How to Build a PPM Schedule That Saves Time and Cuts Downtime
Technicians and operatives in a facilities team often find themselves constantly troubleshooting issues that crop up daily. It's no surprise that facility managers prioritize today's problems, even if some tasks could wait.
Reactive maintenance, while necessary for fixing immediate failures or unanticipated issues, comes with a hefty price tag—unscheduled equipment downtime and production losses that quickly add up.
This approach is understandable. Immediate problems need immediate solutions.
However, this reactive stance leaves little room for effectively developing and managing a planned preventive maintenance (PPM) schedule.
Without an effective system in place, the cycle of reactive maintenance continues, perpetuating inefficiency and escalating costs.
Switching to a planned preventative maintenance strategy can break this cycle.
The stakes for integrated facility management service providers (IFMSPs) are even higher. You manage large portfolios and multiple sites, aiming to keep operations smooth for your clients.
Yet, outdated and fragmented CMMS solutions hold your team back. Legacy maintenance software complicates processes, forcing your team back into manual, inflexible and time-consuming routines.
For example, these systems have rigid templates for work orders with limited customization that stifle flexibility, making it difficult to address unique site-specific requirements or changing conditions.
Additionally, the traditional method of generating work orders with the same start dates can create peaks and troughs in workload, leading to burnout during busy periods and idle time during slow ones.
While cost optimization for maintenance management operations is still crucial, IFMSPs now also need comprehensive visibility into maintenance activities, asset health, and sustainability to maintain customer retention in an already highly competitive space.
It also complicates labor and service planning, as teams often estimate needs without detailed insights, leading to either under- or over-staffing.
This inefficiency hinders day-to-day operations and affects their ability to stand out in RFP bids and secure prestigious projects.
In this article, we’ll look into how to create a balanced PPM schedule with advanced software-based solutions and discuss how this can drive better business outcomes.
What is a PPM schedule?
