What is a work order?
A work order is a formal document—digital or paper—that outlines a specific job, detailing the task, who will do it, when it’s due, and what resources are needed.
In facilities management and maintenance, work orders keep daily operations organized, from scheduling preventive maintenance to handling urgent repairs. They ensure tasks are clear, trackable, and compliant.
A work request is simply a request for a job to be done; once approved with full details, it becomes a work order.
A job order is similar, but is often used in manufacturing or project-based industries.
If you’re wondering “what does work order mean?”, it’s essentially the bridge between identifying a need and getting the job done—clearly, and with accountability.
Purpose of a work order: Why is it important?
Companies use work orders to turn tasks into clear, actionable instructions. They define what needs to be done, who is responsible, the resources required, and the deadline—removing guesswork and miscommunication.
In industries like facilities management, healthcare, manufacturing, and commercial real estate (CRE), work orders are essential for:
- Task clarity – Everyone knows exactly what needs to be done
- Accountability – Assigning responsibility for each job
- Documentation – Keeping a record for audits and performance reviews
- Compliance – Meeting safety and regulatory standards
So, if you're still wondering what a work order is used for?
It’s the operational link between identifying a job and completing it—ensuring work is organized, traceable, and done right the first time.
Common types of work orders
Not all work orders are the same; each serves a different purpose depending on the job. Here are the most common types you’ll encounter in facilities and asset management:
- Preventive maintenance work order – Scheduled tasks to keep assets in good working condition, such as quarterly HVAC servicing or monthly fire safety checks.
- Reactive maintenance work order – Unplanned jobs triggered by an issue, like repairing a leaking pipe or replacing a failed motor.
- Inspection work order – Routine checks to assess asset health, such as elevator safety inspections or electrical system reviews.
- Corrective work order – Follow-up tasks to fix issues found during inspections, like replacing worn belts on a conveyor or recalibrating a sensor.
- Special project work order – One-off or non-routine work, such as office space renovations or seasonal landscaping.
If you’re asking “what is a maintenance work order?”, it’s any of these job types applied specifically to maintaining equipment, systems, or facilities, planned or unplanned.
Key components of a work order
An effective work order includes all the details needed to complete the job without confusion:
- Unique identifier or reference number – Tracks and organizes jobs in your system.
- Job description and scope – Clear instructions on what needs to be done and the expected outcome.
- Assigned technician or contractor details – Who is responsible for the work?
- Priority – Indicates urgency, from routine to critical.
- Required tools and materials – Items needed to carry out the job.
- Target start and completion date – Keeps timelines clear for both requester and assignee.
- Approvals and signatures – Confirms authorization before work begins.
Here's a sample work order format
Work Order ID: WO-20240617-001
Date: June 12, 2024
Requested By: James Pape, Facility Manager
Department: Maintenance
Location: Building A, 3rd Floor, Room 305
Subject: The air conditioning unit in Room 305 is not cooling the room effectively. Occupants frequently report an unusual noise coming from the compressor.
Category: HVAC
Maintenance Type: Corrective
Work to be Performed:
1. Conduct a thorough examination of the air conditioning unit to identify the problem.
2. Check internal components for any damage or blockages.
3. Check and clean the air filters and ensure proper airflow.
4. Repair or replace necessary components, if necessary.
5. Test the unit to confirm it is cooling efficiently and operating quietly.
6. Document the steps taken to solve the noise problem and attach a list of any parts replaced.
Other instructions:
1. Schedule maintenance during lean hours to ensure minimal disruption to the office staff during/occupants the repair.
2. Follow all safety protocols and use appropriate personal protective equipment (PPE).
3. Ensure adherence with all regulatory compliances related to handling of refrigerants.
Priority Level: High
Vendor/In-house: In-house
Assigned To: George Hudson, HVAC Technician
Estimated Completion Date: June 14, 2024
Approval/Authorized by: Merrill T. Metcalf, Operations Manager
Lifecycle of a work order
Every work order follows a lifecycle — from its creation until closure. There are reviews and approvals that happen in between these two milestones.
Here is how a work order usually progresses from creation to resolution.
Let’s understand the lifecycle of a work order better with the example of a reactive maintenance in a rental site, assuming you are the property manager responsible for reviewing and approving work orders:
Let's better understand the lifecycle of a work order using the example of reactive maintenance for a plumbing problem.
