Many facility managers still rely on reactive maintenance, which means fixing problems only after they occur. This approach can lead to costly repairs, downtime, and equipment failures.
A recent survey of facility managers found that 40% of their maintenance workload was still reactive. Facilities that rely heavily on reactive maintenance experience significantly more downtime, defects, lost sales, and inventory issues compared to those with a more proactive approach. They have to depend on reactive maintenance due to various challenges, such as resource constraints, lack of awareness or training in preventive practices, the complexities of older infrastructures and ingrained cultural factors that favor a reactive approach.
Clearly, reactive maintenance is inefficient and unsustainable in the long run. As building maintenance becomes more complex, facility managers must adopt cloud-based predictive solutions to anticipate and avert issues such as equipment failures, energy inefficiency, safety hazards, and operational disruptions before they escalate.
Moving beyond traditional methods, predictive solutions leverage insights from operational history, sensor data, maintenance and repair records, etc., to enable proactive interventions that optimize facility performance and reduce operational risks.
This blog post will explore how predictive analytics can transform facility maintenance and how Facilio’s connected CMMS can help you leverage predictive analytics in facility maintenance.
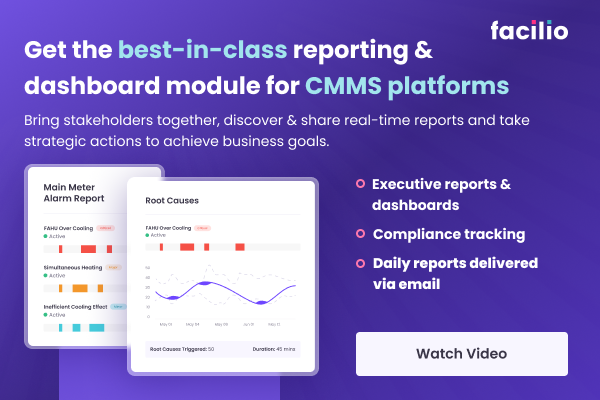
How a predictive approach outshines the reactive approach
Reactive maintenance means waiting for equipment to fail before taking any action to fix it. Often deemed as an uneconomical strategy, it has long been a crucial pain point for facility managers.
According to the Wall Street Journal, reactive maintenance leads to unplanned downtime, which costs industrial manufacturers an estimated $50 billion annually. Equipment failure is the cause of 42% of this unplanned downtime, which not only disrupts production but also results in excessive maintenance, repair, and equipment replacement costs.
Additionally, this short-sighted and risky approach can have severe consequences for the bottom line and the reputation of facility managers.
This is why facility managers are turning to approaches like predictive asset maintenance analytics. Here’s a comparison of predictive approaches vis-a-vis reactive measures:
Predictive analytics in facility maintenance: Why facility managers are turning to data-driven solutions
Predictive analytics transforms facility maintenance by leveraging data-driven insights to manage buildings and systems efficiently. This approach encompasses a wide range of aspects, including:
- Detailed asset monitoring: Continuous performance tracking of assets through sensors and IoT devices, offering real-time data crucial for predicting failures.
For example, sensors and analytics track the temperature, humidity, airflow, and energy consumption of HVAC (Heating, Ventilation, and Air Conditioning) equipment, detecting early signs of wear or malfunction. - Historical data analysis: Utilizing past maintenance records and operational data to identify patterns and trends for improved predictive accuracy.
- Customized maintenance plans: Creating tailored maintenance strategies for different equipment and systems based on specific needs and usage patterns.
- Enhanced safety protocols: Anticipating potential failures to improve safety measures for the workforce and facility users.
- Energy efficiency: Promoting optimal system operations for energy savings and sustainable practices.
Predictive analytics in facility maintenance can generate forecasts and alerts based on the data to help facility managers understand the following:
- When and where a failure or malfunction is most likely to occur
- What are the root causes and contributing factors of the problem
- What are the best preventive or corrective actions to take
- What are the expected impacts and outcomes of the actions
Applying predictive analysis: An overview of predictive maintenance
Predictive maintenance is one of the key applications of predictive analytics, and when combined with computerized maintenance management systems (CMMS), it becomes a robust tool for optimizing facility maintenance. This software provides facility managers with consolidated data about asset and maintenance KPIs to help streamline maintenance operations efficiently.
