Exploring the Relationship Between Maintenance & Reliability
Maintenance comes into action when something breaks down, and you have to troubleshoot and repair problems in equipment or systems. On the other hand, reliability concerns the equipment's design and functionality that define its ability to function seamlessly.
This article will cover the main differences between maintenance and reliability, their core pillars, and key trends.
What is maintenance?
Maintenance involves managing assets, equipment, and systems to overcome asset failure and ensure operational continuity.
A study by the International Association of Maintenance Management Professionals (IAMMP) found that maintenance-related issues account for 10-15% of unplanned downtime in manufacturing industries, which can cost businesses up to $260,000 per hour.
Planning the right kind of maintenance framework to determine monitoring techniques, maintenance activities, and schedules is critical to avoiding costly disruptions.
Maintenance maximizes the hassle-free functioning and longevity of facilities, assets, and entire businesses by proactively predicting issues, improving equipment efficiency, derisking risks & safety hazards, and ensuring compliance.
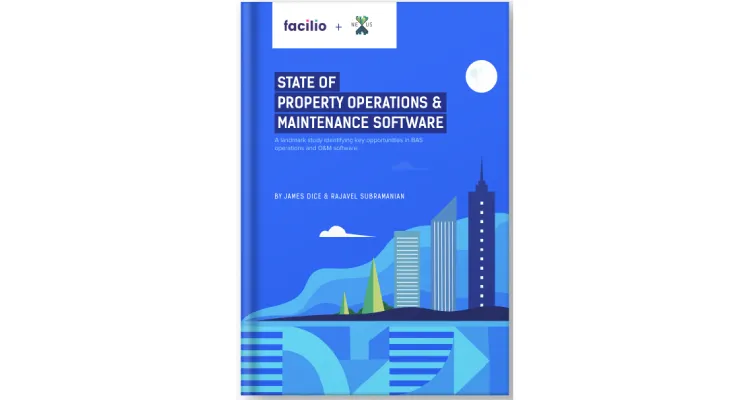
There are four primary types of maintenance: Reactive, preventive, predictive, and breakdown maintenance.
Reactive maintenance (RM): Also known as corrective maintenance, RM aims to restore the equipment to its original functionality once an asset or equipment has malfunctioned. This is typically applied to assets that aren’t very expensive to replace or do not pose threats to operational continuity.
Preventative maintenance (PM): Also known as routine maintenance, preventive maintenance involves scheduled inspections and repairs to prevent equipment failure in the future.
Predictive maintenance (PdM): It uses data and analysis to predict equipment failure based on predefined failure modes. This methodology uses PdM tech (or CMMS software) and IoT beacons for real-time monitoring and insights into asset performance.
Breakdown maintenance: Also known as run-to-failure maintenance, breakdown maintenance is used to repair or exchange the damaged part in case inspection, and other maintenance activities aren't possible due to the breakdown of assets.
Implementing the right maintenance framework and monitoring techniques is essential to improve equipment efficiency, derisk risks and safety hazards, ensure compliance, and maximize the hassle-free functioning and longevity of facilities and businesses.
So how do you assess if your maintenance programs are effective?
Enter: Reliability metrics.
Looking for a CMMS that does more than record-keeping?
Explore Facilio's Connected CMMSWhat is reliability?
Reliability refers to the ability of a maintenance program to ensure the reliability of assets, systems, and equipment. It’s a measure of how well your maintenance efforts ensure continuity in operations with minimal downtime.
Here are some formulas, pros and cons, and examples of different reliability metrics commonly used in equipment reliability analysis:
Failure rate (λ)
The failure rate is a measure of the frequency at which a system or component is likely to fail over a certain period of time.
It is often expressed as the number of failures per unit of time (e.g., failures per hour or per year).
If a manufacturer wants to understand the failure rate of a new production line that has been operating for 1000 hours and has experienced 5 failures, λ = 5 / 1000 = 0.005 failures per hour.
- Pro: Simple to calculate, provides a measure of the frequency of failures
- Con: Does not take into account the age of the equipment or the severity of the failures
Mean time between failures (MTBF)
MTBF is a measure of the average time that a system or component can run without experiencing a failure.
It is calculated by dividing the total operating time by the number of failures that occur during that time.
If a fleet of trucks has been operating for a total of 10,000 hours and has experienced 20 failures, the MTBF = 10,000 / 20 = 500 hours.
- Pro: Takes into account the age of the equipment and provides a measure of the average time between failure
- Con: Assumes a constant failure rate over time and may not be appropriate for equipment with a high initial failure rate.