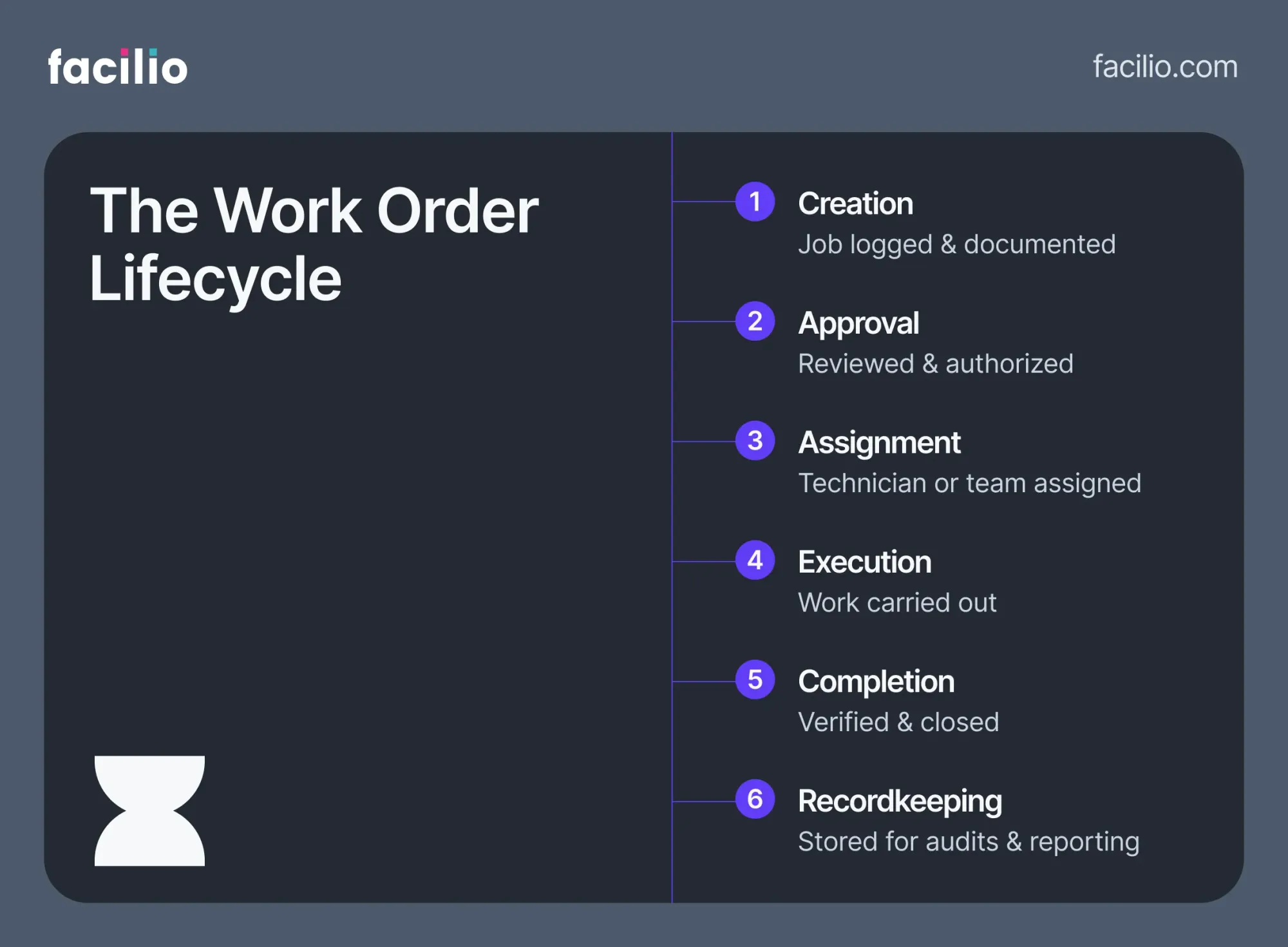
- Identification: The maintenance manager identifies the plumbing problem.
- Creation: A work request is created describing the list of reactive maintenance activities to be done to address the plumbing problem.
- Approval: You review and approve the request, prioritizing it as high urgency.
- Assignment: The work order is assigned to a plumbing technician.
- Execution: The plumbing technician repairs the plumbing and reports back to the maintenance department for review.
- Review: Once the maintenance manager approves the work quality, you review the completed work order and ensure all steps were properly followed.
- Documentation: All actions and findings such as the cause of the plumbing problem, steps taken to fix it, and prevention measures to be taken are documented.
