10 Essential Steps for Establishing an Effective Maintenance Program
Traditional maintenance programs emphasize adherence to rigid schedules and predefined plans. However, the reality is that the dynamics of business environments are constantly evolving.
Adhering to a one-size-fits-all approach for maintenance can be detrimental. Maintenance goals should be tailored to each asset's unique needs and desired outcomes.
In this article, we'll guide you through ten essential steps that will help you develop a maintenance program that ensures the smooth operation and long-term health of your assets.
10 steps to develop an effective maintenance program
How do you create an effective maintenance program that truly works?
Short answer: By embracing flexibility and adaptability instead of blindly sticking to rigid frameworks.
Effective maintenance management requires continuous improvement. Whether it is your first time designing a maintenance program or you're looking for ways to improve it - you should regularly revisit and revise these 10 things for the best operational outcomes.
Step 1: Assess your assets and define maintenance goals
Before diving headfirst into a maintenance program, assessing your assets is crucial. What are the key components of your operation? What are the critical systems, machinery, or infrastructure that demand regular attention?
Take stock of your assets and prioritize them based on their importance and impact on your business. Once you've done that, define clear maintenance goals.
Do you aim to reduce unplanned downtime? Enhance asset lifespan? Boost productivity? Identifying your objectives will help you create a targeted program.
Step 2: Gather data and analyze performance metrics
Data is the backbone of any successful maintenance program. Dive into the numbers and identify patterns or trends.
Are there specific assets that require more frequent repairs? Are there common issues that arise? You can pinpoint areas that need improvement and develop strategies to address them.
While data is undeniably valuable, relying solely on numbers without considering the broader context can be misleading. Complementing quantitative data with qualitative insights, such as equipment usage patterns, operator feedback, and maintenance history, is essential.
With a holistic approach to data analysis, you can uncover hidden opportunities and make informed decisions based on a comprehensive understanding of your assets.
Suggested read: Creating A Strategic Asset Management Plan (SAMP) With Five Handy Steps
Step 3: Determine maintenance strategies
Once you understand your assets and performance, it's time to determine the best maintenance strategies for each. There are various approaches to maintenance, such as reactive, preventive, predictive, and proactive.
Reactive maintenance (RM) involves fixing assets after they break down, while preventive maintenance aims to prevent failures through scheduled inspections and routine tasks.
Preventive maintenance (PM) has long been hailed as a cornerstone of effective asset management. However, blindly implementing a preventive maintenance strategy can be wasteful and inefficient.
Instead of adhering to rigid schedules, organizations should adopt a proactive approach that combines preventive and predictive maintenance techniques.
You can leverage real-time data and advanced analytics to identify and address potential issues before they escalate, maximizing uptime and minimizing unnecessary maintenance activities.
Step 4: Establish maintenance schedules and workflows
Now that you've chosen your maintenance strategies, it's essential to establish clear schedules and workflows. Create a comprehensive maintenance calendar that outlines when tasks should be performed.
Consider factors such as asset criticality, historical failure rates, and equipment manufacturer recommendations. Develop workflows that detail who is responsible for each task, how it should be executed, and any necessary documentation or reporting procedures. Clear communication and accountability are vital to the success of your maintenance program.
Suggested read: From Breakdowns to Breakthroughs: Understanding the Benefits of Preventive Maintenance
Step 5: Invest in training and skill development
A maintenance program is only as good as the people behind it. Ensure that your maintenance staff receives adequate training and skill development opportunities. Equip them with the knowledge and expertise needed to carry out their tasks effectively.
Training can range from technical skills specific to your assets to broader areas such as safety protocols, problem-solving, and communication. Invest in your team, and they will become the backbone of your maintenance program.
Step 6: Implement a CMMS
A Computerized Maintenance Management System (CMMS) is a powerful tool that can streamline your proactive maintenance efforts. CMMS software allows you to automate maintenance schedules, track work orders, manage spare parts inventory, and generate reports on equipment performance.
Facilio's Connected CMMS goes a step further to help you automate everything from inspections, work order, condition monitoring, and vendor and service management to proactive actions based on real-time operating conditions from your assets using IoT sensors.
When Facilio records equipment operating outside its defined parameters, it uses powerful workflow orchestrations to raise alarms and automatically take appropriate action, like executing self-set-point corrections or creating and dispatching work orders to the appropriate available technicians, with a maintenance checklist and inventory details all attached to the work order.
