A complete guide to planned maintenance: what it is, its types, benefits, and how CMMS transforms facility upkeep from reactive to scalable.
Today’s facilities operate under tighter margins and higher expectations than ever. More systems to manage. More sites to oversee. More pressure from audits, SLAs, and cost controls. In this environment, “just keeping things running” is no longer a viable strategy.
And yet, that’s exactly what happens when teams rely on reactive or loosely scheduled maintenance—responding after breakdowns happen or defaulting to OEM schedules without visibility into what’s actually needed.
That’s where planned maintenance changes the game.
This guide walks you through everything you need to know about planned maintenance, including the different types, where and when to apply them, what a reliable planned maintenance workflow looks like when done correctly, and how you can ensure structure, visibility, and scalability across your maintenance programs with a modern CMMS solution.
What is Planned Maintenance?
Planned maintenance refers to any maintenance task that is scoped, resourced, and organized before a failure occurs. It’s a proactive approach that ensures the right assets get the right attention at the right time—with zero surprises and no guesswork.
Planned maintenance is a structured approach to maintaining equipment, assets, and facilities based on an intentional plan, rather than after a failure occurs. It specifies what tasks need to be done, how they’ll be performed, what resources and parts are required, and the sequence for execution.
Examples of planned maintenance
Planned maintenance spans every sector—from buildings to fleets to production lines—helping teams reduce failures, extend asset life, and stay compliant. Common examples include:
- HVAC SystemsFilter changes, coil cleaning, and seasonal tune-ups to sustain performance and indoor air quality.
- Vehicles & FleetsRoutine oil changes, brake inspections, and tire rotations—triggered by mileage or time.
- Manufacturing EquipmentLubrication, calibration, and wear-part swaps scheduled by runtime or usage data.
- IT InfrastructureRegular reboots, backups, and diagnostics to prevent downtime and data loss.
- Lighting & ElectricalLamp replacements and breaker checks—plus thermal scans to spot overloads.
- Elevators & ConveyorsSafety tests, inspections, and calibrations aligned with compliance requirements.
- Non-Critical AssetsLow-risk gear may follow a lighter planned maintenance strategy—or even run-to-fail—while still tracked for visibility.
Types of planned maintenance
Not all planned maintenance looks the same. Some tasks follow a precise calendar. Others depend on condition or usage thresholds. What defines them isn’t when they’re done—but that they’re deliberately scoped, resourced, and controlled in advance.
At a strategic level, there are two primary categories:
- Planned Scheduled Maintenance
- Planned Unscheduled Maintenance
1. Planned Scheduled Maintenance (Often Called Preventive or Scheduled Maintenance)
Planned scheduled maintenance is that which is both planned and scheduled with specific dates or intervals. It involves routine, calendar- or usage-based tasks that are performed regularly to prevent equipment failures.
This is what most teams picture when they think of “planned maintenance.”
Tasks are performed at fixed intervals, either based on time (e.g. every 3 months) or usage (e.g. every 1,000 hours).
Examples: Quarterly HVAC inspections / Monthly generator lubrication / Annual safety checks
Best for: Stable, high-usage assets with known service intervals.
2. Planned Unscheduled Maintenance
Planned unscheduled maintenance is that which is planned in terms of scope, resources, and procedures but not scheduled for a specific time because the exact timing depends on asset condition or unpredictable triggers.
Here’s where many teams get confused. This isn’t reactive—it’s proactive, but flexible.
This is a more adaptive form of planned maintenance, commonly used when failure patterns are variable or data-driven triggers are available.
Tasks are initiated based on real-time indicators, not pre-set timelines.
Examples:
- Replace motor belt only if vibration exceeds limit
- Calibrate equipment after 5,000 hours
- Swap batteries based on voltage drop
Best for: High-value or variable-use assets, CBM/PdM environments, and facilities using IoT monitoring or usage-based tracking.
See Facilio’s CMMS in Action
From calendar-based to condition-based, explore how Facilio adapts your planned maintenance workflows to scale smarter and perform better.
SEE A DEMOBenefits of planned maintenance in facility management
There’s a reason high-performing facility teams never treat maintenance as an afterthought—it touches everything. From your energy costs to technician morale, from tenant experience to regulatory readiness, the ripple effects of poor planning aren’t just operational—they’re strategic.
Planned maintenance builds predictability, controls costs, and protects uptime in an environment that doesn’t tolerate surprises.
The benefits and key aspects of planned maintenance are:
1. Reduced Emergency Repairs and Cost Overruns
Unplanned downtime is one of the most expensive risks in facility operations.
