Maintenance KPIs play a crucial role in helping facility management teams monitor equipment reliability, operational efficiency, and maintenance costs.
These KPIs provide maintenance leaders with the data they need to reduce downtime, optimize resources, and improve overall performance.
While common metrics like MTTR and MTBF remain important, many organisations are now using advanced KPIs to set more precise benchmarks and develop smarter maintenance strategies.
In this guide, you will find the most important maintenance KPIs, practical calculation methods, and expert advice to help you improve your maintenance program and achieve better results.
What is a Maintenance KPI?
These KPIs track team and asset performance, giving facility managers the actionable insights they need to reduce downtime, control costs, and increase asset lifespans.
Maintenance KPIs vary from organisations with respect to priorities and guide continuous improvement toward higher reliability and productivity.
Maintenance Metrics vs. KPIs
Not all maintenance data are KPIs.
Metrics measure specific activities (like work orders completed), while KPIs tie those measurements to broader business goals - such as maximising availability or reducing breakdowns.
For instance, "number of preventive tasks" is a metric, but "PM Compliance Rate" is a KPI because it indicates progress toward preventive maintenance targets. Focusing on actionable KPIs, rather than just collecting metrics, helps teams prioritize what truly drives operational success.
Important Examples of Maintenance KPI Metrics to Benchmark and Track
Effective maintenance management isn't guesswork—it's data-driven. Here are the most powerful KPIs modern FM teams should monitor:
1. Maintenance Backlog
Definition: Maintenance backlog is the total number of outstanding maintenance tasks that have not yet been completed.
For example, if there are 100 outstanding maintenance tasks and 90 of them have been completed, the maintenance backlog would be 10 tasks ((100 - 90) = 10).
- Benefits: Helps prioritize and manage outstanding maintenance tasks, preventing costly failures and ensuring resources are effectively allocated.
- Importance: Critical for operational reliability by tracking pending work and avoiding unplanned downtime due to neglected tasks.
- Shortcomings: Excessive backlog indicates capacity issues or poor scheduling, potentially leading to reactive firefighting and decreased productivity.
2. Overall Equipment Effectiveness (OEE)
Definition: Overall Equipment Effectiveness (OEE) measures how well a piece of equipment is being utilized.
For example, if a piece of equipment has an availability of 90%, a performance efficiency of 95%, and a quality rate of 98%, its OEE would be (90 x 95 x 98) / 100 = 84.1%.
- Benefits: Provides a comprehensive view of equipment utilization, highlighting losses due to downtime, speed, and quality issues, enabling targeted improvements.
- Importance: Helps identify bottlenecks and measure the real performance of assets compared to industry benchmarks (world-class >85%).
- Shortcomings: Can be complex to calculate accurately and may not consider external factors like demand fluctuations or supply chain issues.
3. PM (Planned Maintenance) Compliance
Definition: Planned maintenance compliance is the percentage of planned maintenance tasks that are completed on time.
For example, if there were 100 planned maintenance tasks and 90 of them were completed on time, the planned maintenance compliance would be 90% ((90 / 100) = 90%).
- Benefits: Ensures preventive maintenance tasks are completed on schedule, reducing emergency repairs and extending asset life.
- Importance: High compliance rates directly correlate with fewer breakdowns and more predictable maintenance planning.
- Shortcomings: Does not account for the quality or effectiveness of maintenance work, only task completion timing.
4. Planned Maintenance Percentage
Definition: Planned Maintenance Percentage (PMP) is a metric that measures the proportion of maintenance work that is planned in advance versus the total maintenance work performed
- Benefits: Indicates the proportion of maintenance efforts spent on planned activities, which correlates with a controlled and proactive maintenance strategy.
- Importance: A higher percentage suggests reduced reactive work and better resource management.
- Shortcomings: May overlook the impact of urgent unplanned repairs and the actual condition of assets being maintained.
5. Mean Time To Repair (MTTR)
Definition: MTTR is the average time it takes to repair failed equipment.
For example, if it took a total of 10 hours to repair 3 failed pieces of equipment, the MTTR would be 3.33 hours.
- Benefits: Measures repair efficiency and helps identify delays in restoring equipment, aiding resource allocation and process improvements.
- Importance: Lower MTTR reduces downtime, minimizing production losses and improving operational continuity.
- Shortcomings: Does not address root causes of failures; quick repairs may mask recurring problems requiring deeper solutions.
- Action step: Track MTTR to spot bottlenecks and streamline repair procedures.
6. Mean Time Between Failures (MTBF)
- Definition: MTBF is the average time that passes between failures of a particular piece of equipment.
