Building Operations & Maintenance
10 Proven Ways to Prevent Inventory Mismanagement for Facilities Managers
You’re constantly battling inventory issues. Technicians waste valuable time searching for the right parts. Projects get delayed. Clients become increasingly frustrated.
Profits start to vanish, and growth stalls. This nightmare scenario illustrates the critical importance of effective part inventory management practices.
Inventory mismanagement can stem from several root causes, including lack of visibility into inventory levels, inaccurate forecasting, inefficient processes for ordering and storing parts, poor communication between stakeholders, and inadequate training for technicians.
The good news?
Implementing advanced inventory management systems can reduce these costs by up to 20%, according to a 2023 study.
In this blog post, we will explore actionable strategies to optimize your inventory management platforms, reduce waste, and maximize ROI.
We'll also delve into how leveraging tools like Facilio's inventory management module can transform your practices and drive success.
The high cost of inventory mismanagement
Inventory mismanagement is a silent profit killer for businesses of all sizes, especially small businesses. It creeps into your operations, causing inefficiencies, and hidden costs.
Let’s break down how it impacts your bottom line.
Excess inventory
Every item sitting unused is money that could be better spent elsewhere. You’re paying for storage, insurance, and handling for items you might never use. Plus, there’s the risk of items becoming obsolete.
For example, you’ve stocked up on HVAC parts in storage locations, anticipating future needs, but months pass and those parts are still sitting there. The storage costs alone could have been invested in more pressing needs. And if the parts become outdated, that’s a total loss.
Excess inventory costs you. Holding costs can range from 20% to 30% of the inventory value per year. This includes storage space, insurance, and deterioration costs. Over time, these costs accumulate, draining your resources and impacting your financial health.
Stockouts
On the flip side, running out of stock is just as damaging. Stockouts lead to lost sales and urgent and expensive emergency orders. They disrupt service delivery, affecting your reputation and client satisfaction.
Consider a facility running out of critical cleaning supplies; you have to place an emergency order. Not only does this cost more, but it also disrupts your routine operations. The delay in getting the supplies means your facility isn’t as clean as it should be, and your clients notice.
Stockouts also cause inefficiencies. Workers waste time searching for alternatives or waiting for supplies. This downtime reduces productivity and increases labor costs. According to a study by the IHL Group, inventory distortion was projected to cost retailers $1.77 trillion in 2023. The impact of inventory turnover on customer satisfaction and loyalty can be even more significant.
Inaccurate data
Inaccurate data is a recipe for poor decision-making. You might overstock on unnecessary items or face critical supply shortages. Both scenarios translate to financial losses due to resource misallocation.
Imagine a scenario: Your system shows you have a healthy stock of air filters. A major client places a large order, but during fulfillment, your technicians discover the actual inventory is significantly lower.
This miscalculation forces you to scramble for replacements, potentially delaying the order, damaging client relationships, and incurring additional costs.
Inaccurate data can lead to missed opportunities. You can't accurately forecast demand, fulfill orders efficiently, negotiate better deals with suppliers, or optimize inventory levels. This inefficiency creates a ripple effect, impacting your entire operation and bottom line.
Challenges of inventory management in facilities
Facility managers grappling with large inventories face a constant battle. Inefficiencies and rising costs lurk around every corner if these challenges aren't addressed head-on.
Here's a breakdown of the key inventory management hurdles:
Diverse inventory needs
Facilities often deal with a wide range of inventory items, from maintenance supplies to office stationery and raw materials. Managing such diverse needs requires meticulous planning and organization.
Facility managers face a logistical nightmare: From critical HVAC filters to mundane office supplies, a vast array of inventory items demands meticulous planning and organization.
HVAC filters are mission-critical, ensuring clean air. But unlike printer cartridges, they don't have a predictable usage pattern. This creates a challenge in maintaining optimal stock levels for each category.
Real-time tracking
Without real-time tracking, inventory levels can quickly become outdated, leading to mismanagement.
Let’s say your system shows that you have enough air filters. However, several have been used, but the system hasn’t been updated in real time. This discrepancy can lead to stockout surprises, especially when you need those filters the most.
Demand variability
Predicting fluctuating demand and adjusting stock levels is crucial to avoid disruptions. Seasonal maintenance activities can spike demand for specific items.
Imagine a scenario: winter arrives, and demand for heating system parts skyrockets. Without proper forecasting, you face stockouts, potentially delaying critical maintenance and impacting building operations. This domino effect highlights the importance of anticipating demand variations.
Integration and visibility
Another challenge is the integration of inventory management systems with other operational systems. Without seamless integration, common inventory management issues, visibility into inventory levels across different departments and locations can be fragmented.
Maintenance teams rely on one system to track spare parts, while procurement uses another entirely. This siloed approach can lead to inaccurate data and inefficiencies. A crucial part might be listed as "in stock" in one system while the other reports a shortage, leading to last-minute scrambling and potential delays in maintenance.
