For every business, efficient workflows are the lifeblood of smooth operations. Yet, countless hours are often lost to manual processes that act like cogs in the wheel, grinding productivity to a halt.
Take, for instance, the commercial real estate (CRE) industry—sectors such as land planning, development, construction, brokerage, valuation, and building operations are heavily data-dependent.
To optimize operations and improve ROI for their clients, CRE portfolio IFM managers already have to deal with rising labor costs and inflation, which are hitting the bottom line hard. Companies are scrambling to cut costs however they can.
As the need for data processing skyrockets, so does the demand for more personnel to handle the influx, all amidst a talent shortage.
Companies within and outside the commercial property sector are leveraging data and automation to enhance service delivery, cut costs, and address the labor skills gap, creating a new battleground for data utilization.
However, many of the IFM service industry’s skilled professionals still manually process data, which negatively impacts their clients' facilities’ profitability and operational efficiency.
Warren Shiau, the research VP for the International Data Corporation (IDC), said:
Savvy businesses are offshoring manual tasks to self-driving technology that focuses on basic automation of business processes.
According to a recent survey conducted by Plant Engineering, 37% of companies expect a rise in demand for automated technologies and services for process optimization.
However, the current state of FM is characterized by disjointed processes, manual interventions, and communication gaps. Inefficiencies that lead to delayed responses, increased costs, and decreased tenant satisfaction.
Traditional FM tech solutions often solve narrowly defined problems like recording maintenance logs, generating work orders, and managing purchase orders, but they are rigid and create blind spots, bottlenecks and friction.
While this may have worked perfectly in the past, the dynamic needs of buildings, their assets, and occupants require more flexible solutions.
But, with automation-driven software, you can seamlessly carry out operational processes like work order management.
You can use it to automatically log requests and auto-assign tasks based on technician availability and expertise. Progress can be tracked in real time, and completion updates can be sent automatically. This reduces manual entry, minimizes errors, and ensures timely maintenance, enhancing overall efficiency and tenant satisfaction.
The beauty of automation is that it frees up your time, allowing you to focus on more strategic parts of the company.
A KRC Research survey found that 78% of business leaders believe task automation can save them up to 3 hours a day, with 53% of employers estimating similar time savings.
With the growing need for smarter, faster data handling, automation is the game-changer. It's time to move from tedious manual workflows to streamlined, automated processes that boost productivity and meet client demands head-on.
What is an automated work order system?
It works by automatically generating work orders based on a combination of pre-set schedules, real-time sensor data, or user submissions.
This means that the system springs into action without manual input as soon as a maintenance need arises, whether it’s a routine check or an urgent repair.
For instance, imagine overseeing a large office complex with numerous systems needing regular upkeep, from lighting and plumbing to security alarms.
Whenever a maintenance issue arises, the automated system generates a work order, directs it to the right technician, and schedules the job based on urgency and available resources.
Another key benefit is real-time visibility, as the system provides instant updates and notifications through mobile devices or web portals. This keeps everyone informed and on track about equipment fixes no matter where they are.
Moreover, the system simplifies completion and record-keeping by automatically recording details of each completed task, closing work orders, and storing data for future reference.
This not only streamlines maintenance operations but also creates a comprehensive log that aids in future analysis and decision-making.
The pitfalls of manual work orders
When dealing with work order completions, you might find yourself asking: How do I track and measure the efficiency of the work order process across multiple sites? Which types of work orders show lower completion rates?
Similarly, for performance, questions like are tasks assigned to the most qualified personnel? How do I benchmark performance and downtime metrics across asset-servicing vendors?
If these quantifiable metrics pose such challenges, imagine the difficulties with more subjective metrics like tenant satisfaction.
Building managers need to pinpoint major friction points for tenant discomfort, identify which areas receive the most complaints, and determine which steps in the complaint resolution process lead to tenant frustration.
To answer these questions effectively, you need insights and KPIs grounded in real-time data. However, with current traditional CMMS software, this data is scattered across disparate systems and services.
Manual work orders, a byproduct of legacy systems, exacerbate these issues. They require manual data consolidation or lengthy system integration projects, making it impossible to derive real-time insights to automate processes effectively.
