Asset Lifecycle Management: The Strategic Edge of CMMS Over EAM
Asset lifecycle management is all about managing assets through every stage of their existence—from the initial acquisition to the final phase of disposal or renewal. This comprehensive process encompasses various stages such as planning, acquisition, operation, maintenance, and eventual disposal.
Key takeaways
- Scale asset lifecycle management: Handles long-range maintenance planning or complex intraday scheduling, streamlining operations and reducing manual intervention.
- Control asset projects: Helps in planning, designing, and delivering complex asset operations and maintenance, ensuring projects stay on track and within budget.
- Optimize project operations and maintenance: Enhances overall operational efficiency by minimizing equipment failure, ensuring seamless contractor collaboration, and regaining lost production time.
- Align maintenance to operations: Factors in materials, resources, and duration, optimizing asset utilization, and reducing operational disruptions with accurate maintenance plans.
- Extended asset lifespan and increased efficiency: Focuses on proactive measures that prevent breakdowns, extending the functional life of assets, and optimizing resource allocation.
Let us consider an educational institution where every corner buzzes with efficiency, resources last longer, and every project is executed without a hitch. This vision will come to life through effective Asset Lifecycle Management (ALM), the backbone of optimizing campus assets.
By seamlessly integrating long-term maintenance planning with everyday operations, ALM minimizes manual oversight, ensuring a smooth educational environment. It also holds the reins on infrastructure projects, navigating complex endeavors like renovations with budget compliance, and precision.
Through boosting operational efficiency and aligning preventive maintenance with academic needs, asset lifecycle management not only minimizes disruptions but extracts maximum value from every asset, forefronting educational excellence while extending asset longevity and operational efficiency—a win-win for every school looking to enhance its learning environment.
Enterprise asset management vs. IT asset management
Though both EAM and ITAM aim to manage assets efficiently, they cater to different asset types and thus require distinct management strategies. Selecting the appropriate asset management system is crucial for addressing the unique demands of your organization.
Unpacking the phases of the asset lifecycle management process
The significance of each phase in the asset lifecycle management process can vary based on your organization's structure and priorities. Nevertheless, every stage is essential in maximizing the value derived from your assets, whether large or small, costly or budget-friendly. Let's delve into the four critical stages these assets undergo during their lifecycle.
1. Planning
The design engineering or planning stage is where asset requirements, specifications, and usage are determined based on the organization's needs. This phase often starts by identifying unmet needs within your facility, followed by brainstorming potential assets to enhance facilities management. It's crucial to explore multiple options before committing to a significant financial investment. When considering asset investment, think about factors such as:
- Scaling production
- Improving efficiency
- Replacing outdated equipment
- Ensuring environmental and safety compliance
You can utilize digital twins to optimize asset efficiency across the entire lifecycle and predict faults in advance. Also reviewing previous asset performance will help determine how new assets can operate at optimal operations.
2. Acquisition
The procurement or acquisition phase begins once asset needs are identified. It's vital to secure assets within the predetermined budget while reserving funds for installation, logistics, and sourcing spare parts. After installation, focus on defining asset ownership, inspection policies, and maintenance strategies. Key activities during this phase include:
- Asset purchasing and installation
- Preparing the facility for installation
- Preparing the asset for operation
- Planning preventive maintenance
- Training on asset use
- Integrating asset details into a CMMS
Establishing a centralized supply chain operation can help streamline inventory replenishment, cut costs, reduce risks, and enhance efficiency. Integrate with other enterprise systems for full visibility and faster issue resolution.
3. Operation and maintenance
This phase encompasses the actual usage of assets and their upkeep to maintain optimal performance. It involves asset repairs, upgrades, audits, and maintenance to prolong asset life while minimizing costly reactive maintenance. Key activities include:
- Spare parts inventory management
- Asset performance audits and repairs
- Asset tracking and condition monitoring
- Routine maintenance scheduling and execution
Don’t forget to implement real-time asset health monitoring using IoT sensors as they can provide technicians with valuable insights. Employ reliability-centered maintenance (RCM) to proactively manage resources and forecast maintenance needs.