For example, if a piece of equipment has been operating for 100 hours and has experienced 3 failures during that time, its MTBF would be 33.33 hours.
- Benefits: Tracks equipment reliability by measuring average operating time between failures, guiding maintenance and design improvements.
- Importance: Higher MTBF indicates better asset performance and less frequent breakdowns, reducing maintenance costs.
- Shortcomings: Relies on statistical averages and assumes failure randomness, which may not reflect actual usage conditions or failure patterns.
- Goal: A rising MTBF signals improved reliability.
Let's take a look at some more maintenance management KPIs.
Leading, Modern Maintenance KPI Metrics
Expand your KPI dashboard for deeper insights and future-ready maintenance operations:
- Reactive Maintenance Percentage
Measures the share of urgent, unplanned maintenance relative to all tasks, indicating reliance on emergency repairs. A high percentage suggests the need for stronger preventive maintenance to reduce downtime and costs. - Schedule Compliance
Tracks how consistently maintenance tasks are completed according to the planned schedule, reflecting maintenance discipline and reliability. High compliance supports smoother operations and fewer unexpected asset failures. - Remaining Asset Value (RAV)
Assesses the current value of assets compared to their original cost, providing insight into asset depreciation and replacement timing. Maintaining high RAV helps optimize investment decisions and manage long-term capital expenditures. - Standard Maintenance Cost per Unit (SMCP)
Measures maintenance spending per asset or production unit, allowing cost efficiency evaluation across different assets or processes. Controlling SMCP helps identify opportunities to reduce maintenance costs without sacrificing quality.
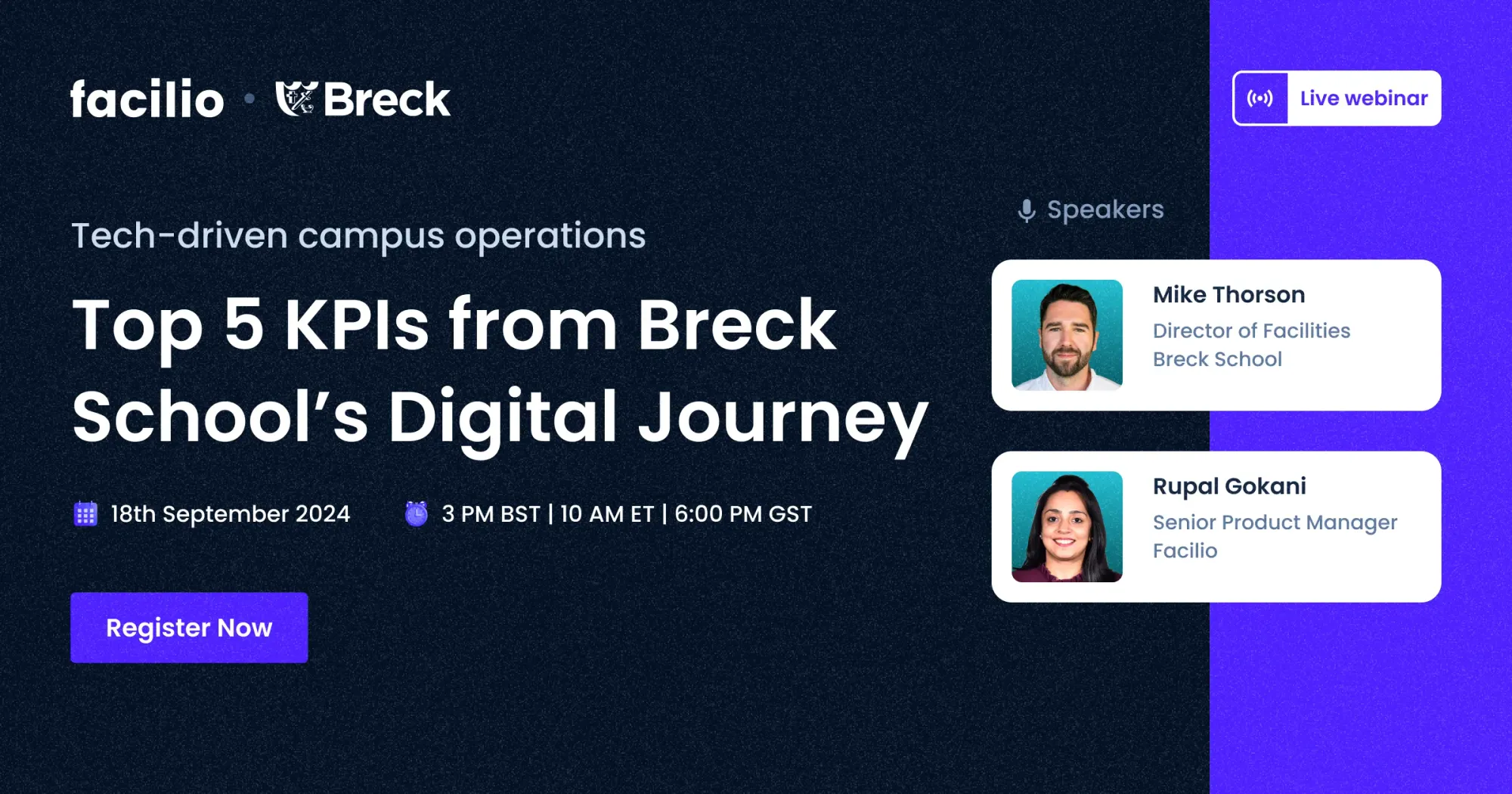
- Work Order Completion Rate
Represents the percentage of maintenance work orders completed within a specified time frame, indicating team productivity and process effectiveness. A high completion rate correlates with improved asset availability and maintenance responsiveness. - Maintenance Technician Productivity
Tracks the amount of work completed by each technician over a given period, helping to assess workforce efficiency. Optimizing technician productivity ensures better resource utilization and quicker response to maintenance needs. - Spare Parts Turnover Ratio