AI-driven facilities management solutions are radically disrupting the established status quo of property operations. Going beyond the capabilities of an ordinary maintenance system, it connects the dots across your operations, people, and systems, giving you a 360° view of your facilities. As a result, facility managers can effortlessly handle work orders, inspections, asset data, service requests, and more.
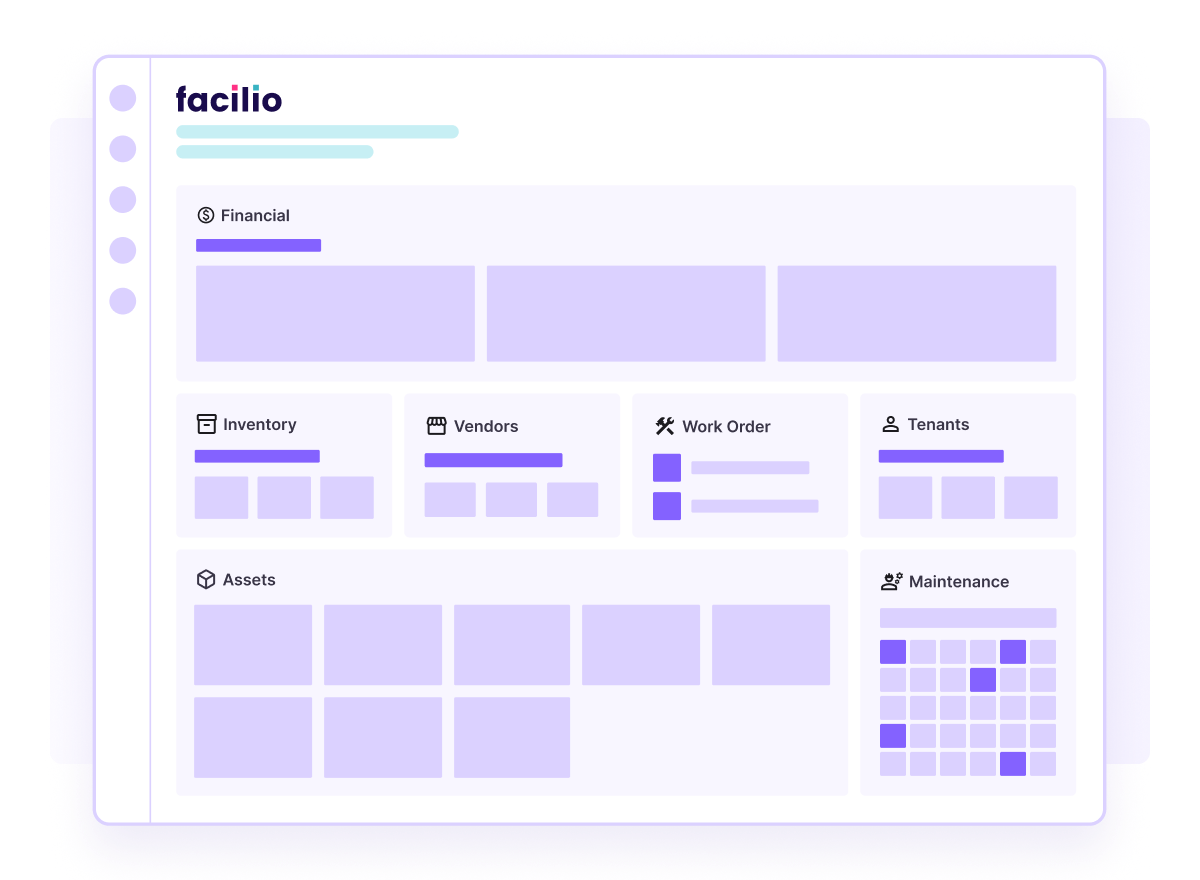
For example, the tool monitors elevator usage patterns and analyzes data from sensors embedded in the equipment. Therefore, facility managers can accurately anticipate issues and schedule maintenance during non-peak hours, reducing disruptions.
How Facilio's Connected CMMS enables the adoption of predictive maintenance
Here are the key features of Facilio CMMS that can benefit forward-thinking organizations:
- Asset management: CMMS provides a comprehensive view of building assets, aiding managers in efficient asset management with QR codes, lifecycle tracking, and easy access to vital data like purchase dates, maintenance schedules, and service vendors.
- Maintenance management: The tool also aids in cost prediction, maintenance scheduling, asset replenishment, and cost reduction. With all equipment centralized, it facilitates both planned and unplanned maintenance, historical data tracking, and task management.
