Improving Operational Efficiency with Enhanced Equipment Reliability
Equipment reliability refers to the ability of a machine or system to perform its intended function without failure or breakdown. It is achieved with systematic approaches to maintenance & reliability that ensure the consistent performance and dependability of equipment throughout its operational life.
In today's fast-paced industrial landscape, equipment reliability is crucial for maximizing productivity, minimizing downtime, and maintaining a competitive edge.
Whether you are a maintenance professional, an operations manager, or an executive overseeing a complex facility, this article will provide actionable insights to optimize your equipment performance and enhance overall operational efficiency.
Understanding equipment reliability: A brief history
The roots of equipment reliability can be traced back to the early days of industrialization. As industries began to rely heavily on machinery for production, the impact of equipment failures became increasingly evident.
The first step in addressing this issue was the establishment of preventive maintenance practices. Organizations started conducting routine inspections, lubrication, and minor repairs to keep their equipment in optimal condition.
In the mid-20th century, the advent of reliability engineering brought a more systematic approach to the field. Reliability engineering focused on analyzing and predicting the performance and failure of equipment.
Methods such as Failure Modes and Effects Analysis (FMEA) and Fault Tree Analysis (FTA) were developed to assess failure risks and identify ways to mitigate them proactively.
Examples of equipment reliability
Enterprises have demonstrated a strong focus on equipment reliability throughout history. Companies like Toyota, General Electric (GE), NASA, and ExxonMobil have demonstrated a strong commitment to equipment reliability.
Toyota implemented the Total Productive Maintenance (TPM) approach, empowering operators to take ownership of equipment reliability, which played a crucial role in its rise to become one of the world's leading automotive manufacturers.
GE embraced the Six Sigma methodology to improve equipment reliability and quality. By systematically analyzing and eliminating defects and failures, GE aimed to achieve a high level of equipment performance and reliability and achieved significant improvements in equipment reliability, quality, and overall operational efficiency within the company.
In 1970, NASA adopted Reliability-Centered Maintenance (RCM) to ensure reliability in critical systems and played a vital role in the success of numerous space missions, where equipment reliability was of utmost importance for the safety of astronauts and the success of the missions.
Meanwhile, ExxonMobil implemented Asset Integrity Management (AIM) to minimize failures and optimize asset performance, ensuring the integrity and reliability of critical assets in the oil and gas industry.
These companies recognized the significance of equipment reliability and its impact on productivity, safety, and customer satisfaction. By prioritizing equipment reliability at scale, they achieved remarkable results and set industry standards for others to follow.
Equipment reliability practices have become widespread across various industries, with companies of all sizes recognizing the importance of maintaining reliable equipment to achieve operational excellence and gain a competitive edge.
Recent Innovations in Equipment Reliability
Advancements in technology and data analytics have revolutionized the field of equipment reliability.
Predictive maintenance and condition monitoring techniques, enabled by the Internet of Things (IoT) and sensor technology, allow organizations to collect real-time data and predict maintenance needs.
Big data analytics and machine learning extract valuable insights from equipment performance data, while remote monitoring and digital twins simulate equipment behavior.
Integration of Enterprise Asset Management (EAM) software with IoT devices centralizes asset management and enables data-driven decision-making.
The concept of equipment reliability has evolved over time, driven by the need to minimize downtime and optimize productivity.
Ensure sustained peak performance and health for all your assets
Book a demoHow to measure equipment reliability?
You can measure the effectiveness of equipment reliability using several different reliability KPIs.
Here are some essential metrics commonly used ones:
1. Mean Time Between Failures (MTBF)
MTBF is a fundamental metric used to quantify the reliability of equipment. It represents the average time between failures. A higher MTBF value indicates greater reliability and longer intervals between failures.
The formula for MTBF is:
For example, if a machine operates for 1,000 hours and experiences 10 failures during that period, the MTBF would be 100 hours.
By tracking MTBF, organizations can assess the effectiveness of maintenance strategies and identify opportunities for improvement.
2. Mean Time to Repair (MTTR)
MTTR measures the average time required to repair failed equipment and bring it back to normal operation. Organizations strive to minimize MTTR to reduce downtime and enhance overall equipment availability.