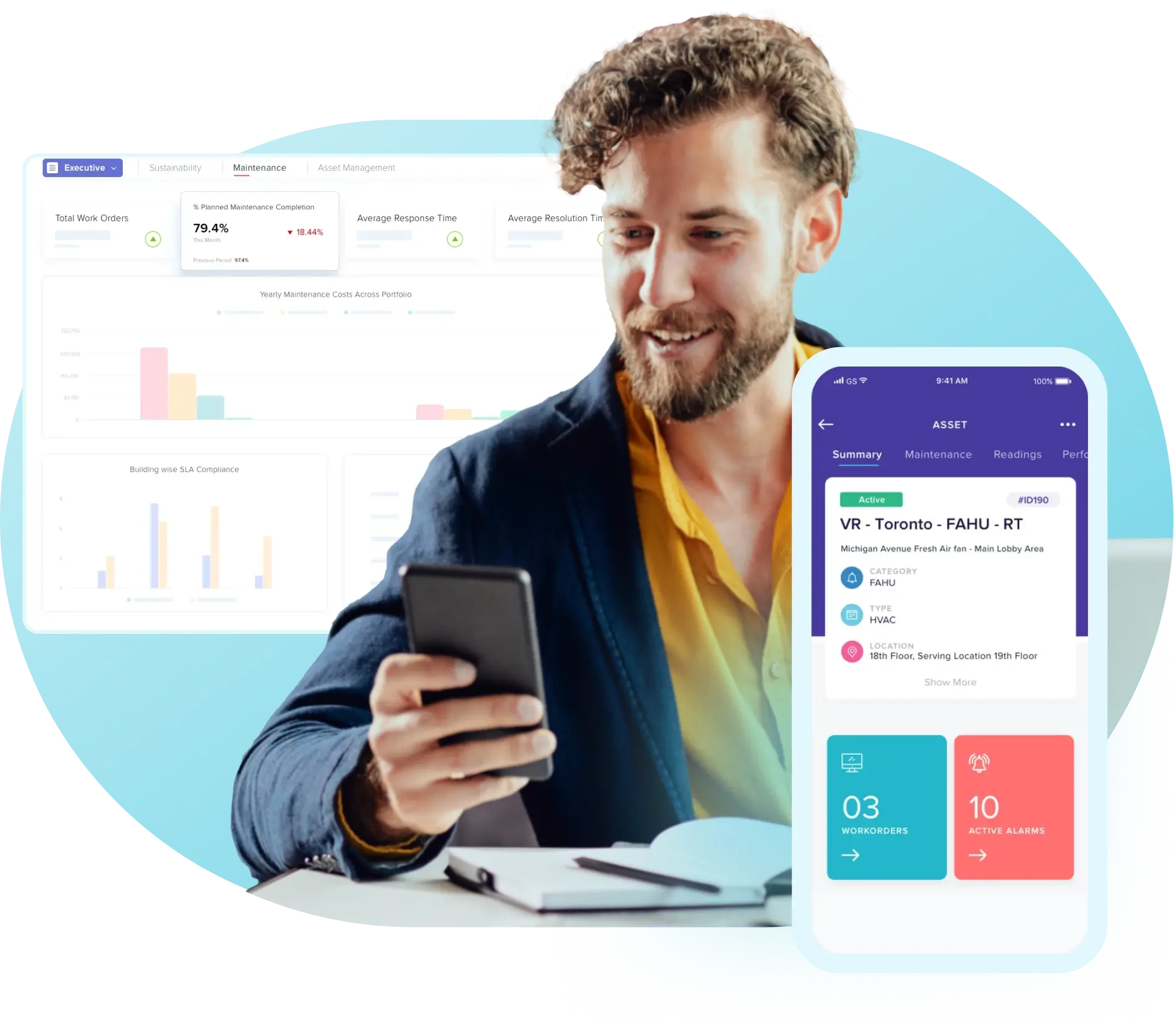
Unify portfolio-wide O&M with Facilio's Connected CMMS
Turn asset management strategies into agile, connected, experience-first operations.
Step 7: Implement a robust spare parts management system
Nothing slows down maintenance more than a lack of spare parts. Establish a well-organized spare parts management system to ensure you have the necessary components readily available when needed.
The conventional approach to spare parts inventory advocates for stocking a wide range of components to minimize equipment downtime. However, this strategy often leads to excessive costs, storage challenges, and obsolescence risks.
Instead, you can embrace a just-in-time philosophy to optimize spare parts inventory by prioritizing critical components and partnering with reliable suppliers.
Facilio intelligently detects inventory levels and places purchase orders with your best vendors to ensure your maintenance technicians have all the spares they need to carry out work orders to perfection.
This lean approach ensures that the right parts are available when needed, eliminating waste and streamlining operations.
Step 8: Continuously improve your maintenance program
Creating an effective maintenance program is not a one-time task; it requires continuous improvement. Regularly review the performance of your program and analyze the results.
Are your maintenance goals being met? Are there any gaps or inefficiencies in your processes?
Seek feedback from your maintenance team and other stakeholders involved. Engage in discussions and brainstorming sessions to identify areas that need refinement.
Maintaining a proactive approach to program improvement helps you adapt to changing operational needs and maximize the effectiveness of your maintenance efforts.
Step 9: Foster a culture of preventive maintenance
Preventive maintenance is the cornerstone of a successful program. Encourage a culture that values proactive measures and preventive actions.
Educate your workforce about the importance of regular inspections, lubrication, and cleaning. Emphasize the significance of early detection and prompt resolution of minor issues before they escalate into major problems.
Reward and recognize employees who actively contribute to preventive maintenance efforts.
Step 10: Monitor, measure, and celebrate success
Lastly, monitor and measure the success of your maintenance program using KPIs. Track metrics such as mean time between failures (MTBF), mean time to repair (MTTR), and overall equipment effectiveness (OEE).
Regularly review these metrics to assess the impact of your maintenance program on productivity, asset performance, and cost savings. Celebrate milestones and achievements with your maintenance team to foster a sense of accomplishment and motivation. Recognize their efforts and the positive outcomes of your program.
Improve asset reliability with proactive maintenance programs
A prevalent misconception is that maintenance programs solely revolve around the care and repair of equipment. However, a truly effective maintenance program should embrace a holistic approach to asset management.
You can achieve sustainable and responsible asset management by considering factors such as environmental impact, energy consumption, and resource optimization.
Remember, maintenance is not just a necessary chore; it's an opportunity to optimize your operations and achieve long-term success with productivity and costs.