item, optimizing space utilization and minimizing search time.
You can start by:
- Designating storage locations: for each part within your warehouse or storage area.
- Labeling and shelving system: for easy identification and retrieval of parts.
- Using digital mapping tools: to create a map of your storage area, showing where each part is located.i
Streamline maintenance with Facilio's integrated inventory management
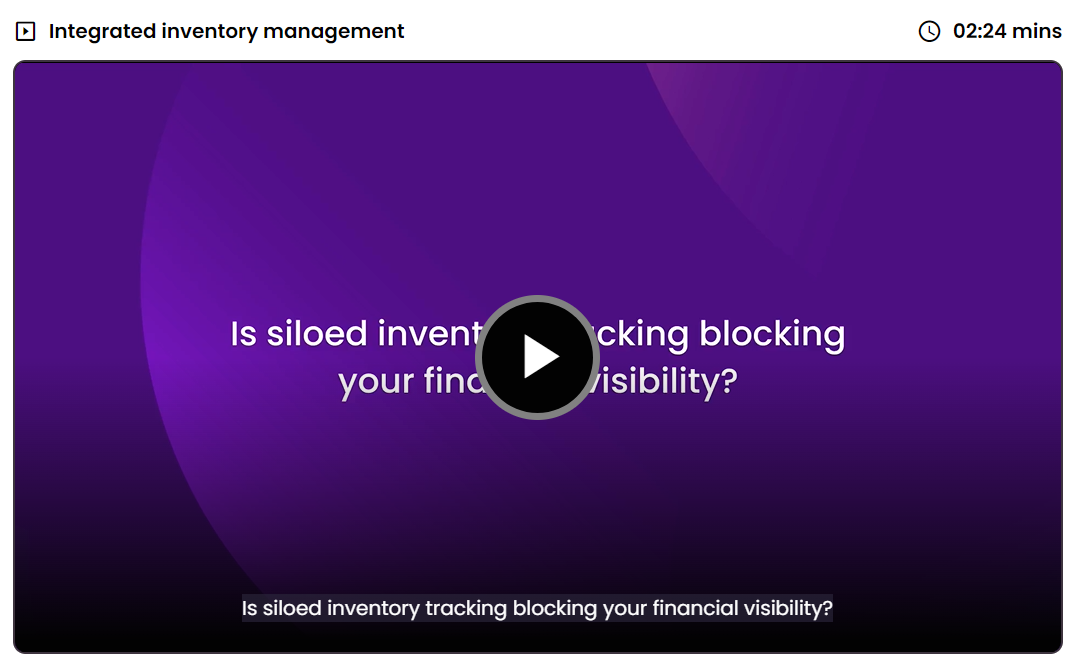
Tired of skyrocketing costs and missed deadlines? Facilio's AI-powered platform is the game-changer you've been waiting for.
Imagine being able to:
Effortlessly manage your workforce: Smart scheduling and real-time tracking mean the right person is always on the right job.
Gain instant insights: Stay ahead of the curve with live dashboards showing job progress, technician performance, and work order status.
Streamline service from start to finish: A centralized portal, automated notifications, and mobile inspections make managing any maintenance request a breeze.
The result? Lower costs, happier customers, and a maintenance operation that runs like a well-oiled machine. Don't wait – transform your business with Facilio today!