Featured Maintenance Management
Facility Condition Assessment: 6-Step Guide + FCA Checklist
What is a Facility Condition Assessment?
A Facility Condition Assessment (FCA) is a detailed, data-driven evaluation of a building’s physical state.
It involves inspecting key systems—structural, mechanical, electrical, and architectural—to determine current condition, performance risk, and remaining useful life.
FCAs help organizations move from reactive firefighting to proactive asset planning by offering a baseline understanding of infrastructure health and upgrade priorities.
Real-world example: When a university campus needs answers
A university preparing for capital upgrades across its 40-building campus utilizes an FCA to identify which roofs are nearing failure, which HVAC units are exceeding efficiency thresholds, and where ADA compliance gaps exist.
Instead of guessing or reacting, the team gets data-backed priorities, saving both budget and risk exposure.
Why are FCAs important?
FCAs are important because they help you:
- Uncover hidden risks before they become costly emergencies
- Support capital planning with evidence-based priorities
- Optimize repair vs. replace decisions with lifecycle data
- Reduce operational disruptions through proactive maintenance
- Ensure compliance with codes, safety standards, and insurance requirements
- Identify energy efficiency opportunities tied to system performance
What’s included in a Facility Condition Assessment?
An FCA typically covers:
- Structural components: Foundations, roofing, load-bearing elements
- Mechanical systems: HVAC, plumbing, elevators
- Electrical systems: Power distribution, lighting, emergency systems
- Maintenance program review: Gaps in existing practices and backlog risks
- Architectural elements: Interior finishes, façades, windows, doors
- Regulatory compliance: Life safety, ADA, fire codes, local building regulations
- Analysis of building’s energy efficiency: Performance of critical systems, retrofitting opportunities
The result is a comprehensive, holistic snapshot of building health, backed by actionable recommendations, risk scoring, and long-term planning insights.
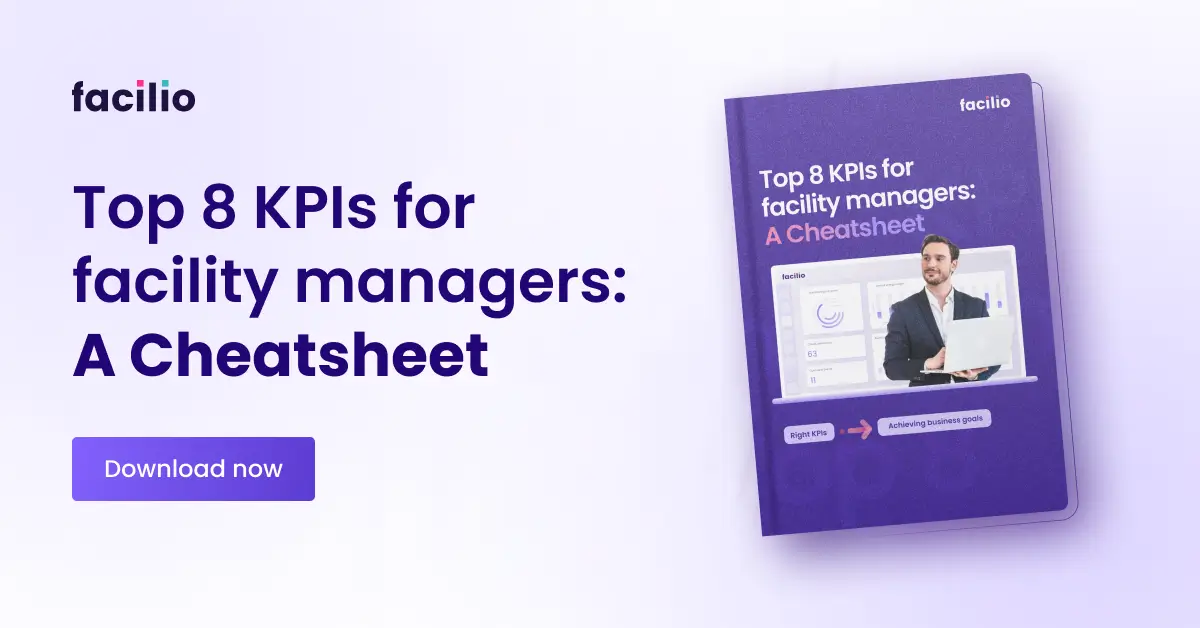
How to conduct a facility condition assessment: A 6-step approach
A well-executed Facility Condition Assessment (FCA) doesn’t just highlight what’s broken—it reveals what’s aging, what’s non-compliant, and where future capital should be directed.