Measures how frequently spare parts inventory is used and replenished, reflecting inventory management efficiency. A balanced turnover ratio prevents stockouts and excess inventory, reducing holding costs. - Equipment Downtime
Totals the hours equipment is non-operational due to maintenance or failure, directly impacting productivity and costs. Minimizing downtime is crucial for maintaining operational continuity and meeting production targets. - Asset Utilisation
Indicates the proportion of time assets are actively used for productive work versus idle time, measuring operational efficiency. Higher utilization means better return on investment but must be balanced to avoid overuse and premature wear. - First Pass Yield (FPY)
Shows the percentage of repairs or maintenance tasks completed correctly the first time without rework, reflecting quality and effectiveness. High FPY reduces waste, lowers costs, and improves equipment reliability.
Develop Maintenance KPIs with SMART Goals
Set your maintenance KPIs the SMART way:
- Specific: Focus on clear, defined outcomes (e.g., "Reduce equipment downtime").
- Measurable: Use precise numbers or percentages.
- Achievable: Set realistic targets given current resources.
- Relevant: Align KPIs with your organisation’s priorities.
- Time-bound: Establish deadlines to keep teams accountable.
Regularly review, update, and communicate KPI goals across the organisation for maximum engagement and alignment.
How to Track Key Maintenance Metrics Automatically with Facilio
Manual reporting is a thing of the past. Facilio’s state-of-the-art CMMS enables facility teams to:
- Automatically capture maintenance activity and KPI data in real-time.
- Visualise trends and outliers with powerful dashboards.
- Generate on-demand custom reports for audits and compliance.
- Identify at-risk assets and proactively schedule interventions.
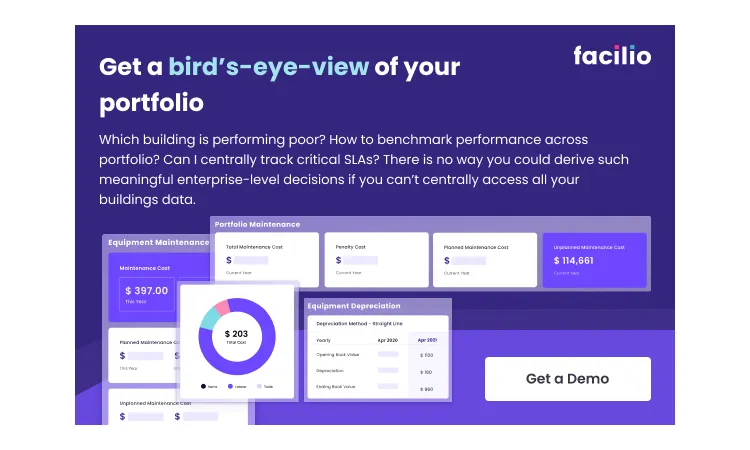
By using automated KPI tracking, FM leaders can make confident decisions, preempt breakdowns, and achieve next-level maintenance outcomes, consistently.
Ready to optimise your maintenance strategy? Start tracking the right KPIs and experience a new era of reliability, efficiency, and ROI.