- Closing: The work order status is marked as complete and closed.
Work order vs. work request
Although often used interchangeably, a work order and a work request are not the same.
- Work request – A submission asking for a job to be done, usually from a tenant, employee, or monitoring system. It’s a proposal, not an instruction.
- Work order – A formal, approved document that includes all necessary details to carry out the job—scope, assignee, timeline, and resources.
Key difference: A work request identifies what needs attention, while a work order defines how and when it will be addressed.
Example:
- Work request – “Air conditioning in Meeting Room B is not cooling.”
- Work order – “Replace air conditioning unit in Meeting Room B; assign to HVAC technician; priority: high; completion by 5 Aug 2025.”
Benefits of using work orders
A well-structured facilities work order system does more than assign jobs—it creates a foundation for consistent, measurable, and compliant operations.
- Centralized task tracking – Every job, from preventive maintenance to urgent repairs, is recorded in a single system. This makes it easier to manage workloads, avoid duplication, and monitor progress in real time.
- Clear accountability – Work orders name the responsible technician or contractor, define the scope, and set deadlines. This reduces confusion, ensures ownership, and improves follow-through.
- Compliance documentation – In regulated industries, proving that maintenance was completed on time and to standard is essential. Work orders create an audit-ready history that supports safety inspections, environmental audits, and quality certifications.
- Historical data for planning and budgeting – By analyzing past work orders, teams can identify recurring issues, calculate asset lifecycle costs, and justify budget requests. For example, a year’s worth of HVAC work orders might reveal the need for equipment replacement rather than continued reactive repairs.
In practice, a strong work order process helps facilities teams stay proactive, reduce downtime, and make better decisions based on accurate, accessible data.
Common challenges with manual work orders
While paper forms, spreadsheets, or email-based work orders may seem manageable, they often create bottlenecks that slow down operations and increase costs. Common issues include:
- Lost paperwork or incomplete records – Physical work orders can be misplaced, and missing details make it harder to track what was done, when, and by whom.
- Delayed approvals and job starts – Approvals that rely on physical signatures or back-and-forth emails can push urgent work days behind schedule.
- Lack of visibility on status and progress – Without a centralized system, managers can’t see in real time which jobs are in progress, pending, or overdue.
