Outdated CMMS tools are dragging retail ops. Discover how connected maintenance platforms are solving real multi-site FM challenges.
It is a collection of strategically planned maintenance activities (reactive, preventive, planned, predictive, condition-based) aimed at maintaining the infrastructure's safety and functionality.
This applies to tasks such as general cleaning, HVAC maintenance, parking lot upkeep, fire-fighting systems maintenance, water treatment, CCTV installations, waste management, and electrical systems maintenance.
Retail chains, both in the food and non-food sectors, are plagued by inefficiencies and broken systems, leading to significant operational challenges.
According to a recent industry survey, “65% of retail managers report that outdated maintenance systems hinder productivity.” This inefficiency results in higher costs, downtime, and reduced customer satisfaction.
The crux of the problem lies in the reliance on legacy Computerized Maintenance Management Systems (CMMS), which, as experts state, “are not designed to handle the dynamic and multifaceted needs of modern retail environments.”
Consequently, retail chains miss out on critical insights into maintenance, asset performance, facility productivity, and energy optimization—all of which contribute to safe, productive, and comfortable facilities.
In this article, we dig deep into the real impact of broken tech foundations on maintenance operations for the retail sector and the far-reaching (and immediately damaging) consequences of a passive stance in this fast-evolving space.
Addressing the most common challenges with retail maintenance management
Your customer-facing, front-end tech promises unified, personalized experiences across the online & brick-and-mortar channels tailored to every customer.
Meanwhile,
- The acute shortage of skilled technicians available (or, most times, not) in the US and the high number of reactive, on-demand maintenance requests and breakdowns have your teams buried in spreadsheets and calls all day.
- Striking a balance between in-store environments and cost-effective energy usage is definitely easier said than done.
