Where Do You Stack Up in the Maintenance Maturity Model?
It's a sweltering morning with soaring temperatures. Employees enter the office only to be met with a failed central air-conditioning system.
The problem?
A worn-out compressor that should have been replaced months ago during routine maintenance. Early warning signs were overlooked, such as unusual noises, increased energy consumption, and reduced cooling.
Now, last-minute fixes come at triple the planned cost, disrupting operations and highlighting the inefficiencies of a reactive, crisis-driven approach. This approach might work for some equipment, but it can lead to extended and costly downtime when applied to mission-critical assets like compressors, motors, and pumps.
This scenario underscores a common challenge in facility management: the consequences of neglecting proactive maintenance.
As equipment ages, it requires increasingly sophisticated maintenance. Facility managers understand these lifecycle stages and adapt their maintenance strategies accordingly.
So, how can facility management leaders assess their maintenance practices and identify areas for improvement?
Let's explore what a Maintenance Maturity Model is and how it can transform your approach to facility management.
5 Levels of maintenance maturity: reactive to proactive approaches
Maintenance maturity reflects the effectiveness and robustness of your maintenance management practices. These practices evolve from basic, reactive approaches to advanced, prescriptive methods.
Understanding the maturity level of your maintenance practices helps you:
- Make informed maintenance decisions swiftly
- Reduce costs and time overhead
- Avoid unexpected breakdowns
- Strengthen client relationships
- Keep stakeholders engaged and informed
- Drive sustained growth through operational excellence
- Establish high levels of adherence to delivery schedules
An organization's specific maintenance level depends on factors like its size, the tools it uses, and its industry. However, when it comes to maturity, the transition is not immediate but incremental.
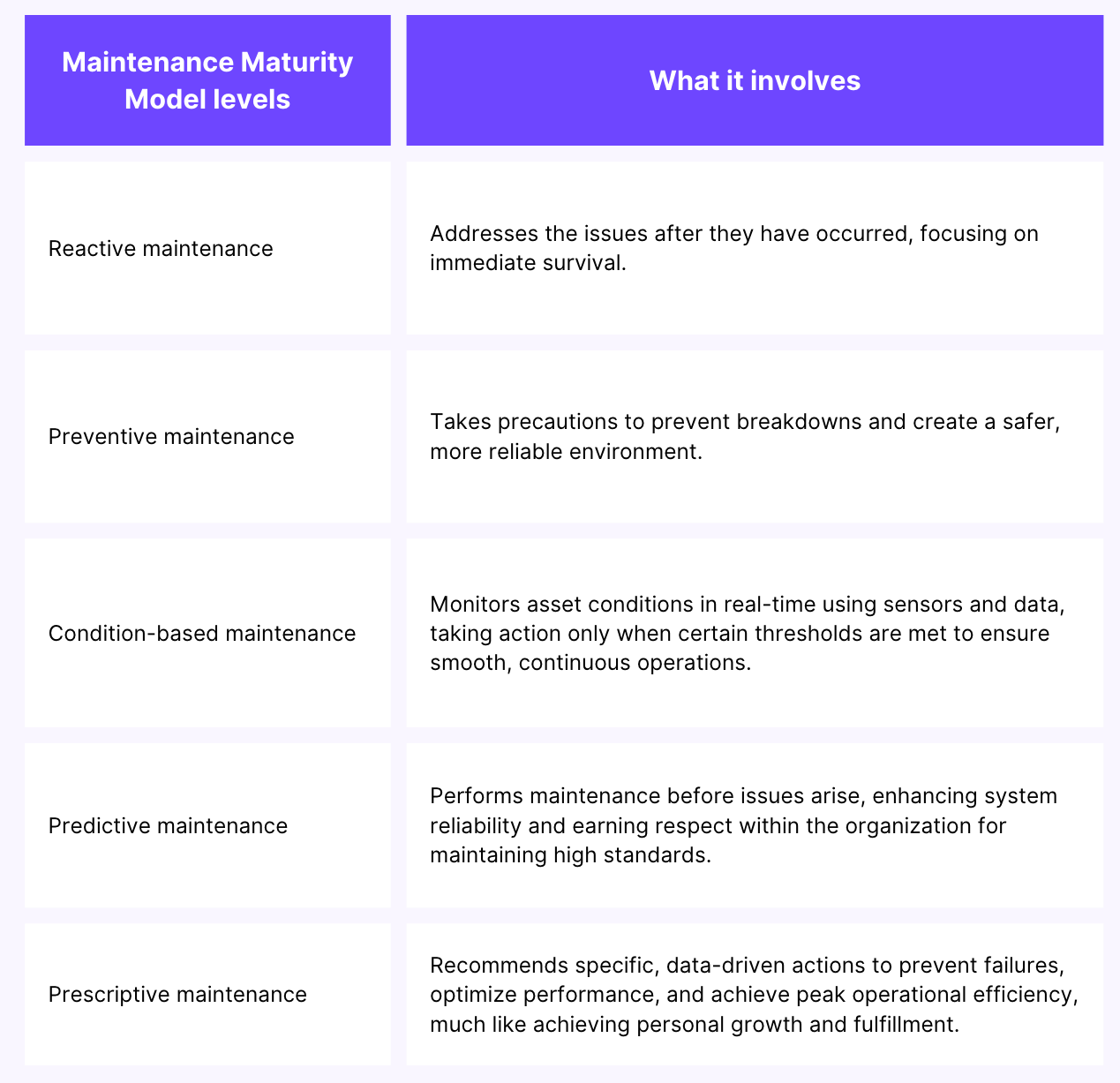
Level 1: Reactive maintenance
When you’re just starting or operating with a small team, it doesn’t hurt to take the “run to failure” approach.
However, responding to issues as they rise—i.e., taking on the reactive maintenance stance—is neither sustainable nor conducive to operational goals.
The worst part of choosing this road must be that whenever there are equipment failures or breakdowns out of the blue, they occur at the most inconvenient time. Here are some pitfalls of solely relying on a reactive maintenance approach:
- Costly recovery: Emergency repairs for critical equipment mean shutting it down completely. Along with the cost of stopping the work altogether, the rush cost of technicians can also add up.
