Featured Internet of Things
From Concept to Creation: Steps to Develop Digital Twins
A digital twin is a virtual replica of a physical asset or process that can monitor and optimize performance in real time.
By creating a digital twin, businesses can gain insight into the behavior of physical assets and processes without disrupting operations.
In this blog post, we'll explore:
- How digital twins work
- Different types of digital twins
- Real-world examples of how businesses are using digital twins
- Steps to develop a digital twin
- Resources you need to develop & implement digital twins, and
- Benefits and downsides you should know about
How does digital twin technology work?
Digital twin technology creates a digital replica of a physical asset or process using real-time data collected from sensors, IoT devices, and other data sources.
This real-time data is fed into digital twin software to simulate the behavior of the physical asset to optimize for a range of desired outcomes.
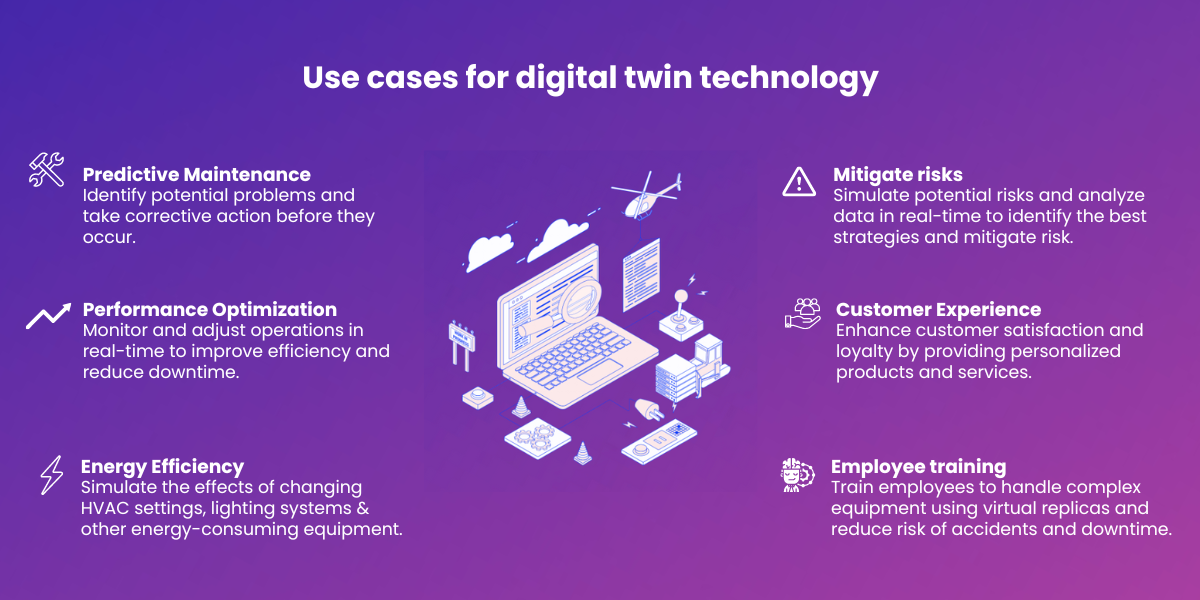
The virtual replica can then be used to monitor, simulate, and optimize the performance of the real-world asset, as well as to create predictive models and simulations to test different scenarios.
What is the Future of Digital Twins?
The digital twin industry is projected to grow from USD 6.9 billion in 2022 to reach USD 73.5 billion by 2027.
Advancements in IoT, AI, and cloud computing and lowering of the cost barrier are motivating businesses to adopt digital twin programs.
As digital twin technology continues to evolve, we will likely see it being used in new ways and across more industries, from transportation to construction.
Digital twins will likely become an integral part of smart cities and infrastructure, allowing for more efficient and sustainable management of public resources.
Types of Digital Twins
There are several types of digital twins, including:
- Product twins simulate individual products or components, providing a detailed digital replica of the product. They are often used in manufacturing and engineering to improve product design and performance.
- Process twins simulate entire systems or processes, such as manufacturing lines, supply chain operations, or energy grids. They provide a holistic view of the system, enabling organizations to optimize performance and identify potential issues.
- System twins simulate complex systems, such as aircraft or industrial machinery. They simulate the behavior of the entire system, including subsystems and components, providing a comprehensive view of the system's performance.
- Performance twins are used for monitoring and analyzing real-time data to identify patterns and trends in the behavior of a system or asset. They are used to optimize performance and predict potential issues before they occur.
- Physics-based twins use advanced modeling and simulation techniques to create highly accurate digital replicas of physical systems. These twins are often used in engineering and manufacturing to improve product design and performance.
- Business twins simulate the behavior of business processes and operations, providing insights into key metrics such as revenue, profit, and customer satisfaction. They can be very useful in identifying areas for improvement and optimize business performance.