Suggested read: How to perform Facilities Condition Assessment
4. Disposal
Once assets reach the end of their useful life, this phase involves removing, selling, repurposing, or recycling them efficiently. Consider asset disposal when maintenance costs exceed replacement costs, when the asset is no longer functional, or when adopting new technology for better efficiency. Activities during this phase include:
- Asset cost-benefit analysis
- Asset repair and replacement analysis
- Asset decommission planning
- Asset disposal procedures
Maintain comprehensive asset history to support data-driven retirement and disposal decisions. Evaluate organizational goals to ensure assets align and effectively serve customer needs.
Best practices for successful asset lifecycle management
To successfully navigate asset lifecycle management, it's essential to adhere to best practices designed to reduce maintenance costs, boost efficiency, and maintain productivity.
1. Structured asset inventory
Start by preparing a comprehensive asset inventory accompanied by a detailed system map. This provides a clear understanding of asset locations, types, and their interconnections within your enterprise. For companies operating across the UK and Middle East, this granular mapping can account for regional variations in infrastructure and regulations, ensuring tailored asset oversight.
2. Asset condition rating and evaluation
Implement an asset condition rating system to gauge the current status of assets. Use sophisticated tools like decay curves to estimate the remaining useful life. This method is ideal for industries such as transport and utilities, as it helps in planning precise maintenance schedules and replacements.
3. Financial and performance scope
It's crucial to find out asset values and associated replacement costs. Analyze customer demand along with satisfaction metrics to inform asset management strategies, ensuring they align with business objectives.
4. Set and communicate performance targets
Clearly set asset performance targets and communicate them with stakeholders. This aligns organizational efforts and ensures a shared vision of asset management goals. Create a hierarchy by listing assets based on their criticality to operations, focusing attention on assets that have the highest impact on productivity and security.
5. Failure analysis and proactive maintenance
Conduct thorough probability failure assessments using root cause and failure mode analyses. This allows you to anticipate potential failures proactively, crucial in the high-stakes environments of oil and gas extraction prevalent in the Middle East.
6. Regular policy updates
Review and update system vulnerability protocols frequently. Adopt predictive maintenance practices to ensure a forward-thinking approach to potential asset issues, fostering resilience against unexpected downtime.
7. Cost analysis for critical decisions
Evaluate the cost of rehabilitation versus replacement for essential assets. This balance is critical for enterprises to make informed financial decisions—especially in industries with tight budgets and substantial return expectations like construction in the UK.
8. Deployment and response
Deploy assets strategically based on specific requirements. This dynamic approach supports operational agility. Meanwhile, analyzing asset failure causes will contribute to more robust response planning, saving time and resources in the long term.
9. Establish an asset annuity
Consider creating an asset annuity dedicated to funding repairs, replacements, and rehabilitations. This fund will act as a financial safety net, ensuring that asset management initiatives remain sustainable and adequately financed.
EAM systems vs. CMMS solutions for asset lifecycle management
When it comes to asset lifecycle management, a connected CMMS like Facilio offers distinct advantages over a standalone EAM system. The case study of Al Fajer serves as a compelling testament to this.
Al Fajer faced inefficiencies with high operational costs and frequent equipment downtimes while using traditional asset management methods, which failed to provide real-time insights. By integrating Facilio's CMMS, Al Fajer seamlessly embedded advanced monitoring within their existing infrastructure.
This integration minimized manual data entry, allowing Al Fajer continuous real-time access to asset conditions. The predictive analytics capability empowered them to foresee maintenance requirements, thus enhancing decision-making processes. Also, Al Fajer experienced a substantial reduction in maintenance costs and improved operational efficiency. The automated maintenance tasks further decreased downtime and bolstered productivity.
On the contrary, a standalone EAM system might lack these dynamic real-time capabilities and flexibility. It can often result in isolated data silos and reduced efficiency compared to an integrated CMMS.
Therefore, as observed, leveraging a connected CMMS provides comprehensive tools for streamlined and proactive asset management, effectively extending asset lifespans and optimizing overall performance.
