Visual Inspection: Types, Techniques, and the Exact Process
What is visual inspection?
Visual inspection is a key technique used in many industries to check the quality and integrity of products, components, and systems.
Traditionally, it’s about directly observing an object or process to spot defects or anything that doesn’t meet the required standards. But with recent technological advancements, visual inspection has evolved so much—incorporating tools like artificial intelligence (AI) and remote imaging to improve both accuracy and efficiency.
Types of visual inspection - Traditional vs automated/remote visual inspection
Visual inspection once relied on the human eye and simple tools to spot defects. Today, AI, machine learning, and high-resolution imaging have made inspections more precise and far more consistent, while remote tools like drones and robotic cameras allow safer, more thorough checks in hard-to-reach areas.
Let’s understand what each of these means with a comparison table.
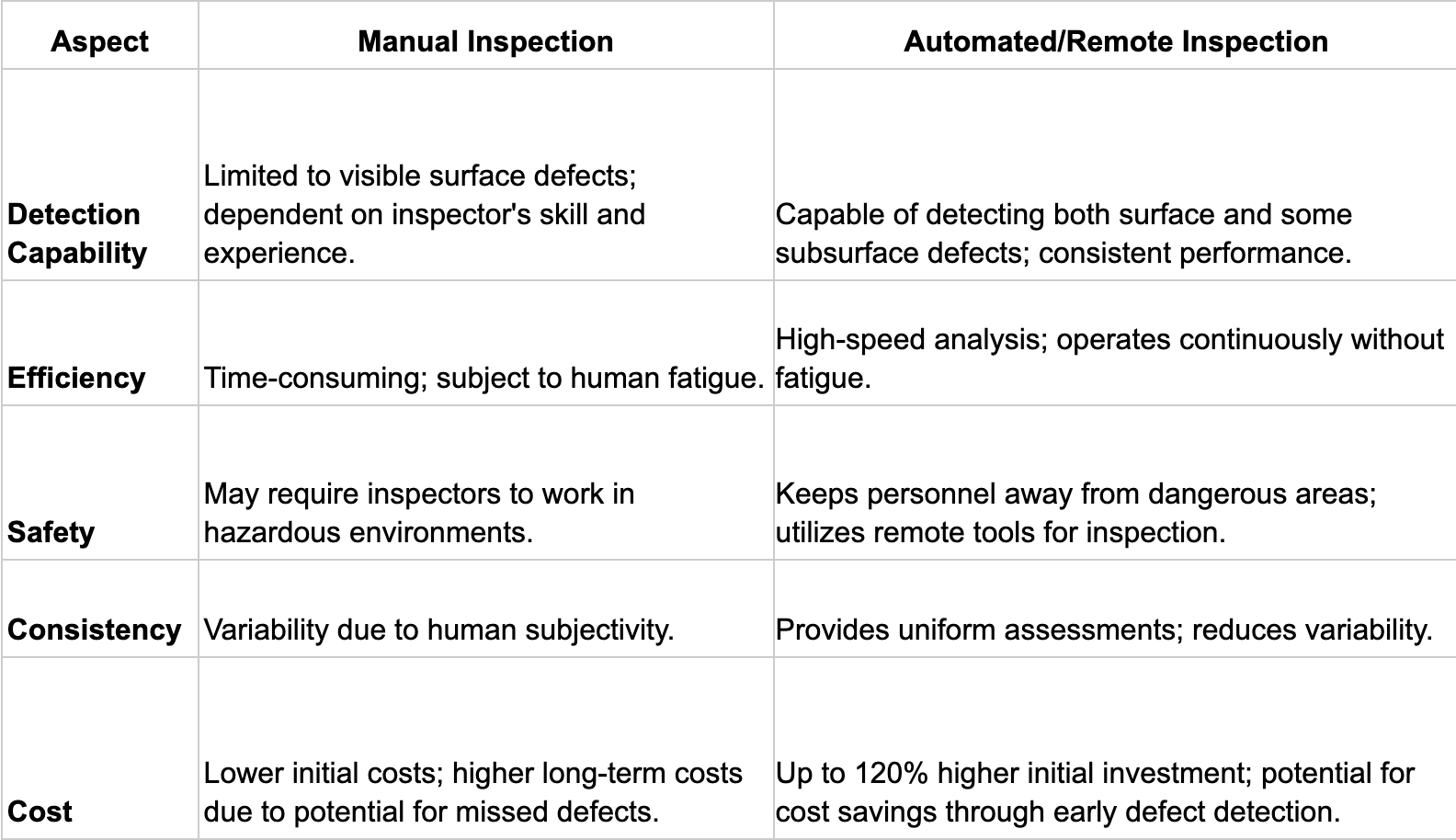
Why is visual inspection so important?
Visual inspection is crucial in maintaining the quality, safety, and efficiency of products and systems across industries. It forms the very foundation of effective quality control and maintenance practices by consistently identifying defects and inconsistencies.
Here’s why it is important and where it makes a difference.
Key benefits of visual inspection
- Enhanced quality assurance: Detecting defects early in the production process helps maintain high-quality standards and prevents defective products from reaching the market.
- Improved safety: Regular inspections uncover potential hazards, enabling quick action to prevent accidents and promote a safer workplace.
- Regulatory compliance: Ongoing visual inspections ensure compliance with industry standards and regulations, reducing the risk of costly penalties.