- Difficulty in budgeting: Sudden equipment breakdowns can make maintenance cost analysis difficult, as there’s no clear indication of when and how the breakdown will happen and how long it will take to resolve.
- Unsafe operating conditions: When assets go unchecked, they might deteriorate over time, making workers operate under unsafe conditions. This may lead to repercussions like employee dissatisfaction.
- Unplanned downtime: Last-minute repairs cause significantly higher downtime, as some equipment might be beyond repair because you left all warning signs unnoticed, just like Penny ignored the “Check Engine” warning in the Big Bang Theory series, costing her a small fortune to get her car up and running again.
High unplanned downtime increases businesses' costs tremendously. Among Fortune Global 500 companies, the annual cost of downtime in 2021-2022 is now $129 million per facility, up 65% from Siemens’ last survey in 2019-20.
Such staggering costs and slow operational capacity can also impact your reputation. For instance, if you always react once the incident has happened, you may appear to be “putting out fires” rather than proactively managing the issue.
As per the previously mentioned The True Cost of Downtime 2022 Siemens report, condition monitoring and predictive maintenance have become indispensable mainstream technologies to counter these kinds of losses.
Level 2: Preventive maintenance
Preventive maintenance is the next obvious choice if you’re ready to take the next step. How cool would it be if you could identify a major breakdown before it actually happens?
You might feel like a James Bond equivalent who just diffused a ticking time bomb. And your feelings are not really far-fetched as you’d be doing the groundwork of doing regular inspections and keeping up with evolving regulatory standards to ensure occupant safety.
You’re a real hero.
Depending on the equipment, size, and other aspects of your facility, preventive maintenance can include a series of tasks, including:
- Frequently lubricating machinery to reduce degradation
- Inspecting and replacing HVAC filters every three months to ensure efficient operation
- Conducting quarterly checks on electrical systems to prevent potential failures
- Organizing ad-hoc training sessions to educate technicians about regulatory updates
Reactive maintenance may offer a quick solution, but it's like treating the symptom without addressing the cause. In contrast, preventive maintenance is all about being proactive, ensuring your equipment stays reliable and performs at its best.
Such preventive measures offer numerous benefits:
- Boost asset performance and lifecycle
- Maximize cost savings due to timely repair
- Reduce risks of accidents with better compliance and safety
A prerequisite for effectively carrying out preventive maintenance is being clear about the goals you want to achieve and the KPIs (Key Performance Indicators) you will use to track performance.