The formula for MTTR is:
For instance, if a machine incurs a total downtime of 50 hours over 5 repair incidents, the MTTR would be 10 hours.
Tracking MTTR helps identify bottlenecks in the repair process and highlights areas where efficiency gains can be made.
3. Overall Equipment Effectiveness (OEE)
OEE is a comprehensive metric that provides insights into equipment performance, availability, and quality. It combines three components: availability, performance efficiency, and quality rate.
The formula for calculating OEE is:
- Availability represents the percentage of time the equipment is available for production.
- Performance efficiency measures the actual production rate compared to the maximum achievable rate.
- Quality rate reflects the percentage of good-quality products produced.
For example, let's say a manufacturing plant operates a machine for 8 hours a day, 5 days a week, with an availability of 90%. The performance efficiency is measured at 80%, meaning the machine operates at 80% of its maximum achievable rate.
The quality rate stands at 95%, indicating that 95% of the products produced meet the desired quality standards.
Using these values, the OEE calculation would be as follows:
OEE = 0.9 (availability) x 0.8 (performance efficiency) x 0.95 (quality rate) = 0.684 or 68.4%
This means the equipment's overall effectiveness is 68.4%. By tracking OEE, organizations can identify areas where improvements can be made to enhance overall equipment performance.
Now, let's dive into how you can identify and implement the right equipment reliability programs for your organization.
How to identify the right equipment reliability program for your organization?
To identify and implement the right equipment reliability technique(s) for your organization, follow these steps:
- Assess equipment criticality: Evaluate the importance of each equipment to your operations. For example, a critical machine in a manufacturing plant may have a higher priority for reliability improvement compared to a non-essential tool.
- Review historical data: Analyze past equipment failures and maintenance records. If you notice a recurring issue with motor failures in your fleet of delivery trucks, you may consider PdM techniques to detect early signs of motor degradation.
- Identify challenges: Identify specific reliability challenges you face. For example, if unplanned equipment breakdowns are causing production delays, focus on techniques like PM to proactively address potential failures.
- Research techniques: Explore available reliability techniques, such as FMEA or condition monitoring. Understand their principles and benefits. For instance, FMEA helps you identify potential failure modes and their effects, allowing you to prioritize preventive measures.
- Consider EAM software: Evaluate the benefits of using EAM software for equipment reliability management. EAM software can streamline maintenance processes, enable data-driven decision-making, and provide insights for optimizing maintenance strategies.
- Consider resource availability: Evaluate resources like budget and personnel. Choose techniques that align with your available resources, including the implementation and utilization of EAM software. For example, consider the cost and training requirements associated with implementing the software.
- Prioritize techniques: Prioritize techniques based on their potential impact, including the role of EAM software. For instance, if downtime is a major concern, focus on techniques like predictive maintenance supported by EAM software that can significantly reduce unplanned equipment failures.
- Implement and monitor: Develop an implementation plan, assign responsibilities, and set measurable goals. Monitor the effectiveness of the implemented techniques, including the utilization of EAM software, and make adjustments as needed. For example, track KPIs related to equipment reliability and maintenance efficiency.
10 ways to improve equipment reliability
Unreliable equipment means unplanned downtimes, which can be devastatingly expensive.
A recent report predicts unplanned downtime will cost Fortune Global 500 industrial companies almost $1.5 trillion this year, 11% of their annual revenues.
Previous research from 2019 to 2020 put the cost to these companies at $864 billion a year, around eight percent of turnover.
Further, the cost of non-compliance and safety risks is very high for organizations that might not pay enough attention to improving equipment reliability.
Here are 10 ways you can improve your equipment reliability program and avoid the nightmares ineffective maintenance programs can bring:
- Implement proactive maintenance strategies, such as preventive maintenance and condition-based maintenance, to identify and address issues before they cause failures.
- Conduct regular equipment inspections and perform necessary repairs promptly to prevent small issues from escalating into major problems.
- Ensure proper lubrication and maintenance of moving parts to minimize friction and wear.
- Train and educate equipment operators and maintenance personnel on proper usage, maintenance procedures, and troubleshooting techniques.
- Use advanced monitoring technologies, such as sensors and predictive analytics, to detect potential equipment failures and take preventive actions.
- Establish an effective spare parts management system to ensure the timely availability of critical components.
