From reducing downtime to ensuring safety, facility maintenance plays a crucial role in operations. Here's how to do it right, backed by real use cases.
Say, you’re overseeing multiple sites across geographies, tracking asset performance, maintenance history, and tenant concerns. The complexity of your facilities grows as you juggle multiple maintenance schedules.
Everything from a missed deadline on a work order to your HVAC systems malfunctioning impacts operational costs, tenant retention, client satisfaction, and overall productivity.
Your current systems are overwhelmed, making it difficult to get a consolidated view of asset performance across sites. Despite your best efforts, you’re constantly firefighting issues rather than proactively managing them.
While optimizing for costs remains a priority, portfolio-wide visibility into maintenance activities, asset health, sustainability, and churn are now under the purview of O&M teams.
Facility maintenance has, therefore, evolved from a mere operational necessity to a strategic business asset. And, legacy computerized maintenance management systems (CMMS) are not up to the challenge.
The need for a future-proof approach to facility maintenance becomes clear. Modern, connected CMMS solutions are emerging as essential tools in O&M, offering operational visibility and seamless communication for everybody—from technicians to executives.
Let’s explore what facility maintenance is and why it’s important, understand some best practices for measuring maintenance KPIs, and learn through case studies how a modern CMMS eliminates the friction in facility maintenance.
What is facility maintenance?
Whether the space is a factory, office, hospital, shopping mall, or school, facility managers make sure the building and all of its components are working properly.
Each site has unique maintenance needs, schedules, and compliance requirements. Without efficient technology, coordinating these tasks becomes a logistical nightmare.
Technicians might be dispatched to the wrong location, maintenance schedules could overlap or be missed, and data silos might prevent a clear view of overall operations. This leads to missed deadlines, increased asset downtime, high operational costs, and high customer churn.
By leveraging a connected CMMS, facility managers and their O&M teams can spend more time on strategic planning than on recurring and manual tasks.
Three key components of facility maintenance
Facility maintenance is a comprehensive practice that can be broken down into three components: inspections, repair, and maintenance.
1. Inspections
These are the frontline defense against equipment failure and system breakdowns. It involves regular checks to identify potential issues before they escalate into major problems.
There are three kinds of inspection to detect deterioration and failure of a facility’s asset:
To select an appropriate inspection method, we need to consider the following factors:
- Interconnected failures: Addressing one issue can prevent others. For example, early detection of a small issue, like an oil leak, can prevent widespread mechanical breakdowns.
- Accuracy of results: An inspection method’s effectiveness depends on the tools used, the inspectors' skill, and, more importantly, the timing of inspections.
- Cost-effectiveness: Balancing the incurred cost of inspections ( e.g., labor, equipment, disruptions) against the benefits, like preventing larger repairs, is important.

2. Repair
The nature of the asset failure determines the extent of necessary repairs, typically categorized into two types:
- Complete failure: This type of failure renders the asset unusable until it is repaired. For example, if a production line's conveyor belt snaps, the entire line halts until the belt is replaced. Unplanned downtime due to such failures is costly and requires immediate attention.
- Partial failure: The equipment may still operate but with reduced efficiency or increased risk. For example, a building's elevator system may continue to function despite a failing motor that causes irregular stops and starts. While the elevator can still transport passengers, the failure affects efficiency and can pose safety risks.
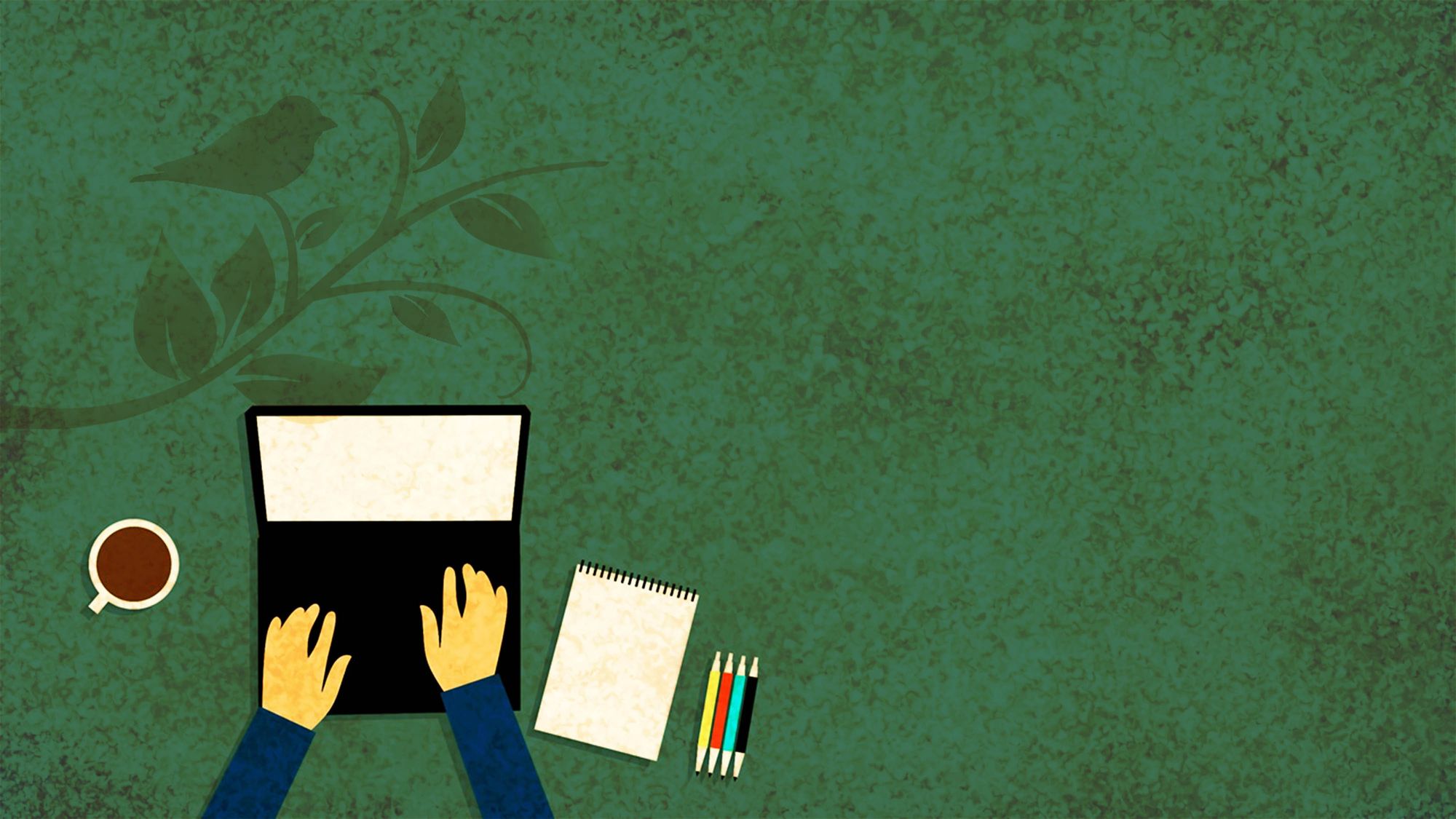
3. Maintenance
This involves ongoing routine tasks aimed at keeping systems and equipment in optimal working conditions and operations running smoothly.