Let’s say you’re a facility manager overseeing HVAC systems across multiple sites in different regions. Additionally, you need to ensure that temperature gauges, fire extinguishers, and sprinkler systems are functioning properly at all locations.
This requires regular inspections, servicing, and repairs at scheduled intervals to catch issues or potential hazards before they escalate.
For FM service providers managing diverse facilities with varying maintenance needs, planned preventative maintenance (PPM) involves a series of well-coordinated activities.
Facilio simplifies this process by allowing the definition of multiple assets or spaces across different sites within the same PPM software. This streamlines maintenance coordination for large or dispersed portfolios and ensures maintained consistency of operations across all sites.
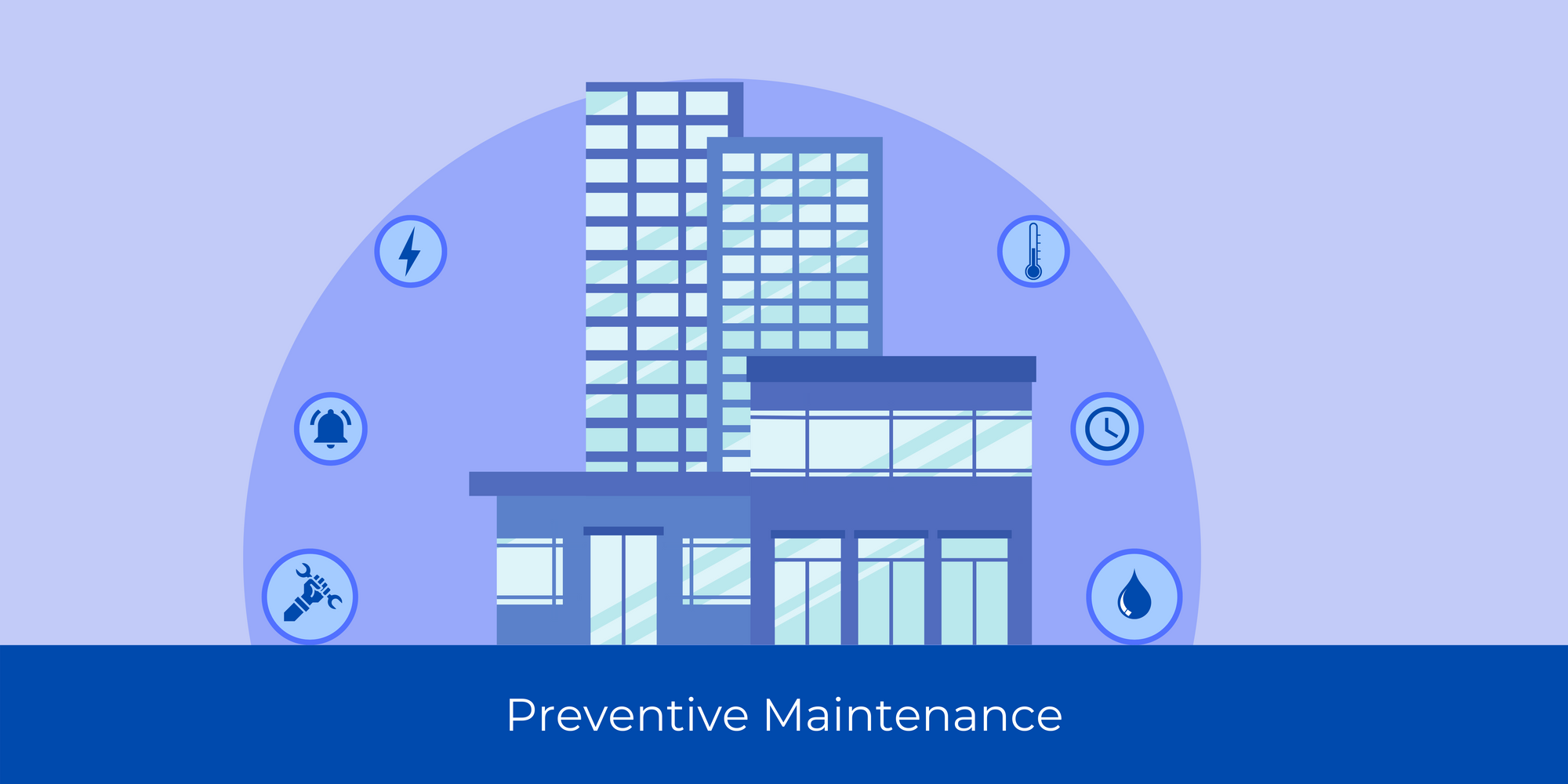
Why is a planned preventive maintenance (PPM) schedule important?
PPM schedules are indispensable in modern facilities management. Here’s why PPM is crucial and how a connected computerized maintenance management system (CMMS) helps.
1. Prolong asset lifespan: With PPM schedules, you can postpone costly asset replacements and reduce major breakdowns. A decrease in the frequency of downtime and breakdowns preserves the life of the equipment over time.
For instance, an IFM company managing multiple corporate office buildings can use such solutions to maintain building elevators. Planned automated scheduling would ensure timely inspections and prevent frequent breakdowns. This, in turn, would reduce frequent downtime logs. The elevators would thus be in good shape during both operational and non-operational periods.
Modern CMMS software offer vast efficiency potential by reducing the need for long travel times to each site via dynamic planning, dispatch, and routing. They also provide remote support networks that enable technicians to troubleshoot issues remotely.
2. Minimized downtime and improved reliability: Scheduling maintenance in advance with a preventive maintenance plan significantly reduces downtime.
Imagine a facilities management provider overseeing HVAC/R maintenance for 5-10 retail buildings in different locations. They struggle with disorganized data and missed inspections because they rely on manual tracking systems and spreadsheets.
An automation-driven, CMMS software could prevent these issues by automating the scheduling of regular HVAC/R maintenance. It can automatically send timely reminders for inspections, tracking spare parts availability in real time, and ensuring maintenance tasks are performed before any costly breakdowns.