Implementing a planned maintenance program significantly lowers emergency repair expenses, reduces overtime, and cuts down on expedited parts shipping.
Facilities that implement proactive maintenance strategies see an average 40% reduction in emergency repair costs and up to 12% overall maintenance cost savings compared to reactive approaches.
2. Extended Equipment Lifespan and Performance
Most assets don’t fail due to catastrophic defects—they fail from neglect, misalignment, or wear that goes unnoticed. Planned maintenance catches those issues before they escalate.
By consistently performing inspections, cleanings, calibrations, and minor adjustments:
- You reduce stress on components
- You slow degradation
- You defer capital replacement costs
A full-scale predictive maintenance program integrated with CMMS can increase equipment uptime by up to 20% and extend asset life, delaying expensive replacements.
3. Improved Compliance and Safety Readiness
Auditors don’t just look for clean checklists—they look for consistency, traceability, and documented accountability. Planned maintenance programs:
- Ensure compliance with OSHA, ASHRAE, and industry-specific regulations
- Help centralize records of inspections, work orders, and asset history
- Prevent safety violations by keeping critical systems aligned and functional
4. Higher Technician Productivity and Morale
Firefighting wears down even your best techs. Planned maintenance gives your team a sense of rhythm and clarity:
- Workloads are spread evenly over time
- Repetitive tasks are automated
- Techs arrive on-site with parts, checklists, and context
5. Predictable Budgeting and Resource Allocation
When maintenance is driven by panic, budgets get wrecked. Overtime, premium shipping, overstocked inventory—it all adds up fast.
Planned maintenance:
- Levels out part ordering cycles
- Enables seasonal labor forecasting
- Reduces maintenance “surprise” costs that blow up forecasts
Over time, facilities using CMMS-backed planned programs transition from reactive cost centers to proactive, value-generating functions.
What are the four phases of planned maintenance?
Planned maintenance isn’t a one-size-fits-all tactic—it’s a layered strategy that helps facilities teams stay ahead of breakdowns, optimize costs, and ensure long-term asset performance. The four phases work together to balance urgency, risk, and resource availability across all asset types.
Phase 1: Corrective maintenance targets issues caught early—like a vibration or leak—before failure. It’s best for assets that can safely operate with minor faults. When paired with inspections and tracked through a CMMS, it avoids escalation without adding urgency.
Phase 2: Preventive maintenance is scheduled upkeep—based on time or usage—that keeps high-wear assets running reliably. It's ideal for compliance-heavy environments or anything with predictable degradation.
Phase 3: Risk-based maintenance shifts the focus from routine to relevance. Instead of servicing everything equally, teams prioritize based on failure impact. Fire safety systems may get weekly checks, while low-impact tools wait longer.
Phase 4: Predictive maintenance uses sensor data to detect when failure is likely—then intervenes just in time. It’s powerful, but not for everyone. Facilities without condition-monitoring infrastructure often struggle to justify the setup.
Many teams over-maintain low-value assets out of habit. RBM combined with a CMMS helps rebalance effort toward what actually matters.
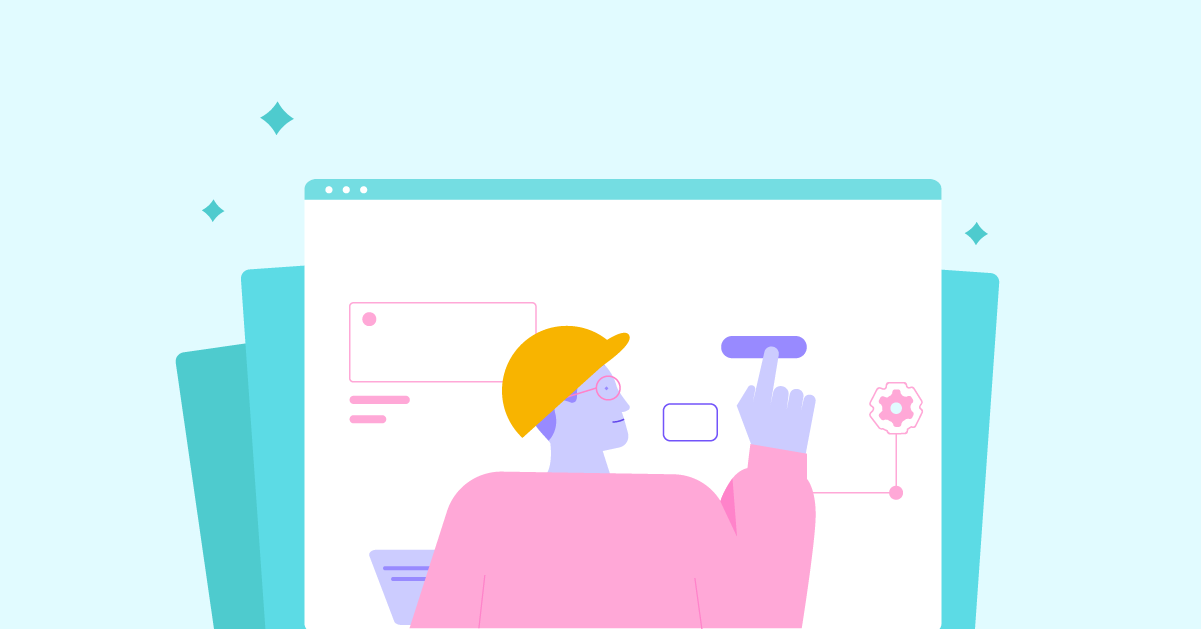
How to set up a planned maintenance workflow
As facilities grow more complex, maintenance workflows must evolve. This guide walks you through setting up a planned maintenance workflow that’s not just organized—but scalable, data-driven, and ready for multi-site operations.
