When to Use Which Maintenance Strategy: A Decision-Maker's Guide
When it comes to maintenance planning, preventive maintenance is a popular choice for many companies, but it's not always the best option.
In fact, excessive preventive maintenance can actually be counterproductive, leading to unnecessary downtime and wasted resources.
Instead, decision-makers should consider a variety of factors, including the age of equipment, operating conditions, and production demands, before choosing a maintenance strategy.
What are the different types of maintenance strategies?
There are eight key types of maintenance strategies that organizations use to ensure that their equipment is running efficiently and effectively.
These include:
- Preventive maintenance: Regularly scheduled maintenance to prevent equipment failures
- Corrective maintenance: Repairing equipment after a failure has occurred
- Predictive maintenance: Using data analysis to predict when maintenance is needed
- Condition-based maintenance: Monitoring equipment to detect when maintenance is needed based on its current condition
- Planned maintenance: Scheduled maintenance performed based on time or usage intervals
- Proactive maintenance: Identifying and fixing potential issues before they cause equipment failures
- Risk-based maintenance: Prioritizing maintenance based on risk assessments of equipment failures
- Reliability-centered maintenance: Focusing on maintaining critical components to ensure overall system reliability
Maintenance is a crucial aspect of equipment management that involves various activities aimed at ensuring optimal equipment performance, reducing maintenance costs, and increasing productivity.
In this article, we'll dive into each strategy and understand its purpose and use cases, associated costs, benefits, technology, and more; to help you pick the right maintenance strategies for your organization.
Preventive maintenance
Preventive maintenance is a proactive approach to maintenance that involves conducting regular maintenance activities, such as cleaning, lubrication, and inspection. It is used for equipment that requires regular maintenance and has predictable failure patterns.
Example of preventive maintenance
Air filters play a critical role in maintaining indoor air quality and system performance in HVAC systems. However, over time, these filters can become clogged with dust, debris, and other contaminants, which can restrict air flow, reduce efficiency, and increase energy consumption.
This ultimately costs you more money in repairs, replacements, and the costs from unplanned breakdowns.
Regularly cleaning or replacing the air filters keeps the system running smoothly and avoids these issues. It's a simple and effective way to prevent problems before they even start and help extend the lifecycles of HVAC systems.
MC/RV = (Annual Maintenance Costs ÷ Equipment Replacement Value) x 100%
Where,
- MC/RV is the maintenance cost as a percentage of the replacement value
- Annual Maintenance Costs are the total maintenance costs incurred over a year
- Equipment Replacement Value is the cost of replacing the equipment
If the cost of maintenance is too high compared to the cost of replacing the equipment, it may be more cost-effective to replace the equipment rather than continue maintaining it.
Cost considerations for preventive maintenance
The biggest cost in preventive maintenance could be the cost of labor, which can shoot very high if your maintenance schedules aren't optimized, and your technicians are performing unnecessary maintenance.
While this may increase your overall costs, it can help prevent major repairs and reduce energy consumption from machines that don't operate at peak performance.
Weigh the costs of labor, travel expenses, and any overhead associated with outsourcing versus the cost of investing in the necessary tools and personnel for in-house maintenance when deciding whether to own or outsource preventive maintenance.
Tips to run effective preventive maintenance programs
- Develop a maintenance schedule to ensure maintenance tasks are performed on time and consistently.
- Create an inspection checklist that outlines the tasks to be performed during each maintenance check to ensure consistency and completeness.
- Maintain maintenance records for all maintenance activities, including the date of service, the technician who performed the task, and any replacement parts used.
- Keep a close eye on inventory to ensure the availability of the necessary lubricants, oils, fluids, and replacement parts for your equipment.
Corrective maintenance
Corrective maintenance refers to fixing equipment or systems after they have already failed. Corrective maintenance is typically used when the failure of a system or equipment would not pose a significant risk to safety or production.
An example where corrective maintenance works perfectly
An example of when corrective maintenance might be used is if a light bulb burns out in an office building. There's no urgent need to fix it immediately, and the failure of the light bulb doesn't pose any significant risk to safety or productivity.
The maintenance team can wait until it's convenient to replace the bulb instead of scheduling regular inspections or preventive maintenance to replace all bulbs before they burn out.
You can check how efficiently your corrective maintenance program is working by regularly tracking maintenance metrics like Mean Time Between Failures (MTBF) or Mean Time To Repair (MTTR).
