From Cost Center to Profit Driver: How IFMs Can Leverage Technology to Achieve Growth
Integrated Facility Management (IFM) systems are essential—they keep the wheels turning, ensure smooth operations, and manage the daily grind of facility upkeep.
However, many facility managers believe that achieving this level of operational efficiency requires accepting high costs as a norm.
It's a common misconception that better operations inevitably come with a hefty price tag. But what if I told you that this isn't necessarily the case?
The truth is, while IFMs get the job done, they often do so with a hidden cost—unnecessary expenses that can be avoided with more strategic management.
Imagine running a facility where every malfunction triggers an immediate and costly response. The lights flicker, HVAC systems sputter, and before you know it, you're writing checks for emergency repairs, paying premium rates for rush jobs, and dealing with the fallout of downtime.
Sure, everything gets fixed, but at what cost?
High operational costs don't have to be a given. You can maintain high standards without the inflated expenses. It's time to rethink how we view IFM costs and recognize that efficiency and cost-effectiveness are not mutually exclusive.
The main drains of facility management budgets
IFM systems come with unseen costs that transform them into perceived cost centers rather than assets that drive value. Here are some of the major inefficiencies that inflate IFM costs:
1. High reactive maintenance costs
One of the major budget drainers in IFMs is reactive maintenance work orders. Relying on reactive maintenance often leads to unexpected breakdowns and costly repairs.
Additionally, reactive maintenance often results in temporary fixes rather than long-term solutions, leading to repeated failures and escalating costs over time.
B2B research firm Aberdeen calculates that businesses typically experience losses of $260,000 for each hour of downtime, amounting to more than $2 million annually. However, the actual figure is probably greater when factoring in additional expenses from workplace accidents, equipment replacement needs, and various other costs.
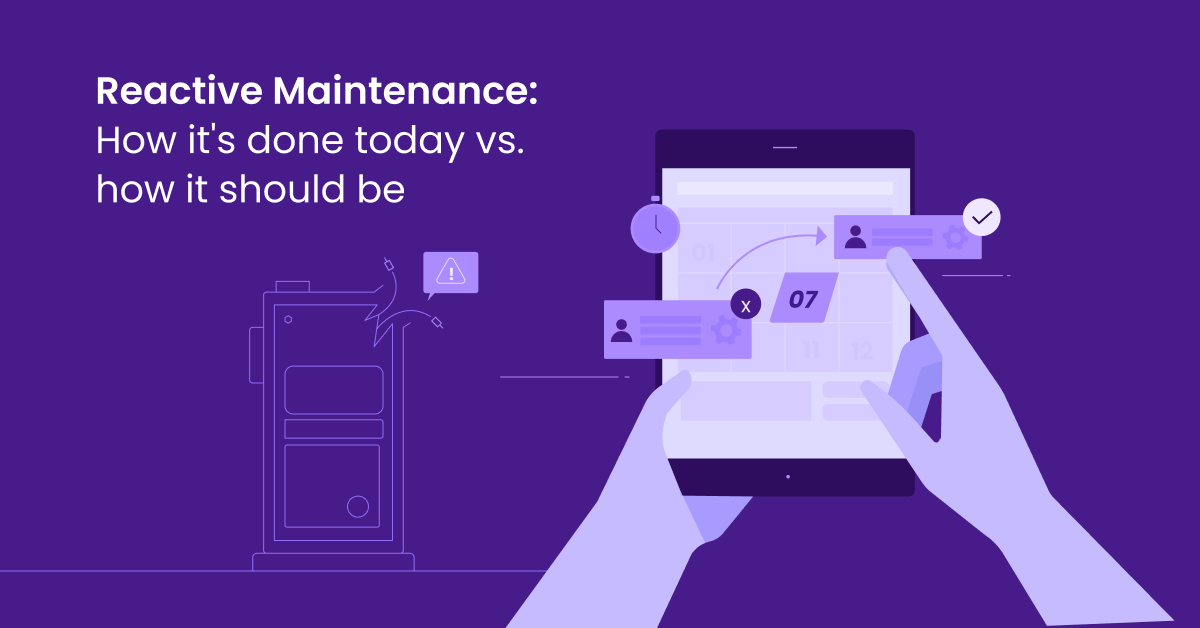
2. Inefficient processes
Many IFMs still operate with outdated, manual processes or traditional CMMS systems that slow down operations and inflate costs. These systems increase the risk of human error in data entry and inventory tracking and lack real-time data integration, making them ineffective for large-scale operations.
Manual processes result in scheduling conflicts, resource underutilization, and delayed responses to maintenance issues, while legacy CMMS platforms suffer from clunky interfaces and poor integration with modern technologies.
This lack of efficiency leads to delayed identification and resolution of problems, causing operational disruptions and escalating costs. Additionally, maintaining these older systems can be expensive, further diverting resources from more strategic initiatives.
3. Lack of data integration
When your data is scattered across multiple systems, it's like trying to piece together a puzzle with half the pieces missing. This means that valuable information—such as asset performance data, maintenance histories, and cost tracking—is isolated in separate systems or departments.
