Using internet of things (IoT) technology in facilities management (FM) presents more opportunities to improve operational efficiency and savings for businesses. More enterprises are transforming their facilities into smart buildings by leveraging the technology and adopting compatible software platforms.
The National Informatics Centre (NIC) goes even further, predicting that by 2025, internet nodes might be embedded in everyday items like food packages, furniture, and even paper documents.
These statistics highlight the pervasive nature of IoT and its transformative potential in various sectors, including facilities management.
Effective monitoring, management, and resource optimization are essential in today's commercial buildings. Energy management, video surveillance, access control, and environmental monitoring are integral to this equation.
The U.S. Energy Information Administration reports that energy consumption in the U.S. is around 9% of GDP, amounting to about $1.3 trillion annually. Globally, residential and commercial buildings account for over 40% of total energy consumption.
IoT technology enhances building energy efficiency through smart heating, ventilation, and air conditioning (HVAC) control, enabling owners, operators, and facility managers to improve asset reliability and efficiency, thus reducing energy consumption and environmental footprint.
Historically, "smart buildings" had automation systems that allowed remote control but were often siloed and unable to communicate with each other.
Last year, we surveyed over 180 leaders in the smart buildings industry, asking them nuanced questions about their thoughts and insights. As a result, we developed a step-by-step guide to unlocking your smart building’s potential.
Read all about it here:
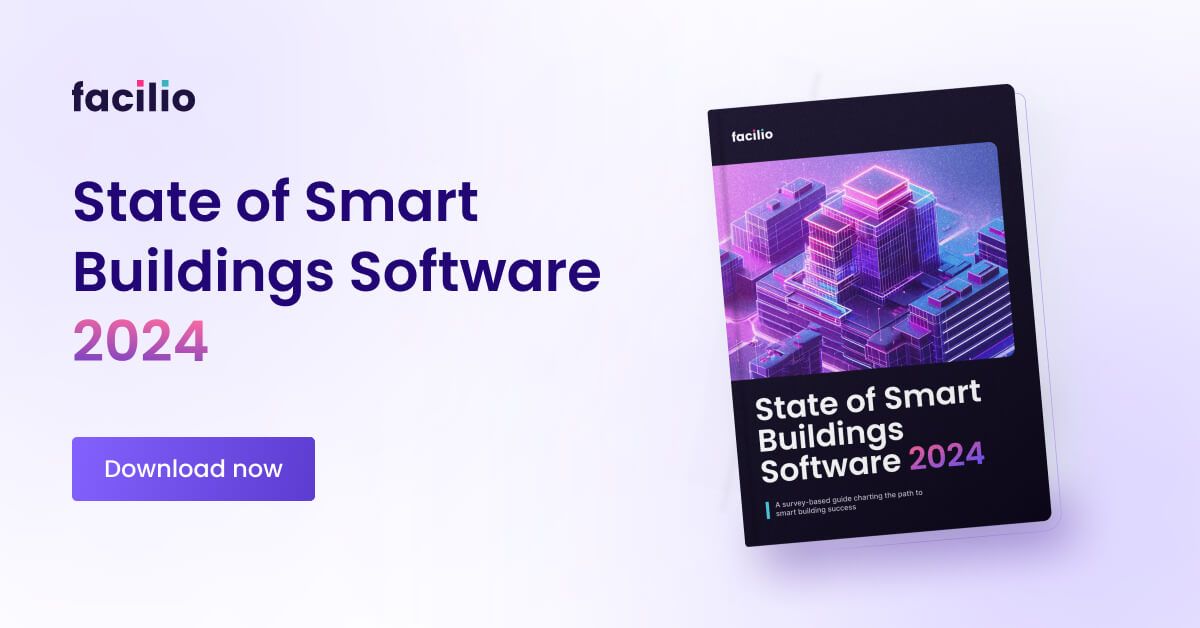
Today, IoT facility management technology enables data collection and sharing between components, fostering a more integrated approach. Real-time data collection on specific building areas informs adjustments to automation protocols.
For example, occupancy sensors might reveal that specific departments frequently work long hours. Over time, this data can be used to modify settings for those areas, ensuring that the building more effectively meets the occupants' needs.
Let’s take a closer look at how IoT in facility management is leveraged for efficient operations and maintenance (O&M).
Operational inefficiencies in traditional facilities management
Traditional facility management systems often rely on outdated technology and manual processes, forcing property operators to work within the confines of predefined workflows, hindering their ability to provide customized, truly customer-centric experiences.