Cost considerations for corrective maintenance
Corrective maintenance can be more cost-effective than preventive maintenance since it only requires repair work when something goes wrong, rather than investing in regular inspections and maintenance.
However, corrective maintenance can also result in unplanned downtime and lost productivity, which can be costly for businesses.
Relying solely on corrective maintenance can be risky for several reasons.
- First, equipment failure can occur unexpectedly, leading to unexpected downtime and loss of productivity.
- Second, major repairs or component replacements can be more costly than regular maintenance.
- Third, corrective maintenance can lead to a reactive approach to maintenance rather than a proactive one, which can result in a cycle of frequent breakdowns and repairs.
It is important to balance corrective maintenance with other maintenance strategies, such as preventive and predictive maintenance, to ensure the equipment operates reliably and efficiently.
Predictive maintenance
Predictive maintenance (PdM) relies on the collection of data from various sensors installed on the equipment, such as vibration sensors, temperature sensors, and acoustic sensors, among others.
The data collected is then analyzed using machine learning algorithms, which use historical data to identify patterns and detect anomalies that indicate a fault is likely to occur.
Example of predictive maintenance in action
Consider a large grocer that relies on refrigeration units to keep products fresh and safe for customers. But what happens when one of these units breaks down?
Not only does it impact the quality of his food products, but can also result in lost sales and a negative customer experience.
By installing temperature sensors in refrigeration units and using machine learning algorithms to analyze the data, you can predict when a unit is likely to fail before it actually does.
For example, if the temperature in a refrigeration unit starts to rise above a certain threshold, it could indicate that the unit is experiencing issues like a refrigerant leak or a faulty compressor.
With predictive maintenance, you can identify these issues early and take action before it impacts your customers and your bottom line.
Cost considerations for predictive maintenance
To implement predictive maintenance, organizations need to invest in the necessary IoT sensors and data analytics tools, as well as skilled personnel to carry out the analysis and maintenance tasks.
You may also need to upgrade your existing BMS/BAS or the painful processes of multiple integrations to access data trapped in vendor data lock-ins, which also comes with significant costs.
The long-term benefits, however, far outweigh the initial costs, which can be further offset with modern, connected CMMS like Facilio, which integrates seamlessly with your existing building systems and software to enable remote operations for multiple sites.
Benefits of PdM
- Facilitates condition-based maintenance (CBM) to optimize maintenance schedules based on the actual operating conditions of the equipment
- Supports the use of machine learning (ML) and artificial intelligence (AI) algorithms to analyze data in real-time and predict equipment failure with greater accuracy
- Provides insights into the root causes of equipment failures, which can help inform design improvements and reduce the likelihood of similar failures in the future
- Facilitates remote monitoring and control of equipment, reducing the need for on-site maintenance and enabling centralized management of assets across multiple locations
- Improves supply chain management by ensuring that critical equipment and components are available when needed, reducing the risk of delays and disruptions
The ability to gather real-time data from equipment across your portfolio and the freedom to analyze it in various contexts opens up opportunities for many optimization measures to achieve operational excellence.
And the platform to enable it - Facilio's Connected CMMS.
As Facilio effortlessly takes over routine tasks and automates not just notifications but also actions like alarm triaging, work order dispatch, or automated resolutions, you also save money on unnecessary maintenance and labor costs.
