What is the Difference Between CaFM and CMMS?
The actual hurdles in modern facility management often arise not from managers' capabilities but from the limitations of their technology stacks. Without advanced digital tools, overseeing portfolio-wide operations becomes complicated, communication across departments suffers, and centralizing facility data grows burdensome.
This is where computerized maintenance management systems (CMMS) and computer-aided facility management (CaFM) come in. These technologies serve as data-driven assistants for facility managers, automating asset management, smoothing property maintenance, and unifying space management under single platforms.
While used interchangeably, CMMS and CaFM carry distinct nuances, especially regionally. CaFM dominates in the UK and UAE, while CMMS rules in the US. But looking closer, CaFM is an umbrella term covering a wide range of capabilities, including those of CMMS.
In essence, CMMS is a component within CaFM's broader scope.
This article deconstructs the similarities and differences between CMMS and CaFM, exploring their respective roles in the facility management context. Grasping these distinctions is key for organizations to decide which system best matches their needs and goals.
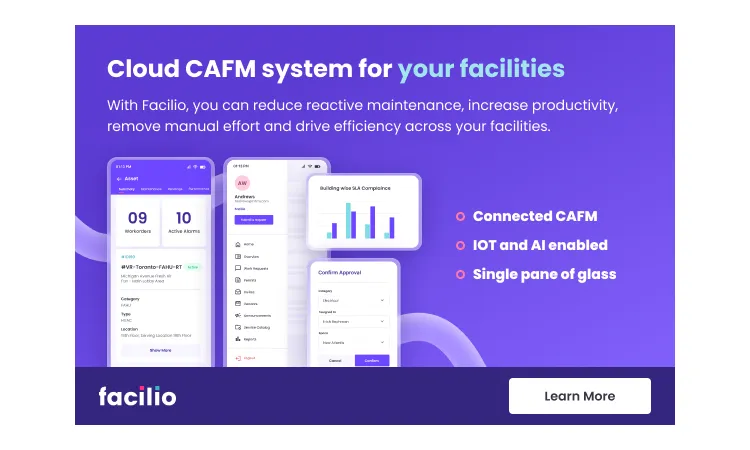
What is CaFM software?
CaFM is a comprehensive facility operations tool designed to provide complete visibility and predictability around facility operations. It empowers facility managers to effectively plan, manage, and monitor people, processes, and systems across the entire real estate portfolio. CaFM brings a single pane of glass visibility towards the entire facility's operations, i.e., from daily operations to yearly organization goal achievements..
Facility management teams juggle countless daily tasks across multiple sites to keep operations running smoothly. A reliable digital tool to help automate and streamline everything could be a game-changer. That's precisely the aim of CaFM—to empower facility managers and O&M executives by simplifying their workload.
Specifically, CaFM provides a comprehensive overview of all work orders completed across locations. It delivers clear visibility into vendor performance through detailed metrics and analytics. The tool also simplifies the process for tenants and occupants to submit service requests and monitor progress.
Ultimately, an effective CaFM system serves as an invaluable assistant for all stakeholders involved in the facility's daily operations. It helps ensure tasks are completed efficiently while providing transparency and insight.
By compiling data and automating workflows, CaFM enhances the management of various facility maintenance and operations elements. This comprehensive approach optimizes administration and aligns it tightly with the organization's larger objectives.
The use of CaFM extends across multiple industries, making it an indispensable tool in real estate for effective property management, for example, in healthcare for streamlined facility administration, and in educational institutions for comprehensive oversight of campus operations.
While it's true that both CaFM and CMMS are equally versatile in their application, CMMS is notably prevalent in the manufacturing sector, where the focus on equipment maintenance and operational efficiency is paramount.
However, this distinction simply highlights that CMMS is tailored to meet the unique maintenance management needs of manufacturing environments. It does not imply any limitation in the broad applicability of CaFM solutions across industries.