Here are some challenges posed by these antiquated methods and what O&M teams are missing out on as a result:
Lack of real-time data
- Time-consuming processes: Manual logging of data from equipment status, energy use, and maintenance activities consumes significant time and labor.
- Delayed reporting: Without real-time data, O&M teams must wait for periodic reports to understand the state of their facilities, leading to delayed responses to emerging issues.
Inefficient maintenance practices
- Reactive maintenance: Many legacy systems follow a reactive-only model, where issues are addressed only after they occur. This leads to increased downtime and higher repair costs.
- Lack of predictive analytics: Without IoT sensors and data analytics, proactively predicting equipment failures and scheduling maintenance is nearly impossible.
Poor resource utilization:
- Manual scheduling: Scheduling maintenance and repairs manually can lead to inefficiencies, such as overlapping tasks, underutilized staff, and missed maintenance windows.
- Ineffective asset management: Without real-time tracking of assets, it's difficult to optimize their use and placement, leading to overutilization, underutilization, and increased wear and tear.
Communication barriers
- Siloed systems: Systems that do not communicate with each other cause isolated data pools, making it difficult to get a comprehensive view of operations.
- Manual coordination: Communication between teams, departments, and important stakeholders often relies on manual processes, leading to delays and miscommunications.
Limited scalability
- Difficulty in expansion: Scaling traditional facilities management practices to accommodate growth or new locations can be challenging due to the need for more flexibility of these systems.