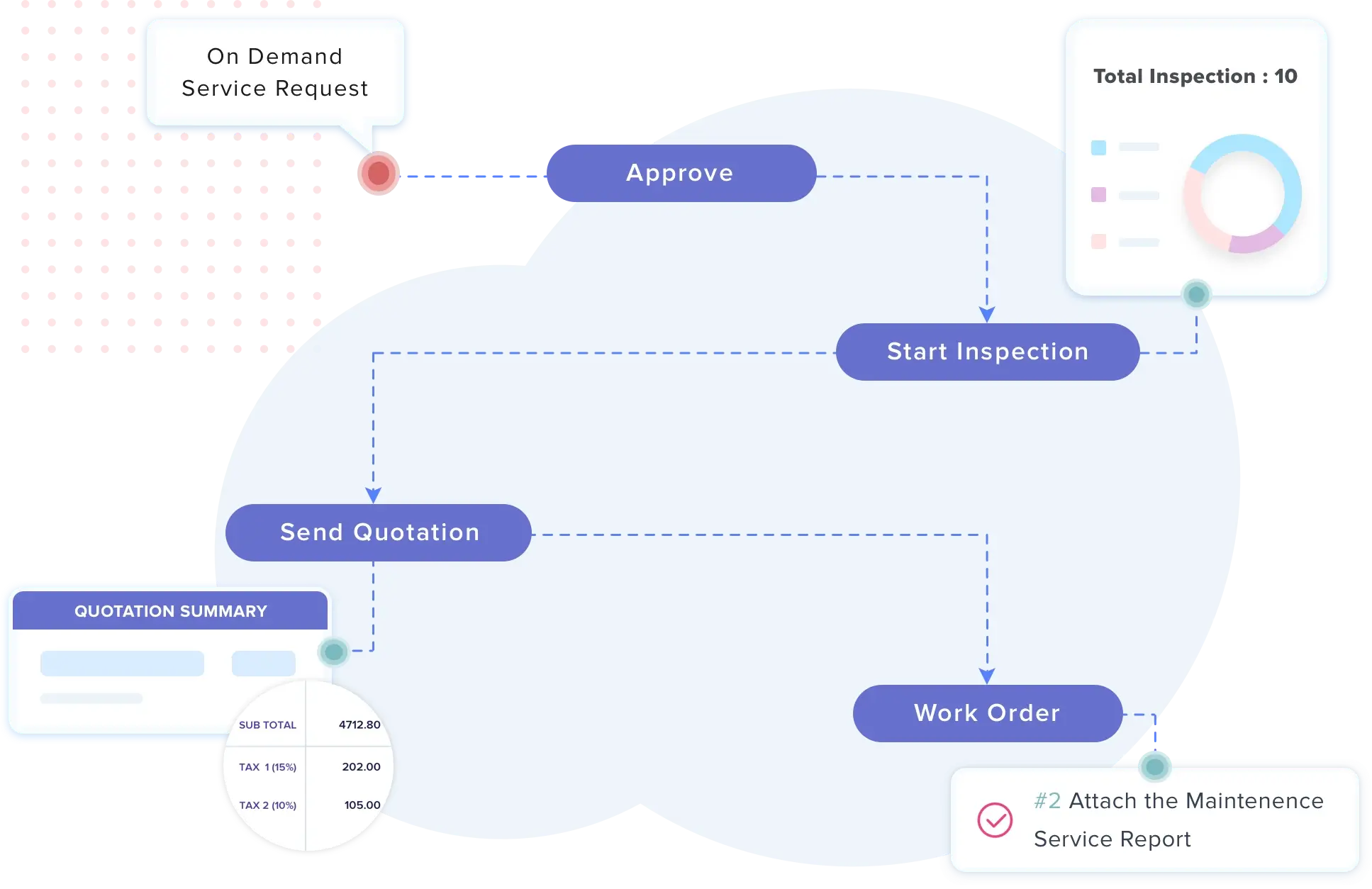
Make the switch from preventive to proactive
Gain flexibility and automation to unlock the best cost and productivity outcomes for all your unique O&M needs.
Condition-based maintenance
Condition-based maintenance, also known as CBM, is an advanced maintenance strategy that relies on real-time data to determine when maintenance should be performed.
CBM uses a variety of technologies, such as sensors and monitoring equipment, to measure and track the condition of equipment in real time.
This way, maintenance is performed only when necessary, reducing downtime and unnecessary maintenance costs.
Example of how condition-based maintenance works
Consider an industrial plant that uses large pumps to move fluids through a network of pipes. These pumps are critical to the plant's operation, and any unexpected downtime can result in costly production losses.
With CBM, the plant can continuously monitor the health of the pumps by collecting data on parameters such as temperature, vibration, and flow rate.
This data is analyzed in real-time by machine learning algorithms to detect any abnormal patterns that may indicate a potential failure.
For instance, if the vibration level of a pump is consistently increasing over time, it could be a sign of impending bearing failure. Then, a CMMS can trigger a work order to schedule a bearing replacement before the pump fails unexpectedly, avoiding costly downtime and repairs.
Condition-based maintenance is commonly applied to a wide range of equipment, such as electric motors, pumps, compressors, turbines, HVAC systems, conveyor systems, bearings, gearboxes, diesel engines, hydraulic systems, gas turbines, generators, transformers, batteries, valves, switchgear, boilers, heat exchangers, fans, blowers, chillers, and more.