- Energy needs only increase with a focus on better customer experience, but with soaring energy costs and compliance regulations on your back, how do you find middle ground?
How does this affect the team?
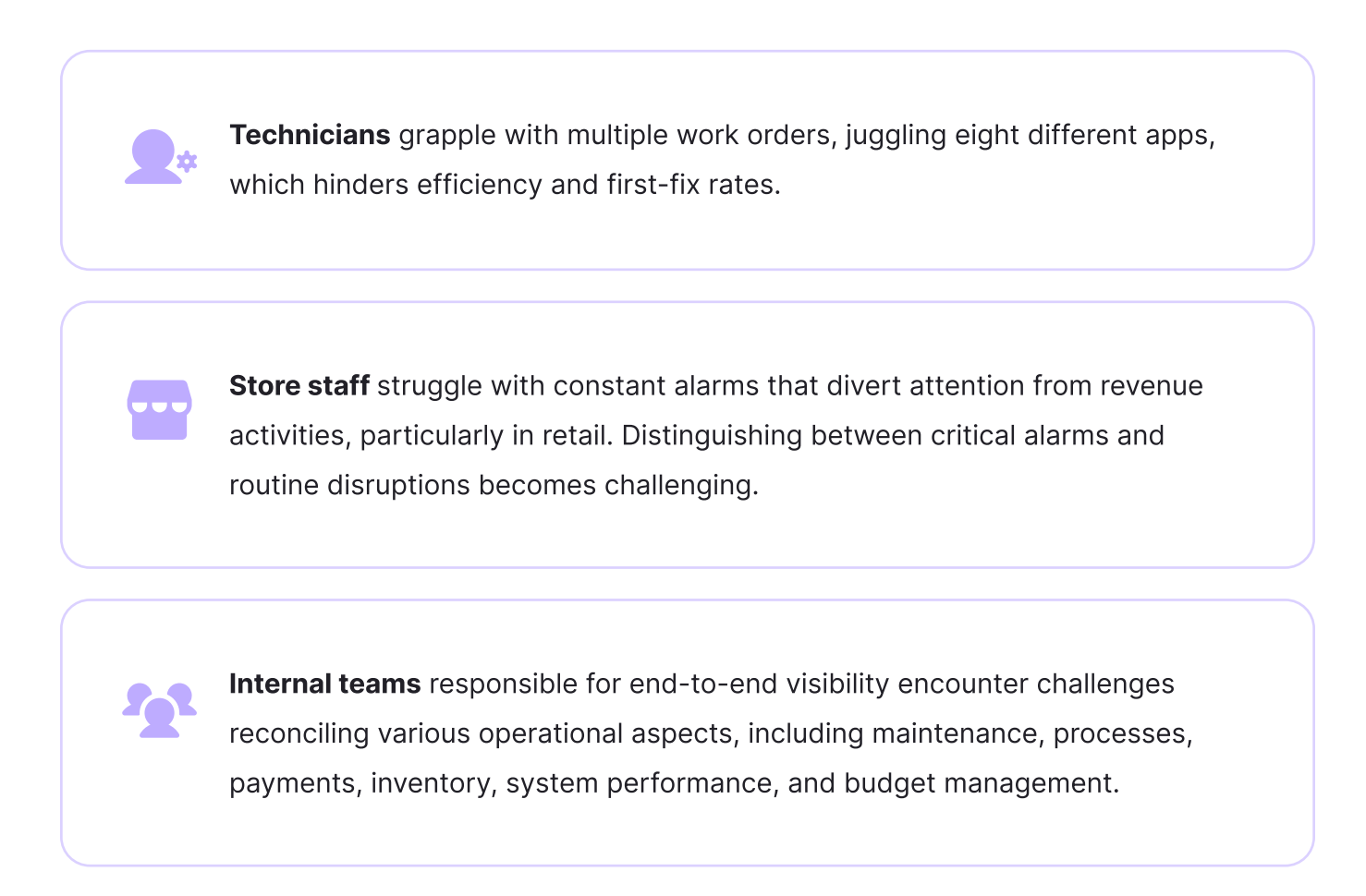
How does it affect your growth?
You know it better than anybody:
- Equipment breakdowns and facility issues destroy customer relationships and eat into your profits. A high reactive maintenance ratio when compared to PPM is never good.
- Inconsistent shopping experiences when your front-end tech promised the world? That's a one-way ticket to losing loyal customers.
- Accurate and timely maintenance reports are vital for demonstrating compliance, and staying in the good books of regulators.
What's really at the centre of all these issues?
Legacy tech, patchwork solutions, and manual processes.
They're holding you back.
The current state of Retail maintenance management
Shoppers now enjoy effortless transitions between digital and physical realms, resulting in streamlined and captivating shopping experiences. This tech revolution has set new standards for customer satisfaction and retail excellence.
However, while the front end dazzles with innovation, back-end operational and maintenance technologies lag, remaining fragmented and decentralized.
This disparity affects operational efficiency and sustainability efforts. Bridging this gap is essential for thriving in the evolving retail landscape.
Let's compare the state of front-end versus back-end technologies in retail:
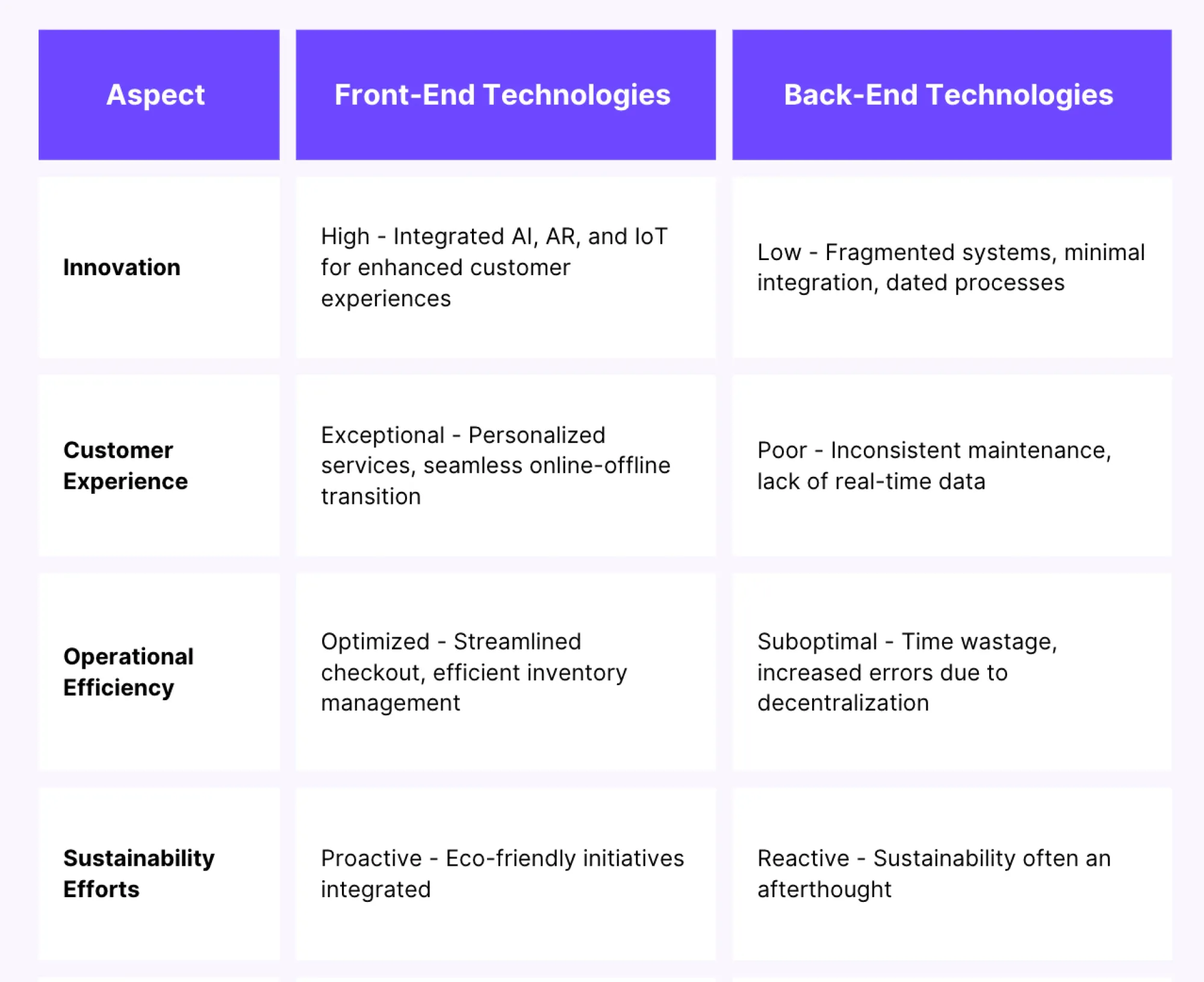
The problem and the challenge are clear: It's time to rethink your backend FM software and how it enables every stakeholder to be productive, informed, and proactive.
Big ways legacy CMMS software hinders Retail operational reliability
Overseeing FM for multi-site retail facilities, like any other challenge worth taking, is easier said than done.
Legacy CMMS hasn't evolved with customer expectations in the retail vertical. Unfortunately, for you, not evolving is not really a choice; it's a matter of survival.