Here’s how manual work order management impacts your business outcomes:
How automated work order systems can streamline workflows, improve communication, and reduce errors
1. Enhances preventive maintenance operations
Automated systems take the guesswork out of scheduling work orders for preventive maintenance. By setting up reminders based on pre-determined conditions—like manufacturer recommendations or usage thresholds—you ensure that maintenance tasks are executed on time.
An IFMA analytical study on the economic value of preventive maintenance (PM) reveals that investing in PM not only recoups the initial cost but also yields substantial returns.
Automating work order reminders for PM schedules can help you optimize financial expenditures and leave little to chance, bringing you closer to achieving these significant returns.
2. Streamlining task management
Automated work order systems use one central platform to create, assign, track, and close work orders, eliminating confusion and streamlining workflows.
When an inspection identifies an issue, automated work order systems spring into action when an inspection identifies a problem. They instantly generate and assign work orders, closing the loop between operations and maintenance teams.
This eliminates delays and confusion, prioritizing tasks based on urgency and importance. Tasks are assigned efficiently, considering resource availability and skill sets, which optimizes productivity and minimizes downtime.
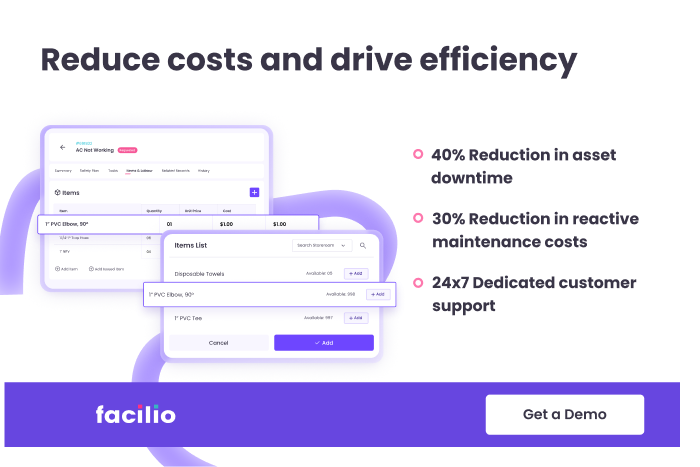
3. Improving communication and collaboration across all stakeholders
These systems consolidate messaging, emails, and notifications into one central platform. This centralization simplifies tracking and fosters transparency, ensuring everyone stays informed about task completions, approvals, and delays.
But why do these projects go off track? Poor stakeholder engagement and communication are significant contributors to these issues.
The study also found that developers often face around six budget changes and five schedule adjustments per project, mostly due to miscommunication and fragmented workflows.
Further research by PMI highlights that effective communication with stakeholders is crucial, as 56% of project risks are linked to communication failures.
For customer-facing tasks, automatic notification updates on the work order management software platform keep tenants/occupants informed about the progress of their service requests.
4. Eliminate manual errors
Unfortunately, redundant tasks like searching, sorting, and validating information are still common.
These losses came from wasting resources on manual data entry, verifying and validating data, and costly delays when staff wait for critical information to address maintenance issues.
Automating work orders can cut out these manual tasks, making data retrieval and updates instantaneous. This means fewer delays and more efficient resolution of maintenance issues, ultimately saving time and reducing costs.
The system can automatically identify missing information or scheduling conflicts in work orders before they become bigger issues, allowing facility managers to address them promptly and prevent delays.
5. Utilizing analytics to optimize operations
Analytics monitoring, such as tracking metrics like Mean Time Between Failures (MTBF) and Mean Time to Repair (MTTR), helps detect issues early and continuously improve performance.
If an asset has a low MTBF, more frequent inspections and quicker response times are necessary. Automated systems can prioritize these tasks and allocate resources effectively, ensuring high-maintenance equipment gets prompt attention.
Additionally, by analyzing MTTR data, automated systems can identify delay sources and adjust workflows—like adding skilled technicians or improving parts procurement. They can also review vendor performance in reaction time to equipment failure and repair.
Automate work order management with connected CMMS
Work management software typically includes various tools like resource management, teamwork coordination, time and job management, budgeting, and reporting. These tools can be integrated with other projects, making them versatile and comprehensive.
Regardless of project size, successful work order management hinges on the execution plan and task order.
It takes skill to manage this well, but investing time in good project management techniques can lead to timely project completion within resource constraints.
Techniques like the Eisenhower decision matrix have been the go-to for many enterprises to prioritize tasks. While effective, this approach has drawbacks:
- It doesn't account for the dynamic nature of tasks, requiring constant reassessment as priorities shift.
