If you've been in building management for a while, you know detecting faults is like being a seasoned chef in a bustling kitchen.
What is fault detection and diagnostics?
Fault detection and diagnostics (FDD) is a software used in buildings to identify and diagnose faults or problems in various systems and equipment. This includes HVAC (Heating, Ventilation, and Air Conditioning) systems, lighting systems, electrical systems, and more. FDD utilizes specialized algorithms to analyze data from sensors and equipment to identify and pinpoint issues, allowing for prompt and efficient maintenance and repair.
How Do Fault Detection and Diagnostics in Buildings work?
Fault detection and diagnostics software utilizes advanced algorithms and machine learning techniques to analyze data from sensors and equipment within a building.
These sensors gather information about various parameters, such as temperature, pressure, humidity, and energy consumption. The software then compares the collected data to predefined patterns and models to identify deviations and potential faults.
But how exactly does this software work?
Let's dive deeper into the process.
The process of fault detection and diagnosis
FDD involves several stages that enable the accurate identification and resolution of issues in building systems. These stages include:
#1. Data Collection
Sensors and monitoring systems collect data on various parameters, such as temperature, pressure, and energy consumption. Then these sensors are strategically placed throughout the building to capture real-time information about the performance of different systems.
Examples of monitored parameters include:
- Temperature (heating and cooling systems)
- Pressure (water supply and HVAC systems)
- Energy consumption (electricity, gas, or other sources).
With these sensors, you can continuously measure and record data, providing a comprehensive picture of the building's operational status.