Step 1: Build a Centralized Asset Inventory
Start by listing every maintainable asset—include make, model, location, install date, usage history, and operational criticality. This forms the foundation of your task logic, budget planning, and future analytics.
Pro tip: Assign each asset a criticality score (High / Medium / Low) to guide how frequently it should be maintained.
Step 2: Prioritize by Risk
Not all assets deserve equal effort. Sort assets by impact of failure—financial, operational, safety, or compliance-related. This step helps avoid blanket schedules and focus resources where they matter most.
Teams that skip this step often waste 30–40% of planned maintenance hours on low-value tasks.
Step 3: Define Maintenance Tasks by Asset Type
Create task lists tailored to each asset’s requirements. Include what needs to be done, how it should be performed, what tools are needed, and how long it takes. Here are resources to help you create a comprehensive task checklist:
- OEM recommendations
- Local regulatory requirements
- Past failure patterns
- Usage environments (e.g., humidity, load cycles)
Step 4: Build a Realistic, Balanced Schedule
Don’t overload your team with clustered preventive maintenance. Spread out tasks logically—by location, technician route, or operational windows. The goal isn’t to do everything. It’s to do the right things at the right time.
Step 5: Choose the Right Management Method
You need a dedicated planned maintenance system to handle the complexity of your business operations. If you're running a small site with limited assets, spreadsheets might hold—for now.
But as operations scale, manual tools break down:
- Technicians lose track of tasks or waste time on admin
- Supervisors struggle to balance workloads or ensure task compliance
- FM leaders lack visibility into costs, failures, and ROI
A CMMS helps centralize task tracking, automate schedules, assign work, and generate clean audit trails—without extra effort.
When to switch: If you're managing multiple sites, 50+ assets, or noticing recurring task misses, it’s time to move beyond spreadsheets.
Step 6: Train Your Team and Build Ownership
Ensure that maintenance staff understand the planned maintenance process, how to use any software tools, and the importance of completing tasks in a timely manner.
Your team isn’t just executing—they are the system. Walk them through why each task matters. Let them question, improve, and co-own the schedule. If it’s a top-down list they don’t believe in, it won’t stick.
Step 7: Monitor, Learn, and Adjust
Maintenance is a feedback loop. Track what’s getting done, what’s missed, and what’s breaking anyway. Recalibrate based on planned maintenance KPIs like:
- Planned Maintenance Completion %: Target 80%+ of work being planned, not reactive
- Unplanned Downtime: Track hours or incidents per month/quarter
- Cost per Asset: Maintenance spend per asset or asset group
- MTBF (Mean Time Between Failures): How long assets last before issues
- planned maintenance Compliance Rate: Are tasks getting done on time?
CMMS advantage: Real-time data helps shift from time-based to condition-based schedules when a clear pattern emerges.
How the Right CMMS helps you scale your planned maintenance
Spreadsheets might work when you’re managing 30 assets in one building. But add a second site, more compliance requirements, multiple vendors, and rotating tech teams—and it breaks. Tasks fall through the cracks, data disappears, and maintenance turns reactive all over again.
That’s why you need a CMMS. But not all CMMS platforms are built to grow with you.
Basic CMMS solutions help you digitize work order creation, task scheduling, and asset database. That’s helpful—but it’ll only get you so far.
Because your maintenance environment won’t stay the same. Asset age. Portfolios expand. Teams change. Compliance grows tighter. IoT sensors come into play. Expectations rise.
The CMMS you choose today needs to scale with all of that tomorrow.