- Cost savings: Identifying defects early on minimizes the need for expensive repairs and cuts down on waste, leading to significant savings.
Key techniques in visual inspection
Visual inspection is so critical for quality control and it ensures that products and systems meet set standards. Several technological advancements over the years have introduced several techniques that improve the accuracy and efficiency of visual inspections. These include
- Surface Inspection - It focuses on identifying visible defects like scratches, dents, cracks, or discoloration. Traditionally done manually, it has now been enhanced by automated systems using high-resolution cameras and image-processing algorithms to spot even the smallest imperfections. Example: In the automotive industry, surface inspection systems detect paint defects to ensure vehicles meet both aesthetic and quality standards.
- Dimension Inspection - This involves checking the size, shape, and alignment of products to ensure they meet design specifications. Automated systems using laser scanners and optical tools improve accuracy, reducing human error and boosting production speed. Example: In semiconductor manufacturing, dimension inspection ensures microchips fit perfectly into electronic devices.
- Statistical Process Control (SPC) SPC uses statistical methods to monitor and control processes, helping manufacturers detect variations and make adjustments to maintain product quality. Integrating SPC with visual inspection provides real-time monitoring and the ability to act quickly. Example: In textile manufacturing, SPC monitors fabric quality to ensure consistency in texture and color across production runs.
- Computer Vision Computer vision leverages AI to analyze visual data, allowing machines to detect patterns and anomalies that may be difficult for human inspectors to spot. Example: In the food industry, computer vision systems are used to check the ripeness and quality of fruits and vegetables, automating the inspection process.
- Predictive Analytics Predictive analytics uses historical data and machine learning to forecast potential defects or failures, enabling proactive maintenance and quality checks. Example: In aerospace manufacturing, predictive analytics helps anticipate wear and tear on components, allowing for timely maintenance before issues arise.
What are the common challenges in visual inspection?
Visual inspection is a key part of quality assurance across industries, but it’s not without its challenges:
- Human error: Manual inspections can suffer from inconsistencies caused by fatigue, subjective judgment, and simple oversight.
- Limited to surface-level issues: Traditional methods often miss internal or subsurface defects, focusing only on visible problems.
- High costs of automation: For small and medium businesses, upgrading to automated systems can feel like a financial stretch.
Understanding these issues and addressing them with smart solutions can significantly improve accuracy and efficiency. (Source: U.S. Department of Energy Office of Scientific and Technical Information)
Solutions to overcome challenges in visual inspection
- Better training programs:
- Offer detailed training to sharpen inspectors’ skills and minimize mistakes.
- Keep training materials fresh by including the latest techniques and standards.
- Advanced tools:
- Use tools like drones and borescopes to reach tricky areas and catch hidden defects.
- Leverage AI and machine learning to spot issues that might escape human eyes.
- Affordable automation:
- Opt for scalable, budget-friendly automation tailored for smaller businesses.
- Roll out automation in phases to spread out costs and give teams time to adapt.
- Integrate with a Connected CMMS software:
- Implement CMMS to standardize processes and make documentation a breeze.
When it comes to improving visual inspection processes, a powerful Computerized Maintenance Management System (CMMS) is a nothing but a game-changer. A Connected CMMS stands out because it centralizes all maintenance data, standardizes workflows, and provides real-time insights, which significantly reduce human error and ensure consistency. You will learn more about this in the next section.
The exact step-by-step process for visual inspection
Implementing a structured visual inspection process is essential for maintaining quality and safety standards across various industries. Below is a step-by-step guide to conducting effective visual inspections:
1. Preparation
- Define inspection criteria: Clearly outline what constitutes a defect or non-compliance.
- Gather necessary tools: Ensure all required inspection tools and personal protective equipment (PPE) are available and in good condition.
- Review documentation: Familiarize yourself with relevant manuals, standards, and previous inspection reports.
2. Inspection
- Initial observation: Conduct a general overview to identify any obvious issues.
- Detailed examination: Inspect specific components or areas systematically, following a predetermined sequence.
- Use of aids: Employ magnifying glasses, mirrors, or other tools to enhance visibility in hard-to-reach areas.
3. Documentation
- Record findings: Note all observations, both compliant and non-compliant, with detailed descriptions.
- Capture visual evidence: Take photographs or videos of identified issues for reference.
- Utilize checklists: Use standardized checklists to ensure consistency and completeness.
4. Reporting
- Compile report: Summarize findings in a clear and concise report, highlighting critical issues.
- Recommend actions: Suggest corrective measures for identified problems.
- Distribute to stakeholders: Share the report with relevant personnel for review and action.
How does a Connected CMMS standardize visual inspections?
Integrating a Connected Computerized Maintenance Management System (CMMS) like Facilio’s into your visual inspection process takes efficiency and accuracy to the next level.
During preparation, Facilio’s CMMS lets you create and store detailed checklists and flowcharts, so inspectors have everything they need right at their fingertips.
When it comes to inspections, the mobile-friendly platform (with offline access support) allows real-time data entry—even in low-network areas—making it easy to document findings on the go.
For documentation, it centralizes all inspection data, from photos to notes, creating a comprehensive digital record that’s simple to access later.
Finally, when it’s time to report, the system automates analytics, helping spot recurring issues and shape smarter maintenance strategies. With Facilio’s Connected CMMS, you can streamline inspections, cut down errors, and ensure top-notch quality every time.
Get started now.
Learn more about an adaptable and self-serve maintenance management approach