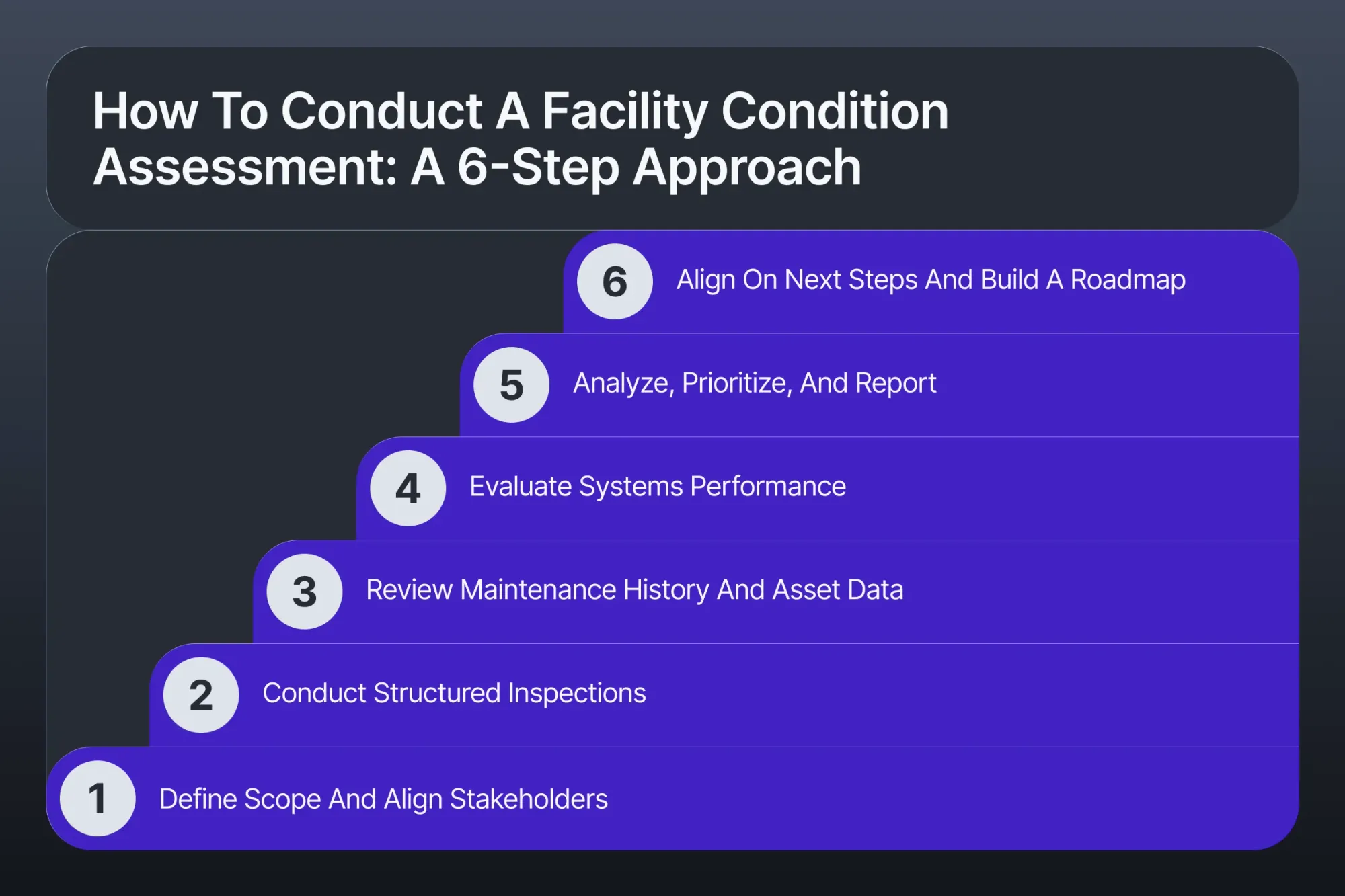
Whether you manage a single site or a multi-building portfolio, here’s a modern 6-step approach to get it right.