#2. Data Analysis
The collected data is then analyzed using fault detection and diagnostic software. With FDD software like Facilio, you can bypass the challenges of implementing complex solutions for each system or site with diverse vendor systems and communication protocols to meet reliability targets.
Instead, you can gain a comprehensive view of Energy Performance Indicators (EnPIs), system failure trends, and resolution times.
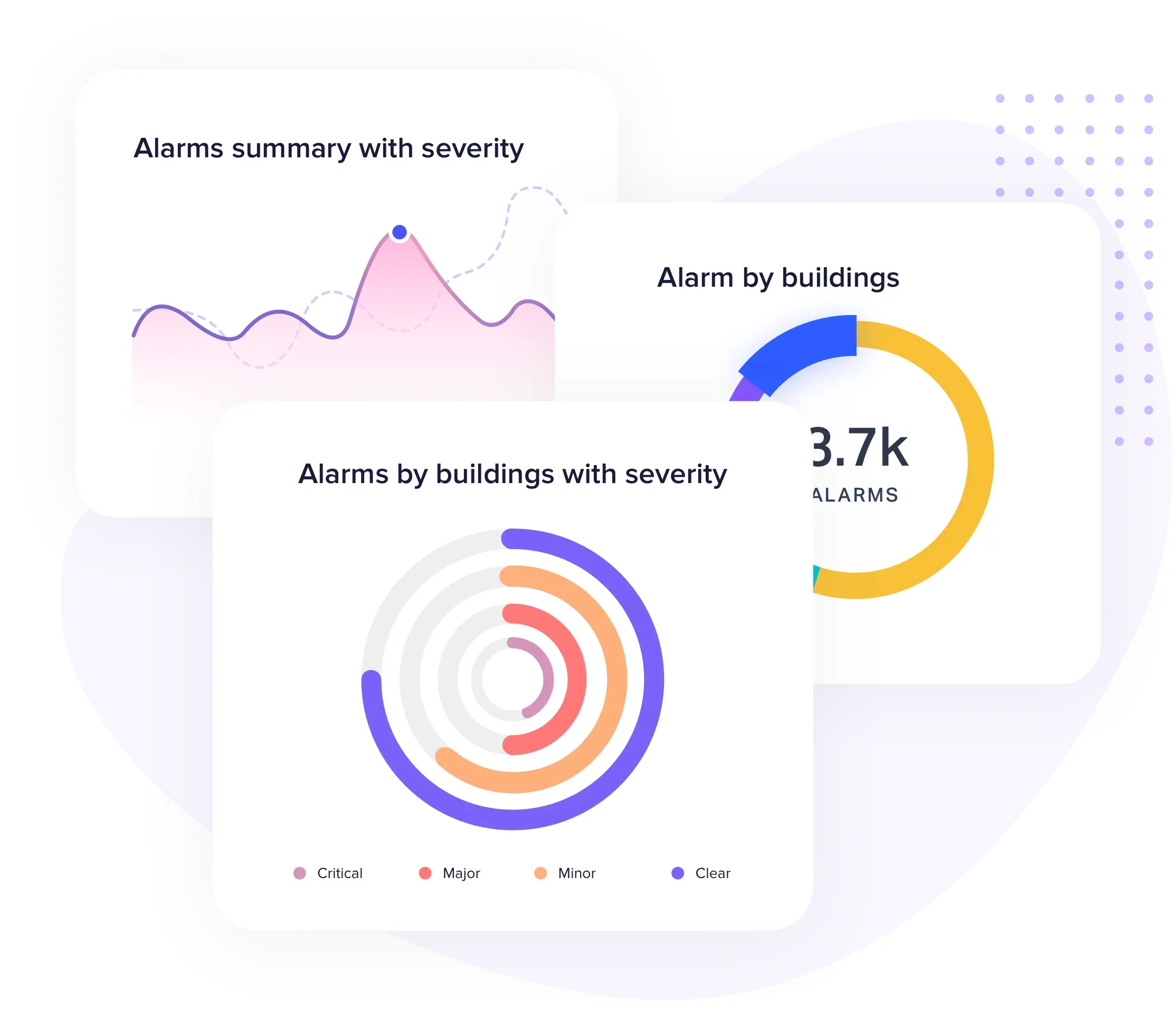
Facilio compares collected data to predefined patterns and models to help detect deviations from normal operating conditions. So, you can identify potential faults that may not be immediately apparent to human operators.
#3. Fault Identification
FDD software then flags deviations and potential faults based on the analyzed data. Luckily, Facilio has predefined alarm templates to meet the unique needs of your building by specifying simple or complex conditions. You can now take charge of your building by going beyond basic alarms and nitpicking every little detail to eliminate inefficiencies
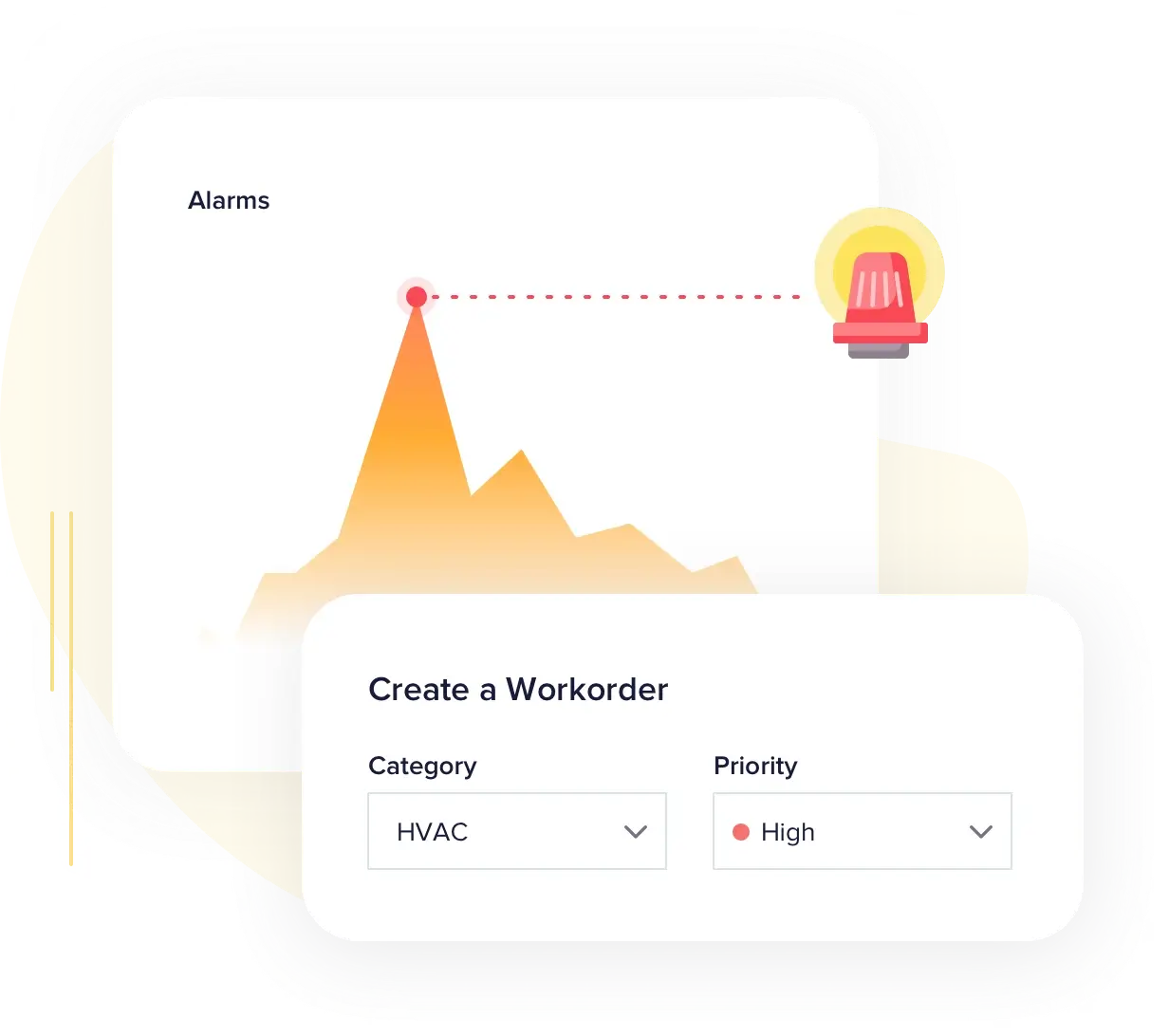
Anomalies are highlighted for further investigation by facility managers and technicians. This helps prevent minor issues from escalating into major problems, minimizing downtime and costly repairs.
#4. Fault Diagnosis:
Once potential faults are identified, further analysis is conducted to determine their root cause. This involves a detailed examination of the data, considering various factors that could contribute to the fault.
The fault diagnosis process aims to provide facility managers and technicians with a comprehensive understanding of the underlying issues, enabling them to develop effective strategies for resolution.
Detailed diagnostics, including recommended actions and potential solutions, are generated to guide the fault resolution process.