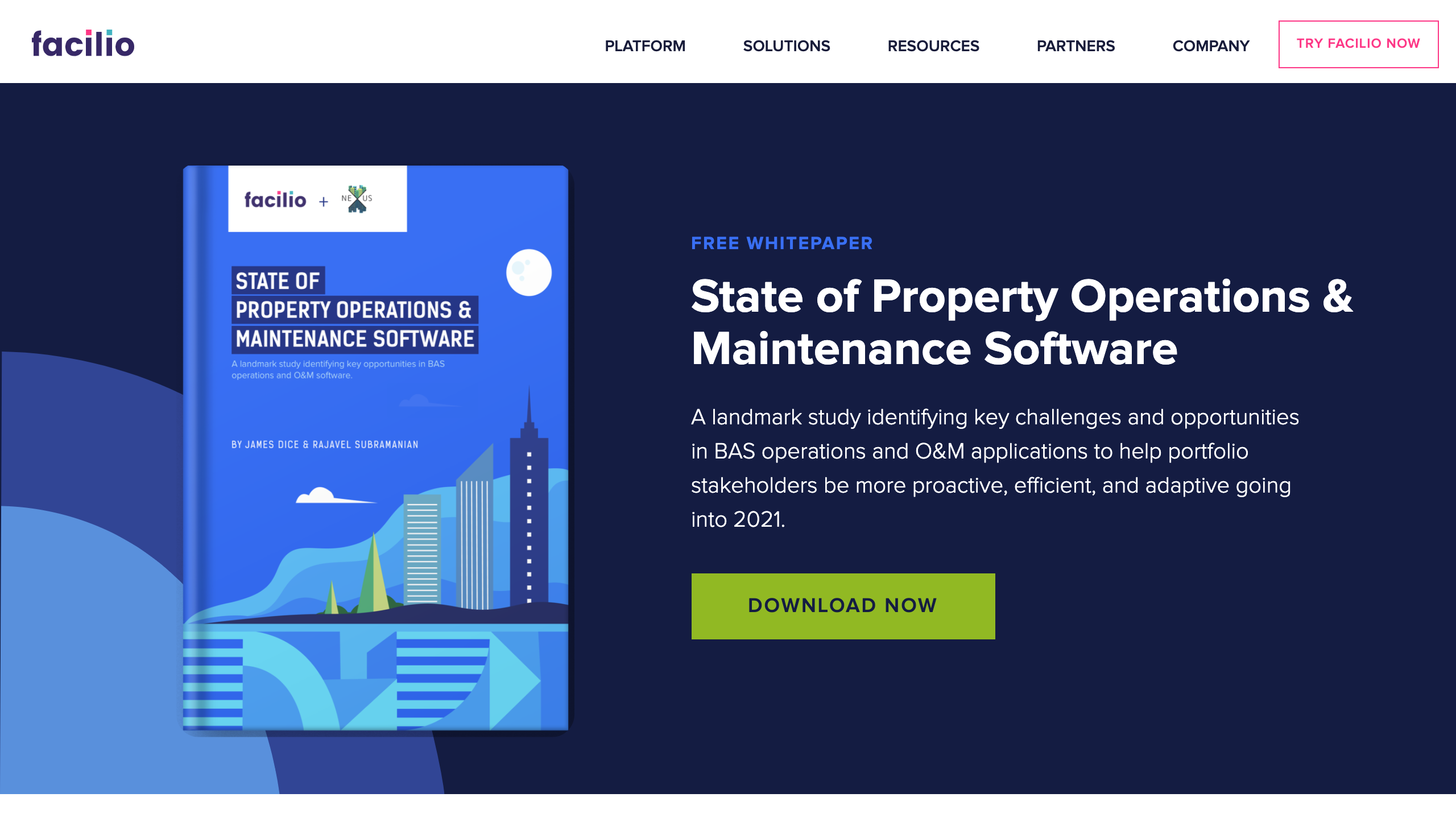
Enhancing performance and extending lifespan with Facilio
Facilio offers a comprehensive Connected CMMS platform that is transforming how businesses manage the full lifecycle of their assets. By leveraging unique value propositions, Facilio not only enhances asset performance but also extends their lifespan. Listed below are the critical features that exemplify Facilio's effective asset lifecycle management capabilities:
- Asset visualization: Gain a clear view of your entire asset portfolio through an interactive dashboard. Monitor asset readings based on various parameters, including static data and dynamic performance metrics, allowing for comprehensive asset condition monitoring.