1. Define the scope and align stakeholders
Before you inspect anything, define what success looks like.
Set clear goals: Are you preparing for capital planning? Building a 5-year maintenance strategy? Justifying budget requests?
Engage stakeholders early—FM teams, finance heads, sustainability leads—to agree on scope, timelines, and reporting needs.
2. Conduct structured inspections
Go beyond visual walkthroughs. Use standardized templates, mobile inspection tools, and QR-coded asset tags to streamline observations.
Capture not just faults, but their severity, risk level, and recurrence likelihood. Include documents with photos, floor plan notations, or videos when helpful.
🔍 Look for:
- Structural damage (cracks, corrosion)
- Mechanical/electrical anomalies (noise, heat, leaks)
- Safety risks (trip hazards, failed egress points)
- Non-compliant elements (signage, accessibility)
3. Review maintenance history and asset data
An FCA is only as strong as the context behind it. Pull records from your CMMS or FM database to analyze service frequency, costs, and past failures.
Look for patterns—has that air handler failed more than twice in 12 months? Is the generator nearing its warranty end?
🗂️ What to gather:
- Maintenance logs and breakdown history
- Equipment manuals and commissioning docs
- Warranties, inspection reports, and regulatory citations
4. Evaluate the system's performance
Assess major systems beyond their surface condition. This may include:
- Testing HVAC output vs. specs
- Checking electrical load balance
- Monitoring plumbing pressure or leakage
- Verifying fire safety systems and alarms. Where relevant, bring in third-party experts or use sensor-based diagnostics to avoid relying on assumptions.
5. Analyze, prioritize, and report
Once inspections are complete, distill findings into a clear, actionable report. Use a consistent scoring system (e.g., Facility Condition Index or asset condition grades).
Prioritize based on:
- Safety and compliance risk
- Business-critical systems
- Remaining useful life
- Estimated repair vs. replacement cost
Your output should include:
- A prioritized list of deficiencies
- Cost estimates (short-term and long-term)
- Forecasts for deferred maintenance backlog
- Visuals: annotated photos, floor plans, dashboards
6. Align on next steps and build a roadmap
The final and most critical step is turning insights into action. Present findings to senior stakeholders with options: repair now, defer with mitigation, or replace. Use your CMMS or capital planning tools to build a phased project roadmap with clear ownership and timelines.
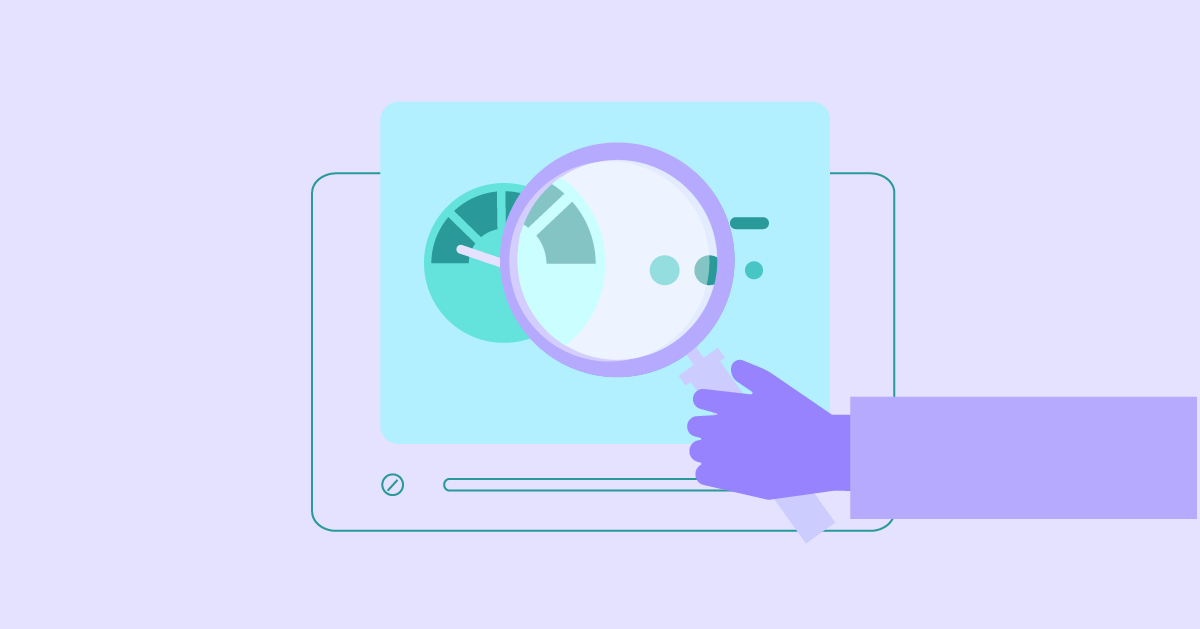
Facility condition assessment checklist: What to track and why
Here’s a strategic checklist to make your assessment both comprehensive and decision-ready:
- Asset inventory – Full catalog of equipment, utilities, and structural elements
- Location mapping – Accurate placement within floor plans or facility management software
- Asset age & warranty – For lifecycle and replacement planning
- Expected useful life – Manufacturer vs. actual performance
- Lifecycle risk markers – Signs of nearing end-of-life or recurring failure
- Condition evaluation – Physical, functional, and compliance health