#5. Action and Resolution
Equipped with detailed diagnostics, facility managers and technicians address faults by adjusting system settings, replacing faulty components, or implementing maintenance procedures. These actions rely on recommendations from fault detection software and the expertise of personnel. Promptly addressing faults optimizes the building's performance and energy efficiency, ensuring a comfortable and safe environment for occupants.
What are the three stages of fault diagnosis in Buildings?
Fault diagnosis typically involves three stages:
#1. Fault Detection
This stage focuses on identifying the presence of faults or abnormalities in building systems. During the fault detection stage, various methods and tools are employed to monitor and analyze the performance of building systems. These methods may include sensor networks, data logging, and automated fault detection algorithms.
By continuously monitoring the system, any deviations from normal operation can be detected, indicating the presence of a fault.
#2. Fault Isolation:
Once a fault is detected, the next step is to isolate the faulty component or subsystem. This involves a systematic approach of analyzing the data collected during the fault detection stage and narrowing down the potential causes.
#3. Fault Identification:
After isolating the faulty component, the fault identification stage focuses on determining the root cause of the fault. This requires a thorough analysis of the component's behaviour, performance characteristics, and any relevant environmental factors.
Once the root cause is determined, a detailed diagnosis is provided, outlining the necessary repairs or maintenance actions to rectify the fault. This enables targeted and efficient maintenance, minimizing downtime and optimizing the performance of the building systems.