Select the type that best fits your needs and objectives, and develop digital twins that provide valuable insights and improve decision-making processes.
Need some inspiration? Let's look at how different industries use digital twin technology.
Examples of Digital Twin Technology in Different Industries
Digital twin technology is being used in various industries, including:
- Manufacturing: Digital twins are used to optimize manufacturing processes and improve product design. BMW, Mercedes, and GM use digital twins to simulate the performance of their vehicles and identify potential issues before they occur.
- Energy and Utilities: Digital twins are used to optimize energy grids and improve energy efficiency. General Electric uses digital twins to simulate the performance of wind turbines and identify opportunities to improve performance and reduce maintenance costs.
- Healthcare: Digital twins are used to improve patient care and treatment. For example, the Cleveland Clinic uses digital twins to simulate the behavior of organs and tissues, enabling doctors to develop personalized treatment plans for patients.
- Aerospace and Defense: Digital twins are used for simulating the performance of aircraft and other complex systems. NASA uses digital twins to simulate the behavior of spacecraft and identify potential issues before they occur.
- Construction: The construction company BAM Nuttall uses digital twins to simulate and optimize the construction of complex infrastructure projects, such as bridges and tunnels.
- Retail: Digital twins are used to improve the customer experience and optimize store operations. For instance, Walmart uses digital twins to simulate the behavior of customers in their stores, enabling them to optimize store layouts and improve the customer experience. They can also be used to monitor inventory levels and optimize restocking processes, reducing waste and improving efficiency.
- Commercial real estate: Digital twins are used to optimize building operations and improve tenant satisfaction. For example, the commercial real estate company CBRE uses digital twins to monitor and analyze building performance data, identifying opportunities to reduce energy consumption and improve tenant comfort.
Digital twins can also be used to simulate and optimize building layouts and space utilization, enabling property owners to maximize the value of their assets.
Assets and spaces work in harmony with a cloud-supervisory platform
See Facilio in actionHow to develop digital twins?
According to a report by Gartner, by 2023, one-third of large organizations will have implemented digital twins, resulting in a 10% improvement in overall business process effectiveness.
Here are steps to creating and implementing digital twin technology in your facility:
- Acquire data: Collect data like temperature, pressure, vibration, and other relevant parameters from the physical asset or system using sensors, operational data, maintenance history, and other sources.
- Develop a digital twin: Integrate this data into a virtual model of the asset using a digital twin solution to reflect the physical asset's condition and performance accurately.
- Connect data sources: Set up real-time monitoring for the physical asset with a cloud-based platform like Facilio, which centralizes all asset data and helps identify potential issues and schedule required maintenance tasks.
- Test and validate: After the digital twin is connected to data sources, test and validate to ensure it accurately reflects the behavior of the real asset. Compare simulation results to actual performance data and make adjustments as needed.
- Simulation and optimization: Analyze data and develop optimization strategies based on desired outcomes, and run simulations. This can involve adjusting operational processes, scheduling maintenance activities, or making changes to the asset itself.
- Monitor and refine: The performance of the asset and the effectiveness of the optimization strategies must be monitored and refined over time. This can involve continuing to collect and analyze data and making adjustments to the digital twin and the optimization strategies as needed.
Requirements for a Digital Twin
Digital twins require several key requirements to ensure they accurately simulate real-world systems and assets.
Here are some of the most important requirements to consider:
- Accurate modeling: Accurately representing the real-world system or asset requires a deep understanding of the system's design, performance, and maintenance requirements.
Engineers may require specialized modeling simulation software like Siemens NX, ANSYS, or the like for modeling mechanical, electrical, and software systems. - Real-time data collection: You will need a reliable data collection infrastructure that can capture and transmit data in real-time.
Depending on the specific use case, different types of sensors may be required, such as temperature, pressure, or vibration sensors.
Data collection, transmission, analysis, and action can be facilitated by multiple point systems or a single cloud supervisory platform like Facilio. - Data processing and analysis: Once data is collected, it must be processed and analyzed to create an accurate simulation of the system or asset.
This requires robust data processing and analysis capabilities, including machine learning and artificial intelligence algorithms using a software platform like Facilio. - Visualization: The simulation generated by the digital twin requires effective visualization tools and techniques that can present complex data in an intuitive and accessible way.
Tools such as Tableau, Power BI, or MATLAB may be used for data visualization, allowing engineers and stakeholders to easily explore and interact with the simulation generated by the digital twin. - Interoperability: Digital twins require interoperability between different systems and data sources, allowing data to be seamlessly integrated into the simulation for accurate models.
This is best done with a vendor-agnostic platform like Facilio, which connects people, processes, and systems across the portfolio to centralize all O&M data and become the command center for all things O&M. - Scalability: Digital twins should be designed to be scalable, allowing them to handle increasing amounts of data and simulate larger systems and assets as needed.