Mean time to failure (MTTF)
MTTF is similar to MTBF, but it is specifically used for systems or components that are repaired or replaced after a failure occurs.
It is the average time that a system or component can run before a failure occurs that requires repair or replacement.
If an electronic component has been operating for a total of 1000 hours and has experienced 10 failures and 5 suspensions, the MTTF = 1000 / (10 + 5) = 66.67 hours.
- Pro: Takes into account the age of the equipment and provides a measure of the average time until the next failure.
- Con: Assumes a constant failure rate over time and may not be appropriate for equipment with a high initial failure rate.
Availability
Availability is the measure of the proportion of time that a system or component is operational and available to perform its intended function.
It is often expressed as a percentage and takes into account both scheduled downtime for maintenance and unscheduled downtime due to failures or other issues.
If a power plant has been operating for 24 hours a day for a year, but has been shut down for 50 hours for maintenance, the Availability = (24 x 365 - 50) / (24 x 365) = 98.6%.
- Pro: Provides a measure of how often the equipment is available for use
- Con: Does not take into account the severity of the downtime
Reliability
Reliability is the measure of the ability of a system or component to perform its intended function over a certain period of time. It takes into account the probability of failure and the consequences of failure.
A reliable system or component is one that is unlikely to fail and can be depended on to perform its intended function consistently.
If a machine has been operating for 2000 hours and has experienced 150 hours of downtime, the Reliability = 2000 / (2000 + 150) = 0.93 or 93%.
- Pro: Provides a measure of the probability that the equipment will operate without failure over a given time period
- Con: Assumes a constant failure rate over time, does not take into account the severity of the downtime
While each metric has its pros and cons, they all provide valuable insights into the reliability of equipment and can help maintenance teams optimize their maintenance activities to increase uptime and reduce costs.
Ultimately, achieving high equipment reliability requires a comprehensive approach that includes preventive maintenance, predictive maintenance, and asset management strategies.
Manage 360° asset lifecycles from a centralized platform
Explore Facilio's Asset Management featuresWhat is the objective of maintenance & reliability?
The primary objective of maintenance and reliability is to ensure the seamless and efficient functioning of equipment, systems, and facilities during their lifetime.
The ultimate goal is to minimize downtime, reduce maintenance costs, and increase the overall efficiency and effectiveness of an organization's operations.
A McKinsey study concluded that maintenance and reliability could reduce machine downtime by 30-50% and extend equipment lifespan by 20-40%.
A comprehensive maintenance and reliability program helps businesses ensure their assets are functioning at their highest level and continue to meet the needs of their customers and stakeholders.
The five pillars of maintenance and reliability
The five pillars of maintenance and reliability are business processes, workforce management, materials management, asset management, and performance management.
- Business Processes: The management systems and processes that support maintenance activities, such as work order management, planning and scheduling, and performance metrics.
- Workforce Management: The practices and tools used to manage and develop the maintenance workforce, including training, performance management, and succession planning.
- Materials Management: The processes and systems used to procure, store, and manage maintenance-related materials, including inventory management, vendor management, and procurement strategies.
- Asset Management: The strategies and practices used to manage the physical assets of the organization, including maintenance strategies, asset performance management, and lifecycle analysis.
- Performance Management: The systems and tools used to measure and analyze maintenance and reliability performance, including KPIs, data analysis, and continuous improvement processes.
To achieve error-free asset performance, it is essential to empower your team to execute, monitor, and iterate maintenance and reliability measures.
Using a smart Computerized Maintenance Management System (CMMS) like Facilio helps manage end-to-end asset lifecycles with 360-degree operational visibility and remote monitoring and control of equipment performance across locations in real-time.
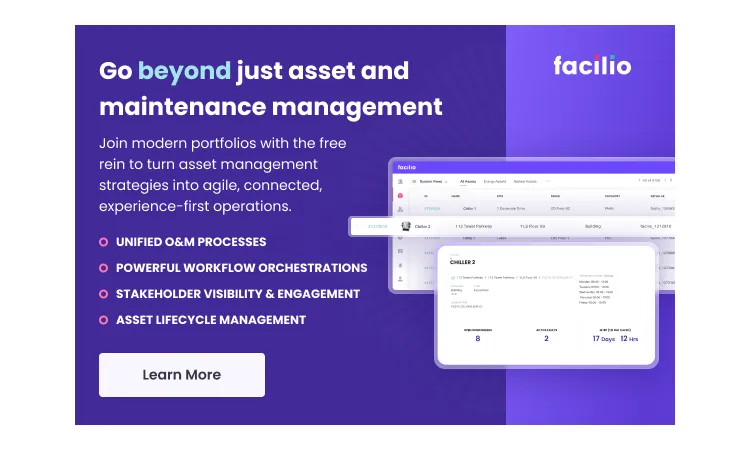
Maintenance and reliability trends in 2023
Time is money rings true for maintenance and reliability managers.