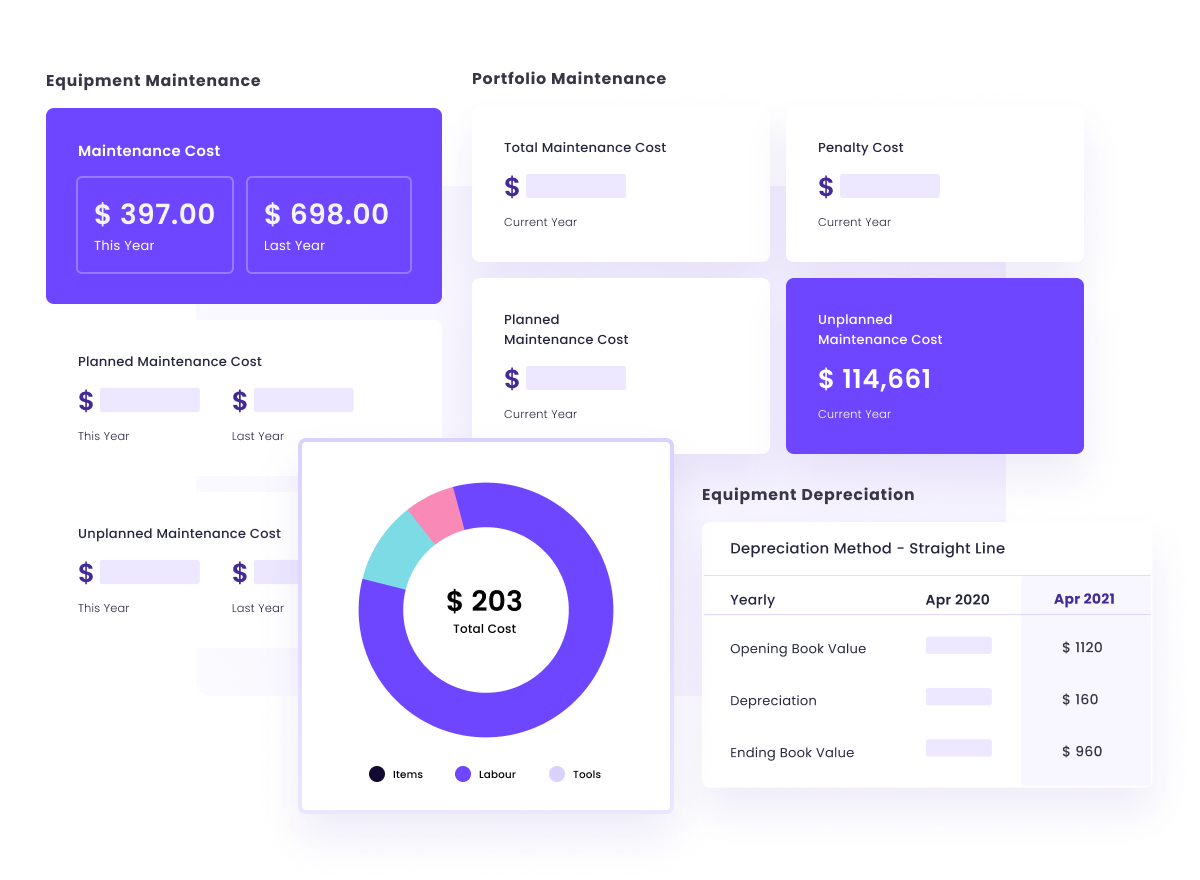
- Inventory management: CMMS solutions enable you to add maintenance items to your inventory, ensuring essential parts are readily available. Additionally, it offers understock alerts to prevent maintenance delays.
- Compliance: The tool aids in compliance with safety, health, and environmental regulations, guaranteeing building standards are met. It also facilitates the establishment and monitoring of service-level agreements (SLAs).
- Environmental impact: Aligned with the contemporary push for sustainable buildings, CMMS assists in complying with safety, health, and environmental impact reports, helping reduce carbon footprints.
- Zero data silos: The tools bridge the gap between different systems and stakeholders involved in a building, promoting information sharing and coordination across various devices.
- Knowledge base: CMMS also contains documentation, manuals, and notes about assets and inventories. Having a comprehensive knowledge base in CMMS simplifies training, streamlines processes, and facilitates quick access to information, enabling efficient operations and troubleshooting. It's a valuable resource for ensuring staff competence and smooth asset management.