- Miscommunication between stakeholders – Details can be misunderstood when information passes through multiple channels, leading to rework or missed steps.
- Inefficient prioritization – Without automation or clear data, low-priority jobs might be handled before critical ones, risking compliance or operational continuity.
These challenges make it difficult for facilities teams to work efficiently—especially across multiple sites—setting the stage for why many organizations turn to automated and connected solutions.
What are automated work orders?
An automated work order uses technology—typically a CMMS (Computerized Maintenance Management System)—to create, assign, track, and close jobs without the delays and errors of manual processes.
Instead of filling out paper forms or relying on email chains, automated systems trigger work orders based on set conditions: a scheduled maintenance date, a sensor alert, or a submitted work request.
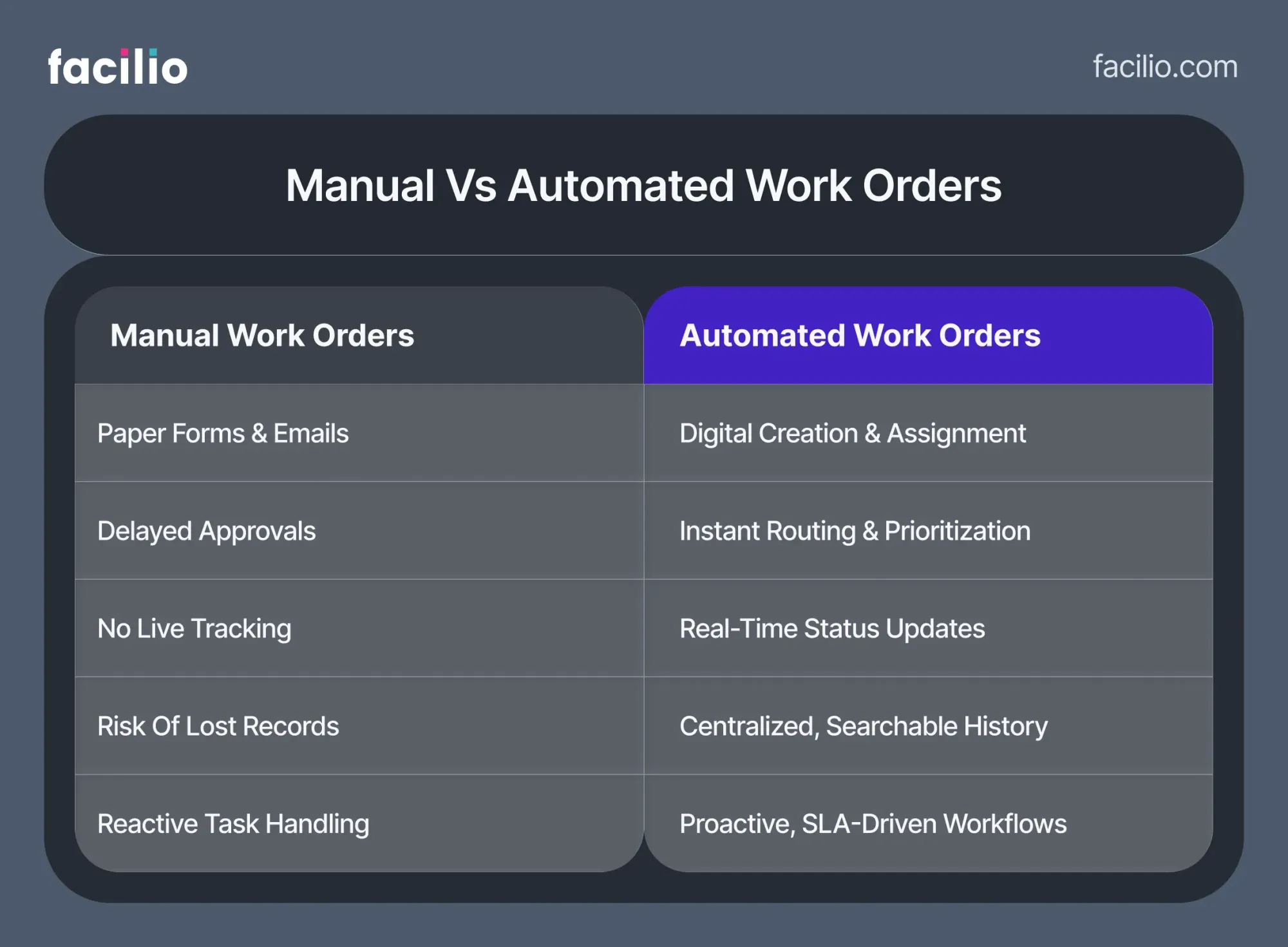
The system then routes the job to the right technician, sets deadlines, and tracks progress in real time.
For facilities, healthcare, manufacturing, and other asset-intensive industries, automation ensures that urgent repairs are handled quickly, preventive tasks aren’t overlooked, and all activity is recorded for compliance and reporting.
By removing manual bottlenecks, automated work orders make operations faster, more accurate, and easier to manage, especially across large or multi-site portfolios.
What are the key benefits of automated work orders?
Switching from manual work order creation to automated work orders delivers clear operational gains:
- Faster turnaround – Jobs are assigned instantly, cutting approval and scheduling delays.
- Reduced errors – Pre-filled templates and standardized workflows remove guesswork and prevent missing details.
- Better prioritization – Automated rules ensure critical tasks are handled first based on SLA requirements, asset criticality, or safety impact.
- Real-time visibility – Managers can track progress live, reassign work when needed, and receive instant status updates.
- Integrated workflows – Links with inventory, asset data, and vendor information to ensure technicians have everything needed to complete the job.
- Stronger compliance – Every step is logged automatically, creating an audit-ready record for inspections and certifications.
Facilio: One connected platform. Every work order. Zero inefficiency.
Most platforms claim to simplify work order management, but in reality, they only digitize existing silos.
Approvals still lag in email chains, updates get lost between systems, and managers spend hours chasing status reports.