Facilio records every problem faced by an asset, the time taken to resolve any issues, and insights on the asset downtime in the form of reports.
Here's how it looks:
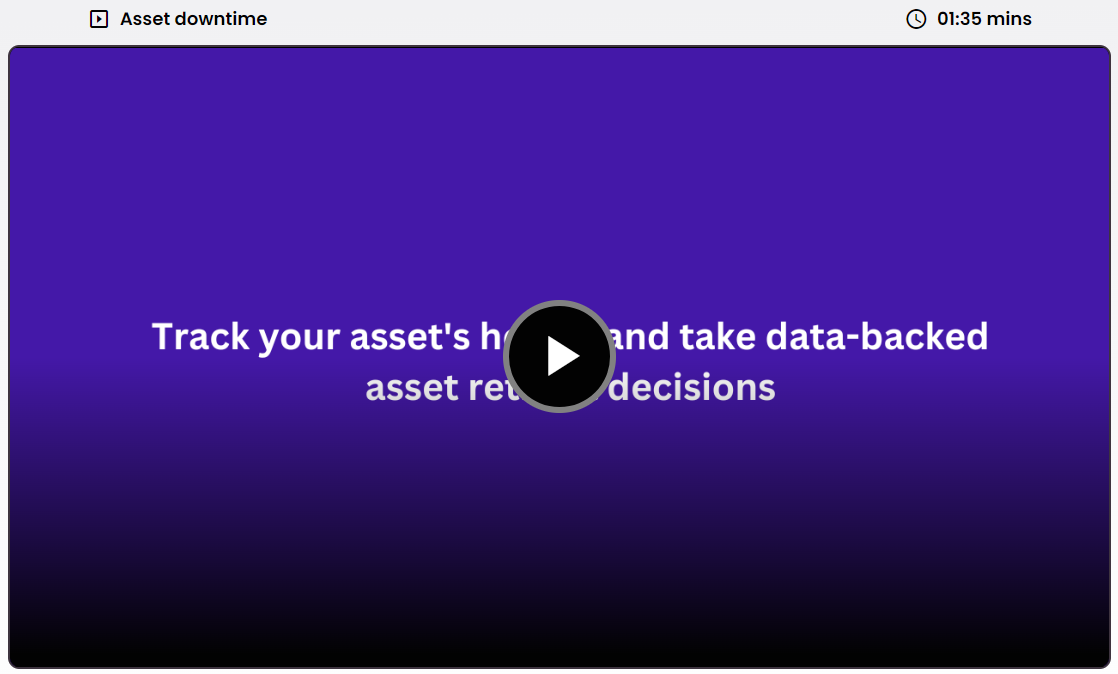
3. Cost efficiency and long-term savings: Preventative maintenance helps FMs identify and fix minor issues before they escalate into major, costly repairs.
This means savings can be directed to other priorities at the institution such as capital renewal or energy reduction projects.
For instance, using data from a PPM system, a company might uncover that scheduling routine maintenance on critical systems like lighting or security reduces overall repair costs.
Modern CMMS solutions provide detailed cost-benefit analyses, ROI reports, financial data to provide insights on opportunities for better cost-cutting and budget optimization
4. Enhanced safety and compliance: Inadequate maintenance compromises safety barriers and increases accident risks, while excessive maintenance may expose personnel to operational hazards.
An optimized PPM schedule maintains the safety and integrity of the process.
In retail, maintaining refrigeration systems is critical. For instance, employees and customers of a major retail chain could face health risks from chemical exposure. The company could also be levied environmental fines for leaks.
Modern CMMS can help ensure compliance with safety regulations and standards by maintaining records of audits, certifications, and safety protocols. It can also schedule inspection and maintenance for regular checks and timely repairs of refrigeration systems.