For example, to decrease maintenance costs at a particular facility, you can use KPIs such as planned maintenance percentage and mean time to repair (MTTR).
Once you have the goals and KPIs written down, follow this four-step process to get the best out of your preventive measures:
Step 1: Find the right technology
Use a connected computerized maintenance management system (CMMS) or computer-aided facility management (CaFM) system like Facilio for asset management, work order requests, and KPI tracking across various facilities.
The CMMS of 2024 should effectively oversee operations, review performance, optimize costs, and improve operational efficiency in the long term, all through a single dashboard, and reimagine facility management as a holistic and unified function.
Move beyond legacy tech, which keeps facility managers and FMSPs from realizing their preventive maintenance goals.
Step 2: Audit and data collection
Identify and prioritize assets based on criticality, failure history, replacement costs, accessibility, and safety. These five factors will help you work on the crucial assets first for smooth business operations.
Additionally, feed in data related to your asset’s performance, age, depreciation rate, current condition, usage, and repairs in your chosen CMMS. This data will be central to all the analysis you’ll do.
Step 3: Identify key maintenance requirements for chosen assets
Read the recommendation from the Original Equipment Manufacturer (OEM) manual to gather key information, such as maintenance guidance, frequency, and usage of critical parts. Another way is to talk to operators and technicians to get more specific insights.
Some of the factors that you must consider while choosing assets for your preventive maintenance plan are:
- Criticality: How critical is the asset in providing uninterrupted service to tenants and occupants? Does an asset's downtime bring losses and dissatisfaction? Prioritize critical assets that are indispensable for tenants’ day-to-day activities.
- Failure history: Give preference to assets with a failure history, as regular maintenance can extend their lifespan and prevent downtime.
- Replacement costs: How costly can it be for your enterprise to replace a particular asset in case of failure? To save on replacement costs, include expensive assets in your PM plan list.
- Accessibility: Sometimes, it can be easy to overlook assets that are harder to access. Do not overlook any asset; understand its value to determine the maintenance schedule.
- Safety: Does the asset’s failure cause security issues and potential risks to tenants and occupants? If yes, the list must include it to perform maintenance tasks and ensure safety for tenants and occupants.
Based on all of this, build an inspection checklist which, in a CMMS, looks like this:
Step 4: Build your preventive maintenance plan
You can build a preventive maintenance plan with your inspection checklist and list of assets. This plan should outline the type of preventive maintenance activities on each asset and the frequency of such repairs.
Suggested read: How to Build a Preventive Maintenance (PM) Checklist?
Level 3: Condition-based maintenance
Condition-based maintenance (CBM) relies on monitoring assets in real-time through sensors. It reports faults when certain thresholds are met, or conditions are triggered, enabling FMs to schedule the necessary maintenance, repair, or replacement tasks before the asset fails or disrupts your facility operations.
For example, in an office building, CBM can involve optimizing HVAC system care by using sensors to monitor key parameters like temperature, vibration, and airflow. By analyzing real-time data, you can detect issues such as unusual vibrations or airflow reductions early on and take preventive actions.
The condition-based approach reduces unnecessary servicing, lowers costs, minimizes downtime, and improves energy efficiency. This proactive approach ensures a comfortable environment for owners and extends asset lifespan.