- Code compliance – Fire, safety, ADA, seismic, energy standards
- Functionality assessment – How well the facility meets user needs
- Remedial actions – Repairs, upgrades, or system overhauls
- Prioritization logic – Based on risk, impact, cost, and urgency
- Cost estimation – Detailed and phased (immediate, 1-year, 5-year)
- Project recommendations – Linked to budget cycles and strategic goals
What should be inspected during a facility condition assessment?
A well-executed FCA looks beyond surface-level damage. It systematically inspects every element that contributes to the safety, performance, and longevity of the facility.
At a minimum, the assessment should include:
- Building envelope: Roofs, façades, windows, and foundations—checking for leaks, cracks, or weather-related wear.
- Interiors: Ceilings, floors, and finishes—assessed for damage, compliance, and usability.
- HVAC, electrical, plumbing: Functionality, safety, and efficiency of all core MEP systems.
- Fire and life safety systems: Extinguishers, alarms, emergency exits, and accessibility elements.
- Structural components: Load-bearing walls, beams, and columns for signs of stress or deterioration.
- External grounds: Parking areas, walkways, landscaping, and drainage infrastructure.
Depending on the building’s type or the assessor’s expertise, the inspection might also include asset-specific systems like elevators, generators, or energy usage evaluations.
The key here is to customize your checklist to reflect real operational risks and future priorities.
Tired of siloed inspections and spreadsheets?
Modernize your facility audits with automated, mobile-first workflows
Start Your Digital FCA JourneyFacility condition assessments across industries
Every building has different wear patterns, compliance needs, and operational priorities, and an FCA adapts accordingly. Here’s how it plays out across key sectors:
- Education: From primary schools to large university campuses, FCAs evaluate classrooms, labs, libraries, and gymnasiums. They assess roofing, HVAC performance, wiring safety, and student-area accessibility to ensure a safe, productive learning environment.
- Healthcare: Hospitals and clinics use FCAs to evaluate patient rooms, surgical suites, diagnostic areas, and life-safety systems. Attention is given to backup power, HVAC systems critical for infection control, and compliance with healthcare-specific codes.
- Commercial real estate: Office towers, malls, and mixed-use properties assess core infrastructure—like elevators, façades, fire protection, and parking facilities—to prioritize capital projects and maintain tenant satisfaction.
- Hospitality: Hotels and resorts assess not just structural integrity but the guest experience. FCAs examine room conditions, plumbing, HVAC, lifts, and leisure areas to ensure both comfort and compliance.
How often should you perform a facility condition assessment?
Most experts recommend conducting a facility condition assessment (FCA) every 3 to 5 years to stay ahead of costly repairs and deterioration. However, the ideal frequency depends on factors like building age, usage, and risk profile:
- Newer facilities (<10 years old) in good condition may only need assessments every 7–10 years.