For instance, your financial data might be in one place, and your maintenance logs in another, with no way to seamlessly connect them. This lack of integration can deprive you of valuable insights and opportunities for cost savings.
Without comprehensive data, it can be difficult to analyze the total cost of ownership of equipment, forecast maintenance needs accurately, or optimize inventory levels for spare parts. Consequently, this disjointed approach can lead to overstocking, stockouts, and inefficiencies in maintenance scheduling and resource allocation.
But what if it doesn't have to be this way? Enter predictive maintenance—a proactive approach that uses technology to anticipate issues before they escalate.
Predictive maintenance: The game changer
But there's a better way. Predictive maintenance revolutionizes how you manage your facilities by anticipating issues before they arise, optimizing operations, and reducing costs—all in real time.
By leveraging IoT sensors and advanced analytics, predictive maintenance provides real-time insights into equipment health, allowing for planned maintenance instead of reactive repairs.
This approach not only reduces costs associated with emergency repairs but also extends the lifespan of your equipment, thus reducing the frequency and severity of breakdowns.
Predictive maintenance can shift your IFM from a financial drain to a profit-enhancing asset and a growth accelerator.
The benefits of predictive maintenance you can’t afford to ignore
Imagine a manufacturing facility plagued by frequent equipment failures that disrupt production and lead to high repair costs and lost revenue. The traditional reactive maintenance model leaves the facility struggling with unplanned downtime and escalating expenses.
For example, when a machine unexpectedly breaks down, not only does it halt the production line, but the rush to get it back online often involves paying premium rates for parts and labour. Additionally, the lack of preparation can lead to longer repair times, as parts may not be readily available, further extending downtime.
Contrast this with the facility's experience after adopting predictive maintenance. The facility would maintain consistent production schedules and note a marked reduction in maintenance expenses due to the reduced downtimes and associated costs. But that is not all. Let's take a closer look at the benefits of having a predictive maintenance system for your facilities.
1. Slash costs and boost operational efficiency
With predictive maintenance, your facility can significantly cut costs associated with emergency repairs and extend the lifespan of critical assets.
This leads to much more efficient operations and substantial cost savings, as maintenance activities are planned based on data-driven insights rather than reactive fixes.
For example, regularly monitoring equipment health can help identify components that are nearing the end of their life cycle, allowing for timely replacements that prevent failures.
Additionally, by analyzing historical data, facilities can optimize maintenance schedules to minimize wear and tear, thus extending the lifespan of assets and reducing the need for costly replacements.
2. Increase productivity and reduce downtime
The proactive nature of predictive maintenance ensures that potential problems are addressed before they disrupt operations. This results in fewer interruptions and a more focused and productive workforce, as team members can concentrate on their core responsibilities without being sidetracked by emergency repairs.
Higher productivity directly correlates with greater capacity for scaling operations, supporting business growth.
3. Optimize resources to enable business growth
The connection between efficiency and growth is clear: when maintenance workflows are optimized, and resource costs are reduced, the freed-up capital and time can be redirected toward innovation, expansion, and other growth-oriented activities.
For instance, a company that saves on maintenance costs can invest in upgrading equipment, expanding its facilities, or entering new markets.
By optimizing resources and reducing waste, predictive maintenance creates a financial cushion that can be leveraged to accelerate growth. Additionally, the optimized efficiency gained through predictive maintenance can enhance a company's reputation, attracting customers and opening new revenue streams.
Case study: From high costs to high growth and efficiency
Let's break down a real-world example to see these outcomes in action:
The problem: A large commercial real estate firm faced high maintenance costs and frequent tenant complaints due to unplanned equipment failures and inefficient processes.
Tenants were often inconvenienced by sudden outages and slow responses to maintenance issues, leading to dissatisfaction and higher turnover rates.
The solution: The firm implements predictive maintenance, integrating IoT sensors and data analytics to monitor building systems in real-time.
This allows them to schedule maintenance activities proactively, avoiding unexpected breakdowns. For example, by monitoring HVAC systems, they predict and address issues before they cause discomfort for tenants.
The results: The firm notes a 30% reduction in maintenance expenses and significantly improved tenant satisfaction by addressing issues before they affected building operations.
The cost savings are reinvested into enhancing tenant amenities, such as upgrading common areas and offering additional services, which further boosts tenant retention and attracts new clients.
Additionally, the streamlined operations and improved tenant experience position the firm as a market leader, allowing it to expand its property portfolio and increase revenue.
Key takeaway: Predictive maintenance turns IFMs from a cost centre into a growth engine. By enhancing efficiency, reducing costs, and improving tenant experiences, IFMs can position themselves for sustainable growth.
Turn your IFM into a growth engine with predictive maintenance
The message is clear: Predictive maintenance isn't just a tool; it's a strategic approach that redefines facility management.
By shifting from reactive to predictive maintenance, your IFM can become a cornerstone of profitability and growth. It's time to make the switch and unlock the full potential of your operations.
Get started now.
Ready to optimize your IFM costs and drive growth?