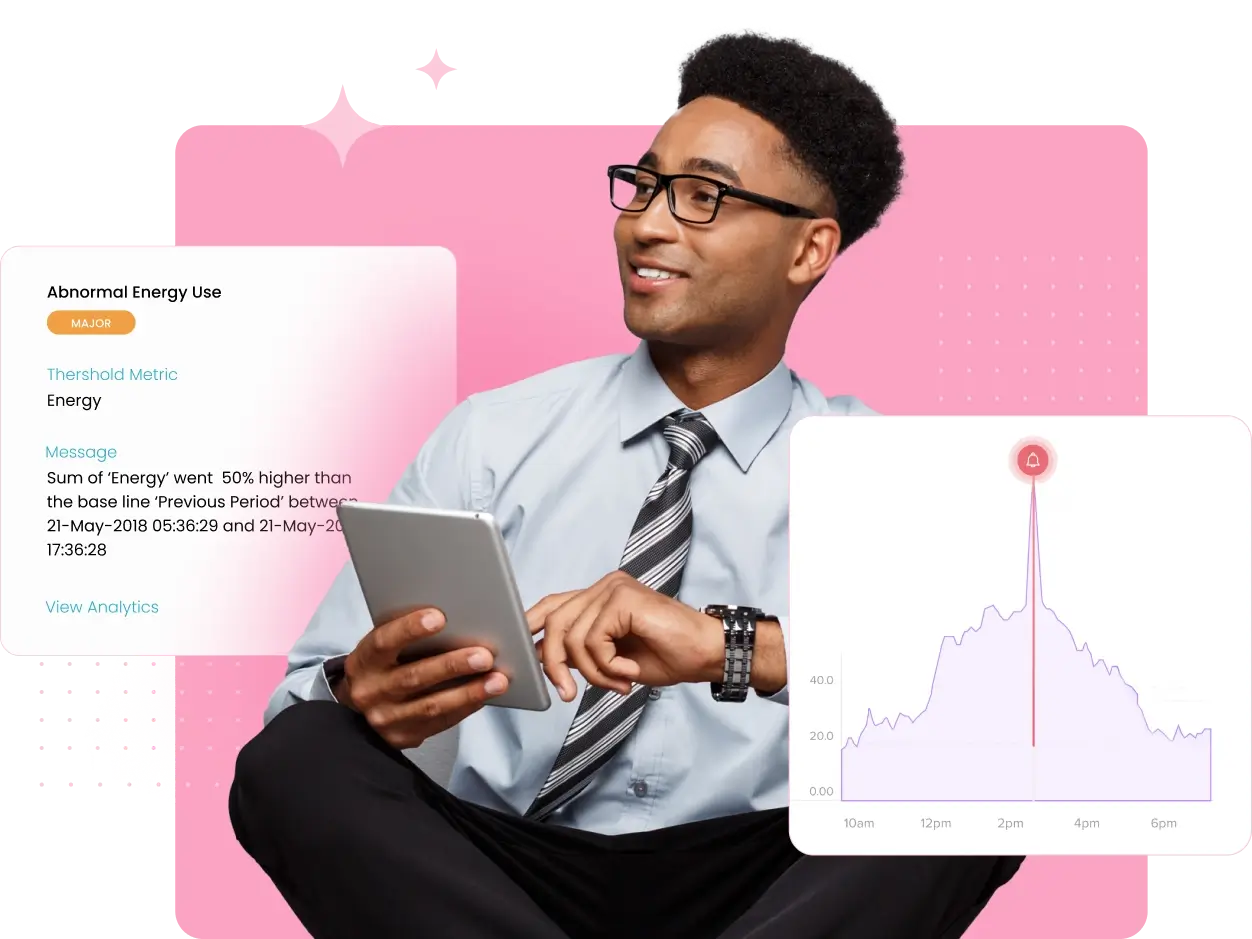
Empower your enterprise with centralized FDD from Facilio
Streamline performance, enhance energy efficiency, and gain unparalleled insights. Elevate your building management to new heights – choose Facilio for a smarter, more efficient future
What are the different techniques for fault detection and diagnosis in Buildings?
When it comes to fault detection and diagnosis in buildings, there are several techniques that are designed to identify and address faults in building systems, ensuring optimal performance and energy efficiency.
Let's explore some of the different types of these methods:
1. Rule-based technique:
Rule-based methods rely on predefined rules and heuristics to identify faults based on specific patterns or thresholds. Imagine you have a rule that says, "If the temperature in a room goes too high, there might be a problem with the HVAC system." Or if a machine is making strange vibrations or a sensor detects unusual pressure, the rules can spot these problems early on.These rules are handy in places like factories or buildings.
However, there's a challenge.
These rules work best when problems follow a pattern. If an issue is more complicated or keeps changing, the rules might struggle. Also, updating the rules can take some effort because experts need to keep an eye on the system and adjust the rules accordingly.
2. Model-based technique:
Model-based methods are like having a blueprint for how a building or system should work. FDD Algorithms create these "blueprints" (models) based on their deep knowledge of the physics and engineering principles behind the system. They use this understanding to predict how things should work under normal conditions.
Now, when the actual performance of the system is compared to what the model expects, any differences can be spotted.
Example, if a building should use a certain amount of energy according to the model, but it's using way more in reality, it might mean there's a problem with how the energy is being managed.