- Optimize equipment operating conditions, such as temperature, pressure, and speed, to maximize performance and longevity.
- Implement a robust equipment failure analysis program to identify root causes and implement corrective actions.
- Regularly review and update equipment maintenance plans based on historical data and performance feedback.
- Foster a culture of safety and accountability among the workforce to ensure equipment is operated and maintained properly.
Types of equipment reliability techniques
- Preventive Maintenance (PM): Scheduled inspections and maintenance activities performed to prevent equipment failures and ensure optimal performance.
- Predictive Maintenance (PdM): Monitoring equipment condition in real-time to detect early signs of deterioration and schedule maintenance actions accordingly.
- Reliability Centered Maintenance (RCM): A systematic approach to determine maintenance strategies based on critical equipment functions and the consequences of failure.
- Failure Modes and Effects Analysis (FMEA): Identifying potential failure modes, analyzing their effects, and assigning criticality ratings to prioritize preventive measures.
- Fault Tree Analysis (FTA): A graphical representation used to identify root causes of failures and analyze the logical relationships between failure events.
- Root Cause Analysis (RCA): Investigating and determining the underlying causes of equipment failures to implement effective corrective actions.
- Reliability Growth Analysis (RGA): Statistical analysis to predict and improve equipment reliability over time based on failure data.
- Condition Monitoring: Continuous or periodic assessment of equipment health using various sensors and techniques to detect early signs of degradation or failure.
- Total Productive Maintenance (TPM): Involving all employees in equipment maintenance to maximize equipment effectiveness and promote continuous improvement.
- Risk-Based Maintenance (RBM): Prioritizing maintenance activities based on risk assessments, and allocating resources to high-risk assets.
- Proactive Maintenance: Identifying and addressing potential failure modes and performance issues before they occur.
- Condition-Based Maintenance (CBM): Making maintenance decisions based on real-time equipment condition data obtained through monitoring techniques.
- Reliability Block Diagram (RBD): Graphical representation illustrating the logical relationship and reliability characteristics of components within a system.
- Weibull Analysis: Statistical technique to analyze failure data and estimate equipment reliability characteristics over time.
- Spare Parts Optimization: Optimizing spare parts inventory to ensure the availability of critical components while minimizing inventory costs.
- Reliability-Centered Spares (RCS): Identifying and prioritizing critical spare parts based on their impact on equipment performance.
- Failure Reporting, Analysis, and Corrective Action System (FRACAS): A structured process for tracking, analyzing, and resolving equipment failures.
- Overall Equipment Effectiveness (OEE): Metric measuring equipment performance, availability, and quality to identify areas for improvement.
What you need to enable equipment reliability at scale is Enterprise Asset Management (EAM) software.
EAM software enables equipment reliability programs by providing a centralized platform for managing assets, facilitating preventive maintenance planning, work order management, and integrating condition monitoring to detect anomalies and enable predictive maintenance, ultimately improving overall equipment reliability.
Leveraging EAM Software for Enhanced Equipment Reliability
EAM software like Facilio are powerful tools organizations can leverage to optimize maintenance operations and improve equipment reliability. It provides a centralized platform for managing and monitoring assets throughout their lifecycle.
With Facilio, you can access comprehensive asset insights on a single screen, allowing stakeholders to monitor real-time performance and track asset movement using intuitive dashboards.