So, what should you look for in a CMMS that’s truly built for scale?
You need a platform that adapts to asset usage, risk, and real-time data, connects teams across your portfolio, and integrates with BMS, IoT, and other systems.
This is where most CMMS platforms fall short.
What makes Facilio’s CMMS the best choice for planned maintenance
As a modern, cloud-based CMMS built to help facilities teams scale maintenance across their portfolio, Facilio doesn’t just automate planned maintenance workflows; it actively makes them smarter.
Here’s how:
- Dynamic Task Scheduling: Intervals automatically adapt based on asset behavior, runtime, or inspection outcomes—not just dates
- Portfolio-wide Visibility: Whether you manage five sites or 50, Facilio gives you real-time visibility into planned maintenance compliance, asset risk, and cost exposure across all locations
- Technician-First Mobile UX: Field teams can access WOs, SOPs, asset history, and record completions in real time—no back-and-forth, no second visits
- Condition-Based Triggering: Use sensor inputs, BMS integrations, or checklist logic to auto-initiate corrective tasks without waiting for breakdowns
- Embedded Intelligence: Spot chronic issues, over-maintained equipment, or high-cost failures with built-in analytics, not external reporting workarounds
When Al Tayer Group needed to manage over 140 sites and 70,000+ assets, spreadsheets and fragmented systems couldn’t keep up. Facilio partnered with Al Tayer to centralize asset tracking, automate work orders, and enforce consistent, portfolio-wide standards with its connected platform.
“The biggest success is that we control the data… our leadership team now has never-seen-before transparency across the entire portfolio operations, including vendor SLAs, compliance, and response times.”
— Thomas Sellwood, Group Facilities Manager, Al Tayer
Facilio didn’t just digitize their maintenance—it rewired it for visibility, control, and scale.
Whether you're a maintenance lead trying to reduce downtime, an operations manager forecasting costs, or a technician tired of repetitive tasks, Facilio equips each stakeholder with a smarter way to do their job.
Conclusion: Laying the Groundwork for Future-proof Maintenance workflows
Planned maintenance isn’t just a box to check—it’s how facilities stay safe, efficient, and financially predictable in an unpredictable world. But the truth is, getting it right at scale takes more than task lists and calendar reminders. It takes structure, adaptability, and visibility.
A CMMS lays that foundation. And choosing the right one matters more than ever. Because the way you maintain today shapes how well you perform tomorrow.
Some platforms help you go digital. Facilio helps you go further.
It brings everything into one connected system—aligning assets, people, and processes across your entire portfolio. Tasks aren’t just automated—they’re smarter, triggered by real-world usage and conditions. Teams aren’t siloed—they’re equipped with shared context, live updates, and full operational visibility.
Instead of managing site by site, you're orchestrating everything from a single, adaptive hub—built to scale with you, not slow you down.
Talk to our product experts now.
Get a firsthand look at how top FMs use Facilio to drive uptime, compliance, and cost control through smarter maintenance.
Frequently Asked Questions (FAQs)
What is the purpose of planned maintenance?
The core purpose of planned maintenance is to prevent equipment failures before they happen. By scheduling tasks in advance—based on time, usage, or risk—it minimizes downtime, lowers repair costs, and extends asset lifespan.
It also ensures regulatory compliance, improves workplace safety, and turns maintenance from a reactive burden into a strategic advantage.
What is the difference between scheduled and planned maintenance?
Planned maintenance defines what needs to be done, why, and how—including task procedures, tools, and required parts.
Scheduled maintenance takes it a step further by defining when and by whom those tasks will be executed.In short: planning creates the strategy; scheduling puts it into motion.
What are the four phases of planned maintenance?
- Corrective Maintenance – Fixes issues identified before full failure occurs.
- Preventive Maintenance – Regularly scheduled upkeep to avoid breakdowns.
- Risk-Based Maintenance – Prioritizes work based on asset criticality and failure impact.
- Predictive Maintenance – Uses real-time data and analytics to service assets just before failure is likely.
These layers work together to build a scalable, cost-efficient, and resilient maintenance strategy.
What is unplanned maintenance?
Unplanned maintenance is reactive work triggered by unexpected equipment failures. It’s unscheduled, often disruptive, and typically more expensive—requiring immediate attention, unplanned labor, and expedited parts. While some failures are inevitable, the goal of a strong planned maintenance program is to keep unplanned work to a minimum.
What is the difference between reactive and planned unscheduled maintenance?
Planned unscheduled maintenance is proactive in planning and preparation, even if timing is uncertain, whereas reactive maintenance is purely reactive, with no prior planning or resource allocation.