In a competitive market like this, you evolve or perish—there is no in-between.
The list of things your CMMS could be doing for you is a long one, but these may be your biggest operational blindspots:
Poor interoperability across O&M software that creates silos at every level
Legacy CMMS solutions were built as systems of record for asset, maintenance, and work orders.
- Fragmented operations: Facilities managers are forced to use separate systems or manual processes for different tasks, clients, and locations, which for obvious reasons, impairs coordination.
- Inconsistent, incomplete, erroneous data: With siloed systems, it becomes difficult to track consistent data on asset performance, work orders, and maintenance schedules across sites.
- Business impact: Delays in service delivery, inconsistent maintenance quality, and increased operational costs are just the first few on a long list of consequences of non-optimized processes at scale.
No portfolio-level oversight to identify inefficiencies and opportunities
Modern retail facilities demand real-time data on asset performance and maintenance needs to make informed decisions quickly. Unfortunately, legacy CMMS tools lack advanced analytics and reporting features.
A lack of actionable insights results in more frequent equipment failures, reduced asset lifespan, and higher repair costs.
- Track KPIs across locations: Without consolidated real-time dashboards, it’s challenging to monitor metrics like maintenance response times, first-time fix rates, repair costs, or asset performance across all sites.
- Predict failures: Legacy systems don’t offer predictive maintenance tools that can foresee equipment failures, leading to reactive rather than proactive maintenance.
- Poor vendor relationships: When you have to depend on vendors for their own performance reports, its hard to identify and nuture better relationships with your best, most reliable vendors.
Inefficient work order management, missed SLAs, and unhappy clients
Legacy CMMS solutions usually come with clunky user interfaces and outdated features that dampen work order management efficiency in multi-site retail environments.