- Inconsistent practices: Ensuring consistency across multi-site locations is difficult without centralized, standardized, and automated systems.
Examples of problems solved by modern technology
Modern technology, however, offers transformative solutions to FM management. Leveraging IoT, artificial intelligence (AI), and machine learning (ML) can solve many real-world problems and vastly improve facility management systems like:
Energy management: A facility using manual controls for HVAC systems may experience fluctuating temperatures and energy wastage.
IoT-led software can use sensors to monitor the temperature and humidity of HVAC systems in real time, while AI algorithms dynamically adjust the settings to optimize comfort and energy use.
Work order management: In a large commercial building, maintenance teams often struggle with coordinating repairs and upkeep across multiple floors and departments.
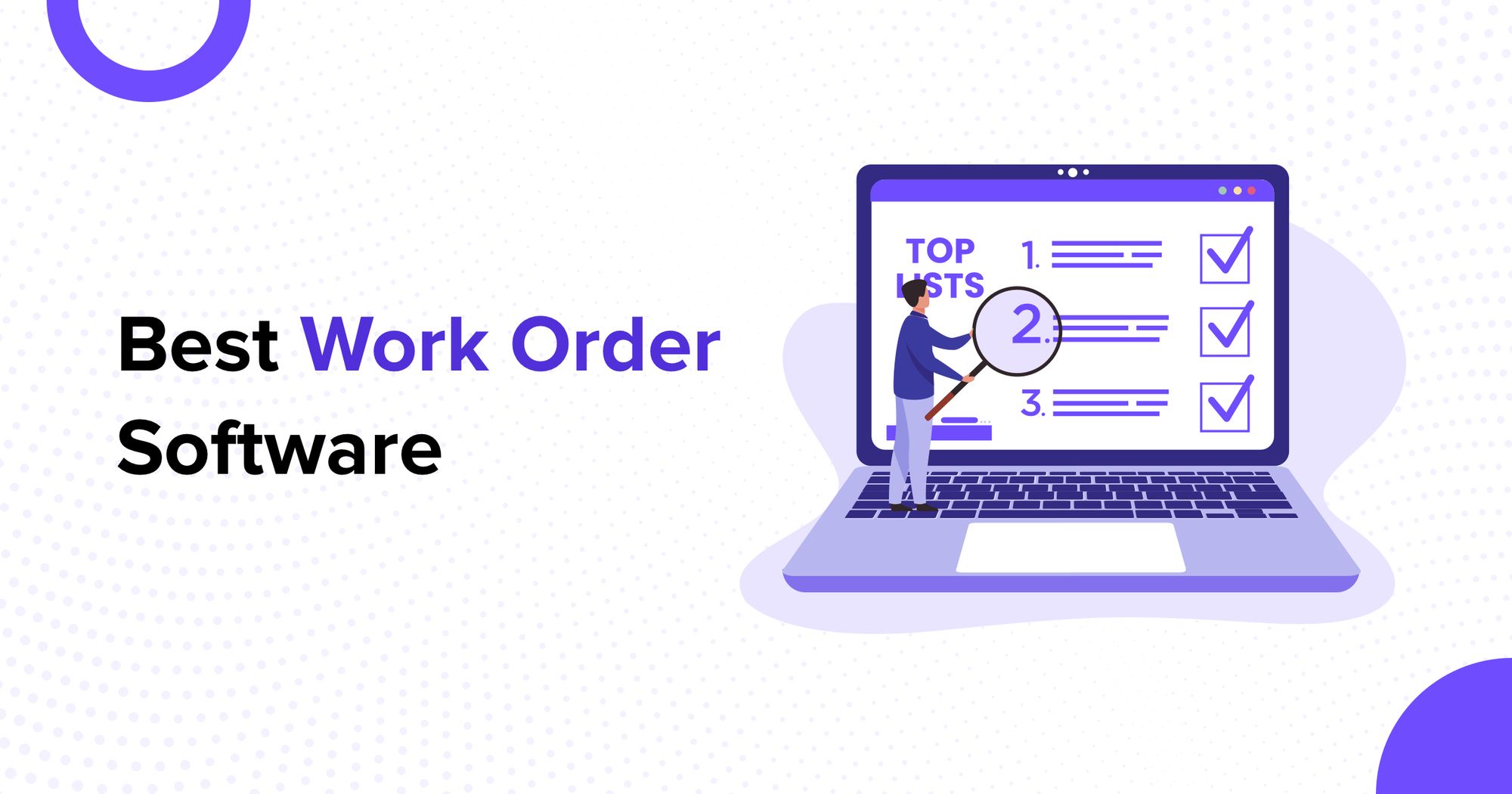
IoT-led software automates work order creation and assignment based on priority and asset criticality. It provides real-time updates on work progress and status changes and enables technicians to access and update work orders remotely.
Asset management: Traditional asset tracking methods, such as manual logs or basic barcode systems, often cause misplaced items, delays in locating critical equipment, and inefficiencies in inventory management.
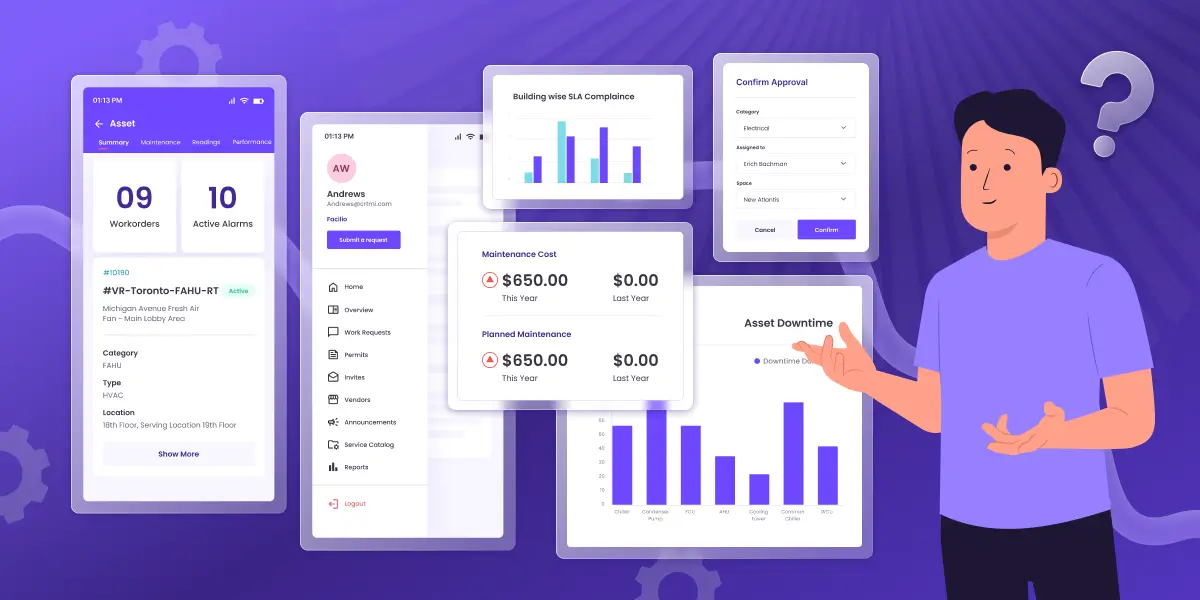
IoT software automates inventory checks and reorder processes based on asset usage and depletion. You can attach radio frequency identification (RFID) tags to monitor assets' real-time status within the facility.