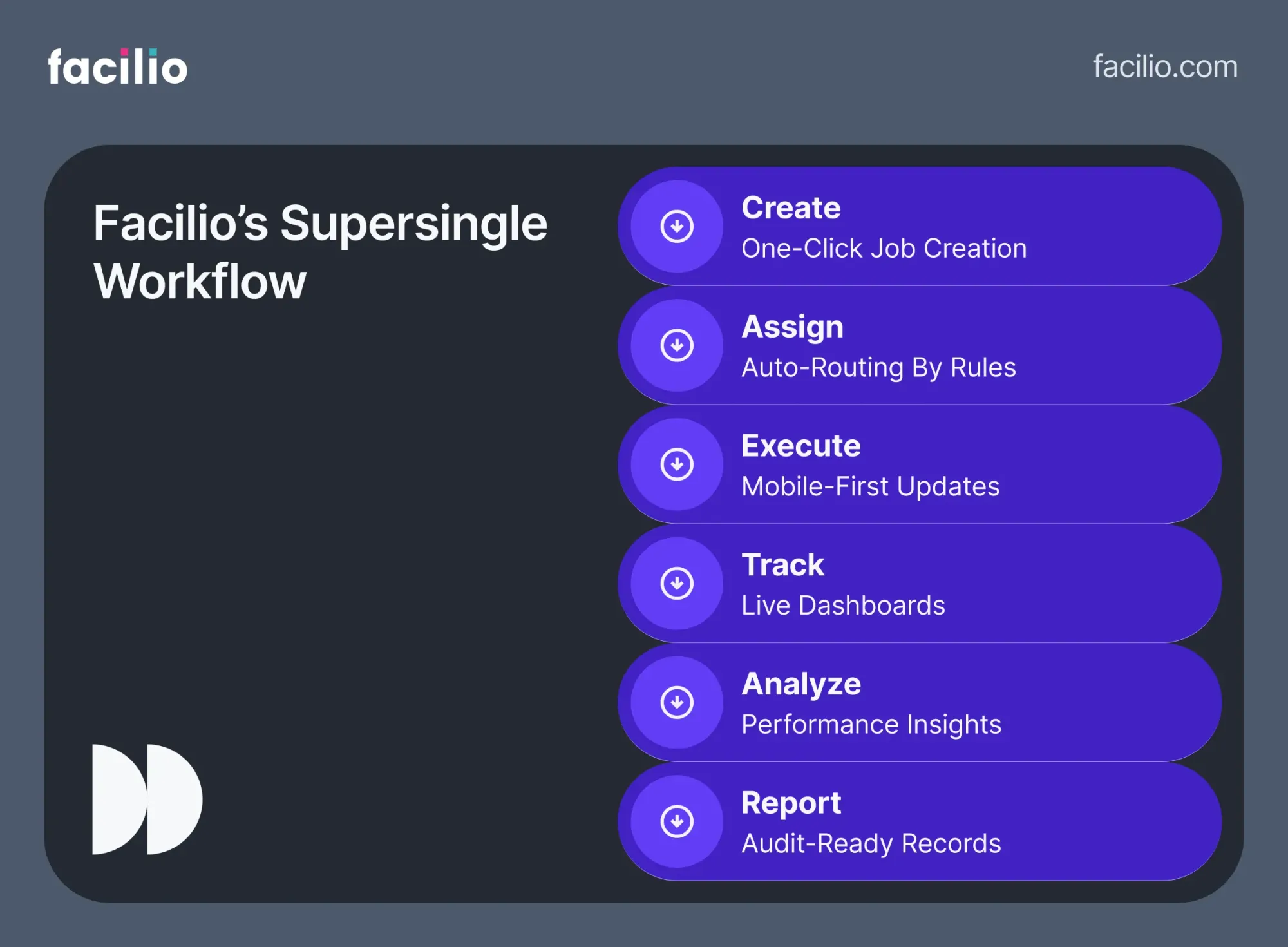
Facilio’s Connected CMMS changes the game with a supersingle work order management flow — every step, from creation to compliance reporting, happens in one platform.
No juggling tools, no duplicate data entry, no blind spots.
Key advantages of Facilio’s Connected CMMS in work order management
- One platform for every job – Create, approve, assign, and close work orders across all sites from a single dashboard.
- Mobile-first execution – Field teams update job status, attach photos, and log time instantly from any device.
- Smart routing & prioritization – Automatically assigns tasks based on SLA rules, asset health, and technician capacity.
- Integration without disruption – Works seamlessly with your existing BMS, ERP, and IoT systems.
- Data-driven decision-making – Turns historical work order trends into insights for preventive planning and budget optimization.
- Audit-ready compliance – Keeps a complete, timestamped record for inspections and certifications.
With Facilio, every work order becomes part of a connected, intelligent process that reduces turnaround times, improves accountability, and drives better maintenance outcomes at scale.
Whether you’re managing one facility or hundreds, it’s the fastest way to move from task chaos to operational clarity.