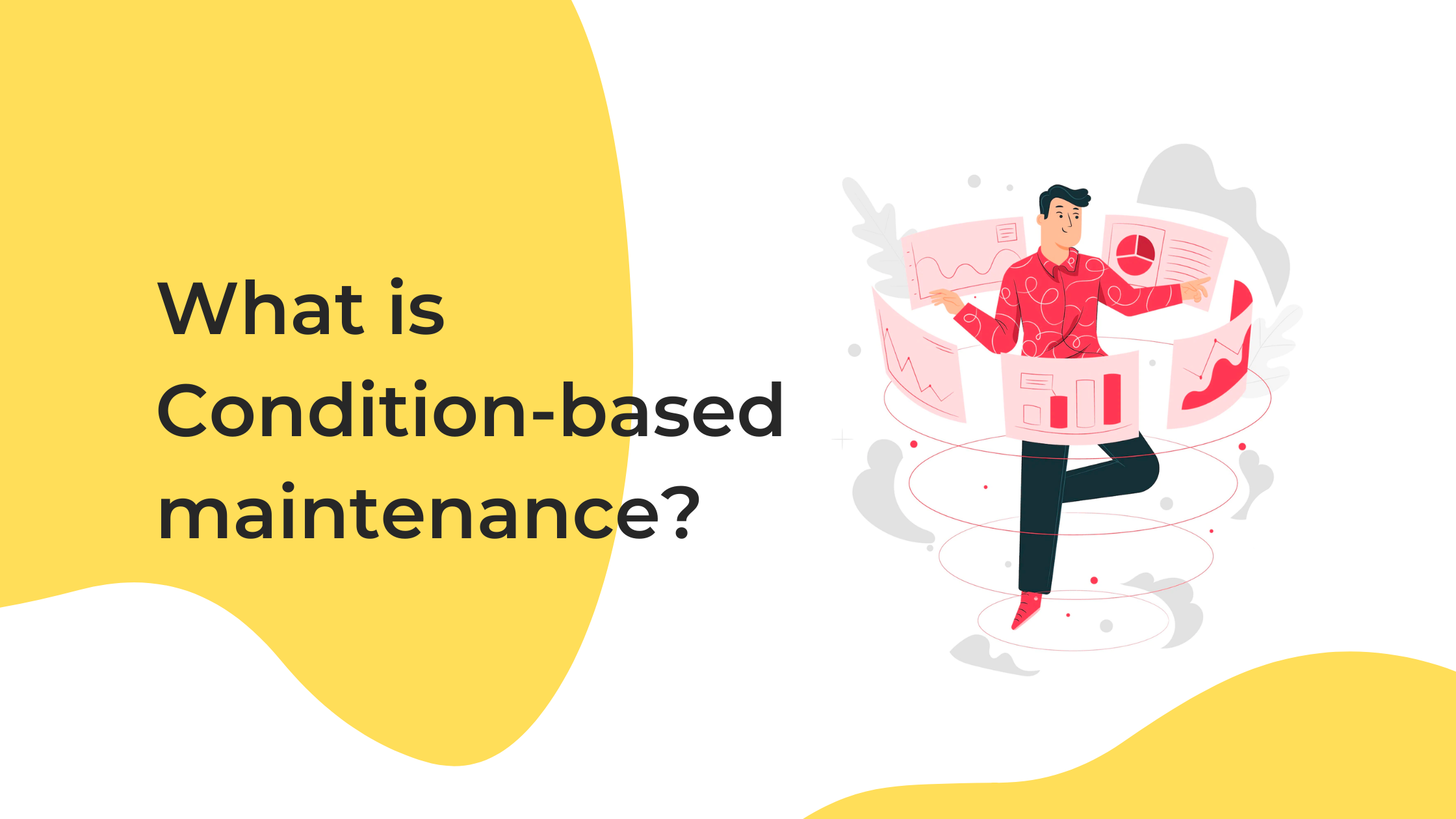
Areas that need PPM scheduling
Facility infrastructure
Everything from electrical systems to plumbing is included here. Well-maintained facilities ensure safety, compliance, and operational efficiency.
