In just 5 minutes, discover why RCM is essential to high-performing operations. From aviation to manufacturing, learn the steps, examples, and how CMMS makes it easy.
What is Reliability-Centered Maintenance?
Reliability-Centered Maintenance (RCM) is a strategic approach focused on optimizing maintenance tasks to ensure asset reliability and functionality. It identifies critical equipment, analyzes potential failures, and prioritizes maintenance based on the impact of failures on operations, safety, and costs.
RCM combines preventive, predictive, and corrective maintenance strategies to maximize uptime, reduce costs, and improve safety.
Where is reliability-centered maintenance needed the most?
RCM is particularly vital in industries where equipment reliability is critical to safety, operations, and cost efficiency. Some of the key sectors include:
- Aviation: RCM originated in the aviation industry to enhance aircraft safety and performance.
- Oil and Gas: In this sector, RCM helps prevent equipment failures that could lead to safety hazards and environmental incidents.
- Manufacturing: RCM is used to maintain equipment reliability, ensuring consistent production quality and efficiency.
- Power Generation: RCM is applied to minimize equipment downtime, ensuring consistent power supply and operational efficiency.
Implementing RCM in these industries helps prevent failures, enhance safety, and optimize maintenance costs.
For instance, RCM has played a key role in the aviation industry, especially in preventing jet engine failures. Experts in the industry used RCM to identify critical failure points early so airlines could implement preventive measures.
This proactive approach not only ensured safer flights but also saved airlines from costly accidents and operational downtime. It set a high standard for reliability in maintenance across various industries.
Components of reliability centered maintenance
RCM methodology is a strategy to plan and maintain equipment, equipment failure, and reduce maintenance costs.
It's a preventive maintenance technique that helps avoid breakdowns by reducing variation in the life cycle costs of your assets.
RCM maintenance has the following components:
Centralization: Combining multiple maintenance functions into one service center allows you to perform asset management and improve work allocation. Companies of all sizes can use this, but it's instrumental when you have thousands or millions of assets across multiple sites. In addition, the centralization process will help ensure consistent standards are applied across your entire operation to maximize asset performance over time.
RCM measures: These are metrics used to evaluate how well resources perform relative to their expected output at each stage in their asset life cycle. This evaluation criterion gives you insight into potential functional failure and whether your systems are functioning as intended so that future improvements can be made if necessary; it also helps identify where new problems may arise so they can be addressed before they become significant issues (and thus expensive fixes).
Reliability growth objectives: These objectives should include increasing capacity utilization rates while decreasing downtime costs per unit produced/served, improving reliability through preventive maintenance tasks like routine inspections, maintaining proper calibration levels for equipment sensors, and more.
Suggested reads:
How to measure asset reliability with a bathtub curve?
A Quick Guide to Avoid Getting Pencil Whipped!
Why is RCM important for industries?
RCM is vital for industries that directly impact human lives, especially those mentioned above. It plays a crucial role in ensuring safety, efficiency, and reliability across these sectors for several key reasons.
- Enhanced safety: RCM helps identify potential failures before they cause catastrophic incidents. In aviation, for example, early detection of engine component issues through RCM can prevent in-flight failures, ensuring passenger safety.
- Cost efficiency: By focusing on critical equipment, RCM helps prioritize maintenance efforts, reducing unnecessary tasks. In oil and gas, this means avoiding costly equipment overhauls and reducing downtime by addressing the most pressing issues first.
- Operational continuity: RCM maximizes equipment uptime, which is essential for industries like manufacturing. For instance, RCM in a factory setting can prevent unexpected machine breakdowns, ensuring continuous production without costly interruptions.
- Regulatory compliance: RCM helps companies meet industry standards and regulatory requirements. For example, in the power generation sector, RCM ensures that plants meet safety and operational regulations, avoiding penalties and maintaining a reliable energy supply.
- Resource optimization: RCM ensures resources are used wisely, directing maintenance efforts only where needed. In the oil and gas sector, this minimizes unnecessary maintenance tasks and allocates resources to areas with the highest risk of failure, improving efficiency.
Suggested read: How to perform Facilities Condition Assessment?
7 key questions you should not overlook in reliability-centered maintenance
The RCM process includes a set of seven questions designed to analyze and improve asset management and maintenance strategies.