- Slow response times: Work orders may take longer to be created, assigned, or completed, resulting in delayed repairs.
- Manual processes: Many older systems require manual input or paper-based processes, which increase administrative burden and introduce room for errors.
- Business impact: Unresolved or delayed maintenance can lead to equipment downtime, store disruptions, and a poor customer experience. For food retailers, this could result in health risks, non-compliance with regulations, or even product spoilage.
Poor mobile accessibility for an already strained field staff
With teams spread across multiple sites, modern maintenance technicians rely on mobile tools to update work orders, check asset history, and report issues in real time. However, legacy CMMS systems often lack robust mobile functionality.
- Inflexible communication: Technicians are tied to desktop systems or paper forms, leading to delays in reporting and updating tasks.
- Poor coordination: Without mobile access, the coordination between field teams and office staff is hindered, slowing down response times.
- Business impact: These inefficiencies lead to longer downtimes, lower technician productivity, and higher labor costs. For food retailers, poor mobile access can be particularly costly in critical areas like refrigeration equipment monitoring.
Compliance takes a backseat with manual audits and logs
For food retailers, compliance with safety, sanitation, and refrigeration regulations is non-negotiable. However, legacy CMMS tools often lack the features needed to easily manage and document compliance activities across multiple sites.
- Automated audits and inspections: Legacy systems cannot automate compliance checks or generate reports needed for audits.
- Tracking sanitation and temperature: Without integrations for IoT sensors or digital logs, maintaining compliance for refrigeration units, food safety protocols, and OSHA regulations becomes cumbersome.
- Business impact: Failure to stay compliant can result in fines, store closures, or reputational damage. For food operations, this is a critical risk that legacy systems cannot mitigate effectively.
There are many more reasons why legacy CMMS aren't up to the challenge today's retail environments bring.
Experts in Retail Operations Technology, Jim Owens, the President of EcoTrax, and Basant Singhatwadia, who heads customer innovation and strategy in Facilio Inc's Retail division, discussed the current challenges in multi-site facilities management, and outlook for the future + a playbook for O&M transformation.
You can get a free copy here -
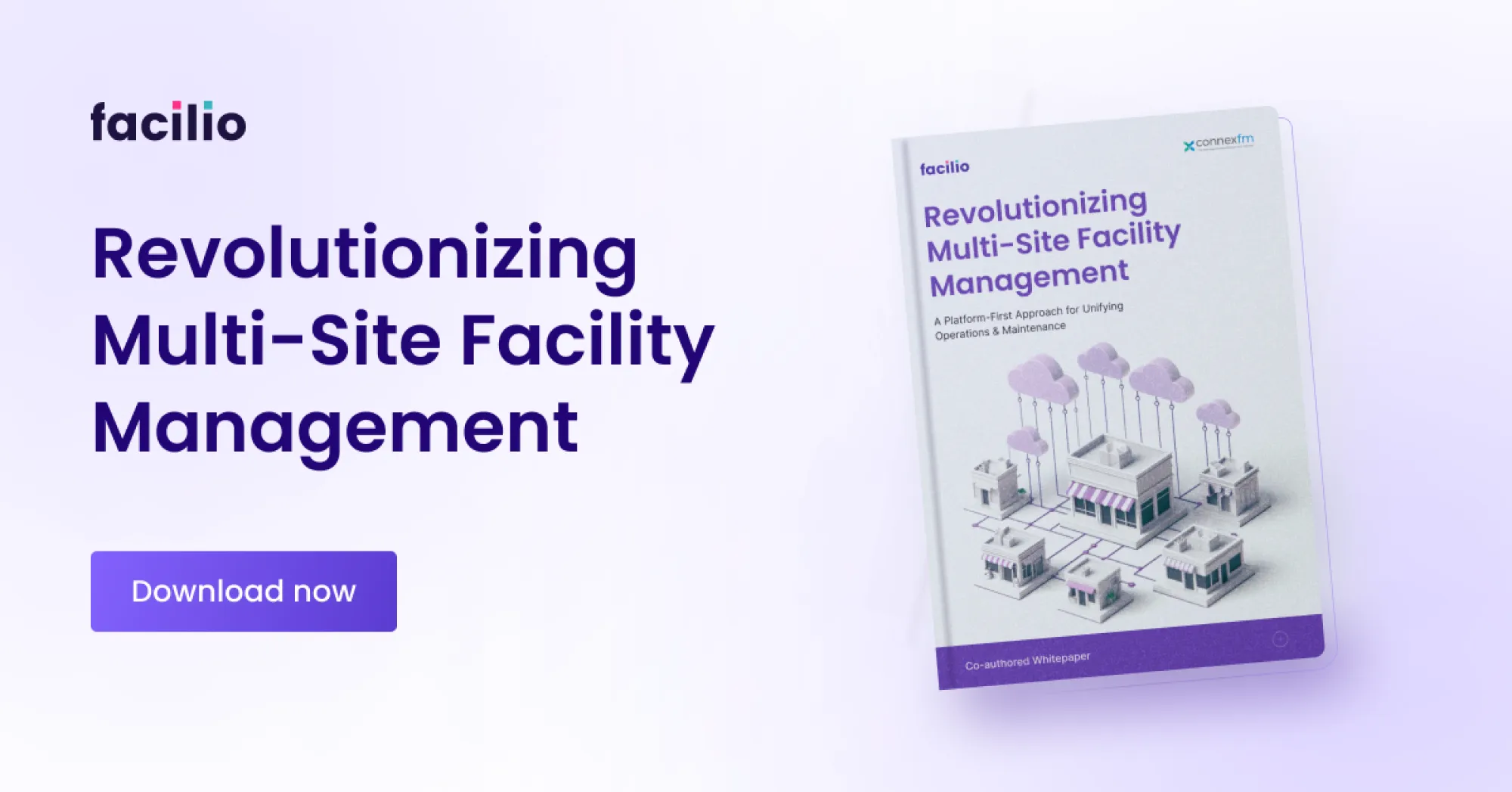
The mindset shift that transformed retail operations for Tutenlabs
In a retail environment, every minute counts, and efficiency can make or break a season's profits.
When it comes to a retail chain with outlets spread across multiple locations, each has its unique set of challenges, from maintenance issues to energy management.