- It focuses on individual task management rather than team-based priorities, which can be problematic in collaborative settings.
- It overemphasizes urgent tasks, leading to a reactionary workflow that neglects long-term planning and strategic tasks.
- It sorts tasks solely based on urgency and importance, and it doesn’t account for available resources and labor for addressing issues.
Also, current CMMS don’t cut it either as it is limited with technician-only focus, little to no automation or integration with the rest of O&M tech stack.
It enhances teamwork by supporting collective task management, ensuring projects are well-coordinated and resources are effectively allocated.
Using predictive analytics and intelligent scheduling, it balances immediate concerns with long-term goals, preventing the neglect of strategic planning in favor of urgent tasks.
Connected CMMS solves O&M challenges related to portfolio operations and maintenance by prioritizing the automation of processes, engaging stakeholders and enhancing interoperability efficiency.
How Facilio’s connected CMMS enables you to automate work orders
Facilio work order management software is a platform-based CMMS that serves as a centralized hub for managing (O&M) across multiple sites
It enhances your service request and work order processes through real-time data insights, allowing you to prioritize tasks efficiently on a single, consolidated platform. This flexibility ensures improved maintenance oversight and operational continuity.
With Facilio, you can streamline work order automation using triggers like specific dates, times, alarms, meter readings, or any defined irregular activities. This proactive strategy allows you to anticipate and address potential issues by closely monitoring asset health and planning regular inspections.
It links asset activities to alarm triggers, creating work orders automatically and providing immediate notifications on the status of asset repairs or replacements.
Key features of Facilio work order management
Facilio work order management system is equipped with several key features designed to streamline operations for facility management service providers (FMSPs):
Integrated inventory tracking
By tagging spare parts to specific work orders and vendors, Facilio’s system precisely manages inventory. It tracks their storage location and automates reordering when stock levels drop.
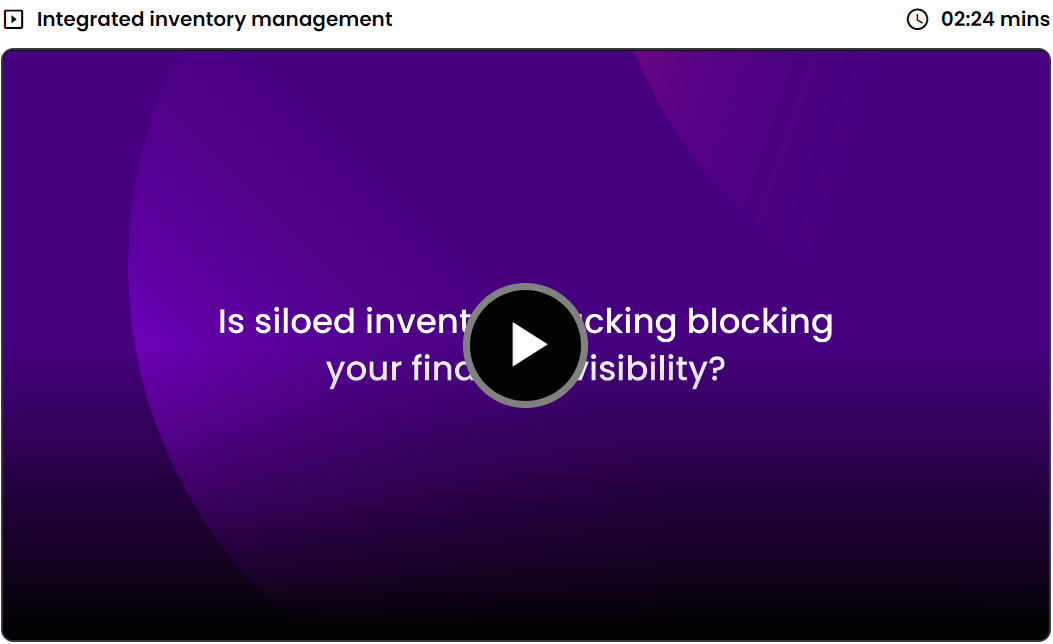
For example, suppose a technician requests a replacement bulb for a malfunctioning light. In that case, the system will automatically check stock, order new bulbs if needed, and update the inventory records.