The goal is to understand better how each asset operates, what could go wrong, and how to prevent or mitigate those failures. The process involves addressing seven key questions for each asset:
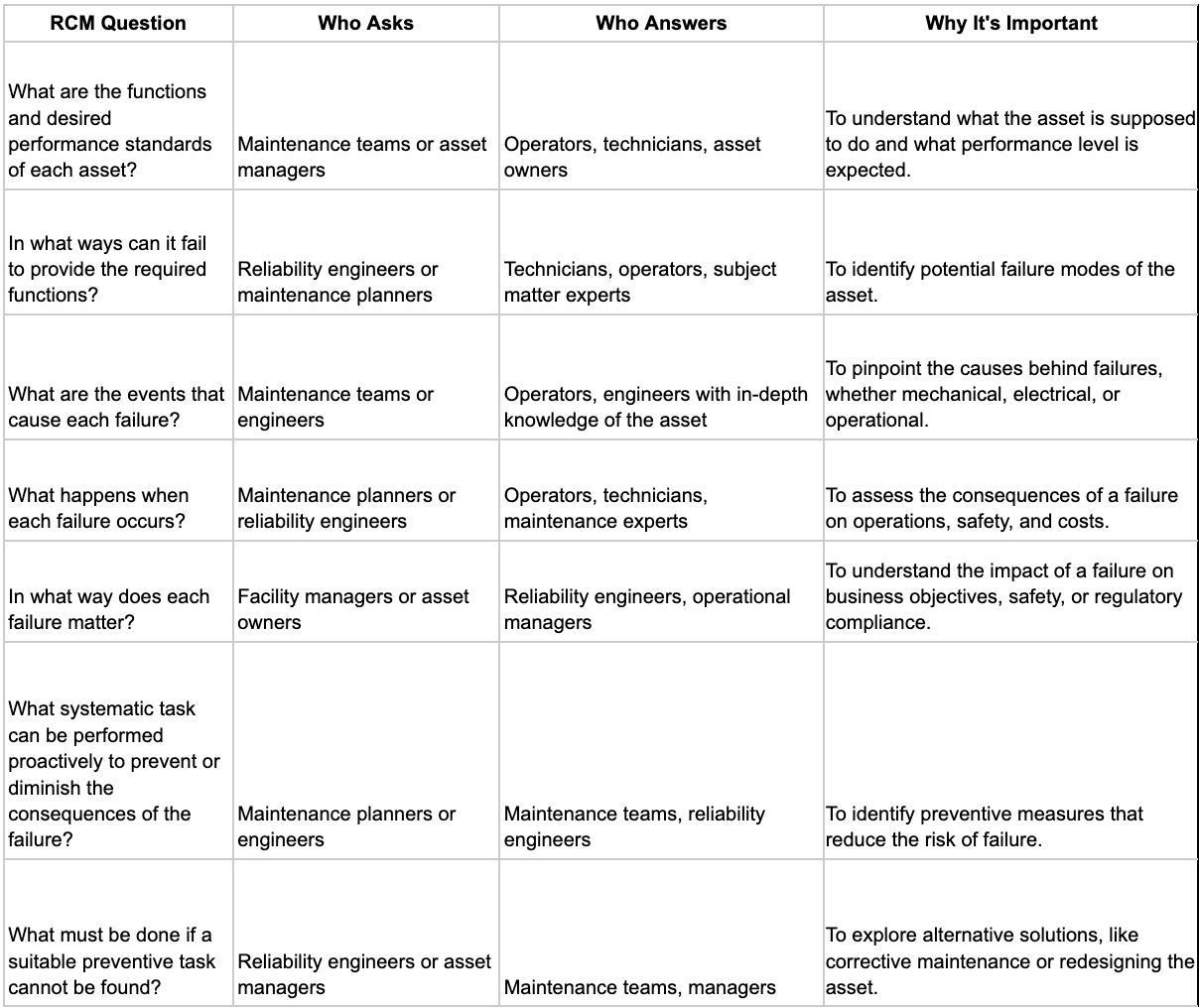
Get in touch today and learn how Facilio helps you perform RCM activities with ease.
The RCM process: A comprehensive 7-step guide for effective implementation
Without a doubt, RCM is a powerful strategy that helps organizations achieve optimal performance, minimize downtime, and reduce maintenance costs. However, implementing RCM effectively requires a well-defined, step-by-step approach.
So, we have devised an expert-driven, actionable framework for integrating RCM into your maintenance strategy.
Step 1: Identify critical assets for RCM Analysis
The first step in implementing RCM is to determine which equipment and systems warrant analysis. This process starts with a criticality analysis to assess the potential impact of equipment failure on operations, safety, and financial outcomes.
Key considerations:
- Assess the cost of failure and its effect on production, safety, or the environment.
- Prioritize high-value assets or those critical to the facility’s core functions.
- Consider historical maintenance costs and the frequency of failure.
This step ensures that RCM focuses on what matters most.
Step 2: Define system boundaries and functions
Once you’ve selected the assets, the next step is to define the systems that house these critical components. This includes understanding the role of the asset within the larger system, its inputs, outputs, and overall function.