A supervisory platform like Facilio allows infinite scalability and continuous optimization, enabling you to envision, implement, monitor, and optimize assets and operations–from one place.
Manage. Optimize. Control.
A centralized cloud command center for all your O&M needs.
Book a demo with FacilioBenefits of Digital Twins
There are several benefits of digital twins, including:
Improved asset performance
Businesses can test different scenarios in a virtual environment to identify the optimal parameters for the asset or process to boost operational efficiency, reduce costs, and improve asset performance.
For example, a manufacturing plant could use a digital twin to simulate different production scenarios and identify the optimal production schedule and inventory levels.
Reduced asset downtime
Integrating digital twins with a platform like Facilio enables predictive maintenance to improve asset uptime.
By continuously monitoring performance using sensor data and machine learning (ML) algorithms to identify patterns and anomalies in the data that can indicate impending failure or degradation, Facilio empowers O&M teams to schedule maintenance before the asset fails.
Additionally, by continuously monitoring the performance of the asset, businesses can identify areas where they can optimize the performance and reduce the need for routine maintenance.
Better decision-making
The differentiating factor between digital twins and traditional modeling & simulation methods is the use of real-time data, enabling the creation of dynamic and adaptive models that reflect the current state of the asset or system.
This way, decision-makers gain greater visibility into the asset performance and act on accurate and up-to-date information.
For instance, they can use the digital twin to simulate how a proposed change to an asset or system will impact performance and evaluate different scenarios to identify the best course of action.
In addition, by sharing a common virtual representation, decision-makers, engineers, and technicians collaborate more effectively to identify and resolve issues quickly.
Risk mitigation
Predictive algorithms and digital twins together can identify patterns and trends that may indicate areas of risk, such as potential equipment failures or safety hazards.
These potential failure modes can be used to create "what-if" scenarios and assess the associated risks, enabling decision-makers to prioritize risk mitigation efforts and allocate resources more effectively.
They can also be used to evaluate the effectiveness of risk mitigation strategies to help teams identify the most effective approach.
Next, digital twins can be used for training employees on operating assets without the need to practice on the physical asset, responding to different failure scenarios and emergencies to improve safety and reduce risks.
Downsides of Digital Twins
While digital twins can be incredibly useful, there are some potential drawbacks to consider.
- Cost: Developing and implementing digital twins can be expensive, especially if you're dealing with complex assets or systems, making it difficult for smaller organizations to take advantage of this technology.
- Data quality: Digital twins rely on accurate, high-quality data to be effective. If the data used to create the digital twin is inaccurate or incomplete, the simulation may not reflect the behavior of the physical asset or system accurately.
- Integrations: Integrating a digital twin with existing systems and sensors is challenging, particularly with older assets or systems. Ongoing maintenance and updates are necessary to keep the digital twin accurate and effective, which can be time-consuming and costly, especially for large or complex assets or systems.
- Security: Digital twins rely on real-time data from sensors and systems, which can be vulnerable to security risks such as data interception, data breaches, denial-of-service attacks, and system infiltration.
To mitigate these risks, organizations must implement strong cybersecurity measures, such as up-to-date systems and sensors, strong access controls, regular security assessments and audits, and a comprehensive incident response plan.
Interested but don't know where to start? We can help.
How Facilio lays the foundation for scalable digital twin programs
Facilio collects and normalizes data from multiple systems and streams to enable intelligent analysis in different contexts, becoming the data powerhouse for all your digital twin initiatives.
- Data integration: Facilio integrates data from various sources, such as sensors, building automation systems (BAS/BMS), and maintenance records, to create a comprehensive digital twin model.
- Real-time monitoring: It monitors real-time asset/equipment performance, providing alerts and notifications for issues. This can help identify potential problems before they occur and reduce downtime.
- Analytics and insights: It analyzes data from the digital twin model to provide insights and recommendations for optimizing operations and reducing costs. This can help improve energy efficiency, reduce maintenance costs, and improve tenant comfort.
- Collaboration and communication: It provides a centralized platform for collaboration and communication between different stakeholders–from facility managers and technicians to tenants. It streamlines workflows and improves communication, reducing response times and improving efficiency.
- Continuous improvement: Finally, it identifies areas for improvement based on data and analytics, enabling facility managers to optimize operations and improve the performance of their assets continuously.
Further, Facilio enables bi-directional communication with systems and equipment across portfolios to automate action based on real-time insights, enabling O&M teams to eliminate all manual, repetitive work and focus on optimizing performance and RoI from digital twin programs.
And yes, Facilio integrates seamlessly with the most popular digital twin technology providers.
Our product experts would love to walk you through Facilio's capabilities and how they can help you supercharge digital twin initiatives for quick and maximum returns on your investment!