Environmental monitoring: Environmental compliance and occupant health are critical concerns in any facility.
IoT sensors monitor indoor air quality (IAQ), temperature, and humidity levels continuously. Alerts are triggered for deviations from set parameters, allowing facility managers to take immediate corrective actions to maintain a healthy and comfortable environment.
Data analytics: With remote monitoring tech, you can process and analyze large volumes of data generated by IoT sensors to derive actionable insights.
AI and ML help forecast trends, identify patterns, and recommend improvements to enhance overall facility performance and reduce costs.
Common examples of IoT devices in commercial buildings
IoT devices have varied applications depending on industry and use cases. While this is not a comprehensive list, here are some of the most common IoT devices used in facility management:
- IoT sensors for condition monitoring
- Beacons for asset monitoring and security management
- RFID trackers for asset tracking, inventory management, and location tracking
- NFC (Near Field Connectivity) or QR codes for stock monitoring
- Occupancy sensors for room scheduling and reservations
Trends in facility management technologies
IoT technology combined with robust facility management software gives facility managers the real-time operational insights they need to optimize operations and maintenance (O&M) remotely.
If you're responsible for managing a facility, it's important to stay up-to-date on the latest trends in the industry. We’ve collected the latest trends that have helped facility managers across the globe drive data-driven facilities.
Let’s dive right in.
Data analytics
Data analytics are a powerful tool used in facility management to deliver high-performing buildings.
For example, data analytics record operational data for equipment and study their maintenance/repair patterns, alerting managers to potential issues before they become problems.
Additionally, data analytics help optimize energy consumption, allowing businesses to identify areas where conservation efforts can be made.
Remote monitoring
By using technology to monitor building systems and equipment remotely, facility managers save time and money while improving operational efficiency.
Perhaps the most common example of remote monitoring technology is CMMS software.
It collects real-time data from building automation systems (BAS) and monitors them continuously to identify anomalies and automatically create work orders for maintenance and repairs.
This way, FMs are always on top of their building performance, and optimize continually for maintenance efficiency.
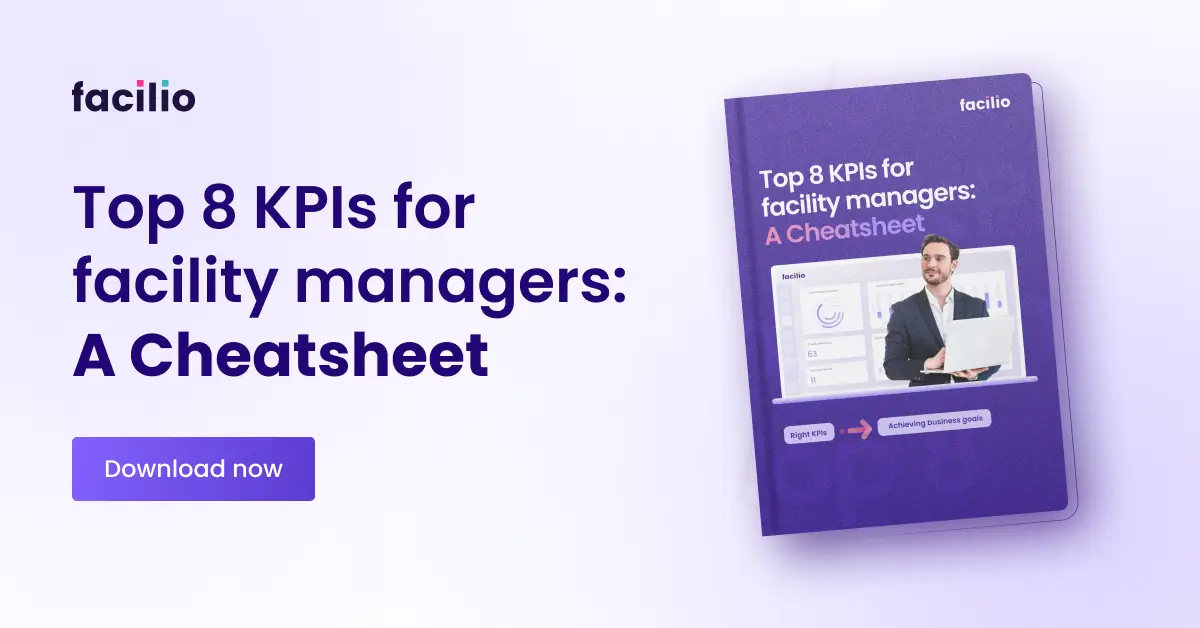
Interoperability using third-party integrations
Building automation systems collect real-time operational data from equipment and buildings that supervisory software need for data analysis.