Cost considerations for condition-based maintenance
With CBM, maintenance is carried out only when needed based on the actual condition of the equipment rather than according to a predetermined schedule.
As a result, the costs associated with unnecessary maintenance activities, such as labor, parts, and downtime, are minimized.
CBM also reduces the likelihood of unexpected failures, which can lead to additional costs such as emergency repairs, loss of production, and damage to other equipment.
IIoT sensors, cloud-based platforms, and other technologies automate the monitoring process and reduce the need for manual inspections, further reducing costs.
- Increased equipment availability and reduced downtime
- Extended equipment lifespan and improved reliability
- Reduced maintenance costs through targeted and efficient maintenance
- Enhanced environmental sustainability through reduced waste and energy consumption
- Improved data collection and analysis for better decision-making
CBM provides a more accurate assessment of equipment condition, allowing for more informed decision-making regarding repair, replacement, or upgrades and enabling you to make significant performance improvements without the need for massive and upfront capital investments.
Planned maintenance
Planned maintenance, also known as scheduled maintenance, involves scheduling maintenance activities at predetermined intervals based on the manufacturer's recommendations, equipment specifications, or industry best practices.
It's a proactive approach to maintenance that helps avoid unexpected downtime and prolongs the life of the equipment.
But how and when should you use planned maintenance?
Example of planned maintenance for a conveyor belt
Imagine a large manufacturing plant that relies on a conveyor belt to move products from one end of the factory to the other. This conveyor belt is critical to the plant's operations, and any downtime would be catastrophic.
To keep the conveyor belt running smoothly, the plant manager implements a planned maintenance program.
First, the maintenance team creates a maintenance plan for the conveyor belt. They identify all the components that need to be inspected and serviced, such as the motors, bearings, and belts.
They also establish a schedule for these tasks, such as performing a full inspection every six months and replacing the belts every two years.
Next, the team conducts regular inspections and maintenance tasks according to the maintenance plan. During these inspections, they check for signs of wear and tear, such as cracks in the belts or loose bearings. They also perform routine maintenance tasks, such as lubricating the motors and tightening bolts.
By following this planned maintenance program, the plant manager ensures that the conveyor belt stays in good working order and avoids costly breakdowns.
Planned maintenance is based on the assumption that equipment will require maintenance at regular intervals, regardless of its actual condition.
Here, maintenance is based on a time-based schedule, which involves performing maintenance tasks at specific intervals, such as every six months or every 10,000 hours of operation.
Proactive maintenance goes beyond simply following a maintenance schedule and involves actively monitoring equipment performance, identifying potential issues before they become problems, and taking corrective action as needed.
Proactive maintenance may involve the use of condition monitoring tools, such as vibration analysis or thermal imaging, to detect early signs of equipment wear or failure.
Preventive maintenance is similar to planned maintenance in that it involves scheduled maintenance activities designed to prevent equipment failure.
However, preventive maintenance is typically based on a set of predefined tasks, such as lubrication, filter changes, or inspections, rather than on specific time intervals.
The goal of preventive maintenance is to identify and address potential equipment issues before they lead to failure.
Proactive maintenance
Imagine being able to predict when a machine will fail and schedule maintenance during a planned shutdown rather than scrambling to fix it during an emergency shutdown.
That's the power of proactive maintenance. It's a way to stay ahead of the game and keep your equipment running at peak performance.
Example of proactive maintenance
For instance, if a chiller is being maintained proactive, the maintenance team may schedule a monthly inspection of the chiller's evaporator and condenser coils to check for any signs of wear or damage.
They may also monitor the chiller's performance parameters, such as refrigerant levels, compressor suction and discharge pressure, and motor current draw on a regular basis to detect any deviations from the normal operating range.
If any issues are identified during the inspections or monitoring, the maintenance team can proactively address them before they cause a breakdown or failure.
For instance, if the monitoring system indicates that the refrigerant levels are dropping, the maintenance team may schedule a refrigerant recharge or inspect the coils for leaks.
Data on the chiller's performance and condition over time helps facility managers and maintenance teams develop a more comprehensive understanding of its health and predict when components are likely to fail.
This data can then be used to create a more targeted maintenance schedule and avoid unnecessary maintenance activities.
Risk-based maintenance
In risk-based maintenance, maintenance decisions are based on the likelihood and consequence of equipment failure.