Tuten Labs, a technology leader helping retail stores in the US fought an uphill battle with fragmented data, inconsistent maintenance schedules, and long downtimes. The pressure of increased costs and customer dissatisfaction only escalated.
The learning?
Disconnected systems and software–a large assortment of tech that doesn't work together and creates more work than it helps with.
They needed to address the problem of fragmentation to sort through the noise of alarms and enable their people to rise above human-centric processes that software should be able to handle.
They needed a platform that brings together all things O&M across client portfolios to return time back to the team, and enable them to do things that matter, not manage alarm noise and fire-fight breakdowns.
Facilio's connected CMMS was their solution of choice. With Facilio, they unified all maintenance operations under a single pane of glass; special thanks to real-time monitoring and automated scheduling, which brought the most transformative change.
- Managers no longer needed to rely on manual checks or reactive maintenance. Instead, the system continuously monitored equipment health, predicting failures before they occurred and scheduling preventive maintenance automatically. This not only reduced downtime but also extended the lifespan of crucial assets.
- For the staff, the CMMS streamlined issue reporting.
Whether it's a leaky HVAC system or a malfunctioning refrigerator unit, employees could report issues through a centralized system, which would then notify the nearest technician in real-time. This quick response mechanism improved repair times significantly, and ensured minimal disruption to store operations. - Energy management is supercharged with real-time monitoring.
The CMMS provided actionable insights into energy consumption patterns, allowing the chain to implement energy-saving measures which would bring most impact to their specific use case.
Smart sensors, integrated with the CMMS, adjusted lighting and HVAC systems based on occupancy and demand. This resulted in substantial cost savings and a reduced carbon footprint. - This connected approach benefited more than just the front-line employees and the maintenance crew. Management gained access to comprehensive analytics and reporting tools. They could now make data-driven decisions, plan maintenance budgets more accurately, and track key performance indicators with ease.
In a nutshell, the implementation of Facilio's connected CMMS revolutionized Tuten Labs' operations with end-to-end visibility, powerful automation, and actionable insights–all delivered with simple, intuitive, tailored O&M apps.
Jonathan Wolter, the Director of Sales, North America Tutenlabs, sat down with Basant Singhatwadia to discuss a real-life case study about how they leveraged remote monitoring and a platform-based approach to unify operations and maintenance across 10000+ stores for a top C-store chain.