However, most BAS usually come with a data-lock in problem that prevents data from flowing freely between tools and systems.
Often, minor changes like revising normal operational parameters and creating maintenance work orders have to go through the BAS vendor, which creates delays and inefficiencies and is not scalable for portfolio operations.
Fortunately, there is a better alternative to this painful process - deploying a cloud-supervisory platform like Facilio for O&M management.
Platforms bypass the data lock-in problem, connecting site-level systems and cloud supervisory systems to enable portfolio operations.
Suggested read: Best Building Management Software
IoT and machine learning for predictive analytics
IoT and machine learning are two powerful technologies used in predictive analytics for facility management.
IoT devices, such as occupancy sensors, vibration analysis, oil analysis, and many more, collect real-time operational data that is then analyzed using AI to provide insights into how facilities are being used and how they can be improved.
AI-powered facility management software uses predetermined parameters to identify potential issues ahead of time, determine the root cause, and recommend how to fix them.
Predictive and prescriptive analytics eliminate unplanned downtimes and optimize asset maintenance work while supercharging your preventive maintenance programs.
Suggested read: #5 Questions With Building IoT Expert
Cloud capabilities for facility management
Cloud supervisory platforms like Facilio help meaningfully integrate data from people, processes, and systems to unlock real-time portfolio-wide optimization, data-driven decision-making, and maintenance efficiency that boosts productivity, improves safety, and reduces costs.
With a cloud supervisory platform, facility managers can access performance data across buildings in one place. If a building is performing better than the rest, a cloud supervisory platform analyzes why that is, and how to apply learnings to create a high-performing portfolio.
Suggested read: The Future of Buildings and Real-time Facilities Experience
Applications of IoT technology in facility management solutions
- Fault detection and diagnostic (FDD)
- Data-driven repair or replacement decisions
- Optimization of preventive and predictive maintenance programs
- Reduce carbon footprint with automated energy consumption management
- Reduce operating and maintenance costs
- Efficient resource utilization and boosting productivity
- Increased safety for field professionals and technicians
- Delightful occupant experiences
Build more efficient facility management solutions with Facilio’s IoT-led platform
Facilio’s O&M platform leverages IoT technology to gather and centralize difficult-to-access building data. This enables the real-time optimization of HVAC systems and overall building performance, promoting effective sustainability measures and enhancing the tenant experience—all from a single platform.
Facilio partners with estate owners and operators to deliver real-time insights into building performance, allowing proactive interventions instead of traditional reactive measures.
Facilio helps bridge the gaps that pose issues with optimizing facility management in the following areas:
Key features
Real-time data acquisition
Facilio gathers real-time data, securely connecting with and streaming performance information from diverse building system controllers.
Facilio uses real-time data to predict operations across your entire portfolio. For instance, if your chiller detects pressure anomalies in its evaporator and raises alarms, you can anticipate an imminent failure and take proactive measures.
Integrates with IP and non-IP systems
- IP-based systems: Facilio’s IoT edge software is designed to integrate smoothly with industry-standard protocols such as BACnet/IP, Modbus, oBIX, and OPC. This ensures compatibility with a wide range of traditional building systems.
- Non-IP-based systems: For systems that aren't IP-based, Facilio utilizes the Niagara framework. It can connect with JACE controllers and other Tridium and IoT-based middleware.
Real-time backup and recovery
Facilio ensures operational continuity even in environments with limited connectivity or unreliable networks. It seamlessly updates system data when connections are restored, maintaining uninterrupted functionality.
Bi-directional communication
Facilio enables effortless interaction with building systems by executing commands such as adjusting set points or directing system actions. This bi-directional communication streamlines operations, enhancing control and responsiveness from the cloud.
Case study: Bellimo implements Facilio’s IoT solution for its HVAC systems
Belimo, headquartered in Switzerland and established in 1975, leads the global market in HVAC field devices such as sensors, control valves, and damper actuators.