For example, a conveyor system used to transport goods:
- Inputs: Goods and mechanical energy (powered by motors).
- Outputs: Finished products delivered to the next stage of production.
- The function of the system is to transfer goods efficiently, which must be assessed in relation to its parts.
By setting clear boundaries, you ensure all components affecting performance are considered.
Step 3: Identify failure modes
The third step involves systematically identifying all the potential ways each system can fail to meet its desired function. This requires collaboration among maintenance teams, operators, and engineers to ensure every possible failure scenario is explored.
Examples of failure modes:
- The conveyor belt could fail to carry goods due to slippage or excessive wear.
- A motor could experience overheating, causing it to shut down unexpectedly.
Identifying failure modes is essential to understanding what could go wrong and why.
Step 4: Root cause analysis
After failure modes are identified, the next step is to understand the underlying causes. This is where deep expertise is required to differentiate between symptoms and root causes.
Methods for root cause analysis:
- Conduct fault diagnostics with maintenance technicians.
- Review historical maintenance logs for recurring issues.
- Involve equipment experts to inspect designs or material choices that could be contributing to failure.
Example:
- A failed bearing might be traced to poor lubrication practices, which could be rectified by introducing a better lubrication schedule.
Accurately diagnosing root causes ensures that corrective actions address the true problem rather than just the symptoms.
Step 5: Evaluate the consequences of failure
In this step, each failure mode is evaluated for its potential impact on operations, safety, and finances. This is a critical phase where the severity and probability of failure must be assessed.
Techniques used for evaluation:
- FMEA (Failure Modes and Effects Analysis) to quantify the risk of failure.
- FTA (Fault Tree Analysis) to identify potential fault paths.
- RBI (Risk-Based Inspection) for prioritizing critical failure modes based on risk.
Example:
- The failure of a pressure relief valve could lead to a catastrophic explosion, whereas a vibration in a pump might result in minor operational disruptions. These differences must be considered when determining the priority of corrective actions.
Evaluating failure consequences ensures that resources are focused on preventing the most severe risks.
Step 6: Select the appropriate maintenance strategy
With failure modes prioritized, the next step is to choose the most effective maintenance strategy. The chosen tactics must be both technically feasible and economically viable for each identified failure mode.
Common strategies include:
- Condition-Based Maintenance (CBM), which uses monitoring tools to detect early signs of failure.
- Time-Based Preventive Maintenance (PM), which schedules maintenance tasks at regular intervals.
- Run-to-Failure, where the asset continues operating until it fails but is replaced quickly.
Example:
- For a motor, condition-based monitoring might detect increased vibration or temperature, allowing for corrective maintenance before a complete failure occurs.
- For less critical assets, a run-to-failure approach may be more cost-effective.
Selecting the right strategy ensures you apply the most efficient and effective maintenance methods.
Step 7: Implement and Continuously Review Maintenance Strategies
The final step in the RCM process is to implement the selected maintenance strategies and ensure they are carried out consistently. Regular performance reviews and feedback loops are necessary to gauge effectiveness and make adjustments as needed.
Continuous review activities:
- Track key performance indicators (KPIs) such as downtime, mean time between failures (MTBF), and maintenance costs.
- Conduct post-maintenance reviews to determine if maintenance actions were successful.
- Implement scheduled audits to ensure strategies remain relevant and effective.
Example:
- After implementing a new preventive maintenance schedule for a cooling fan, the team monitors the fan's performance over time to verify the reduction in failures and operational disruptions.
This step is essential for refining RCM practices and ensuring they evolve with the needs of the organization.
Reliability-Centered Maintenance vs Preventive Maintenance vs Predictive Maintenance: What’s the difference?
It’s understandable that people often confuse RCM with preventive and predictive maintenance, as these terms are sometimes used interchangeably. However, each approach serves a distinct purpose and is based on different strategies for maintaining equipment and ensuring reliability.