It encompasses all procedures necessary to preserve the initial condition of assets or systems and maintain their functionality throughout their entire lifecycle.
Key aspects of maintenance
- Cost avoidance: Functional failure as a result of low quality maintenance means great effort and cost including direct losses in productivity, sales, and increased downtime.
Unplanned downtime costs Fortune Global 500 companies 11% of their yearly turnover—nearly $1.5 trillion, up from $864 billion (8% of turnover) about four years ago. Costs vary significantly by sector, with lost hours averaging $39,000 in Fast-Moving Consumer Goods factories and exceeding $2 million per hour in the Automotive industry.
Immediate repairs often come at a higher expense. Regular maintenance can help minimize downtime and mitigating these costs. - Warranties and guarantees: Extended warranties function similarly to service contracts. The contract's terms can vary and may include corrective and/or preventive maintenance actions.
If a business neglects to maintain an asset, it risks losing warranty coverage. Keeping these warranty contracts valid can help put the burden of costs of repair and replacements on the manufacturer.
Following a structured O&M manual can help you stay on top of compliance with maintenance schedules to keep your warranties intact. - Forecast equipment mishaps: While preventive maintenance—scheduling regular maintenance to prevent breakdowns—is prevalent in facility management, predictive maintenance takes it a step further.
Predictive maintenance utilizes data and analytics to forecast potential failures based on real-time equipment data. According to a Deloitte study, predictive maintenance can increase productivity by 25% and decrease unplanned outages by 70%.
The aim of maintenance work is to delay the wear and tear of objects, systems or technical equipment.
Certifications for facility professionals
Facility managers ensure that organizational spaces are comfortable, sustainable, efficient, and safe. They drive operational excellence and sustainability within diverse environments and contribute to a company’s strategy and bottom line.
A set of core competencies is required for personnel performing facility management, energy management, building operations, and maintenance functions.
In addition, facility managers need to have the relevant certifications, degrees, registrations, and licenses to stay compliant with these core competencies.
Facility Management Professional (FMP)
The FMP certification, offered by the International Facility Management Association (IFMA), is a must-have for entry-level and transitioning facility management professionals, and it includes finance and business, O&M, leadership and strategy, and project management modules.
Individuals at any stage of their careers can use this to strengthen their knowledge of core facility management topics.
Certified Facility Manager (CFM)
The IFMA also offers the CFM certification for facility professionals looking to validate their expertise in managing facilities across a range of disciplines. It is ideal for seasoned facility managers with at least five years of experience.
LEED
The LEED certification provides a framework for building owners and operators to identify and implement practical and measurable green building design, construction, and O&M solutions.
Offered by the U.S. Green Building Council (USGBC), the LEED certification is for facility managers, architects, engineers, and professionals who establish sustainable practices and comply with environmental regulations.
With over 36,835 projects certified between 2017 and 2021, it's clear that more managers are prioritizing sustainability and environmental standards in their projects.
ASHRAE Certifications
The American Society of Heating, Refrigerating, and Air Conditioning Engineers (ASHRAE) offers several certifications for professionals in HVAC systems and energy management.
Certified Energy Manager (CEM)
This certification is offered by the Association of Energy Engineers (AEE)—ASHRAE is a partner organization. It is for facility managers and professionals focused on optimizing energy use and improving energy efficiency.
It enhances career prospects in facility management by validating expertise in energy management and helping professionals advance into roles focused on energy auditing, management, and consulting.
ISO and other standards
The International Organization for Standardization (ISO) committee develops globally recognized guidelines and frameworks to ensure quality, safety, efficiency, and environmental sustainability across various industries.
For instance, ISO/TC 251 provides best practices for effective asset management, while ISO/TC 205 focuses on standards for indoor environmental conditions, including thermal performance, air quality, and energy efficiency.
In addition to ISO standards, there are industry-specific standards like NFPA 99, which ensures medical facilities comply with safety and fire protection compliance regulations at local, state, and federal levels.
Organizations that implement ISO standards can seek certification from accredited third-party bodies through an audit process, verifying adherence to these rigorous requirements.
For further resources and professional development in facility management, explore the Facilities Management Institute launched by the U.S. General Service Administration.
This institute promotes collaboration and continuous education between public and private sectors in the facility management community, supporting the development of the profession.
Why is facility maintenance important?
Over time, assets and equipment experience wear and tear, leading to unexpected breakdowns and higher operating costs.
Effective maintenance helps prevent costly breakdowns, extends the lifespan of equipment, ensures compliance with safety regulations, and enhances the overall workplace environment. It directly impacts productivity, safety, and occupant satisfaction.
Here’s why facility maintenance should take top priority:
1. Affordable upkeep to prevent major breakdowns
Regular preventive maintenance is an economical way to avoid expensive breakdowns. Routine checks and timely repairs prevent small issues from escalating into costly outages. For instance, replacing a worn-out HVAC filter on schedule prevents system failure during peak usage, avoiding expensive emergency fixes and downtime.
2. Keeping property value intact
Regular maintenance of a commercial property’s exterior prevents deterioration, maintaining curb appeal and financial market value. Properties that adhere to current safety and building codes are more likely to meet buyer or tenant expectations and achieve higher market value.