Belimo employs 1,900 people globally and is present in over 80 countries. It is listed on the Swiss Exchange (SIX).
The company specializes in IoT-enabled devices that optimize HVAC system efficiency and performance, catering to the evolving demands of modern buildings.
The hurdle:
Bellimo faced challenges in optimizing HVAC system performance and managing energy consumption effectively to improve tenant experiences.
Facilio collaborated with Belimo to help real estate owners, operators, and service providers transform IoT data into operational insights and workflows to optimize building performance and comfort in real time.
The solution:
Facilio integrates Belimo’s advanced IoT devices into its cloud-based O&M solution, offering:
- Sustainability management: Analytics for real-time energy consumption, performance benchmarking, and comprehensive reporting.
- Remote asset performance & optimization: Real-time monitoring and control of HVAC assets through a unified interface, supported by automated ML-driven fault detection & diagnostics.
- Automated maintenance: Customizable workflows for preventive, condition-based, and predictive maintenance.
- Improved tenant & occupant experiences: A user-friendly app enabling remote access, service requests, and visitor management, enhancing operational efficiency and tenant satisfaction.
Read complete case study: Facilio and Belimo join forces to advance IoT-driven connected building environments.
Belimo’s building IoT facility management expert said,
“The real estate industry is engaged in creating sustainable buildings and contributing to ESG goals through digital transformation and industry collaborations. The synergy between Belimo's digital ecosystem and Facilio's O&M platform leverage available data to unlock the potential of connected buildings and address the new challenges.” - Salvatore Cataldi, Global Strategic Building IoT Expert, Belimo.
Benefits of IoT in facility management
One key area where IoT has the potential to help improve facilities management systems (FMS) is in the field of optimization.
There are several ways in which IoT can be used to improve FMS:
Reduction in energy expenditure
By using occupancy sensors and other devices that can relay information through the internet, IoT can detect when energy-consuming equipment is running low on power or when it has stopped functioning altogether. This allows for quick action before energy costs become unmanageable.
Checkout Our Smart Buildings Webinar Series on how Robert dyas achieved 20% energy savings in 3 months
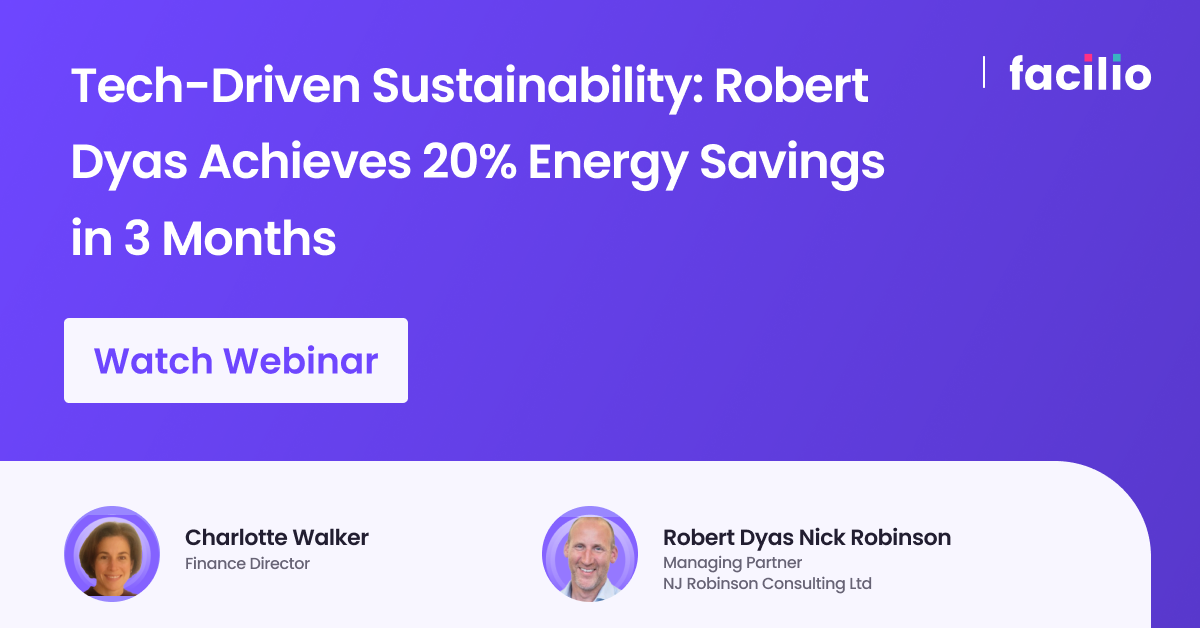
Improved quality of service
With access to real-time data from across a facility, managers can identify trouble spots and make changes to ensure quality field service management at all times.