Let’s look at four key maintenance and reliability trends changing the game in 2023:
- Digital transformation: Digitizing O&M processes with CMMS built for modern use cases will be essential for operational efficiency.
Organizations are increasingly switching from reactive to proactive methods of monitoring and maintaining critical equipment and spaces. - Predictive analytics: According to a report by Precedence Research, the predictive maintenance market will grow to $10.79 billion in 2023.
Utilizing IoT devices such as sensors, artificial intelligence, and digital twins can help identify patterns and predict equipment behavior to enable timely maintenance and improve reliability. - Workplace safety: Automating redundant and mechanical tasks can free up employees’ time and allow them to focus on the most important aspects of their roles.
Providing a safe work environment for maintenance staff enhances the quality of work and job market appeal. - Virtual technologies: Augmented reality (AR) and virtual reality (VR) are becoming crucial for on-site inspections.
AR enables professionals to place a camera in front of the machine and receive real-time notes and insights on a screen, facilitating timely maintenance and inspections.
How does a CMMS help with maintenance & reliability?
According to a survey conducted by Plant Services, training new M&R personnel is the industry's biggest challenge in 2023, with 31% of people voting for this problem.
Some of the most common challenges are:
- Training new M&R personnel – 31%
- Supply chain issues – 30%
- M&R labor shortages – 26%
- Maintenance debt/backlog – 14%
A CMMS software centralizes all information for effectively managing maintenance activities, asset management, and enabling data-driven decision-making.
This can further improve equipment reliability with predictive analysis, reduce maintenance costs, and optimize your maintenance operations.
What’s more, the implementation of effective CMMS will aid in incorporating reliability-centered maintenance (RCM) strategies that further enhance productivity, cost optimization, and increased O&M efficiency.
Case Study: IDC Study - How CMMS is Evolving Beyond Asset Management & Maintenance
Here's how a CMMS can improve maintenance and reliability:
- Better planning and scheduling: CMMS centralizes work orders and maintenance schedules, reducing downtime and optimizing workloads.
- Improved asset management: It improves asset management by monitoring equipment performance, preventing breakdowns, and optimizing asset utilization.
- Enhanced inventory management: It helps ensure that the right parts are in store when they are needed, reducing downtime and minimizing the cost of spare parts.
- Streamlined communication: It streamlines communication by providing real-time access to work orders and maintenance schedules.
- Better data analysis: Data analysis from CMMS provides insights to improve maintenance and reliability by identifying areas for improvement.
Facilio's cloud-based Connected CMMS solution provides a powerful suite of features that enable you to streamline and optimize your maintenance operations, boost equipment reliability, and maximize uptime.
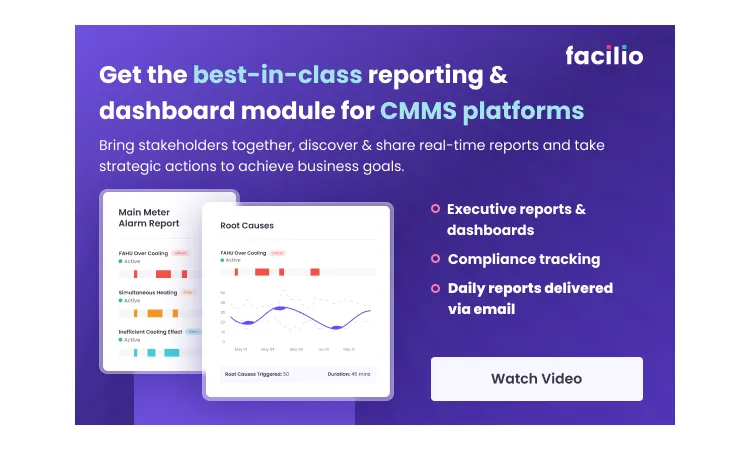
It offers AI-powered analytics and predictive maintenance capabilities that automatically identify potential issues before they occur and prevent them from becoming costly problems.
Further, with powerful workflows and automated work orders, from requests to resolution and quotes for service, you can finally bid goodbye to repetitive, tedious maintenance tasks and focus on important things that deserve your time and expertise.
Take the first step towards a more efficient and reliable maintenance system today by scheduling a demo today!