- Older buildings (50+ years) or those with complex retrofits benefit from more frequent reviews—typically every 3–5 years.
- High-traffic spaces like schools, hospitals, and airports require tighter cycles due to faster asset wear.
- Low-occupancy sites such as storage warehouses may follow a longer interval if infrastructure is stable.
Major changes in use, occupancy, or compliance requirements should also trigger an interim FCA, even if you're between cycles. Routine assessments not only reduce emergency costs, they also inform better asset lifecycle planning and capital forecasting.
What is a Facility Condition Index (FCI), and how is it calculated?
The Facility Condition Index (FCI) is a standardized metric used to quantify the condition of a building or portfolio. It helps facility managers prioritize investments, justify funding, and make data-backed asset decisions.
At its core, FCI measures the ratio of repair needs to replacement value—essentially showing how much of your building’s value is “consumed” by deferred maintenance.
🧮 FCI formula:
FCI (%) = (Total Cost of Repairs / Total Replacement Value) × 100
- Cost of Repairs = All deferred maintenance or required upgrades.
- Replacement Value = What it would cost to rebuild the asset completely today.
📊 Interpreting FCI scores:
📌 Example:
If a building requires $2M in repairs and has a replacement value of $10M:
FCI = (2M / 10M) × 100 = 20%
This indicates a fair condition—repairs are significant but manageable if addressed proactively.
✅ Enables apples-to-apples comparisons across sites or assets