Safety and security systems
Regularly maintaining fire alarms, sprinkler systems, and security cameras is essential. PPM activities include system tests, battery replacements, sensor checks, and software updates.
IT and data center equipment
Imagine there’s an IT outage across 20-30 of your facilities that causes severe disruptions and data loss. A PPM schedule includes regular backups, hardware inspections, software updates, and maintenance of cooling systems.
HVAC systems
Your air units failing is not a good sign. But by scheduling filter changes, performance checks, and seasonal maintenance, you can curb productivity losses.
Specialized equipment
Depending on the industry, this could include medical devices, laboratory equipment, or industrial machinery. A PPM schedule for calibration, sterilization of medical equipment, part replacements, and performance checks can improve reliability and avert costly downtime.
Preventive maintenance plan vs. preventive maintenance schedule
It includes objectives, policies, procedures, resources, and key performance indicators (KPIs) for maintenance activities.
In contrast, a PPM schedule is a detailed timeline that specifies when maintenance tasks should be performed on assets. It includes the frequency, specific dates, and assigned personnel for each task.
Here’s a quick look at the major differences between the two:
Both contribute to improved operational efficiency by ensuring assets are well-maintained.
PMP is broad and strategic, focusing on the "what" and "why" of maintenance.
A PPM schedule as tactical, focusing on the "when" and "who" of maintenance. It details the specific timing and personnel for maintenance tasks.
Different types of planned preventive maintenance (PPM) schedules
There are several approaches to scheduling preventive maintenance for your assets, depending on the specific needs of the equipment and the operational preferences of your team. Here’s an overview of the main types:
Six simple steps to creating your PPM schedule
1. Take an inventory of your assets
Start by cataloging your most critical assets, which are the ones whose failure would significantly disrupt operations. Details you need to record:
- Make and model of equipment
- Serial number
- Unit number
- Location/site of assets
- Category
- Primary users
- Parts for each asset.
Use a spreadsheet or your enterprise asset management system (EAM) to keep track.
2. Prioritize your assets
Focus on what matters most first.
One way to achieve this is by calculating each asset's risk priority number (RPN). This simple calculation helps you assess and rank the criticality of each asset.
- Severity: Rated from 1 to 10, where 10 signifies a catastrophic impact on operations. This metric gauges how serious the consequences of a failure would be for your business.
- Occurrence: Assesses the likelihood of failure, with higher scores reflecting greater chances of an asset malfunctioning.
- Detection: Evaluates how easily you can identify a potential issue before it escalates, with higher scores indicating more difficulty in detecting problems.
RPN = Severity ✕ Occurrence ✕ Detection
Once you’ve calculated the RPN for each asset, rank them from highest to lowest. This helps you address the most critical assets first to optimize your maintenance schedule based on their risk.
With the Facilio CMMS software, you can track asset lifecycle movement and real-time performance with static and dynamic parameters presented on intuitive dashboards.
This can help you quickly identify inefficiencies in maintenance processes with detailed reports on metrics about your assets. These insights enable accurate asset classification based on criticality to production and safety.
3. Set predetermined intervals for maintenance
Planned preventative maintenance schedules can sometimes lead to over-inspection, wasting time and resources.
Review historical maintenance data to understand each asset's maintenance needs. This data will highlight past failure patterns and critical components requiring regular attention.
4. Schedule recurring tasks
The simplest way to manage recurring maintenance is through modern CMMS software. It allows you to schedule tasks for each asset and set appropriate maintenance intervals.
Add instruction sets and preventive maintenance checklists for technicians.
An EAM solution like Facilio enables you to generate, assign, track, and store recurring work orders in a centralized, user-friendly platform. Facilio automates short-term and long-term schedules to ensure no maintenance task is overlooked.
5. Assign responsibilities to O&M team
Generate work orders for preventive maintenance tasks and assign them to specific team members based on their expertise and availability.
Using maintenance software, you can set up automated approval workflows, incorporate detailed checklists for each maintenance task within the software, and monitor the status of each maintenance task in real time, from initiation to completion.