3. Data-driven technique:
Data-driven methods utilize machine learning algorithms to analyze historical data and identify patterns and anomalies that indicate faults. These methods are great because they can find complex problems that might not be caught by simple rules or blueprints.
They keep an eye on data coming from various sensors and systems all the time. If there's a sudden change or something doesn't match the usual patterns, the algorithm raises a red flag.
Example, if the amount of energy used in a building suddenly behaves strangely, the detective algorithm can tell us that something might be wrong with specific equipment or systems in the building.
4. Hybrid Methods:
Hybrid methods combine multiple fault detection and diagnosis techniques to enhance accuracy and diagnostic capabilities.
A Hybrid method may combine rule-based and data-driven approaches to improve fault detection accuracy and reduce false positives.
For building owners and operators, having a hybrid system of fault detection methods is crucial. It means you can catch issues early, fix them on time, save energy, and cut down on costs. It's like having a reliable security system for a building's health, making sure everything runs smoothly for a long time.
Related Resources:
- What is Preventive Maintenance? A Comprehensive Guide
- Balancing Reliability and Availability: Striving for the Best of Both Worlds
How to Implement the right FDD for your Portfolio?
The market is saturated with numerous FDD solutions, each with its own set of methods, models, and features. This abundance often leads to information overload, leaving you, as a building owner or operator, unsure about what to consider beyond technical features. It becomes challenging to compare the different approaches and frame the right questions to evaluate what’s best for your portfolio needs.
Here are some things to consider before choosing your FDD:
- Product vs Service
- Cloud vs On-Prem
- Flexibility in Analysis
- Ease of Switching
- Operational Intelligence
- Total Cost of Ownership
Interested in knowing more? Grab our free FDD Evaluation guide and find the right tool for your portfolio.
Benefits of automating your building's fault detection and diagnostics with Facilio
Benefit #1: Centralized fault detection and management for each asset/building
(Instead of relying on disparate and siloed monitoring systems)
You can create entries for each asset, gaining a comprehensive overview of issues. Record entry times, track status, and apply filters to suppress redundancies
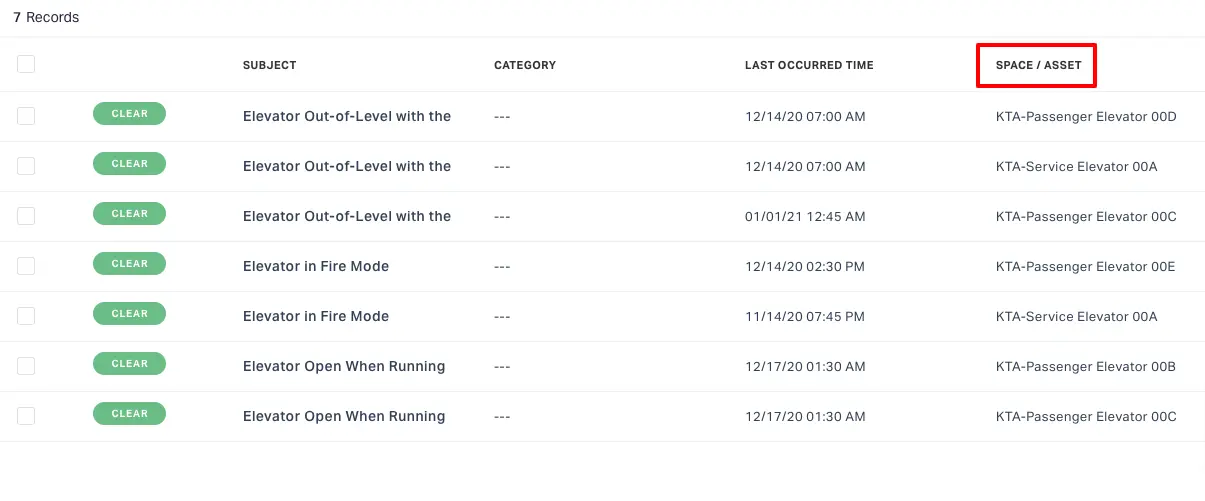
Benefit #2: Individual fault summaries with it's insights
( Instead of triaging through the long list of alarms)
With Facilio's root cause and scoring feature, you can create separate summary for each faults and view it's insights including the list of possible route causes for the particular fault.