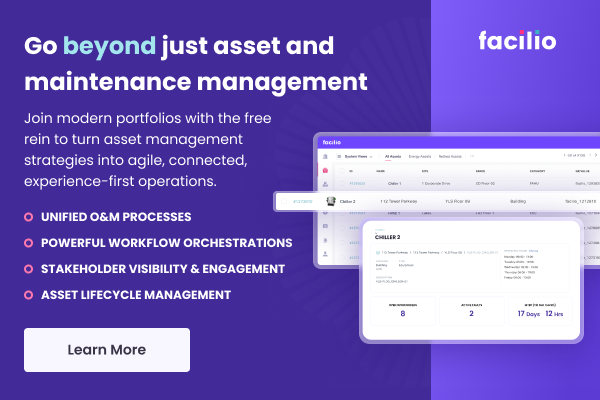
Benefits of predictive analytics: An overview
According to a Deloitte report, predictive maintenance can lead to a 5%-15% reduction in facility downtime, freeing up capacity and improving operational efficiency. Some of its major benefits include:
1. Reduces maintenance costs: Predictive analytics helps facility managers plan and schedule maintenance activities based on the actual needs and risks of their assets. This reduces excessive maintenance and prevents costly breakdowns and repairs.
2. Extends equipment lifespan: By intervening early, facility managers can detect signs of deterioration, wear and tear, and potential failures in the equipment. This enables appropriate corrective actions, which extends the lifetime of the equipment.
3. Improves operational efficiency: Predictive analytics eliminates inefficiencies and bottlenecks, ensuring smooth workflow and optimized resource allocation. This improves the productivity and quality of the facility operations.
For example, Predictive maintenance detects leaks, water pressure irregularities, or other plumbing and water systems issues. It also addresses potential plumbing problems before they lead to disruptions in water supply.
4. Enhances occupant comfort and safety: Predictive analytics ensure the optimal conditions and functionality of the facility environment, such as temperature, humidity, lighting, ventilation, and security. This can improve the comfort, well-being, and safety of the occupants.
5. Data-driven decision-making: Facilities can leverage predictive analytics to make more informed and strategic decisions. By leveraging real-time data, businesses can identify trends, anticipate future outcomes, and optimize strategies, leading to more accurate and effective decision-making processes.
While predictive analytics holds tremendous potential, its implementation can be challenging for facility managers. For example, you need to overcome key hurdles in data, technology, and organizational alignment. Therefore, to begin with, facility managers must assess their infrastructure, workflows, and data quality to ensure readiness. Internal capability building and stakeholder buy-in are also essential. The point is that you must approach predictive analytics with a clear understanding of the commitment it demands.
Challenges in implementing predictive analytics for facility maintenance
While there are many compelling benefits in using predictive analytics, implementing predictive analytics in facility maintenance can be challenging, as it requires:
- Data integration: One of the biggest hurdles is integrating fragmented data across facility systems into a unified structure. The data likely resides in siloed, legacy systems that don't easily integrate. Standardizing this data is extremely challenging.
Without consolidated data with portfolio-wide visibility, predictive analytics tools have limited value. So, the lack of interoperability across systems makes seamless data integration an uphill battle that facility managers must be prepared to take on. - Data analysis: Legacy systems often hinder facility managers from effectively analyzing and interpreting maintenance data. These outdated platforms lack advanced analytics capabilities like statistical modeling, artificial intelligence, and neural networks. This technology gap becomes the bottleneck rather than the manager's abilities.
To gain valuable insights from their data, facility managers require flexible systems like Facilio CMMS that seamlessly integrate advanced analytics.
- Evolving responsibilities: Modern facility management teams face the challenge of expanding their strategic responsibilities beyond cost reduction. As their responsibilities include managing vendors, tenants, and sustainability initiatives in addition to maintenance, they are confronted with multiple disjointed point solutions, leading to substandard performance.
- Insufficient CMMS features: Traditional CMMS systems have limited functionality focused only on assets, work orders and maintenance. They lack capabilities to support cross-functional communication, data integration, advanced analytics, and custom workflows.
- Insufficient sensor coverage: Much of the data required for effective predictive analytics comes from sensors installed on equipment and systems. Limited sensor coverage makes data collection incomplete. Expanding sensors can be costly without proper ROI analysis.
- Cybersecurity risks: With more reliance on networked software and connected devices, cyber risks grow. Ensure proper authentication, encryption, access controls, and other security measures are in place.