3. Structured timelines and responsibilities for effective management
Effective maintenance management ensures everyone knows their roles and tasks are completed on time. The preset maintenance schedule ensures that no aspect of maintenance is overlooked. For instance, a detailed maintenance calendar helps teams plan tasks and avoid conflicts, leading to more organized and efficient operations.
4. Enhanced facility security with routine upkeep
Maintenance acts as a safeguard for facility assets, protecting them from damage and ensuring longevity. This prevents potential hazards and preserves the integrity of equipment and infrastructure. Routine maintenance checks on electrical systems can prevent dangerous malfunctions and ensure compliance with safety regulations.
5. Benchmarking for better performance evaluation
Establishing a baseline through regular maintenance helps in evaluating performance and identifying areas for improvement. It provides a reference point to measure the effectiveness of maintenance strategies and operational efficiency.
But what happens when proactive facility maintenance isn’t given the required attention?
You would run into issues like:
- Higher maintenance expenses, where repairs become more frequent, leading to higher costs and potential revenue loss
- Escalated energy consumption as the facility will likely see higher energy bills and contribute to greater carbon emissions—The International Energy Agency (IEA) projects that to achieve net-zero by 2050, direct CO2 emissions from buildings need to be reduced by 50%.
Poor quality maintenance can lead to non-compliance with ESG requirements and potential fines, while also damaging the organization’s reputation. - Missed data opportunities as research shows that 95.5% of data captured in engineering and construction goes unused.
Not leveraging data for predictive maintenance and decision-making means missing out on opportunities to optimize building performance and reduce operational costs
Despite knowing how important facility maintenance is, IFMSPs face the challenge of being stuck with systems that hamper their ability to optimize maintenance operations.
The challenge: Legacy CMMS and its limitations
As facility management evolves, O&M roles are increasingly tied to strategic decision-making and effective communication.
Currently, facility managers and their teams are expected to use performance evaluation metrics to track success, guide their strategic decisions, and align stakeholder goals.
Unfortunately, legacy CMMS are rarely built for end-to-end digitization, and hence create data silos at every level. This lack of visibility and collaboration makes it challenging to operate efficiently.
A significant portion of time is spent on tools outside the CMMS—our recent webinar revealed that 47% of the audience reported their teams spend more than four hours per week using external tools.
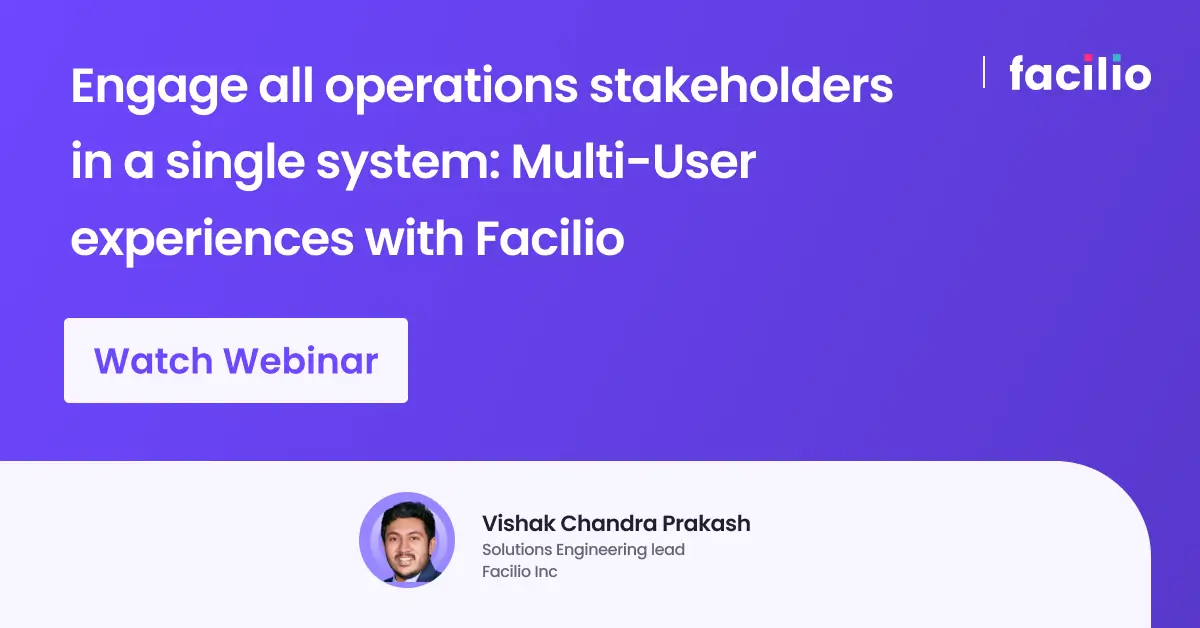
This leads to a fragmented approach, where various point solutions are used to cover up lapses.
Facility managers are left with scattered data and disconnected tools, which complicate operations and often result in inconsistencies and errors. The administrative burden increases, straining in-house IT resources and causing operational delays.
The lack of integrated functionality also makes maintaining a cohesive strategy across multi-site portfolios difficult. This can lead to potential deviations from long-term maintenance objectives and increase the risk of compliance issues and unplanned expenditures.
These systems hamper operational efficiency and undermine the reliability needed for optimal facility maintenance.
The need for a unified solution
A connected CMMS addresses these issues by offering a unified platform that centralizes various functionalities, simplifies operations and reduces administrative overhead.
This integrated system minimizes data inconsistencies and lowers overall costs while providing operations leaders enhanced visibility and control.
A connected CMMS facilitates smoother records, more effective communication, and accurate data management by bringing processes, stakeholders, and tools together in a single space.
With a connected CMMS, maintenance strategies can shift from less reactive maintenance measures to efficient, proactive ones.
The philosophy of facility maintenance is built on the principle of proactive care.
This proactive approach is grounded in the science of reliability engineering, which uses data and analytics to predict failures and optimize facility maintenance schedules.