✅ Informs capital planning and budgeting decisions
✅ Tracks deterioration or improvement trends over time
✅ Supports compliance, insurance, and audit reporting
✅ Helps prioritize investments based on real need, not assumptions
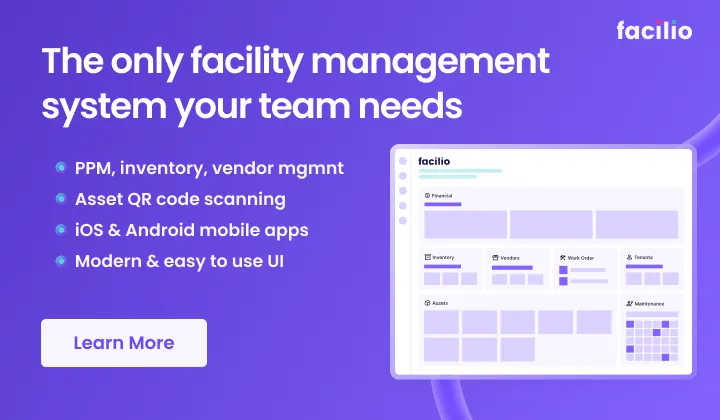
How to create a facilities condition assessment (FCA) report
An effective FCA report doesn’t just list issues; it guides capital planning, prioritization, and stakeholder communication.
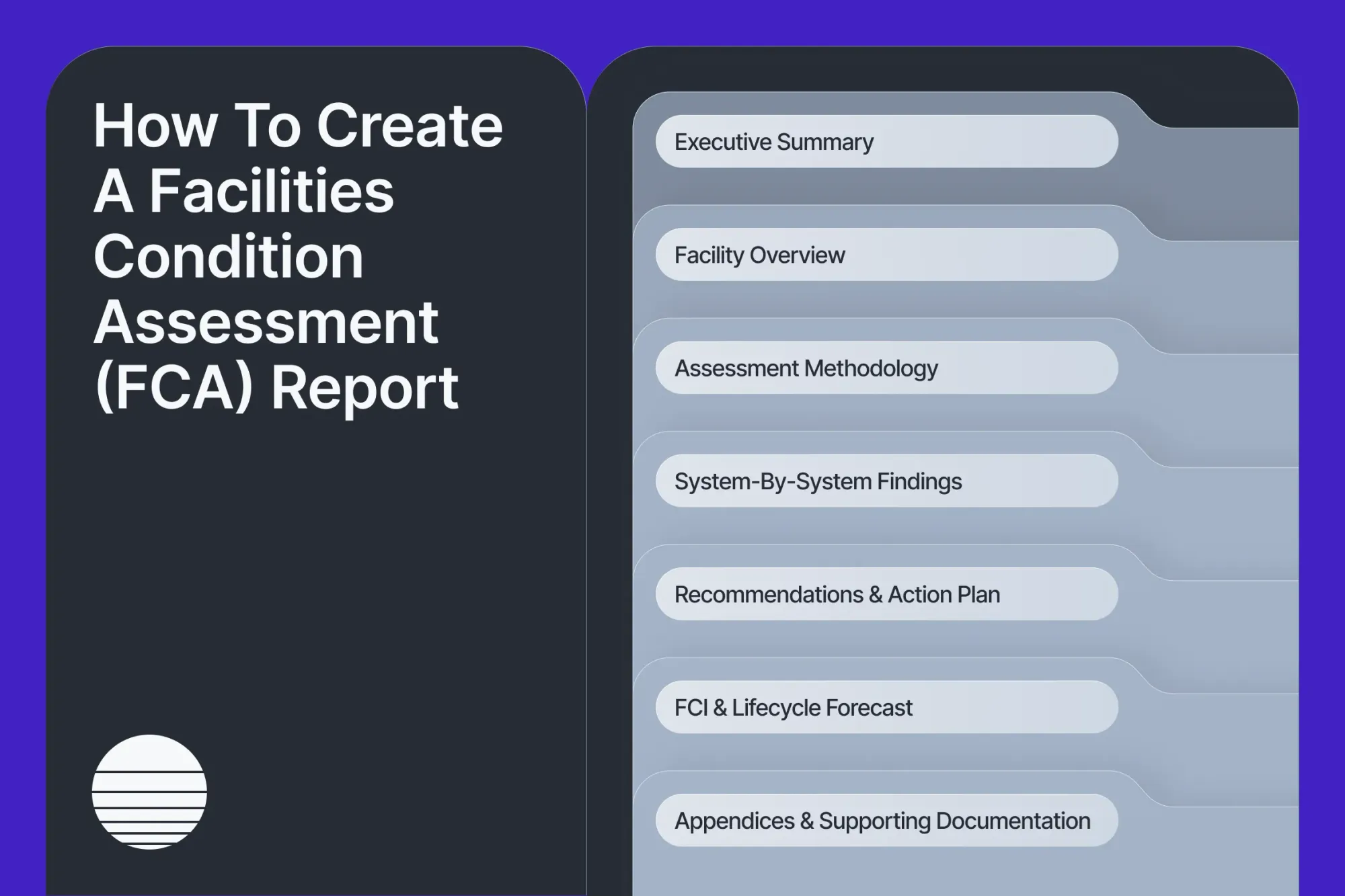
A well-structured report typically includes the following elements:
1. Executive Summary
A concise snapshot of:
- Assessment objectives and scope
- High-level findings and risk highlights
- Urgent priorities and cost implications
This is often tailored for leadership teams and non-technical stakeholders.
2. Facility Overview
Briefly outlines:
- Building age, size, usage, and historical background
- Current operational context (e.g., occupancy, function)
- Any recent renovations or incidents that could influence asset condition
3. Assessment Methodology
Explains how the data was collected, including:
- Visual inspections, system testing, interviews, and document reviews
- Tools used (e.g., drones, thermal imaging, CMMS data)
- Rating systems or scoring models applied (e.g., ASTM, APPA standards)
4. System-by-System Findings
Breaks down the observed condition of:
- Structural elements (roof, façade, foundation)
- MEP systems (HVAC, electrical, plumbing)
- Life safety and accessibility features.
Each system is typically rated (Good, Fair, Poor) with associated photos and notes.