Catch the insider details here -
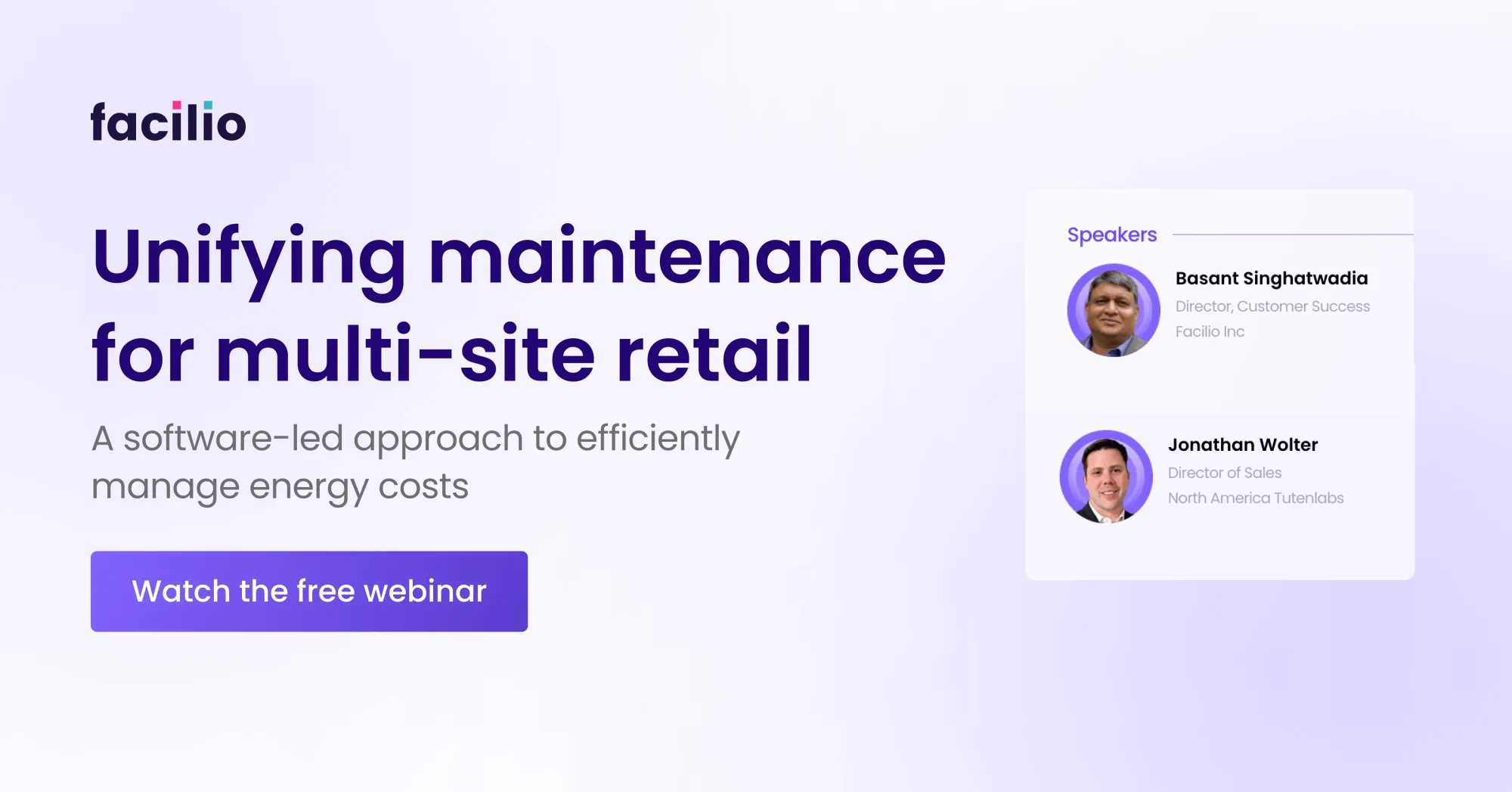
Wrapping up–Closing the loop
Maintenance isn't just about keeping things running; it's the backbone of a smooth customer experience and healthy bottom line. Outdated analog systems simply can't keep up with today's challenges.