For example, equipment that is critical to the production process or poses a safety risk would be given a higher priority for maintenance than equipment that has a lower impact on production or safety.
To implement risk-based maintenance, a risk assessment is typically conducted to identify the equipment, the risks associated with failure, and the potential consequences of failure.
This assessment can take into account a variety of factors, such as the age of the equipment, the operating conditions, the level of usage, and the availability of replacement parts.
Based on the results of the risk assessment, preventative, predictive, or corrective maintenance activities are then prioritized based on the level of risk associated with each piece of equipment.
Example of risk-based maintenance
Imagine you own a fleet of airplanes that are used for commercial flights. As the owner, you want to ensure that each plane is maintained to the highest standards to minimize the risk of any malfunctions or accidents during flights.
This is where risk-based maintenance comes in. For example, the engine is a critical component that, if it fails, could cause the plane to crash. Therefore, you may decide to implement more frequent inspections and maintenance on the engines compared to other parts of the plane.
To put this into practice, let's say one of your airplanes has experienced multiple instances of hydraulic system failures during flights.
By conducting a risk assessment, you identify that the hydraulic system is a critical component that requires closer monitoring and maintenance to avoid potential safety issues.
With this information, you can schedule more frequent inspections and maintenance on the hydraulic system to reduce the risk of future failures.
- RBM focuses maintenance efforts on high-risk assets, ensuring that they receive the attention they need to operate reliably and efficiently.
- By identifying high-risk assets and focusing maintenance activities on them, RBM can help to reduce the risk of accidents and injuries in the workplace.
- RBM helps organizations to understand their assets and how they perform over time, leading to more effective asset management, as well as improved decision-making around equipment replacement and capital expenditure.
- It also helps organizations to meet equipment maintenance and safety requirements and demonstrate compliance to regulators.
Reliability-centered maintenance
Reliability Centered Maintenance (RCM) is a comprehensive maintenance strategy that identifies potential failures and addresses them before they occur.
It uses a systematic approach to prioritize maintenance tasks based on their impact on safety, environment, and cost.
RCM is typically used for complex and critical equipment in industries such as aviation, manufacturing, and power generation.
An example of RCM in action
RCM can be used to identify the most critical equipment and develop maintenance strategies that ensure maximum equipment reliability while minimizing maintenance costs.
For example, RCM can be applied to gas turbines in power generation industry by identifying the failure modes of critical components such as the combustion chamber, compressor, and turbine blades.
- Develop maintenance tasks that can detect or prevent each failure mode. For example, vibration analysis can detect potential failures in the turbine blades, while regular cleaning can prevent the build-up of debris in the compressor.
- Prioritize the maintenance tasks based on their criticality and cost-effectiveness. This ensures that the most critical tasks are performed first and that the maintenance program is optimized for cost and efficiency.
This way, you can develop a maintenance strategy that maximizes the reliability and availability of the gas turbine while minimizing maintenance costs to deliver a more efficient and profitable power generation operation.
How to choose the right maintenance strategy?
The answer lies in understanding your assets, your organization's goals, and your budget.
What do you want to achieve through maintenance?
- Are you looking to reduce downtime?
- Improve reliability?
- Minimize repair costs?
Defining your maintenance goals and narrowing down your options to choose a strategy that aligns with your objectives.
The selection process begins by evaluating the potential risks of equipment failure and the impact it may have on the business.
If the cost of repairing the equipment after failure is lower than the loss of production and revenue, then reactive maintenance may be a suitable option. However, if the loss from equipment failure exceeds the cost of maintenance, then a proactive strategy may be a better choice.
In some cases, a combination of maintenance strategies may be necessary, depending on the nature of the equipment and operations. Reactive maintenance can be useful for equipment that is approaching the end of its lifecycle or still under warranty.
Efficiency in maintenance management processes requires regular inspection, updates, and tracking outcomes for continuous improvement, irrespective of the methods you use. A flexible and modern CMMS like Facilio can help you plan, execute, automate, and optimize your maintenance operations at a scale.
Supercharge your maintenance management with Facilio's Connected CMMS
Connected CMMS is a reimagined approach to property operations and maintenance that meaningfully connects your systems, people, and processes.
It goes beyond work orders and maintenance to automate processes, enable stakeholder engagement, and drive connected efficiency — all in one place.
Investa, one of Australia's most recognized commercial real estate companies, had a tech stack that was unable to manage O&M and concierge services at scale.