Features:
- Vendor management
- Inspection management
- Space management
- Service request management
- Downstream integrations
- Energy analytics & BI
- Cloud-based optimization
- Remote multi-Site monitoring
- Soft service compliance management
- Lease management
- Data dashboards
Benefits:
Here are some of the benefits of using CaFM for your business:
- Accelerate work order execution with powerful automation
The tool streamlines maintenance by automating work order creation, assignment, and tracking. This reduces manual errors, speeds up response, and ensures prompt, efficient task completion.
- Replace multiple subscriptions with one unified platform
By consolidating facility operations into a single platform, businesses can eliminate multiple software subscriptions. This simplifies their stack, reduces costs, and enhances user experience through an integrated interface.
- Identify opportunities for cost saving
CaFM systems provide detailed operational expense insights, helping businesses spot inefficiencies and savings opportunities. Through energy analytics, asset lifecycle management, and vendor tracking, it enables strategic cost optimization decisions.
- Improve stakeholder engagement with a unique login for all
A CaFM platform offers personalized access for facility managers, technicians, vendors, tenants - all stakeholders. This improves communication, collaboration, and transparency, increasing engagement and satisfaction.
Read More: Best CAFM Software in 2024: Features, Benefits & Comparison
What is CMMS software?
A computerized maintenance management system (CMMS) is software that centralizes maintenance information and facilitates maintenance operations. The core of a CMMS is its database, which organizes information about assets, equipment, materials, work orders, preventive maintenance, labor management, and inventory. It streamlines tasks such as work order management, preventive maintenance scheduling, and materials tracking. In summary, a CMMS helps organizations efficiently manage maintenance processes and enhance operational resilience. It helps organizations increase their assets’ lifespan, improve production efficiency and profits, and prevent occupational hazards.
People also read: What exactly is a CMMS and how it works?
With CMMS, facility managers can manage incoming work orders, plan maintenance, track the condition of equipment in real time, record maintenance issues, connect field operators to plants and warehouses, interact with outside partners, and update paperwork for compliance.
It helps ease the hassle of maintenance by providing you with a proactive maintenance process.
CMMS is used in industries like engineering, manufacturing companies, and healthcare that require equipment maintenance and servicing.
Features:
- Work order management
- Maintenance management - Planned, Preventative, and Reactive
- Asset lifecycle management
- Asset history tracking
- Fault detection and diagnosis
- Inventory & storehouse management
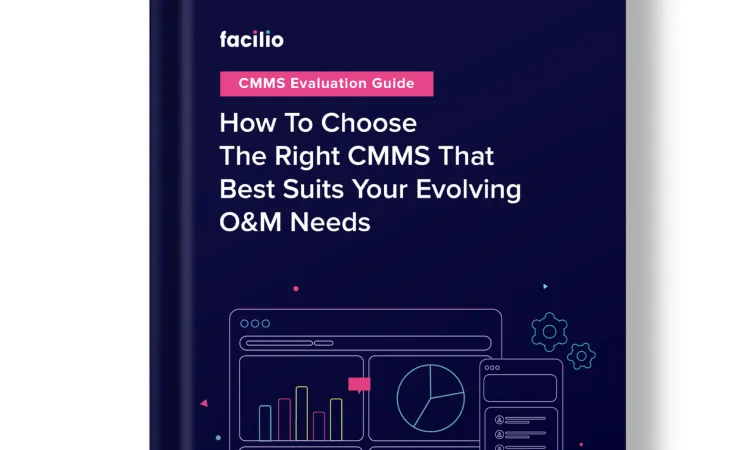
Benefits:
CMMS has various benefits for businesses. For instance:
- Increased asset lifecycle
Implementing CMMS software significantly extends asset lifespans by ensuring timely maintenance and repairs. Through systematic tracking and management of maintenance activities, assets stay in optimal condition, reducing the need for premature replacements and maximizing value over time.
- Improved asset efficiency & reliability
It also enhances asset efficiency and reliability by facilitating preventive maintenance and fault detection. This proactive approach minimizes unexpected breakdowns, keeps assets performing at their peak, and enables continuous production without interruptions.
- Automated maintenance schedule
In addition, CMMS automates maintenance scheduling, guaranteeing preventive and corrective tasks are executed on time. This eliminates guesswork and manual tracking, streamlining maintenance operations and freeing up staff for more strategic work.