When maintenance issues arise, work orders are created based on technician availability. For example, if a technician is unavailable due to sick leave, you can quickly reschedule work orders through an intuitive resource scheduler and calendar. This flexibility allows continuity and reduces scheduling conflicts.
Automate recurring work orders
The platform automates recurring maintenance tasks and sets prioritization alerts and criteria for spare part reorders. For example, you can automatically schedule regular filter changes for HVAC systems and notify you in advance to reorder filters, ensuring maintenance is consistent and inventory levels are maintained.
Service request management
Tenants and clients can easily submit service requests via web and mobile portals. These requests are automatically routed to the appropriate facility manager or maintenance staff, streamlining the process and ensuring timely and effective responses.
Configure SLA schedules and escalations
The platform allows you to set up SLA schedules and escalation procedures to handle breaches effectively. For instance, if a repair request isn’t completed within the agreed time frame, the system will automatically escalate the issue to higher management and adjust workflows to address the delay promptly.
Mobile inspections with automated deviation work orders
Facilio speeds up issue resolution by generating deviation reports and creating work orders based on real-time data. When a technician uses their mobile device to inspect HVAC systems, any detected deviations, such as a temperature fluctuation outside the acceptable range, automatically trigger a work order for immediate attention.
AI-powered workforce optimization
Facilio leverages AI to optimize workforce management by automatically assigning staff based on job type and specialization. It dynamically adjusts assignments based on shift timings, attendance, and breaks.
Real-time maintenance dashboards
Comprehensive real-time dashboards offer detailed insights into maintenance operations. You can see open work orders, completion times and current servicing/repair activities.
On the dashboard, you can see that Technician A is currently handling an in-house electrical repair, taking approximately 3 hours, while Technician B is completing an outsourced plumbing job. With this real-time report, you can make adjustments to your optimize your workflow.
The dashboard also shows SLA compliance for each work order and the associated costs, enabling accurate tracking and billing for services provided to clients.
Facilio ensures transparent communication by facilitating feedback from tenants on work orders, allowing property teams to engage effectively with all stakeholders.
After a tenant submits a service request for a leaky faucet, they can provide feedback on the repair process via their mobile portal. The property team and facility managers can view this feedback, ensuring the tenant's satisfaction and allowing for continuous improvement in service quality.
Case studies: FMSPs who benefited from the Facilio work order management system
Facilio is leading the way in helping companies make this switch. Here are two examples of FMSPs that have benefited from using an automated work order system.
Case study I: Facilio improved Q3’s service quality by automating PPM
Q3 services is a facilities management service provider company based in the United Kingdom. The company faced three major challenges:
Challenges
- Multiple work orders for planned maintenance made work order management more complex and disorganized.
- Teams communicated through various platforms, hindering efficient sharing of information and collaboration.
- The company used multiple manual systems, leading to dark data accumulation and making it hard to extract important insights.
Solutions
- Facilio transformed Q3's planned preventive maintenance by grouping similar assets and using deviation work orders, streamlining operations, and providing strategic insights.
- Facilio replaced various external tools with user-specific apps and portals, improving communication and granting stakeholders real-time data access.
- Facilio integrated seamlessly with Xero for financial management, ultimately boosting efficiency and accuracy in tracking and reporting financial data.
Impact
- Simplified predictive maintenance processes.
- Reduced dependence on offline communication.
- Improved visibility for better asset management.
- Efficient compliance monitoring.
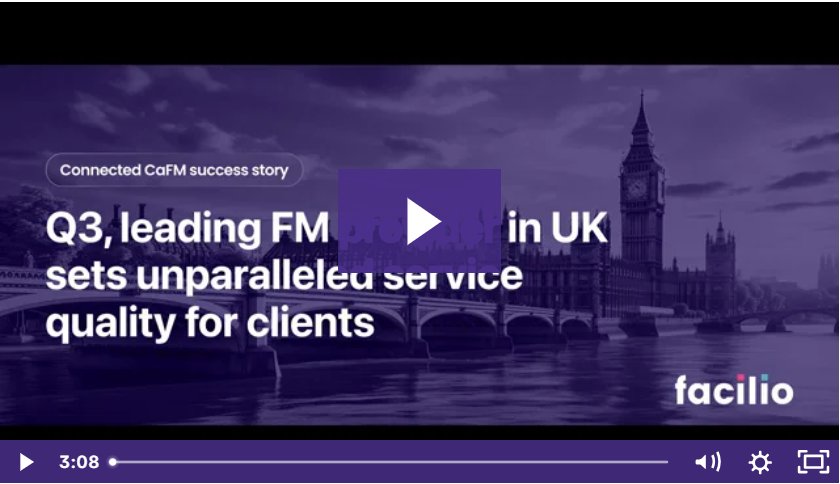
Case study II: Facilio helped CIT Group Ltd create threshold-based automated work orders
CIT is a company that manages national landmarks and cities in Makkah province, Saudi Arabia.