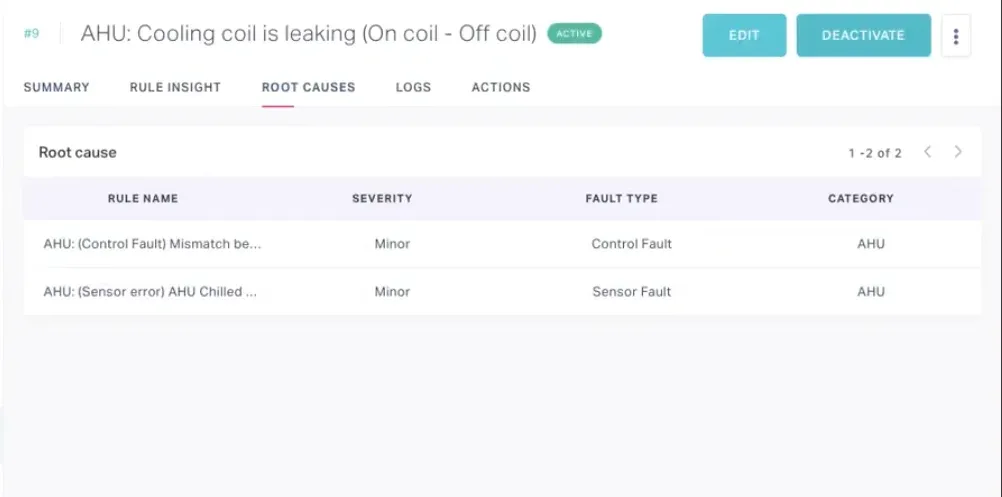
Benefit #3: You can edit and modify root causes effortlessly
Learn how to perform a root cause analysis with Facilio
Benefit #4: Assign scores to specific Root causes to prioritize and resolve issues in real-time
(Instead of wasting your time on irrelevant causes)
The higher the score assigned to a specific root cause, the more probable it is to be the actual issue. Example, here in the image below, the particular fault has been ranked 2 out of 10 most common alarm issues.
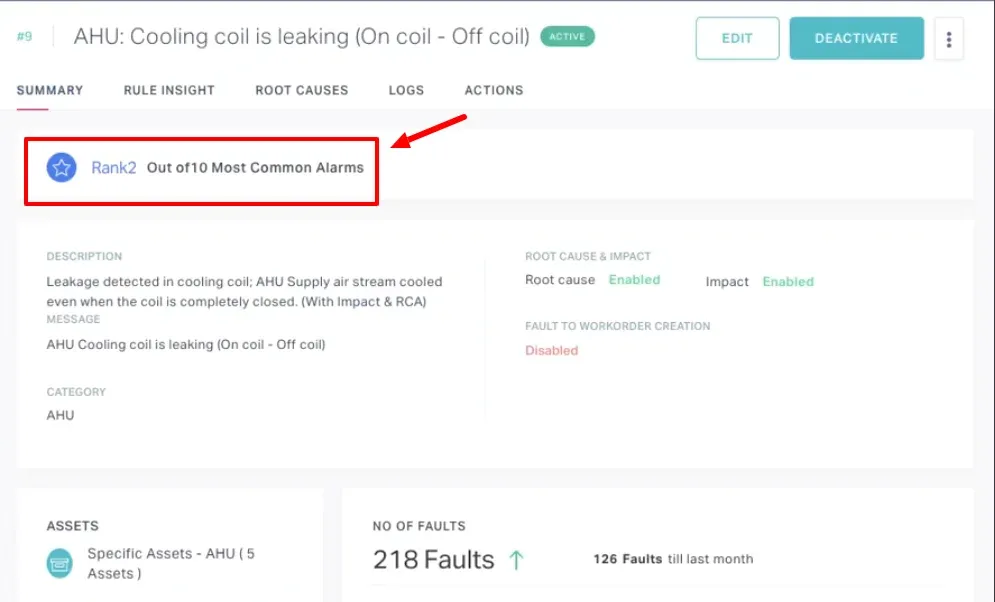
This comprehensive scoring method will allow you to prioritize actions and resolve issues efficiently preventing major breakdowns and costly repairs.
Transform Your Fault Detection and diagnostics with Facilio
Facilio eliminates the need for complex implementations across various systems/sites with diverse vendor systems and communication protocols. Beyond achieving reliability targets, this streamlined approach offers insightful visibility into Energy Performance Indicators (EnPIs), system failure trends, and resolution times.
This empowers you to assess asset health comprehensively and identify opportunities for energy savings throughout your portfolio.
Interested to learn more?