A centralized platform needs to become a staple to achieve operational reliability across client portfolios. Here's what it offers to close the loop from monitoring to work orders for truly seamless retail operations:
- End-to-end maintenance management
- Real-time operational visibility
- Energy management & optimization
- Intelligent remote monitoring & alarm triaging
- Compliance, leak detection & refrigeration management
- Field service management
Here's what the CEO of Tutenlabs, Roi Amszynowski had to say about Facilio's impact on their business:
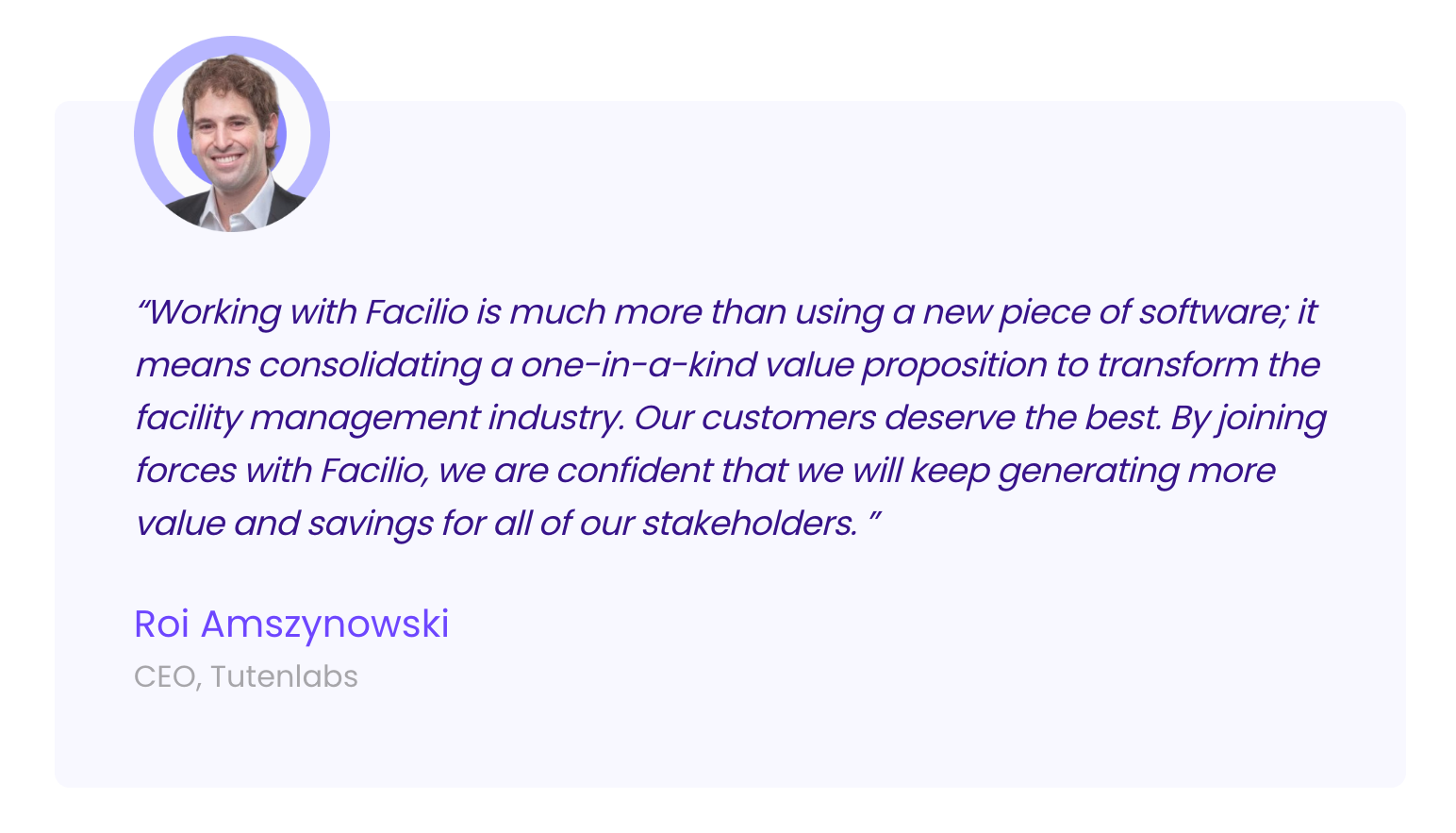
Interested in Facilio?
Explore Facilio's Connected Retail solution for yourself, or book some time to see a personalized demo.