To overcome these challenges and set themselves up for an accelerated journey toward their goals, Investa needed a unified solution that can consolidate silos across multiple systems from over ten years of operations.
Long story short, here's what Investa's operations looked like before and after Facilio:
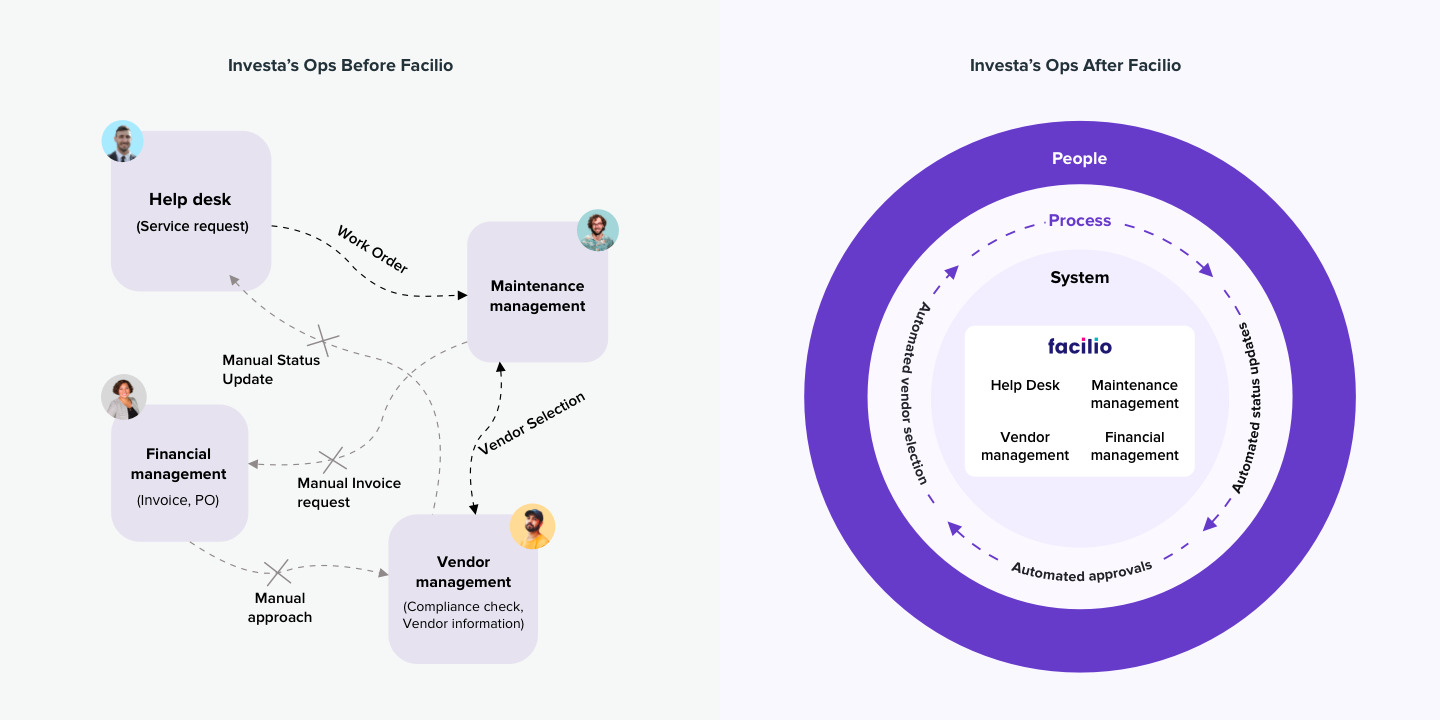
Neat, right?
The General Manager of Facilities Services at Investa, a few weeks after implementing Facilio, said
“One, it ensures that planned maintenance is tracked, including timelines, completion ratios, benchmarking building vs. building, vendor vs. vendor, state vs. state etc. This streamlines recordkeeping.
With Facilio, we no longer need to scour through emails/hardcopy etc., to find service records. Now, vendors add them to the work orders itself. It also ensures accurate payment tracking.
Two, it helps perform accurate maintenance forecasts. We have clear visibility into the near-term and long-term future. As a result, we can perform predictive maintenance to avoid downtime.”
Read the full case study, or see how Facilio can help you future-proof your facilities and achieve operational excellence.