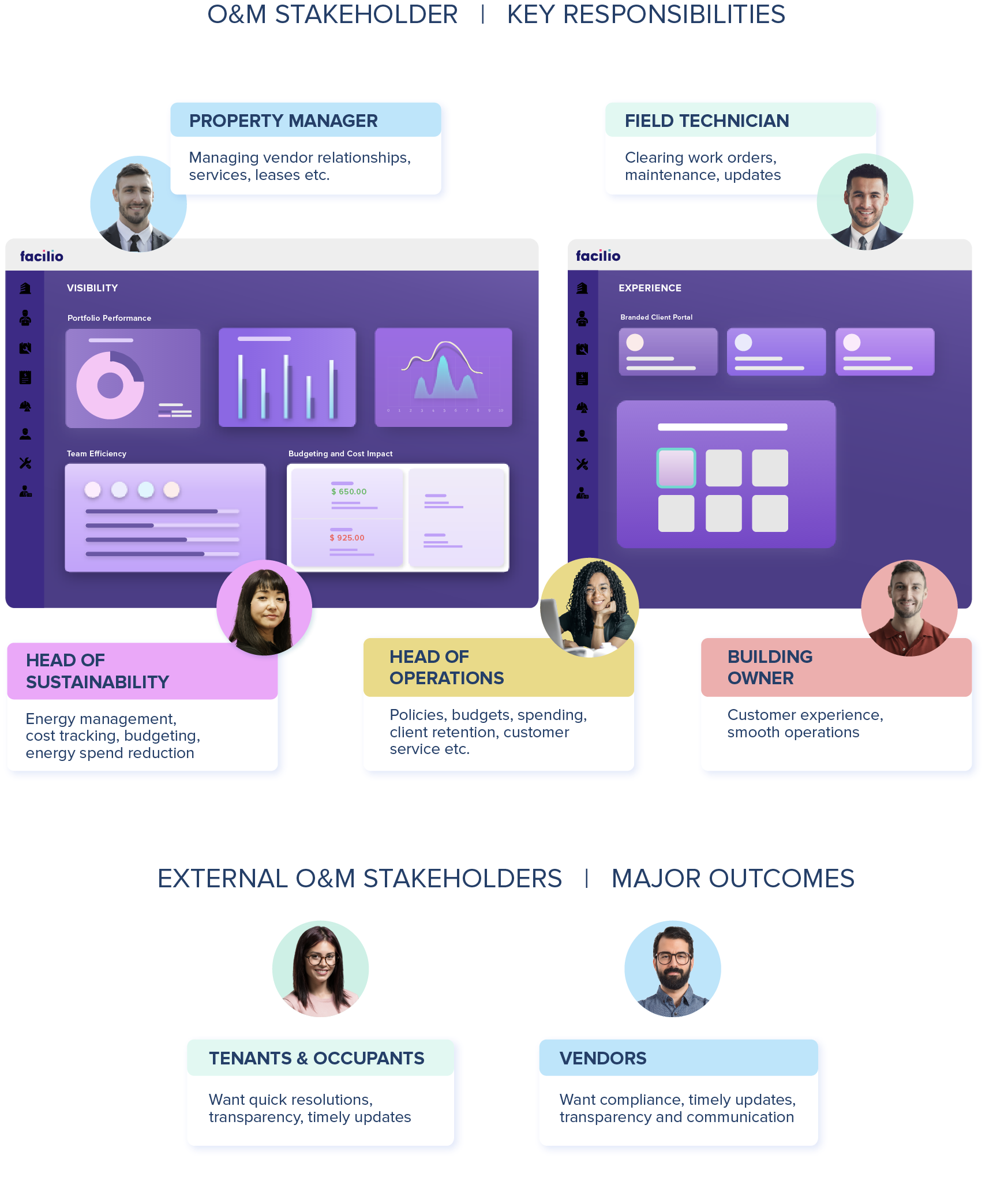
Three types of facility maintenance
1. Corrective maintenance: Focuses on fixing equipment after it fails, either planned or unplanned. It addresses immediate issues but can lead to costly and disruptive downtime.
2. Preventive maintenance: Involves regular, scheduled tasks like inspections and replacements to prevent equipment failures, extending asset lifespan and improving operational efficiency.
3. Predictive maintenance: Uses real-time data and advanced monitoring to predict failures before they occur, optimizing maintenance and reducing unexpected downtime, though it requires high upfront costs for setup.
Measuring success in facility maintenance: essential KPIs to track
While general metrics can provide a broad view of various aspects of facility operations, they don’t always help make informed decisions.
On the other hand, maintenance KPIs are a specific type of metric loosely tied to an organization’s goals and offer crucial information for making better decisions.
Tracking facility management KPIs gives insight into how effectively your facility operates, helping organizations refine their maintenance programs.
Some major KPIs include:
Mean Time Between Failures (MTBF)
Measures the average time between consecutive equipment failures, providing insight into the reliability and longevity of assets.
MTBF = Total Operating Time/Number of Failures
Mean Time to Repair (MTTR)
Calculates the average time taken to complete repairs from the moment a failure is reported until the asset is restored to operational status.
MTTR= Total Repair Time/Number of Repairs
First-time Fix Rate (FTFR):
Tracks the percentage of maintenance issues resolved on the first visit, indicating the effectiveness and efficiency of maintenance personnel. A high first-time fix rate signifies efficient problem-solving and reduced repeat visits.
FTFR= (Number of Issues Resolved on First Visit)/(Total Number of Issues) * 100%
Overall Equipment Effectiveness (OEE)
Measures the efficiency of equipment by combining factors of availability, performance, and quality. It provides a comprehensive view of how well equipment is utilized.