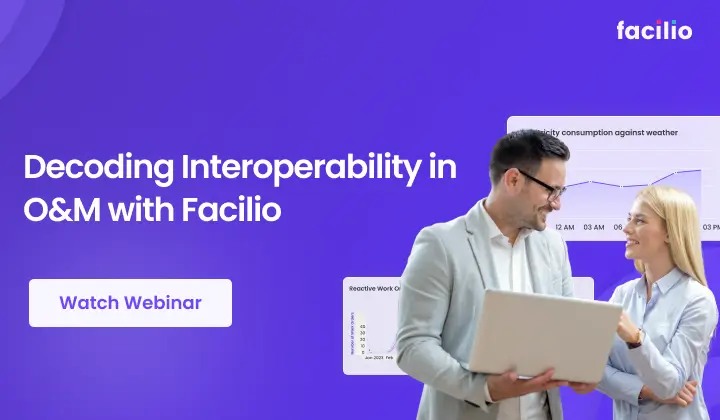
6. Monitor, review, and tweak your schedule
After setting up your preventive maintenance schedule, monitor its effectiveness. Adjust inspection timelines or increase maintenance frequency as needed.
Track maintenance metrics like the following:
Using preventive maintenance software to oversee PPM schedules
Most enterprises and large multi-site operators are stuck in a maintenance rut. Facility managers are relying on spreadsheets, legacy CMMS, and fragmented tech to keep things running.
You might think investing in PPM software is unnecessary or overly complex for your needs. Or that your current system, though imperfect, is sufficient.
It’s a myth that an IT-led and AI-driven solution will not provide a significant return on investment.
We understand why you find comfort in familiar patterns and systems. However, this habitual reliance on manual or reactive maintenance leads to a host of hidden costs and operational disruptions.
Why PPM software is better
Preventative maintenance software represents a fundamental shift in how maintenance is managed.
It goes beyond providing an alternative method within the same old framework. It redefines and evolves into a proactive, efficient, and cost-effective system.
How Facilio enables you to create PPM schedules
Here’s how an automation-driven CMMS software like Facilio can help with intelligent and contextual PPM scheduling:
Facilio adopts a platform-based approach that enhances building O&M management at the portfolio level.
As a cloud-based CMMS software, this connected operations platform enables customers to fill gaps in their tech stack easily, derive immediate value, and transition from isolated point solutions to cohesive, interoperable modules.
Facilio seamlessly integrates all maintenance operations, including corrective, reactive, and breakdown-related tasks, scheduled inspections, routine preventive maintenance, and audits.
PPM with Facilio
Customizable data collection with custom fields
Facility managers can tailor data collection and reporting to their specific needs, with custom fields for planned work orders.
You can also automate task allocation and assign repair or replacement jobs to the appropriate technicians based on their availability and current inventory status.
Enhanced coordination and oversight with centralized PPM templates
Instead of juggling separate maintenance schedules for different sites, facility managers can define and manage multiple assets or spaces within the same PPM software.
Facilio's PPM templates allow facility managers to centralize and streamline schedules across multiple sites.
Let’s say you’re an internet service provider with 5-9 buildings seeking a comprehensive CMMS solution to manage assets, set up PPM maintenance schedules, and track environmental sustainability metrics.
Using PPM templates, you can get ahead of your maintenance tasks, leading to reduced downtime and enhanced operational efficiency.
Tailored maintenance schedules with multiple frequencies
Uniform maintenance frequencies for all assets often result in inefficiencies.
Facilio allows for the customization of maintenance intervals for each asset or space, ensuring each receives the appropriate level of attention based on its unique needs.
With this, optimized asset performance and lifespan are achieved, reducing unnecessary maintenance activities and associated costs.
Reduced manual work with automated vendor mapping
Manual vendor assignments are error-prone and time-consuming.
Facilio's automation workflows map vendors to services, streamlining the process and reducing potential mistakes. This automation cuts down on administrative work and frees up time and resources for other maintenance operations.