Some of the common types of condition-based monitoring include:
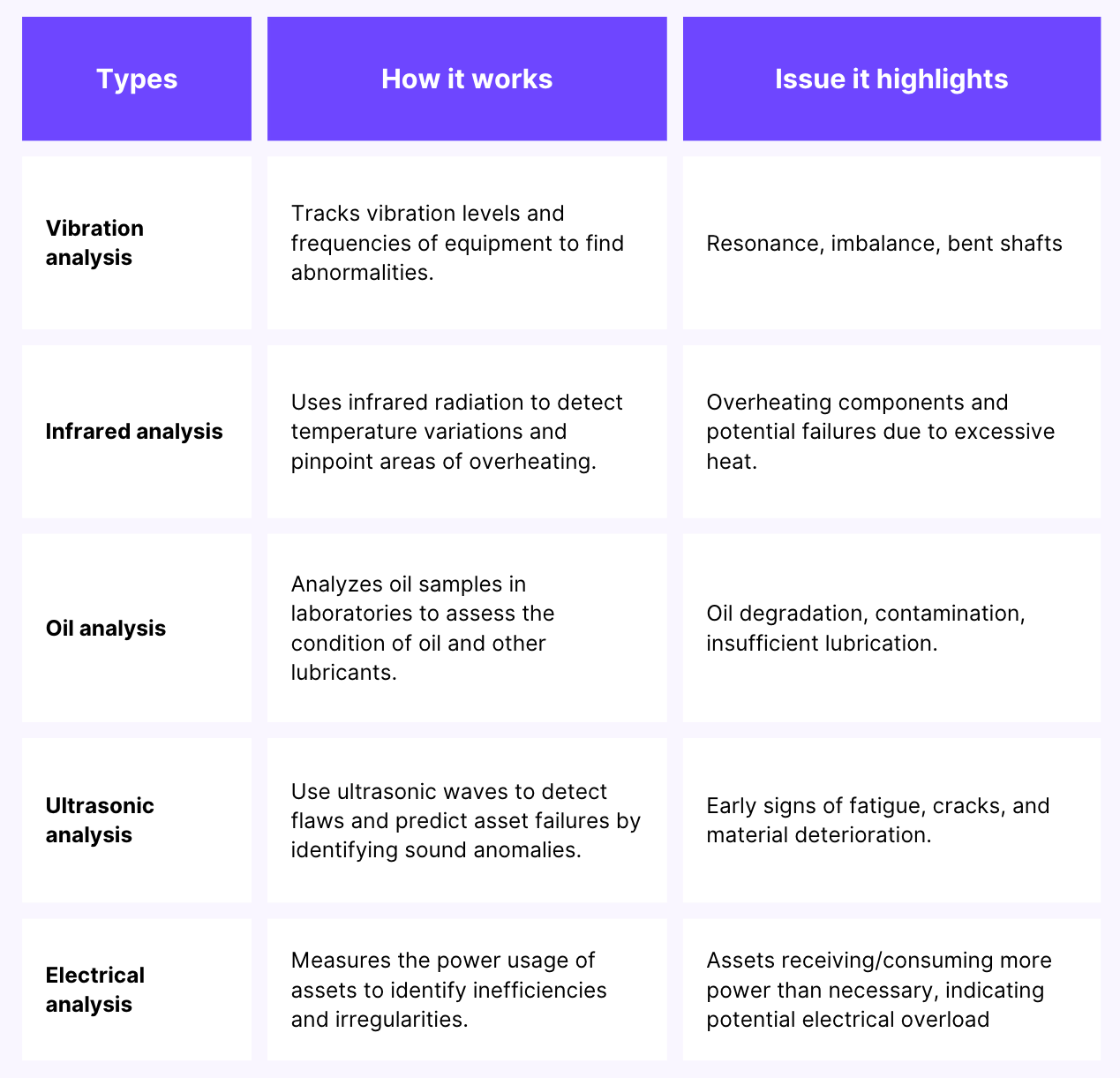
To effectively implement CBM, start by mapping out your assets, identifying failure modes, and establishing baselines with a connected CMMS.
By understanding what’s typical for your equipment and tracking its performance over time, you can gauge the overall health of your assets and determine when maintenance is needed.
A connected CMMS solution like Facilio not only helps FMs monitor equipment health but also tracks when maintenance is due. It also allows you to spot trends in failure rates, which can signal when it’s time for repairs or replacements.
Additionally, knowing the normal operating ranges for each piece of equipment in your fleet enables you to detect any anomalies that might indicate potential issues with specific machines or processes.
Level 4: Predictive maintenance
Predictive maintenance (PdM) anticipates when equipment will fail by combining data and advanced AI-powered analytics, allowing maintenance to be performed in advance.
Predictive maintenance involves real-time condition-monitoring devices, IoT sensors, hardware, and software that help you track equipment’s health, collect data, and make predictions before breakdowns occur.
For predictive maintenance to work, the following technologies are essential:
- Internet of Things (IoT) sensors
These sensors are the backbone of predictive maintenance, facilitating real-time monitoring and analysis of an equipment's health.
They monitor and control equipment remotely, requiring less manual inspection, send alerts when abnormal conditions occur (overheating or unusual vibrations), and feed data into cloud platforms, which help you predict breakdowns.