OEE= (Availability) * (Performance) * (Quality
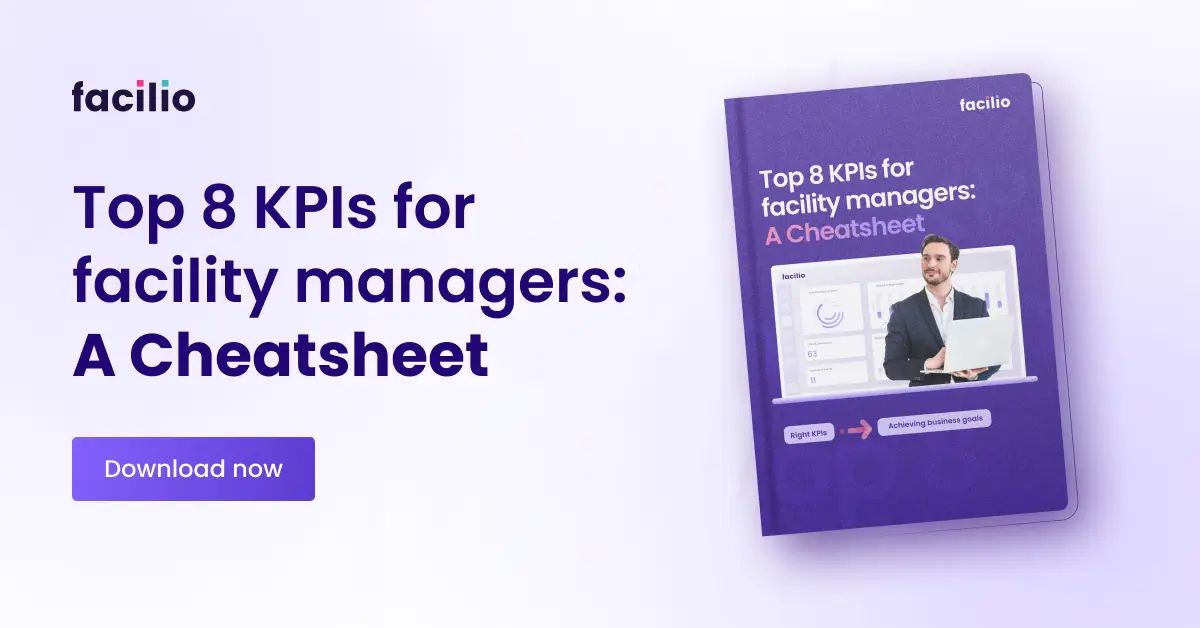
Best practices for measuring facility maintenance performance
1. Data collection and analysis: Gather data on equipment availability, MTBF, MTTR, and maintenance costs. This information helps identify areas for improvement in equipment reliability and efficiency.
2. Stakeholder feedback: Conduct surveys or interviews with employees, customers, and other stakeholders to gauge satisfaction with maintenance services and identify areas for enhancement.
3. Safety monitoring: Track the frequency and severity of accidents or injuries among maintenance staff to ensure a safe working environment.
4. Audits and inspections: Regularly inspect and audit maintenance activities to assess quality and identify deficiencies.
5. Benchmarking: Compare your performance against industry standards to identify gaps and set realistic improvement targets.
6. Periodic KPI reassessment: Regularly review and update KPIs to ensure they remain relevant to your evolving business goals and technological advancements.
Leveraging advanced technology for KPI tracking
One of the most effective ways to track and monitor KPIs is by using a CMMS solution. However, legacy CMMS lacks real-time data integration and advanced analytics capabilities.
They’re not designed for portfolio-wide visibility, not interoperable, not automatable, not scalable, and not customizable.
A connected CMMS is not just another alternative. It uses an IoT-based model to gather real-time data for predictive and condition-based maintenance KPIs.
It also presents KPI data in an accessible and understandable format, such as dashboards or visual reports tailored to different stakeholders.
This allows for detailed technical insights for O&M teams and high-level summaries for executives. Additionally, it establishes a feedback loop where insights from KPI analysis can guide future facility maintenance strategies and decision-making.
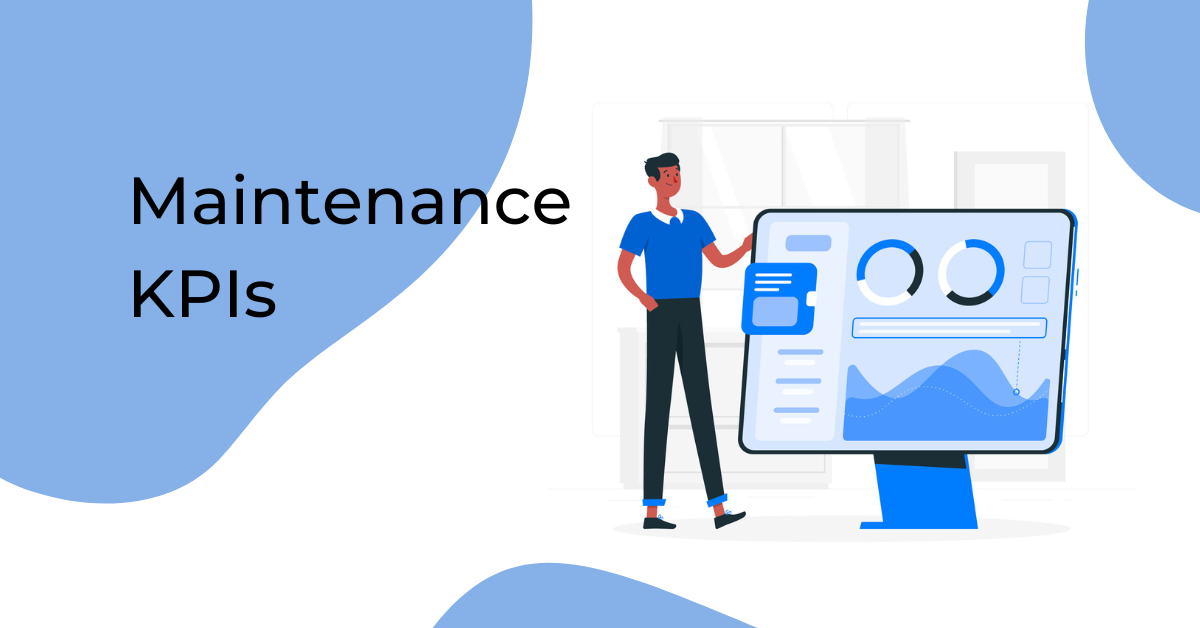
Facility maintenance strategies FMs swear by
As facility maintenance strategies evolve, so does the role of facility and operations teams. No longer confined to being mere cost centers or reactive problem-solvers, these teams have become central to driving strategic business outcomes.
Their responsibilities now extend well beyond just maintaining equipment and handling emergencies. They are at the forefront of integrating data-driven solutions that enhance overall business efficiency. The strategic look into what FM is, is changing to become more data-driven and focusing on adding value rather than just cost reduction.
Research shows that FM now contributes to business profitability by offering crucial support services, optimizing energy performance, and improving operational strategies to cut energy usage in buildings.
With tools like connected CMMS, advanced analytics, and IoT technology, teams leverage real-time data to anticipate issues, optimize operations, and prevent disruptions.
This forward-thinking, data-driven approach transforms facility teams into key players in driving organizational success.
Effective facility maintenance strategies blend proactive measures with advanced technology. You might opt for a 'run-to-failure-then-fix' strategy for non-critical assets where the cost of downtime is relatively low.