- Performance optimization: Facilio leverages real-time IoT-driven insights to provide a holistic understanding of asset health and energy consumption. This empowers data-driven decisions to optimize asset performance and maximize efficiency.
- Renewals, audits, and compliance: Automate tasks like audit approvals and compliance work orders to ensure timely replacements and renewals, minimizing risk. This streamlines processes and reduces administrative burdens.
- Conditional alarms and fault detection: Move beyond reactive maintenance. Facilio's system generates conditional alarms based on pre-defined parameters, allowing for early detection of potential problems and enabling proactive intervention.
- Root cause analysis: Empower your team to identify the root cause of asset issues, addressing underlying problems to prevent recurrence. This proactive approach contributes to improved asset reliability and performance.
British Land’s asset management transformation with Facilio
British Land, a leading UK-based property development and investment company, experienced the transformative power of a connected approach in maintaining and optimizing their property assets. With the challenge of managing a vast portfolio of over £14.1 billion in assets under management that required seamless operation across diverse sites, British Land turned to Facilio's CMMS.
Data integration and centralization
The initiative began with a targeted effort to integrate data-driven insights into their asset management framework. By implementing Facilio, British Land was able to centralize their vast array of onsite and back-office data into a single, easily accessible solution. This transition not only streamlined operations but also provided real-time visibility into asset performance.
Predictive maintenance success
British Land utilized Facilio's IoT-enabled platform to monitor critical asset metrics continuously, thus enabling proactive interventions well before potential issues arose. This predictive capability led to a notable reduction in maintenance costs while extending the lifespan of their assets and increasing the return on investment.
Strategic planning and informed decision-making
Facilio’s centralized dashboard provided British Land's management team with a comprehensive overview of assets, promoting informed decision-making. This capability was particularly advantageous for strategic planning, as it allowed the company to efficiently allocate resources and align maintenance activities with broader business goals.
Enhanced compliance and sustainability
The connected CMMS also improved British Land’s compliance and sustainability efforts. By automating compliance checks and generating detailed reports, British Land not only reduced administrative overhead but also ensured all regulatory standards were met seamlessly.
With the adoption of Facilio, British Land experienced a remarkable 50% reduction in energy consumption year-on-year, showcasing significant improvements in energy efficiency and gaining invaluable real-time insights into energy and occupancy metrics.
Get a 360° view of your assets portfolio
Effective asset lifecycle management can transform EAM from a routine function into a crucial pillar of business strategy. It enables predictive maintenance, which can anticipate issues before they occur, reducing costly downtimes.
British Land's partnership with Facilio exemplifies how leveraging advanced asset lifecycle management technologies can drive operational efficiency, cost savings, and strategic growth. Integrating smart technologies such as IoT, CMMS platforms now enable real-time monitoring of asset conditions and performance, presenting you with the opportunity to make informed decisions swiftly and accurately.
Facilio stands out by providing a comprehensive asset lifecycle management solution that helps businesses reduce downtime, increase reliability, and ensure compliance. By utilizing Facilio's unique capabilities, businesses can transition from traditional maintenance practices to a more proactive and efficient asset management strategy.
If you’re interested in gaining a complete and accurate picture of your assets, schedule a demo and see Facilio’s asset management capabilities in action.
FAQs
What is an asset lifecycle?
An asset lifecycle refers to the series of stages an asset goes through during its lifetime. An asset starts its lifecycle with planning and remains a part of it till disposal. Asset lifecycle management helps businesses track asset replacement and ensure asset reliability.
Why is asset lifecycle management important?
Asset lifecycle management minimizes downtime, reduces maintenance costs, and ensures compliance with regulatory standards by providing a structured approach to maintaining and managing assets.
What are the stages of asset lifecycle management?
The stages include planning, acquisition, operation & maintenance, and disposal. Each stage focuses on different activities to maintain and optimize asset performance.
How can technology improve asset lifecycle management?
Technology can improve asset lifecycle management by providing real-time monitoring and data-driven insights into asset performance, enabling predictive maintenance to prevent costly downtime and repairs. Additionally, automation streamlines processes, reducing human error and ensuring compliance with regulatory standards.