- Reduced asset/Facility downtime
By enabling early detection of potential issues and regular maintenance, the tool plays a crucial role in minimizing asset and facility downtime. This reduction in downtime not only boosts productivity but also substantially decreases costs associated with unscheduled repairs and lost operational hours. learn more on benefits of CMMS
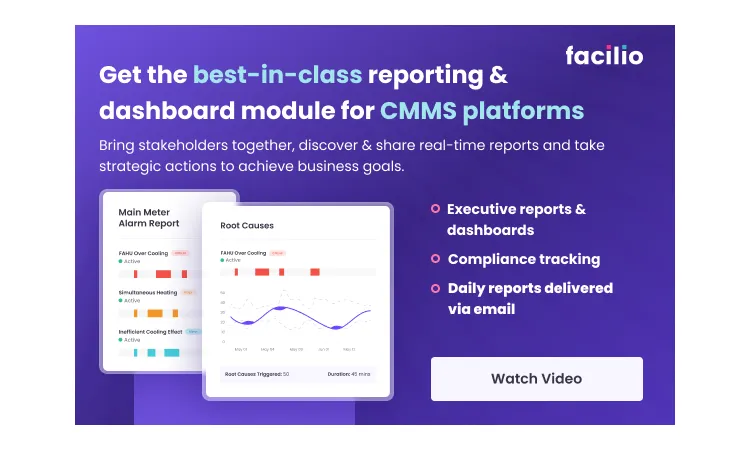
Read More: Best CMMS Software in 2024: Features, Benefits & Best Practices
Key differences between CMMS and CaFM
CaFM use case
Consider a facility management service company that manages various commercial properties, including office spaces, retail centers, and shopping malls. The facilities manager tasked with overseeing these buildings struggles to efficiently organize space, control rising maintenance costs, and ensure smooth day-to-day operations.
A CaFM solution can be used to address these challenges. Here is how it will help:
- It provides the facilities manager with enhanced visibility into how each space is utilized across the company's diverse property portfolio, enabling smarter reallocation of resources.
- The software also maintains detailed records of all maintenance activities and expenditures, highlighting areas where money can be saved through improved efficiency and cost control.
- The CaFM platform contains a comprehensive database of approved contractors & vendors, streamlining the process of hiring qualified professionals to handle any required jobs.
Planning for future needs and budgeting becomes much simpler with all information related to the buildings' assets, warranties, and repairs centralized in one location.
CMMS use case
In a manufacturing facility where smooth production depends heavily on properly functioning machinery, the maintenance manager's greatest challenge is avoiding unexpected machine breakdowns that would halt critical production lines.
To address this issue, the company decides to implement a CMMS software solution that transforms the facility's maintenance program and routines.
- It automatically generates and schedules preventative maintenance checks based on running hours, calendar dates, or other triggers, heading off machine failures before they occur.
- The CMMS also maintains comprehensive records of all maintenance activities, parts and materials costs, and machine repair histories, making this data accessible to all technicians and managers associated with upkeep activities.
- The detailed documentation within the CMMS ensures the manufacturing plant meets all safety standards and industry regulations, helping avoid costly fines.
The outcome improves efficiency in completing maintenance tasks, as well as data-driven decision-making when issues arise.
Recommended Read: CMMS vs. EAM : What's the Difference & Which is Right for you?
Take the First Step Toward Next-Gen Facility Management
As facility managers face the ever-changing landscape of building operations, upgrading technology becomes less of an option and more of a must for staying competitive. Facilio's Connected CMMS/CaFM represents the leap into a future where asset and maintenance management sync intuitively with your portfolio's strategic vision.
With Facilio, you're not just getting a tool—you're embracing an intelligent assistant that provides tailored solutions to boost efficiency, cut downtime, and optimize costs. The unified solution brings facility management to the 21st century with the power of data collected from all corners of the facility, to make experience-driven operations a reality.
As a result, facility managers can empower themselves with real-time data, streamlined workflows, and a unified platform that brings systems, people, and processes together.
Embrace change, unlock portfolio-wide operational and maintenance efficiencies, and join the ranks of forward-thinking companies around the world.