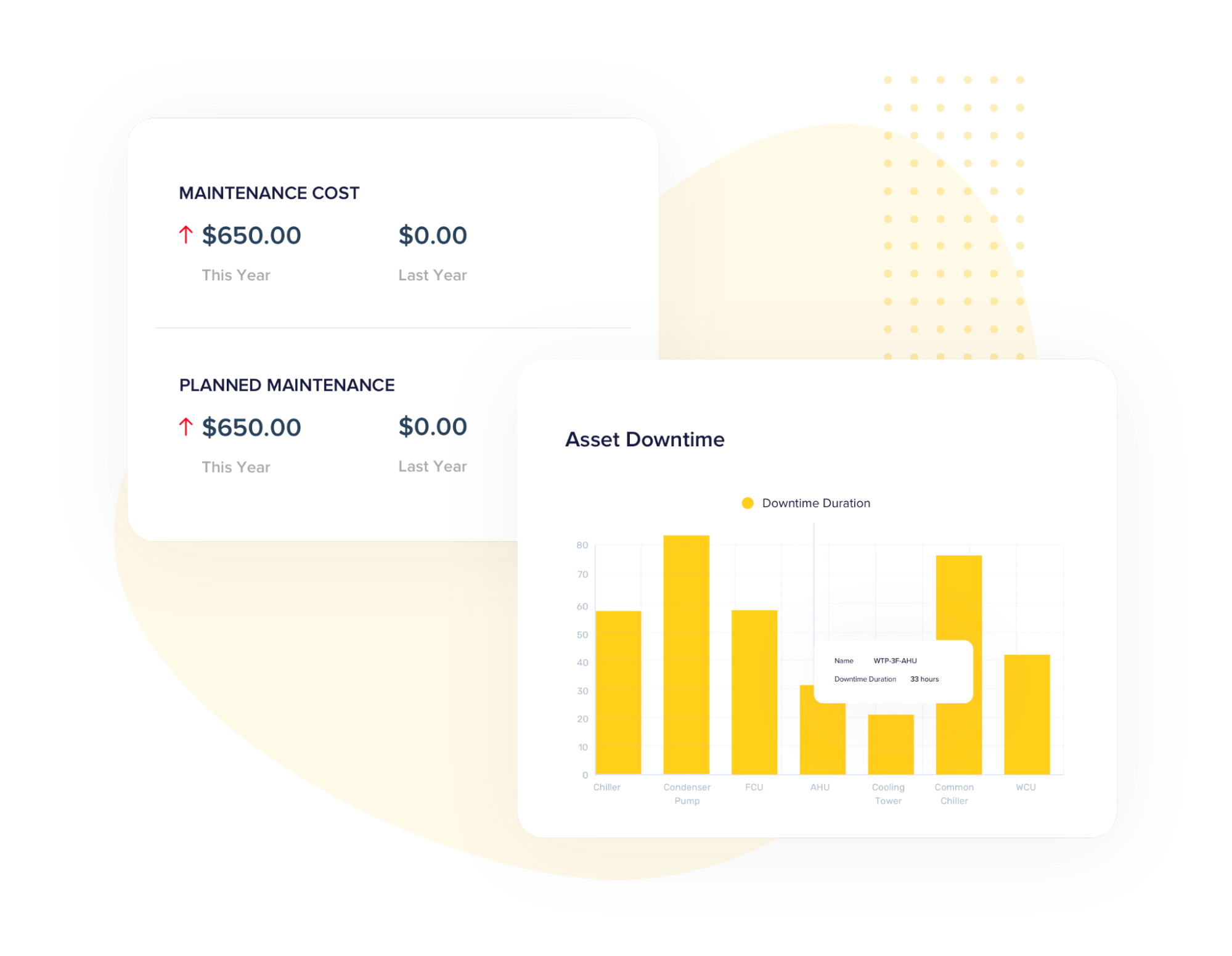
With detailed reports on maintenance metrics like mean time to repair and replace, mean time between failures, and lifecycle cost; users can easily identify inefficiencies in maintenance processes.