Alternatively, implementing a preventive maintenance plan ensures that routine inspections and repairs are scheduled to prevent equipment failures. Additionally, utilizing technology for predictive maintenance allows leveraging real-time data and analytics to anticipate and address issues before they occur.
An effective facility management strategy incorporates clear goals, comprehensive assessments, proactive maintenance, and technology solutions.
Hence, the renewed focus on reliability-centered maintenance (RCM) as the next evolving step in the right direction:
Reliability-centered maintenance (RCM): Evolving facility maintenance strategy
It focuses on ensuring assets function reliably by identifying potential failure modes and developing targeted maintenance strategies. This comprehensive approach combines preventive, predictive, and run-to-failure strategies.
This strategy identifies frequently attended equipment through regular inspection, data-driven analysis, and predictive diagnostics.
A well-planned RCM accurately predicts necessary replacements, preventing costly equipment failures and avoiding production run surprises.
Successfully implemented RCM strategies also depend on regularly well-trained maintenance personnel skilled in failure modes effects analysis (FMEA), fault tree analysis (FTA) and risk prioritization.
For a closer look at how leading organizations are leveraging RCM to boost operational efficiency, see how it works in practice here,
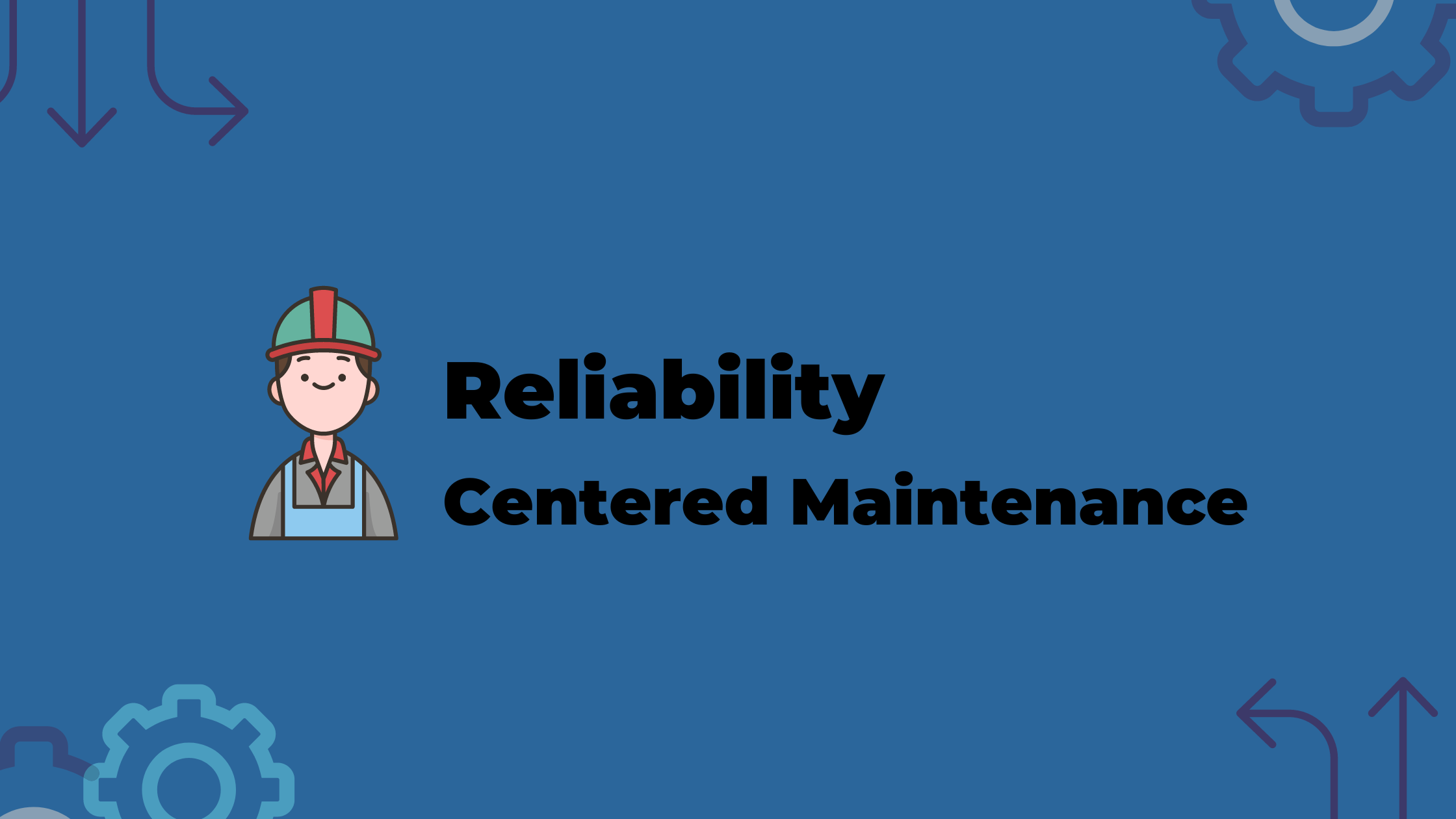
Facility maintenance management tools
- Facilio
- ServiceChannel
- Hippo CMMS
- Brightly Asset Essentials
- FMX
1. Facilio
Facilio is designed with a platform-first philosophy, allowing customers to manage their entire portfolio operations from a unified platform rather than juggling multiple point solutions.