5. Recommendations & Action Plan
For each deficiency or risk area, include:
- Suggested corrective actions (repair, replace, monitor)
- Cost estimates (short-term and life-cycle based)
- Prioritization: critical vs non-critical, grouped by urgency and impact
6. Facility Condition Index (FCI) & Lifecycle Forecast
- Presents the calculated FCI for the benchmark condition
- Includes 5–10 year capital planning forecasts if available
7. Appendices & Supporting Documentation
Such as:
- Inspection photos, floor plans, system manuals
- Cost breakdowns, vendor quotes, or test results
- Risk matrices or scoring rubrics are used during the evaluation
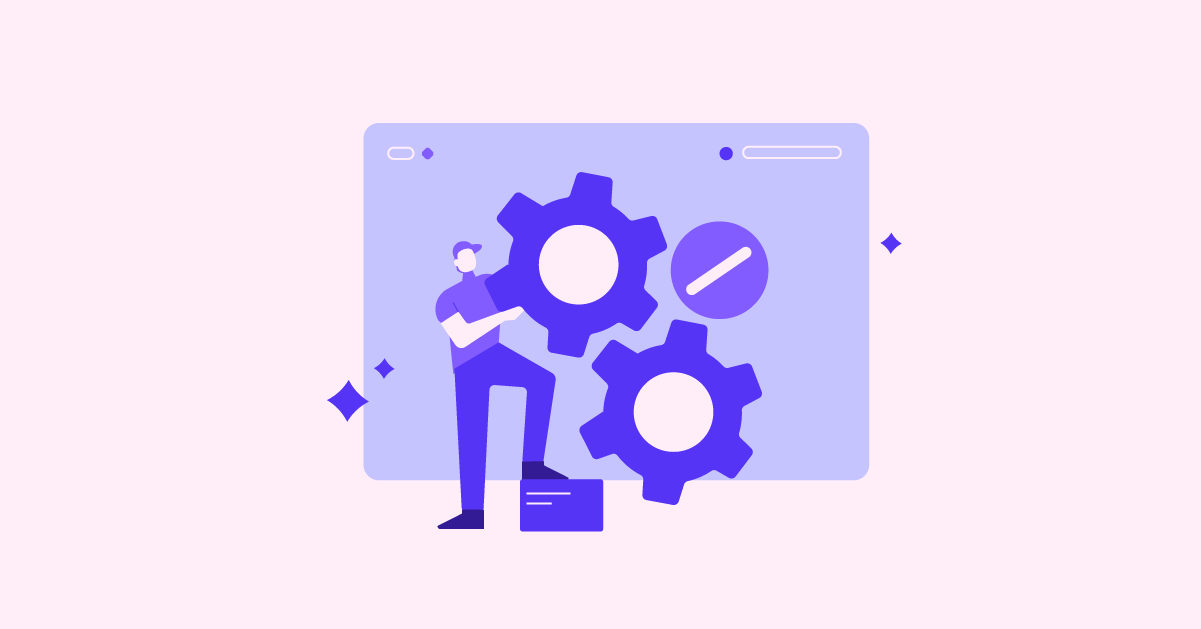
Futureproof your FCA strategy with Facilio’s Connected CMMS
Facility Condition Assessments are no longer static, one-time exercises—they're strategic, ongoing programs that demand real-time data, smart coordination, and portfolio-level visibility.
That’s where a Connected CMMS software like Facilio makes the difference.
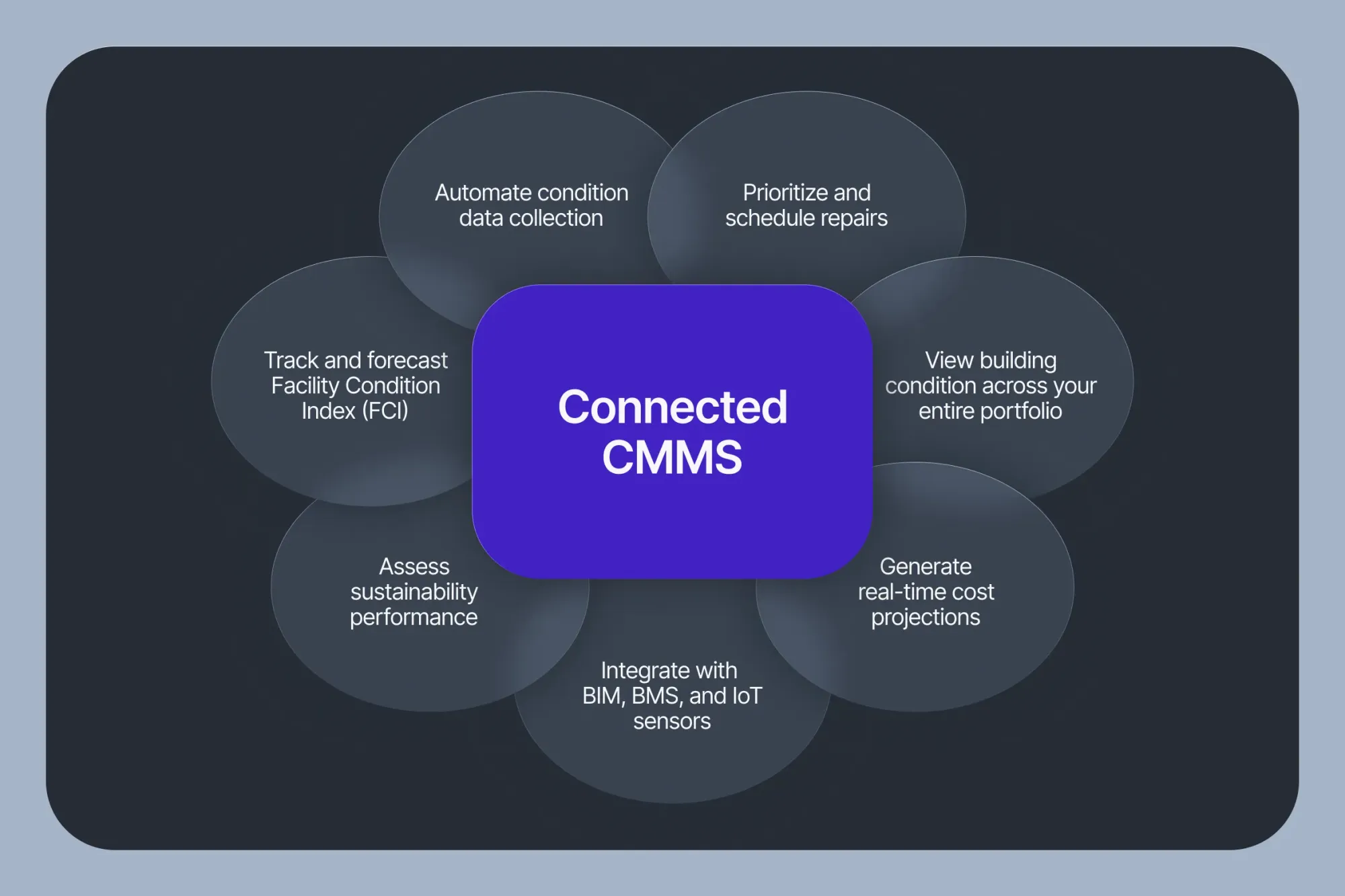
By unifying asset performance, work orders, inspections, and capital planning in one platform, Facilio transforms how you approach and act on FCAs:
- ✅ Automate condition data collection through scheduled inspections and mobile task execution
- 📊 Track and forecast Facility Condition Index (FCI) using live asset health and lifecycle data
- 🔗 Integrate with BIM, BMS, and IoT sensors to capture granular system-level insights
- 📅 Prioritize and schedule repairs based on urgency, compliance risk, and budget availability
- 💸 Generate real-time cost projections for capital planning and deferred maintenance
- 🏢 View building condition across your entire portfolio—from a single command center
- ♻️ Assess sustainability performance alongside physical condition and energy efficiency
Whether you’re preparing for an FCA cycle, a capital budgeting season, or audit readiness, Facilio helps you move from manual guesswork to predictive intelligence.
Ready to modernize your condition assessments and unlock data-backed FM? Explore how Facilio’s Connected CMMS helps you build future-ready facilities from the ground up.
From inspection to execution—all in one place
Plan, track, and optimize maintenance with a centralized Connected CMMS software
Book a Custom DemoFrequently asked questions about FCA
Who typically conducts facility condition assessments?
Facility condition assessments are typically conducted by trained professionals such as engineers, architects, or facility managers.
How long does a facility condition assessment take?
The duration of a facility condition assessment can vary depending on the size and complexity of the facility, but it generally takes several weeks or months to complete.
How often should facility condition assessments be conducted?
Facility condition assessments should be conducted periodically, with intervals typically ranging from at least once every five-10 years, depending on factors such as the age and usage of the facility.
Can a facility condition assessment help with budget planning?
Yes, facility condition assessments can assist with budget planning by providing valuable insights into current maintenance needs, future capital expenditures, and long-term facility management strategies.