Challenges
CIT Ltd. faced several challenges in its FM operations at RCU - Al Jadidah, which it aimed to address through Facilio:
- The company lacked a unified and efficient computerized maintenance management system (CMMS).
- There was difficulty in gaining a centralized view of assets and PPM activities.
- The company experienced a lack of visibility into daily and weekly operations, including pending work orders.
- There was limited insight into SLA adherence and vendor/technician KPIs.
- CIT Ltd. could not effectively document workforce attendance for training, QHSE, and OSHA audits.
Solutions
Here’s how Facilio helped CIT:
- Facilio provided CIT with a digital calendar and automated work orders, streamlining maintenance for technicians and vendors.
- CIT used Facilio’s intuitive dashboards for real-time SLA monitoring, KPI tracking, and asset management, enabling data-driven decisions
- Facilio offered predictive maintenance insights, reducing equipment downtime and cutting costs. Automated work order alerts ensured proactive and reactive maintenance.
- In Al Jadidah Village, Facilio managed attendance and generated automatic analytical reports, streamlining daily and weekly reports for training effectiveness and compliance.
- CIT used Facilio’s analytical dashboards to monitor and generate reports on PPM, reactive maintenance, and pending work orders.
Impact
- Reduced manual work with threshold-based automated work orders.
- Improved visibility and clarity on asset management.
- Swift CMMS implementation within three weeks.
- Achieved portfolio-level visibility of assets.
Here’s how Facilio has helped them:
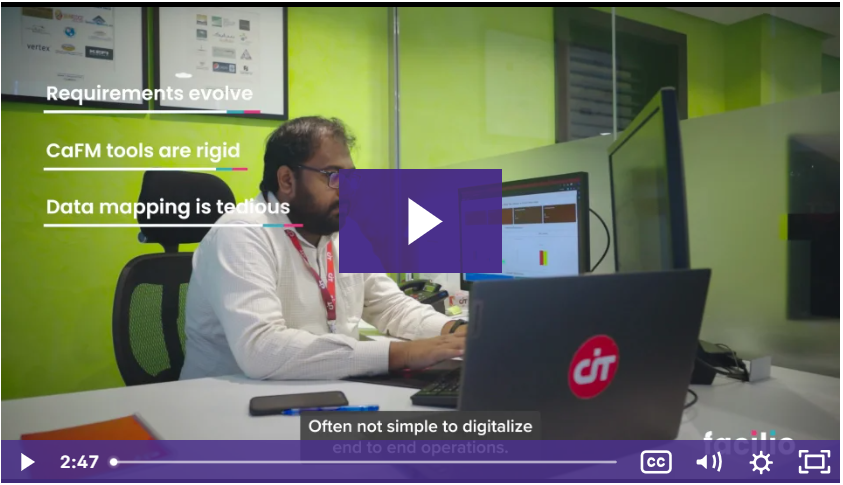
Experience streamlined, stress-free facility management operations with automated work orders in Facilio
At the end of the day, the true power of workflow automation lies in enhancing customer experience. To achieve this, it's essential to establish a streamlined program that ensures smooth operations and keeps customers/tenants satisfied.
Consider the difference when a technician can simply press a button upon arrival to notify facility managers and tenants that work has begun.
Tenants receive automatic updates about their service requests without needing to chase for information. Complaints are resolved faster and more effectively, and feedback is collected automatically, driving continuous improvement.
Legacy systems, with their manual processes and fragmented data, often fail to deliver this level of service. They create bottlenecks, prolong downtimes, and frustrate both staff and customers.
Facilio’s automation-driven approach not only replaces these outdated systems but also transforms how property operations are managed. It connects systems, people, and processes in a meaningful way.
Explore how Facilio can transform your facility management operations.