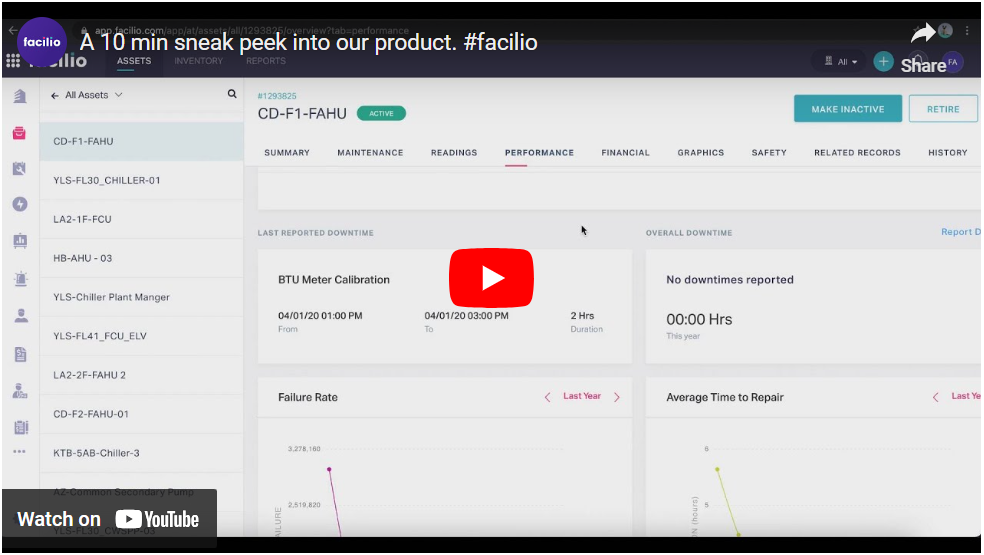
This cloud-based connected operations platform seamlessly integrates with existing tech stacks, delivering immediate value and helps IFMSPs eventually transition from point solutions to seamless, interoperable modules.
Its platform architecture helps you manage all facilities and operations from a unified platform, gives you 360-degree visibility into your operations, balances proactive and reactive maintenance to reduce downtime and optimize resources, and gives you real-time ops and growth insights.
As you now know one of the most critical tools your O&M teams need to have for smoother maintenance and portfolio operations is a centralized, data-driven facility maintenance software like Facilio.
It offers sophisticated features that make managing multi-site facilities more efficient and effective. It not only streamline maintenance tasks but also provide valuable insights into asset performance and maintenance schedules.
How IFMSPs can optimize facility maintenance with Facilio
Centralized helpdesk and self-service solutions
Imagine your facility maintenance team using Facilio's centralized help desk to streamline issue reporting.
Instead of juggling emails and phone calls, all requests are funneled through a single platform, where priority-based routing ensures that urgent issues, like HVAC malfunctions or security concerns, are addressed immediately.
This not only speeds up response times but also keeps all stakeholders—clients, contractors, or internal teams—in the loop with broadcasts and announcements.
This setup reduces response times and enhances the overall user experience, improving operational efficiency and customer satisfaction.
Streamlined inspections and audits: reducing compliance risks
For IFMSPs overseeing multi-site enterprise facilities, compliance is non-negotiable and hard to keep up with. Facilio transforms how your team handles inspections and audits by digitizing processes that are traditionally manual and error-prone.
For example, technicians can use mobile apps to complete SFG20 checklists on-site, instantly flagging non-compliance issues. This immediate feedback loop allows for quick corrective actions, reducing the risk of regulatory breaches.
Customizable inspection forms and templates enable your team to generate work orders automatically when deviations are detected across multiple sites, ensuring proactive and thorough maintenance.
Configurable SLA schedules and automated escalations help manage breaches effectively, keeping your operations compliant and efficient.
Procurement and budgeting efficiency
Managing procurement and budgeting across multiple sites can be complex, but Facilio simplifies this with its comprehensive procurement module.
As an IFMSP handling large portfolios, you can maintain a detailed history of purchase requests, vendor quotes, purchase orders, and invoice verifications all in one place.
This centralized system enables you to plan maintenance budgets more effectively, ensuring alignment between financial planning and operational needs.
An IFM company overseeing a large portfolio can use these data-driven logged reports to plan maintenance budgets more effectively, aligning financial planning with operational needs.
The platform allows site-specific budgeting and automated quote processes to not only simplify financial management but also optimize expenditure.
Optimized maintenance and work orders
Facilio's 52-week maintenance work order schedule is a boon for IFMSPs looking to optimize resource allocation and expedite issue resolution. It also provides work order reports for a better overview of the facility's state.
By leveraging IoT and BMS data, along with occupancy and condition-based reports, you can help your clients transition from reactive to proactive maintenance strategies.
This approach reduces downtime and extends the lifespan of equipment, resulting in cost savings and improved operational efficiency. The integrated inventory tracking system ensures that parts and materials are readily available when needed, minimizing delays and disruptions.
Streamlined vendor management
Managing vendors effectively is crucial for IFMSPs, and Facilio provides the tools to do so with precision.
For example, real-time KPIs and SLA reports allow your team to monitor vendor performance closely, identifying areas where costs can be negotiated or services improved.
This data-driven approach ensures that your company receives the best value for its investment. Standardized vendor induction processes and mobile check-in/check-out functionalities streamline vendor management, while automated reordering based on inventory levels prevents stockouts and ensures continuous operations.
The following case study shows you how Facilio’s facility maintenance software delivers value.
How UK’s leading IFM company improved service quality across 300+ sites for its clients with Facilio
Before Q3, partnered with Facilio, they were facing serious roadblocks in delivering consistent service quality for their multi-site portfolio clients. From delayed onboarding that took over a year, to the chaos of managing planned maintenance work orders and miscommunication across fragmented systems, their operations were becoming more of a headache than a help to their clients.
Facilio stepped in with a unified, low-code platform that streamlined everything. Onboarding was templated, cutting the time to bring new clients online. Workflows became fully customizable, payment processes integrated seamlessly with Xero, and, perhaps most importantly, all communication was centralized.
This meant no more missed invoices or dark data lurking in the background—just clear, actionable insights. With predictive maintenance now decluttered and compliance monitoring more efficient than ever, Q3 regained full control over their operations, providing better visibility and higher service quality.
2. ServiceChannel
ServiceChannel offers facility managers a unified platform to manage repairs, maintenance, and operational data across their organization. It consolidates all aspects of facility upkeep into one comprehensive solution.
3. Hippo CMMS
Hippo CMMS simplifies facility management by streamlining maintenance tasks, schedules, and asset tracking. This software enhances efficiency, cuts costs, and optimizes overall facility performance.
4. Brightly Asset Essentials
Brightly Asset Essentials empowers operations teams to manage facilities, control maintenance expenses, and improve decision-making. Its advanced reporting tools provide actionable insights for resource planning, while integrations with tools like Microsoft Excel and ArbiterSports enhance its utility.
5. FMX
FMX is a cloud-based facility management platform that streamlines facility maintenance and operations. It simplifies daily tasks, enhancing efficiency and optimizing upkeep processes for organizations.