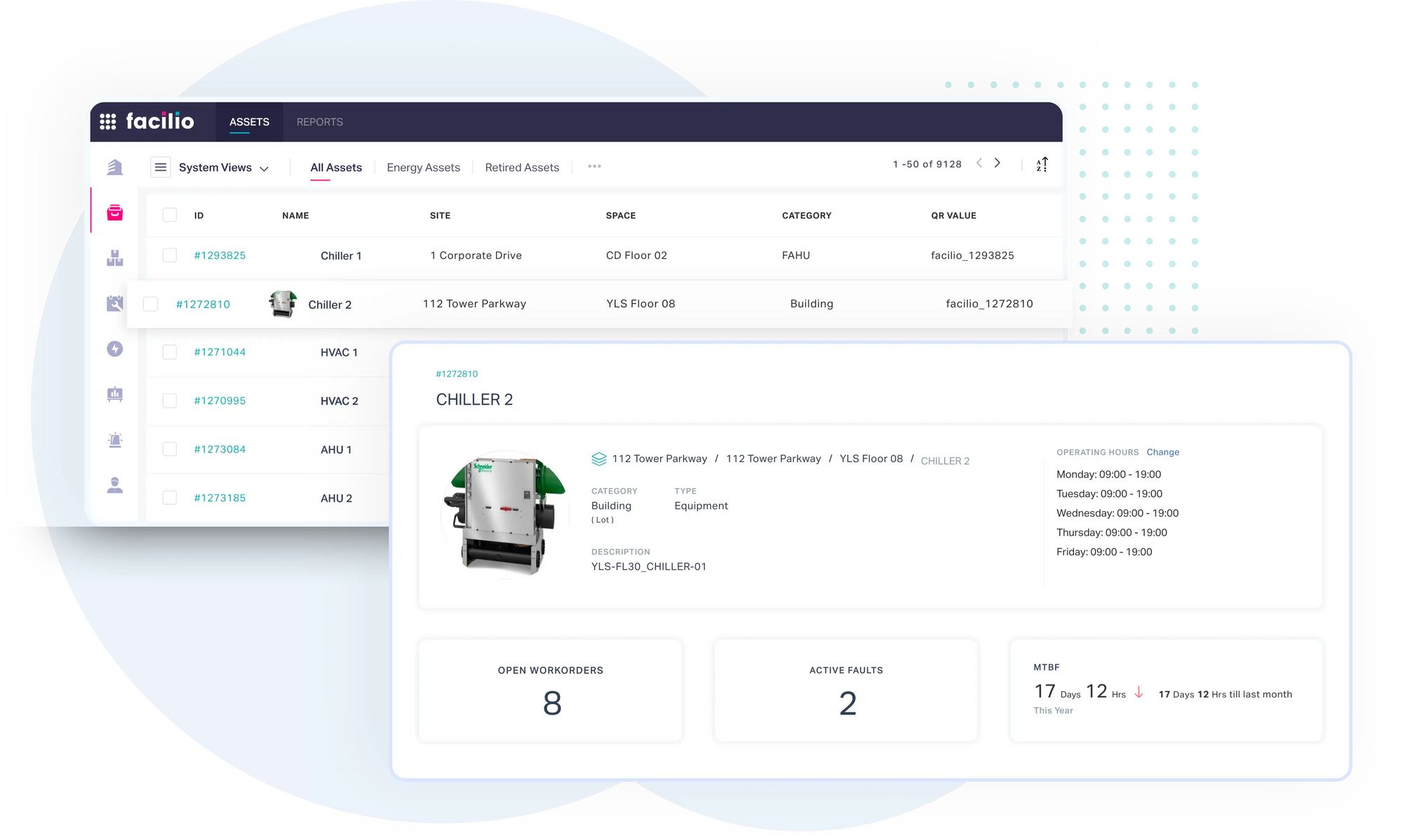
Additionally, the software provides complete visibility into asset performance history, enabling users to analyze health and performance metrics, minimize downtime by identifying deviations, and access all asset information in one centralized location.