IoT sensors fitted on conveyor belts, for instance, track vibrations and usage patterns. When sensors detect irregularities—such as increased motor vibrations—they trigger alerts, prompting your team to inspect the machine before a breakdown occurs.
- AI and machine learning
Machine learning and AI are what make predictive maintenance possible. With these techniques, you can process historical and real-time data from sensors at lightning speed.
You can identify patterns that predict looming equipment failure using such quick analysis. The best part is that the more data these sensors send, the more machine learning and AI can learn and make more accurate and timely predictions.
- Cloud platforms
Cloud software houses a large volume of data from IoT sensors and helps you process, manage, and evaluate it in real time.
One of the leading software is a CMMS, which comes with built-in features such as asset history tracking, reporting dashboards, machine learning, and work management. Through a central management system, you can monitor your assets’ performance, raise requests when maintenance is paramount, and track the overall health of your assets across multiple facilities.
Facilio, for example, automatically creates maintenance work orders when it detects machinery is operating at a lower capacity than the assigned limit.
As with CBM, PdM collects data from sensors or hardware installed on various equipment and analyzes it using a connected CMMS. But there are a few key distinctions between these two approaches:
- Type of data used to approach maintenance: With CBM, the maintenance department performs maintenance on an as-needed basis, while PdM uses data analysis and machine learning to predict when it’s time to perform maintenance tasks. Compared to PdM, CBM is more of a reactive approach.
- Techniques used: CBM relies on inspections, tests, and real-time data to assess the equipment's current condition, while predictive maintenance is based on continuous monitoring and data analysis to predict future equipment behavior.
While both approaches aim to improve maintenance and operational efficiency, PdM takes CBM further by monitoring current conditions and forecasting future equipment health. Such proactive measures improve asset reliability, reduce maintenance waste, reduce inventory cost, and improve workplace safety.
For example, a leading offshore oil and gas operator reduced its facility’s downtime by 20% on average and increased production equivalent to more than 500,000 barrels of oil annually by implementing a PdM system across nine platforms in its African and Latin American facilities.
ICD Brookfield Place, for example, tapped into Facilio’s data consolidation, automatic fault detection, and predictive capabilities and raised alarms for the operations & maintenance teams to interject before the tenant raised a complaint.
Level 5: prescriptive maintenance
Prescriptive maintenance is the highest level of maintenance maturity and focuses actively on shaping a facility’s operational future, helping them stay ahead of issues rather than merely reacting to them.
It not only predicts failures but also suggests specific actions in advance to prevent them. This level of maturity goes one level beyond the predictive approach.
For instance, while predictive maintenance helps you anticipate future breakdowns, the prescriptive approach removes the guesswork by offering unbiased, more solid estimates of costs and issues.
Predictive maintenance is fueled by predictive analytics, which uses AI and machine learning to process historical data. It “learns” what has happened while uncovering unseen data patterns, interactions, and relationships to recommend the best course of action.
For example, Limbach, a premium service provider, optimized its building performance, identified energy-saving opportunities, and reduced operational costs even during non-operational hours.
The team achieved this through Facilio’s energy analytics dashboard, which offered real-time trend analysis, weather-based comparisons, and valuable insights based on their factory’s energy consumption.
The outcomes of reaching the highest level of maturity are unrivaled. Reduced equipment downtime cost, increased operational efficiency, and higher reliability are among the most noted.
Moving up the maintenance maturity ladder
Each maintenance level contributes value depending on the facility's size and the equipment's life cycle stage.
For instance, reactive maintenance resolves quick fixes, while predictive maintenance is called upon to plan and save days of downtime and additional technician costs. The peak of this model, prescriptive maintenance, focuses on advanced analytics and recommends specific actions to optimize performance.
Moving up to advanced levels of the maintenance maturity model, like predictive and prescriptive maintenance, offers significant advantages, such as lowering maintenance and production costs and reducing inventory needs.
However, it also demands various tools and technologies, such as a platform-based connected CMMS, and the expertise to use them effectively and interpret the data they generate.
A platform-based SaaS solution like Facilio can help you implement a cost-efficient, ROI-focused maintenance strategy.
If you’re ready to take the first step towards enhancing your facility management, book a demo and explore how Facilio can help elevate your maintenance maturity.