For an in-depth overview on the 10 of the best softwares for facility maintenance read here -
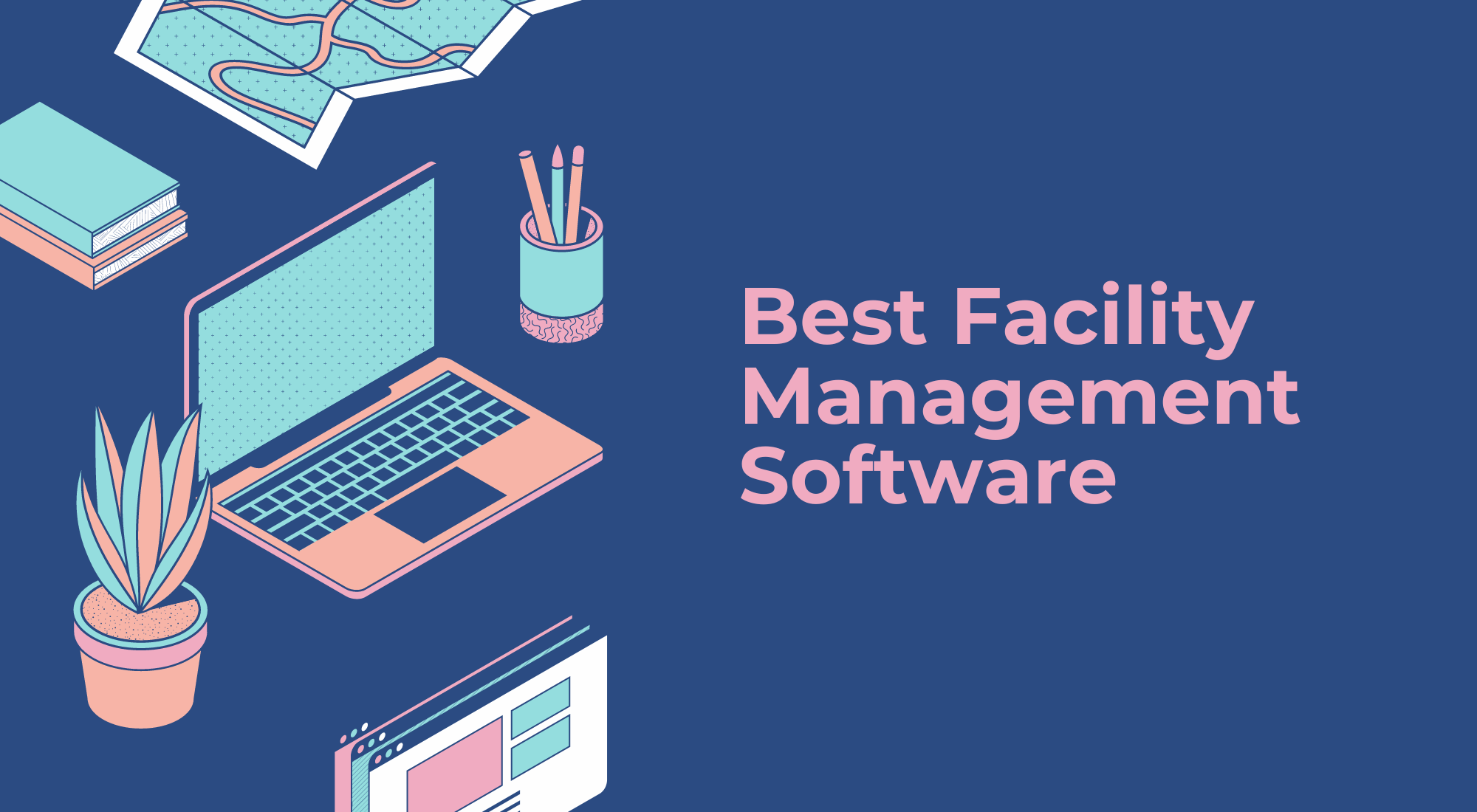
Adapting to new market demands: The case for better operations visibility in facility maintenance management
Facility maintenance management is quickly adapting to new market demands for better operational visibility and impactful changes in O&M strategic roles within the commercial real estate sector.
Cost optimization is still key, but O&M teams must now also deeply understand asset health, maintenance histories, tenant interactions, and customer retention. Leaders are focusing on energy efficiency, monitoring usage and waste, and comparing performance across portfolios to maintain high standards.
Additionally, wellness indicators like air quality, along with tenant comfort and satisfaction metrics, are crucial. O&M teams must integrate these insights into a cohesive strategy to effectively manage facilities and stay competitive.
Explore how Facilio can enhance your facility maintenance strategy, reduce operational costs, and enhance efficiency across your portfolio.
FAQ
What is the difference between facility maintenance and facility management?
Although used interchangeably, they serve distinct and complementary roles within an organization. Facility maintenance is the hands-on, day-to-day care of the physical environment. In contrast, facility management is the strategic big-picture planning that ensures those daily efforts work well with broader organizational goals.
Facility maintenance is the frontline defense against disruptions. It addresses the immediate needs of the building's infrastructure, focusing on fixing what’s broken and preventing breakdowns.
In contrast, facility management integrates various functions to create a harmonious and efficient ecosystem, considering short-term and long-term strategies for better optimization of business resources.
What is the primary goal of facility maintenance?
The main goal of facility maintenance is to ensure the optimal performance, safety, and sustainable operations of an organization's space and physical assets. This involves the proactive upkeep of buildings, equipment, and systems to prevent breakdowns, minimize downtime, extend asset lifespans, and improve occupant conditions and satisfaction.
What does a facility manager do?
Facility managers are responsible for maintaining the integrity and safety of buildings and infrastructure. This includes overseeing maintenance upkeep and planning and coordinating routine inspections to ensure all operational systems are functioning optimally.
Facility managers also liaise with internal departments, senior management, and external service providers. They provide regular updates on facility status, manage stakeholder expectations, and address any concerns promptly.
What is the primary purpose of a facility manager?
A facility manager primarily serves as a strategic partner who aligns facility operations with organizational goals and contributes to a business's overall success, which directly and indirectly influences the company’s reputation and operational continuity.
These include helping meet legal and regulatory requirements and health and safety standards, controlling operational costs, curbing excess waste, and leveraging tools and tech to enhance facility performance.