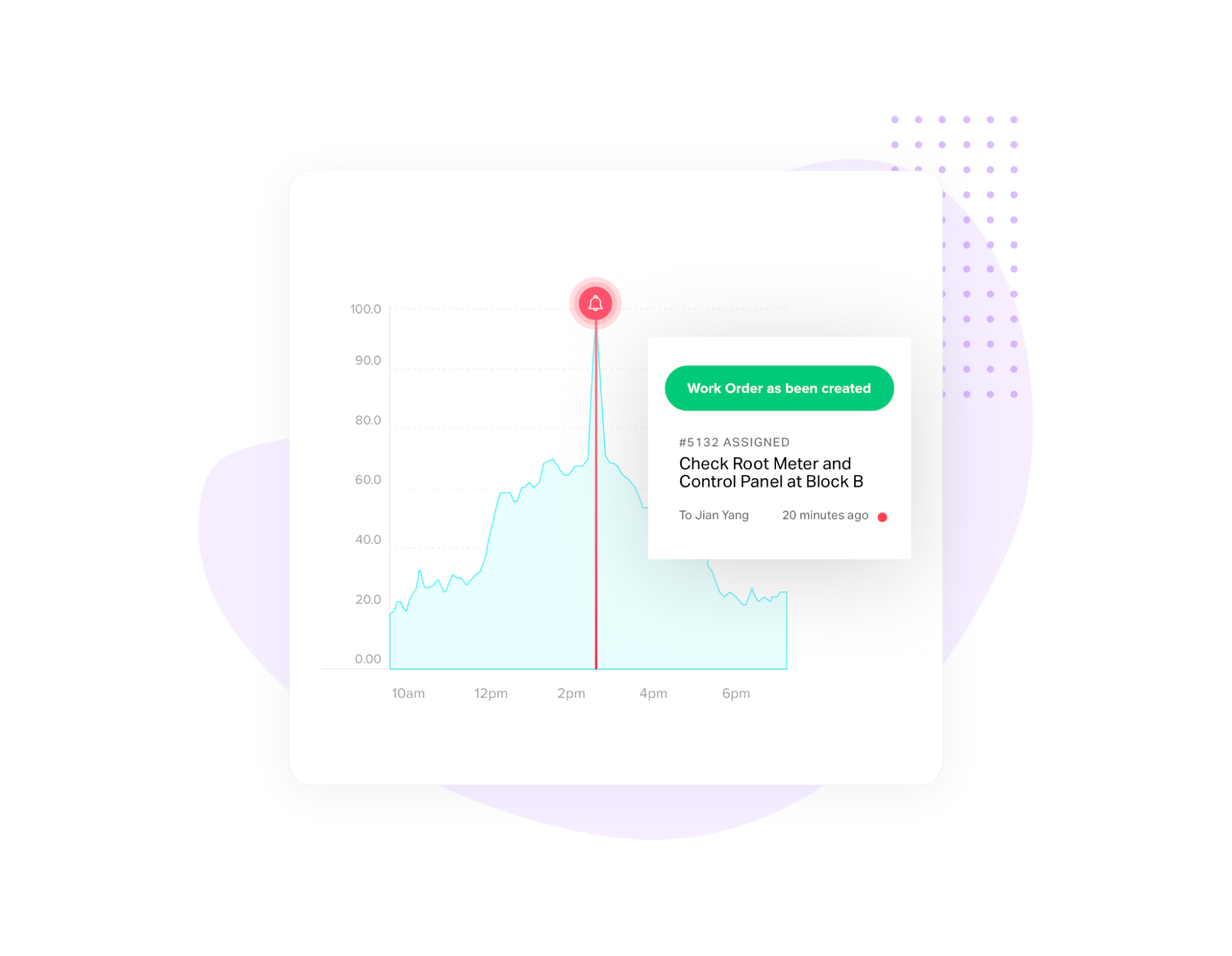
Facilio also helps mitigate risks by offering customizable audit and compliance work orders and automating approvals, task follow-ups, and workforce assignments. This streamlines processes ensures maximum efficiency, and reduces the risk of compliance violations and associated penalties.
Want to see Facilio in action? Get a personalized demo today!
Get a centralized cloud command center for all your assets
Book a demoFAQs
Q: How often should preventive maintenance be performed?
A: The frequency of preventive maintenance activities depends on factors such as equipment type, operating conditions, and manufacturer recommendations.
It is generally recommended to follow a structured maintenance schedule, conducting inspections and maintenance tasks at regular intervals based on equipment usage and criticality.
Q: What role does data analytics play in improving equipment reliability?
A: Data analytics plays a crucial role in improving equipment reliability by providing insights into equipment performance, identifying patterns and anomalies, and enabling proactive maintenance interventions.
Analyzing equipment data helps organizations make data-driven decisions, optimize maintenance strategies, and enhance overall operational efficiency.
Q: What is equipment reliability testing?
Equipment reliability testing is a systematic evaluation process that assesses the performance and dependability of equipment under various conditions.
It involves subjecting the equipment to rigorous tests to identify potential failures, weaknesses, and performance issues, ensuring optimal reliability and operational efficiency.
Q. What are the reliability factors of equipment?
The reliability factors of equipment refer to the various aspects that influence the dependability and performance of the equipment.
These factors include design quality, component quality, maintenance practices, operating conditions, environmental factors, and the overall lifecycle management of the equipment.
Organizations use these factors to enhance equipment reliability and minimize the risk of failures or breakdowns.