Detailed job planning
Generic maintenance plans miss important details. Static plans can quickly become outdated.
Facilio's dynamic and detailed plans cover everything from tasks and parts to labor, ensuring nothing slips through the cracks.
Facilio lets you keep your plans up-to-date, so your maintenance team always knows what to do. Well-planned maintenance leads to better results.
Balanced workloads with staggered start dates
Facilio lets you generate work orders for different assets at different times, spreading out the workload.
This prevents staff burnout, ensures consistent coverage, and stops bottlenecks from slowing you down.
Proactive resource management with planned inventory management
Reactive inventory management causes delays and increased costs.
Facilio's system ensures that all materials needed for work orders are scheduled in advance. This proactive approach prevents work stoppages, reduces emergency procurement costs, and ensures timely maintenance execution.
Why choose Facilio
- Quick deployment: Facilio’s platform-based architecture is designed for speedy implementation, allowing for deployment in just 6 to 15 weeks, depending on the portfolio size and complexity. This starkly contrasts the years-long implementations often required by other solutions.
- Open API: With Facilio’s open API, you can seamlessly integrate the software with your current facility management tools. This means you can retain valuable modules from your old solutions while adding new capabilities from Facilio, effectively filling gaps and enhancing overall functionality.
- Adaptable modules: Facilio offers modular solutions that are easily configurable. You can quickly add or remove modules to suit your changing needs without disrupting existing workflows.
- Unified data: All data from integrated systems flow into Facilio, creating a single source of truth. This unified data architecture ensures that all information is readily available and easily accessible, enhancing decision-making and operational efficiency.
Managing preventive maintenance the old-fashioned way is no longer ideal.
How to improve your service quality with tech that gives you a competitive edge
Service quality is crucial for IFMSPs to attract and retain clients. Outdated systems exacerbate issues like customer churn, hindering efficient maintenance planning.
Additionally, setting up planned preventative maintenance schedules within these legacy systems is overly complex. The lack of automation and monitoring capabilities results in missed opportunities to optimize operations, causing significant inefficiencies.
That’s where the Facilio CMMS comes in.
By centralizing data, automating tasks, and providing real-time insights, Facilio helps IFMSPs deliver exceptional service, increase productivity, reduce operational costs, and gain a competitive edge.
In the CMMS, define the maintenance tasks and input your task information; make sure to include details like location, who’s responsible, and the materials needed.
Don’t forget to set up automatic reminders so that tasks are completed on time. You can also generate reports on the maintenance activities to identify areas for improvement.
Explore how Facilio can support you as an IFM provider in setting up PPM schedules and managing other facility-related issues with its connected CMMS.
FAQs
1. What is PPM in maintenance?
PPM stands for Planned Preventive Maintenance—a proactive approach where equipment is regularly inspected and serviced before failures occur. It reduces downtime, lowers repair costs, and extends asset life by addressing issues before they become disruptions.
2. What is the meaning of a PPM schedule?
A PPM schedule is a structured plan that outlines when preventive maintenance tasks should be carried out.
It includes recurring inspections, servicing, and minor repairs at set intervals—whether time-based, usage-based, or condition-based—to ensure equipment stays operational and compliant.
3. What is a PPM checklist?
A PPM checklist is a detailed list of maintenance tasks assigned to a specific asset or system.
It outlines what needs to be inspected, cleaned, tested, or replaced during each service. Using a checklist ensures consistency, minimizes missed steps, and helps technicians complete preventive maintenance to standard every time.
4. How do you prepare a PPM schedule?
Preparing a Planned Preventive Maintenance (PPM) schedule involves five essential steps:
- Document your assets – Identify which equipment requires regular servicing.
- Prioritise tasks – Focus on high-risk or business-critical assets.
- Set service intervals – Use OEM data, asset usage, and past issues.
- Plan recurring tasks – Schedule activities in advance using a CMMS or digital calendar.
- Review and adjust – Refine based on performance, feedback, or evolving needs.