How data-driven inventory control can optimize inventory levels
To combat the challenges of inventory management, data-driven inventory control is a life saver.
Implementing real-time tracking of complex supply chains, demand forecasting, manual inventory tracking, and automated reordering can optimize inventory levels and cut costs. Here's how you can achieve this.
Real-time tracking
Real-time tracking ensures your data is always current, allowing for accurate monitoring of stock levels and preventing costly overstocking and stockouts.
RFID tags provide constant visibility into your exact inventory levels, empowering you to make informed decisions about restocking and maintain optimal stock levels.
Real-time tracking also improves accountability. Every movement of inventory is logged, reducing the risk of theft and loss. This transparency ensures that everyone on your team knows what’s available, reducing the time spent searching for items and improving overall efficiency.
Demand forecasting
Demand forecasting uses historical data to predict future inventory needs. This proactive approach helps in maintaining optimal stock levels.
By analyzing past usage patterns, you can predict future needs and avoid stockouts. For example, you might order extra air filters before the allergy season. This foresight ensures that you have the necessary items when demand spikes, without holding excessive stock.
Demand forecasting also allows for better budgeting. Knowing what you’ll need in the future helps you allocate resources more effectively. This reduces the financial strain of sudden large orders and spreads out expenditures more evenly.
Automated reordering
Automated reordering systems trigger purchase orders when stock reaches a predefined level. This ensures you never run out of essential items.
Automated reordering for cleaning supplies, for instance, ensures you always have enough stock without over-ordering. This helps you maintain optimal inventory levels and reduce costs.
The system tracks inventory levels and places orders automatically, freeing up your time for other critical business tasks.
Automated systems also help standardize ordering processes. Standardized processes minimize errors, ensuring accurate and timely orders. This translates to good relationships with suppliers and a happier team.
10 proven ways to prevent inventory mismanagement for facility managers
Facility managers face a unique set of challenges in managing inventory. Here are some best practices to prevent inventory mismanagement, ensuring smooth operations, reduced lead times, and cost efficiency:
Implement regular audits
Regular audits are crucial for maintaining accurate inventory records. They help identify discrepancies between recorded and actual stock levels, allowing you to address issues before they become major problems.
Tip: Schedule quarterly audits. Use a checklist and barcode scanners to streamline the process. This proactive approach helps catch and correct errors early, maintaining inventory accuracy.
Train your staff
Your staff plays a crucial role in the inventory management system. Proper training ensures everyone knows how to use the systems in place and follows best practices.
Tip: Conduct regular training sessions. Use online resources and in-person workshops to keep everyone up-to-date. Well-trained staff can significantly reduce errors and improve efficiency.
Predictive and condition-based maintenance
Predictive and condition-based maintenance leverages data and analytics to predict when maintenance should be performed. This proactive approach prevents unexpected failures and reduces maintenance costs.
Tip: Use predictive maintenance solutions like Facilio to monitor equipment health and predict failures based on historical data and real-time analytics. Implement condition-based maintenance to perform maintenance tasks only when necessary, based on the actual condition of the equipment.
Categorize your inventory
Organizing inventory into categories makes it easier to manage. It speeds up finding items and restocking. Use logical categories that make sense for your operation.
Tip: Group items by usage frequency or type. For instance, categorize cleaning supplies separately from office supplies. This makes retrieval faster and more efficient.
Establish reorder points
Setting reorder points ensures that you never run out of critical items. This involves determining the minimum stock level for each item and reordering before reaching that point.
Tip: Use inventory management software like Facilio to set and monitor automatic reorder points. This ensures timely reordering and prevents stockouts.
Maintain accurate records
Accurate record-keeping is vital for tracking inventory levels, understanding trends, and making informed decisions. Use digital records and update them regularly to reflect any changes in stock.
Tip: Regularly reconcile physical inventory with digital records. This practice helps maintain accuracy and ensures reliable data for decision-making.
Fault detection & diagnostics
Fault detection & diagnostics (FDD) is critical to prevent serious inventory mismanagement by identifying and addressing faults and inventory problems before they become major issues.
Tip: Implement FDD solutions like Facilio, to continuously monitor the performance of building systems. Use data-driven insights to predict potential failures and plan maintenance activities proactively. This reduces unplanned downtime and extends the lifespan of your equipment.