Here’s a comparison between Reliability-Centered Maintenance (RCM), Preventive Maintenance (PM), and Predictive Maintenance (PdM) to help clarify their differences and uses:
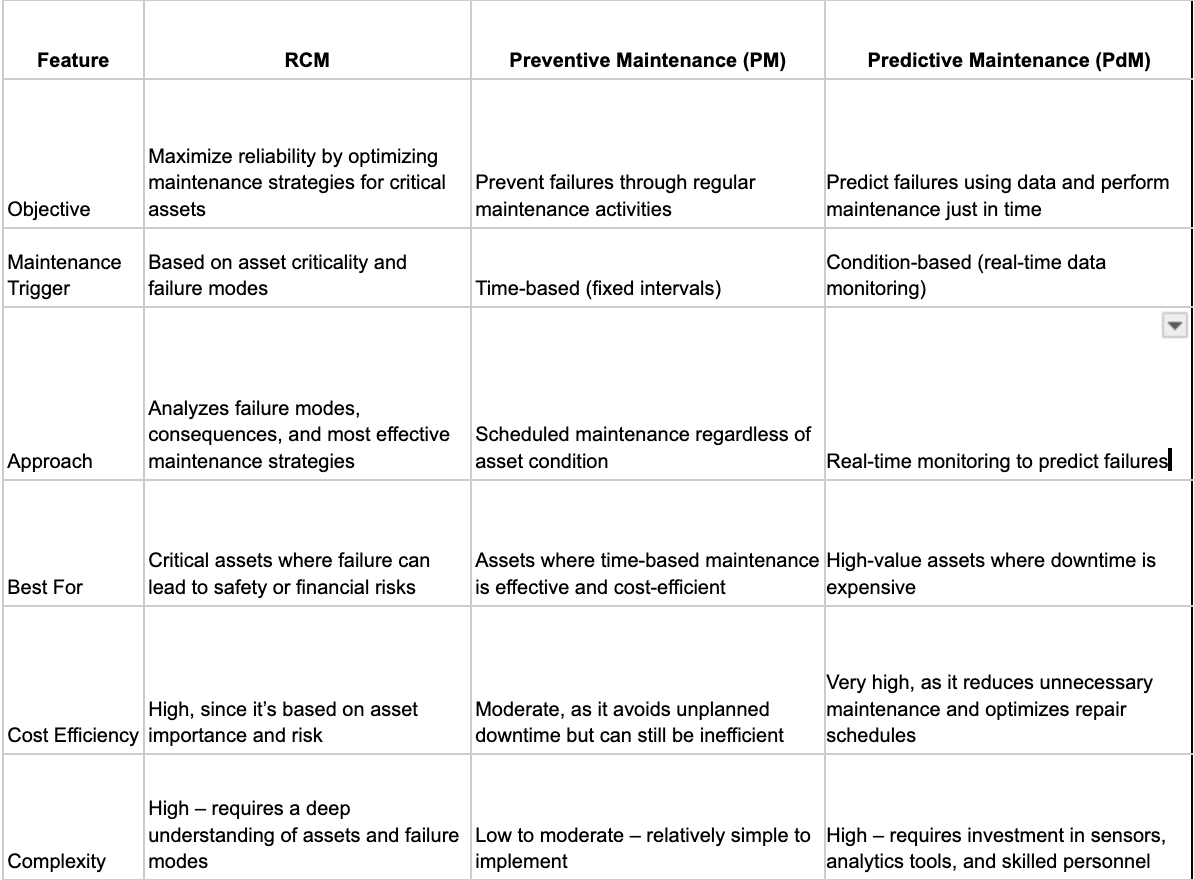
Summary
- RCM is a comprehensive, systematic approach that prioritizes maintenance efforts on critical assets based on their impact, risk, and function.
- Preventive Maintenance is a time-based approach to reduce the likelihood of failures through regular maintenance tasks. Over here, the maintenance is scheduled regularly regardless of asset condition.
- Predictive Maintenance uses real-time monitoring and data analytics to forecast when an asset will likely fail, allowing for maintenance to be performed just in time.
Each strategy has its strengths and is suited to different needs, but RCM is typically the most robust for complex and critical systems where optimizing maintenance efforts is crucial.
Check out the 10 Best CMMS Software in 2025!
How does a Connected CMMS help in effective RCM implementation?
Implementing RCM is not just an option; but a fundamental pre-requisite for organizations aiming to boost asset reliability and operational efficiency. A Connected CMMS like Facilio's can significantly streamline this process.
Here’s how Facilio's Connected CMMS can help you in seamless RCM implementation:
- Centralized data management: Facilio consolidates all maintenance data, including equipment history, failure modes, and repair costs. The dashboard is also capable of sharing a bird’s eye view essential for effective RCM analysis.
- Automated workflows: Facilio automates all your workflows, ensuring adherence to RCM strategies and reducing manual errors. This automation enhances efficiency and consistency in maintenance operations.
- Real-time monitoring: Facilio's integration with IoT devices enables real-time monitoring of equipment conditions, facilitating predictive maintenance and timely interventions.
- Seamless integration: Designed with an API-first approach, Facilio integrates effortlessly with existing systems, ensuring a smooth transition and minimal disruption during RCM implementation.
- User-friendly interface: The platform's intuitive interface simplifies the management of complex maintenance tasks, making it accessible for teams with varying technical expertise.