For example, if sensors placed in different parts of a restaurant show that the microwave oven is not working in one area but functioning normally in another, an alert can be sent to the staff member on duty so that he or she can replace the unit quickly.
Reduction in waste
With remote monitoring systems, managers can identify when equipment has stopped working and order repairs before complete breakdowns.
Further, by tracking how much energy various devices use over time, facility managers can take steps to reduce the amount of waste produced by their organization.
Improved security
For example, suppose sensors detect an unexpected spike in temperature or other signs of a security breach, such as vibration or sound levels that are too high.
In that case, systems can be implemented to ensure unauthorized individuals do not enter the premises and cause harm.
Improved ESG reporting
Facilities managers need precise data from IoT sensors to track key performance metrics like energy consumption, water usage, waste generation, and greenhouse gas emissions (GHG).
This data must be collected, verified, and analyzed from various sources such as utility bills, sensors, surveys, and audits. IoT platforms can integrate these data sources, analyze ESG data, and provide accurate reporting to ensure regulatory compliance.
Increased customer satisfaction
While there are many ways that IoT can improve facility management systems, it is important to note that the best benefits will only be realized when all components of a system are working together.
IoT and facility management software like Facilio enables interoperability to connect people, processes, and systems and deliver high-performance buildings, energy efficiency, and delightful occupant experiences.
Suggested read: How to perform Facilities Condition Assessment?
Step-by-step guide to deploying IoT and AI technology in your facility
Real estate hasn’t traditionally been an early adopter of new technology, but data-driven facility management is no longer optional, with a rising focus on compliance and sustainability regulations.
Here are some tips for facility managers to create IoT ecosystems for their use cases:
Identify critical equipment/processes for automation
IoT and AI together show the maximum ROI for critical equipment that is expensive to replace. Picking such equipment for your pilot program can help you make a strong case for facility management automation with your management.
Set goals for automation and create a framework for the same
Start by clearly visualizing your IoT project goals. What problems are you trying to solve? What benefits do you want from the data that will be collected by these objects? Who is going to use the information, and how?
Run a pilot to iron out the kinks
If you plan to install IoT devices for HVAC monitoring, conduct a pilot program at one or a few locations before installing them across the portfolio.
By running a pilot on critical equipment that’s essential for day-to-day operations, you can show the maximum RoI and make a case for portfolio-wide deployment.
You can hire software developers and expert engineers to create, test, and optimize IoT applications for your use case.
Predict and prevent; don’t wait for breakdowns!
IoT sensors can be installed throughout the facility to monitor and predict problems before they occur.
For example, temperature and humidity devices placed in server rooms or other areas prone to overheating can detect when temperatures rise so that the system can automatically adjust before damage occurs.
Future trends in IoT and facility management
As IoT continues to evolve, its integration into facility management promises to shape the future of building operations profoundly. Here’s a look at the emerging trends and the imperative for ongoing innovation:
- Edge computing for real-time decision-making: Edge computing will empower FM systems to process and analyze data locally, reducing latency and enhancing responsiveness for critical operations.
Continued advancements in edge computing infrastructure and algorithms to support complex data processing requirements in diverse FM environments. - Enhanced sustainability practices: IoT will play a pivotal role in achieving net-zero energy goals by optimizing energy consumption, constantly monitoring environmental impacts, and promoting sustainable practices.
Developing IoT sensors and platforms that provide granular insights into energy use, carbon footprint, and resource efficiency will be essential for sustainable FM practices. - Predictive analytics and AI: Continuous advancements in AI algorithms and machine learning models will be crucial to enhance predictive capabilities and accuracy.
Closing thoughts
IoT technology is everywhere these days, and for good reason. In fact, technology can provide real-time information about various aspects of smart buildings, such as temperature and air quality. This information can then be used to make informed decisions to make spaces comfortable for occupants and save energy and costs for businesses.
Furthermore, IoT facility management technology can also help automate repetitive processes, such as maintenance inspections, which can save time and resources.
If you're looking to improve the efficiency of your facility maintenance operations, you should definitely consider using IoT-powered cloud-based platform like Facilio.