Step up from reactive to predictive maintenance with Facilio
Switching to predictive maintenance is a critical decision for facility managers, and when it comes to making that transition, Facilio’s Connected CMMS stands out as the all-in-one solution.
While traditional CMMS tools often fall short in addressing the complex needs of modern facility management, Facilio reimagines property operations and maintenance by meaningfully connecting systems, people, and processes.
In short, Facilio goes beyond piecemeal CMMS tools to provide an integrated environment for predictive maintenance at scale. Let us show you how:
Unified O&M data with Connected Systems
Integrating disjointed data is difficult with traditional systems. Facilio seamlessly brings together data from CMMS, BMS, sensors, work orders, equipment manuals, and more into a structured data lake using ETL and normalization. Both structured and unstructured data are made analysis-ready.
No code/Drag & drop data analytics dashboards/reports
Gone are the days of complex external data science platforms. Facilio allows building predictive models directly within the CMMS using interactive drag-and-drop tools. Choose from advanced analytics algorithms like machine learning, deep learning, statistical modeling, simulation, and more based on your use case. For all this, no coding is needed.
- Actionable insights from historic asset maintenance data
Analytics isn't just insights. It's about driving actions. Facilio maps model outputs like failure predictions, degradation alerts, and maintenance recommendations directly to work orders, preventive maintenance schedules, and mobile technician workflows.
2. Customizable dashboards for portfolio-wide visibility
Visualize model outputs like equipment health indicators, failure probability, and optimal maintenance windows through Facilio's library of customizable dashboards. Gain unprecedented visibility into the performance and maintenance needs of each asset.
3. Mobile access for every field technician
Workflows are streamlined by removing paper-based processes. Technicians can view predictive work orders, alerts, parts inventory, repair instructions, and equipment history on the fly through Facilio's mobile apps.
4. Standard onboarding processes for rapid adoption across portfolios
Predictive models built in Facilio are ready for immediate rollout across your real estate portfolio without months of custom coding. Settings can be configured portfolio-wide with just a few clicks. Moreover, new sites are onboarded instantly.
5. Continuous improvement as new data is generated
As assets operate over time, new data is incorporated back into models to improve accuracy through retraining. Optimization is ongoing and hands-free, ensuring maintenance strategies keep pace.
6. Interoperability with existing software systems
Facilio’s OpenAPI access enables easy integration with other enterprise systems like accounting, procurement, inventory management, and more that might be used in maintenance workflows.
How Facilio’s Connected CMMS predicts problems before they begin
Facilio’s connected CMMS enables facility managers to implement predictive analytics and achieve remarkable results. Let us explain this with a real-world example of Investa, a leading Australian real estate company that manages a portfolio of commercial office buildings nationwide.
Investa faced numerous challenges in managing its facilities due to its vendors relying on outdated and disconnected systems. To solve this, it needed a modern and integrated solution to improve its operations, efficiency, and performance across its portfolio.
Here’s how Facilio’s Connected CMMS helped Investa.
- Facilio integrated various functions across portfolios, such as asset management, incident handling, vendor relations, and maintenance workflows. It offered comprehensive visibility and control over Investa's entire portfolio operations.
- The connected CMMS enabled custom workflows and flexible implementation to suit Investa’s unique processes.
- The platform also streamlined vendor management and tracked vendor performance and feedback.
- Investa gained valuable portfolio-wide insights and analytics through the connected CMMS, empowering their executives with the data needed to make informed decisions
Futureproof your Asset and Maintenance Management with predictive analytics
To sum it up, adopting predictive analytics in facility maintenance with Facilio's Connected CMMS is like upgrading to a smart assistant for your buildings. This approach focuses on fixing issues at hand, understanding patterns with interoperable data, and preempting any risks, ensuring the efficiency and longevity of assets.
Notably, organizations that leverage Facilio's connected CMMS can achieve a 40% reduction in asset downtime, a 30% decrease in reactive maintenance calls, and an overall 15% cost savings across their building operations.
So, it is evident. For modern organizations, it's a strategic pivot from merely reacting to problems to proactively optimizing operations. With several successful projects to its credit, Facilio has proven its capability to transform facility management by providing comprehensive insights for smarter, data-driven decisions.
Ready to make your facilities intuitive?
Facilio's Connected CMMS could be your partner in achieving operational excellence that's sustainable and forward-thinking.