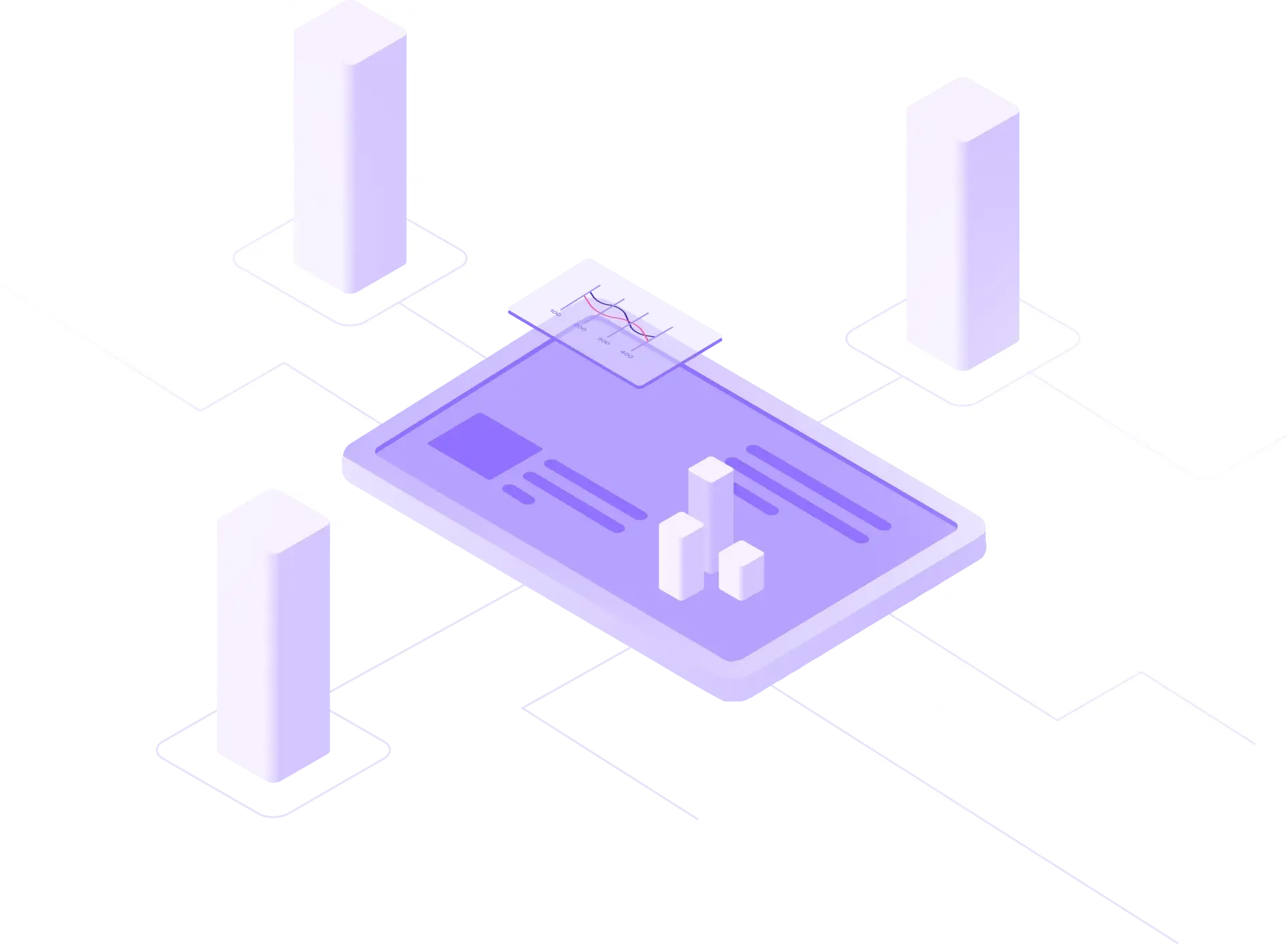
Optimize storage solutions
Efficient storage solutions can prevent stock damage, improve accessibility, and maximize warehouse space utilization. Consider using shelving, bins, and pallets to organize your inventory effectively.
Tip: Implement a clear labeling system and organize items logically. This improves retrieval times and reduces the risk of damage.
Conduct supplier performance reviews
Regularly review your suppliers' performance to ensure they meet your standards for quality, delivery times, and pricing. This critical aspect helps in maintaining a reliable supply chain.
Tip: Use a standardized evaluation form to assess supplier performance. Regular reviews help build strong relationships and ensure you receive quality supplies consistently.
10. Integrate with procurement systems
Integration of manufacturing processes with procurement systems streamlines the manufacturing and ordering process. It ensures that all orders are tracked and managed in one system, reducing the risk of errors.
Tip: Use integrated inventory management software like Facilio that connects with your procurement system. This seamless integration improves efficiency and reduces administrative workload.
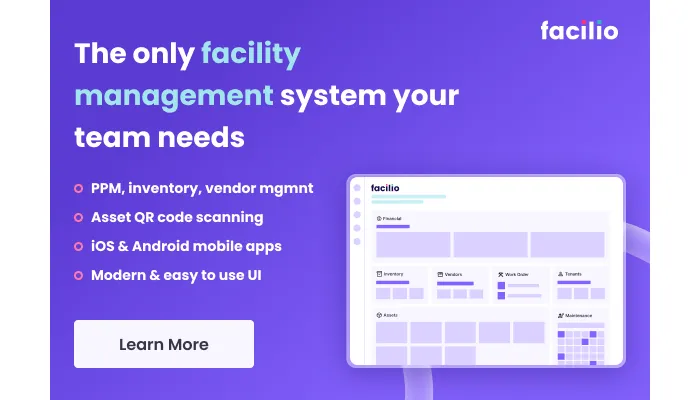
Streamline facility operations with Facilio's integrated inventory management
Facilio's integrated inventory management platform provides a robust suite of features to ensure optimal inventory levels and seamless warehouse operations. Here’s how:
- Facilio offers real-time tracking of inventory levels across all locations to ensure immediate visibility. It helps prevent both stockouts and overstock situations, maintaining optimal inventory levels at all times.
- With automated reordering, the system generates purchase orders automatically when stock levels fall below predefined thresholds. This reduces manual intervention, minimizes human error, and ensures continuous supply chain efficiency.
- Facilio integrates smoothly with procurement systems, facilitating better coordination with suppliers. This improves order accuracy, reduces lead times, and boosts overall procurement efficiency.
- Facilio provides strategic insights through comprehensive dashboards, which visualize patterns in parts usage and track inventory levels. This helps in making data-driven decisions to reduce overhead costs and improve operational efficiency.
You can also watch our webinar on tech-led FM growth to learn how to scale operations efficiently without compromising service quality.
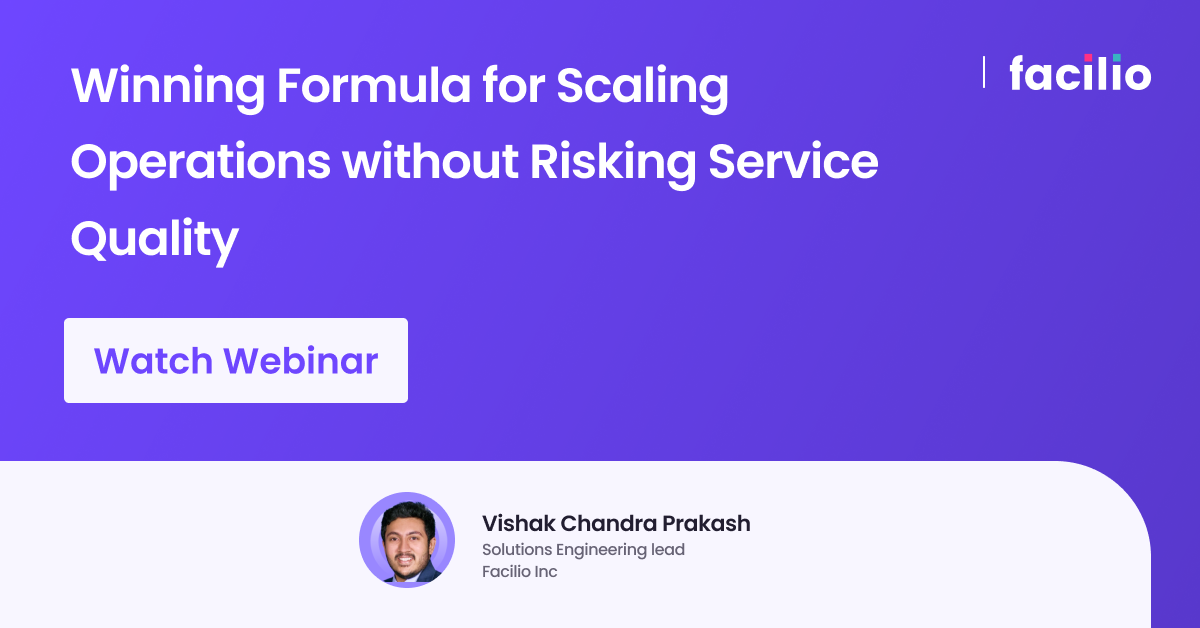
Boost operational efficiency with better facilities inventory management
Inventory woes plaguing your facility?
Stockouts, rising costs, and inefficient processes can cripple your operations.
Efficient and effective inventory management is crucial for facility managers and service providers
Facilio empowers you to take control of your inventory. Real-time data for informed decisions, automated reordering to keep things running smoothly, and seamless integration for streamlined efficiency.
The purpose-built, IoT-driven, and API-first enterprise software offers an easy-to-use solution to optimize your inventory management and boost your bottom line. Its strategic insights and reporting capabilities provide a clear picture of your company and inventory, helping you make data-driven decisions.
Explore Facilio's inventory management solution and see how it can transform your operations. Book a demo today!