Building Operations & Maintenance
How To Wield Simplified FDD To Fix Building Anomalies In Real-time?
Today, as pressurized Facilities Managers rummage through software tools to predict building performance and plan operations better, they harbor mixed thoughts.
It’s a constant conflict between “Can I?” and “I’ll seek the vendor’s help”. A classic example – FDD. Predominantly a cumbersome package that’s quintessential FM software, its descent to a simplified interface that’s equally easy to control is still behind a veil.
Truly superior FDD engines roll out intuitive process flows to achieve portfolio-wide fault diagnostics. To top it, they seamlessly integrate with routine FM activities.
Sounds like a far cry from the usual BMS-dependant FDD system? Absolutely yes! Let’s elaborate.
Walk past the potholes of conventional FDD
Traditional BMS-dependent FDD systems have not been able to apply diagnostics to many different building profiles, systems, and types of equipment across a portfolio.
They encompass limitations like:
- Rigid alarm configuration process – tedious to replicate across buildings.
- Limited alarm rules, sometimes pre-defined.
- Raw fault data with limited to no insights – not actionable.
- Inability to couple FDD to systems other than HVAC, like lighting, elevator, security, etc.
The modern Facility Manager is desperate to break the mould and look outside the building(if not a box!) into its entire expanse.
Need of the hour- A solution that dissolves the complexity that is so FDD-typical and offers an end user-oriented design.
That’s the impetus Facilio needed to craft an FDD capability with a refreshing approach, way beyond mere inflexible service.
From a single centralized platform to view the entire portfolio’s performance to real-time response to faults, here’s an automated system that redefines and simplifies the FDD – Building relationship!
So, how do you blend this capability with your building workflow and revolutionize its performance?
5 ways Automated FDD can put your building on a high-performance track
1. Earn back your time and effort with precise root cause insight
You can now configure alarms with drill-down root-cause analysis. Conjectures or time-consuming trial-and-error methods are bygone ways of defect diagnosis.
Let’s say, an alarm for FAHU overcooling goes off; there could be a bunch of underlying reasons for this.
With an effective root cause engine, you can accurately figure out if, for example, the cooling coil valve leak was at fault in one particular instance.
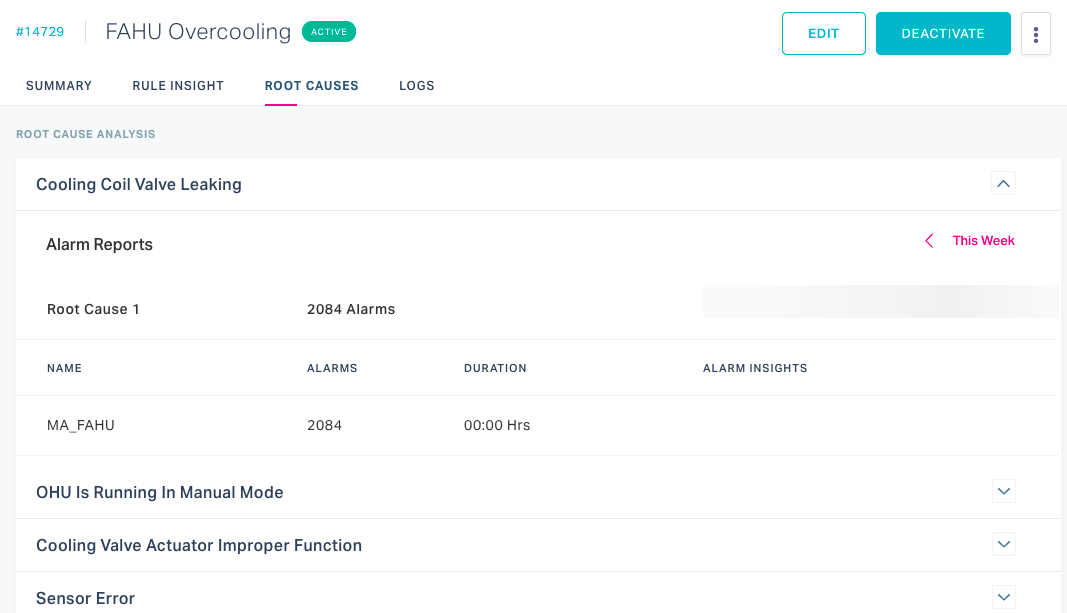
So the next time an alarm fires, you can focus on execution of resolution, rather than hunting for the origin of fault.
2. Seamlessly configure automated resolution
Does your BMS engineer call up a technician to give out work instructions to clear a new alarm? Or do you wait for your 3rd party ticketing system to receive the alarm and then raise a work order? One critical alarm goes up and it’s like a time-bomb ticking off!
A pre-designed sequence of action items that will kick off the moment fault occurs is like attacking the tiger the instant it pounces on you. Delay increases risk!
i) Automate Work order as response to an anomaly.
For example, you can create a work order and map it to a Chiller action, say, chiller’s differential temperature(Delta T) dropping below 5 degrees celsius.
So the next time this alarm triggers, the work order will be automatically assigned to the designated team with priority details.
You can keep abreast of real-time updates to alarm response activities, and even define SLAs on them!
ii) Send controls to automate setpoint changes
Now you can update the field values of the system automatically using rules that aid in saving energy.
Suppose an alarm for abnormal chiller water supply air temperature sets off, you can automate the change of temperature to a specific value.
That’s some pro-level preparedness for an eventuality!
3. Monitor cost impact due to energy inefficiency
The monetary impact of an asset’s downtime is now definable. This helps to drive urgency for technicians, and also calculate the exact cost an anomaly begets.
For example, you can associate a cost with every unit of energy that’s lost. So when the diagnostics tracks an energy loss of 100 units(say, .44 USD per energy unit), the equivalent cost incurred is recorded.
4. Effortlessly set up alarms and derive intelligent interpretation of faults
Now, you can easily create simple to complex alarm rules, be it a simple ON or OFF, or complex ones like equipment short cycling.
Like the below sample alarm for FCU Valve leakage which is based on a complex relation between various parameters-
You may even pick one from the bunch of powerful plug-and-play alarm templates.
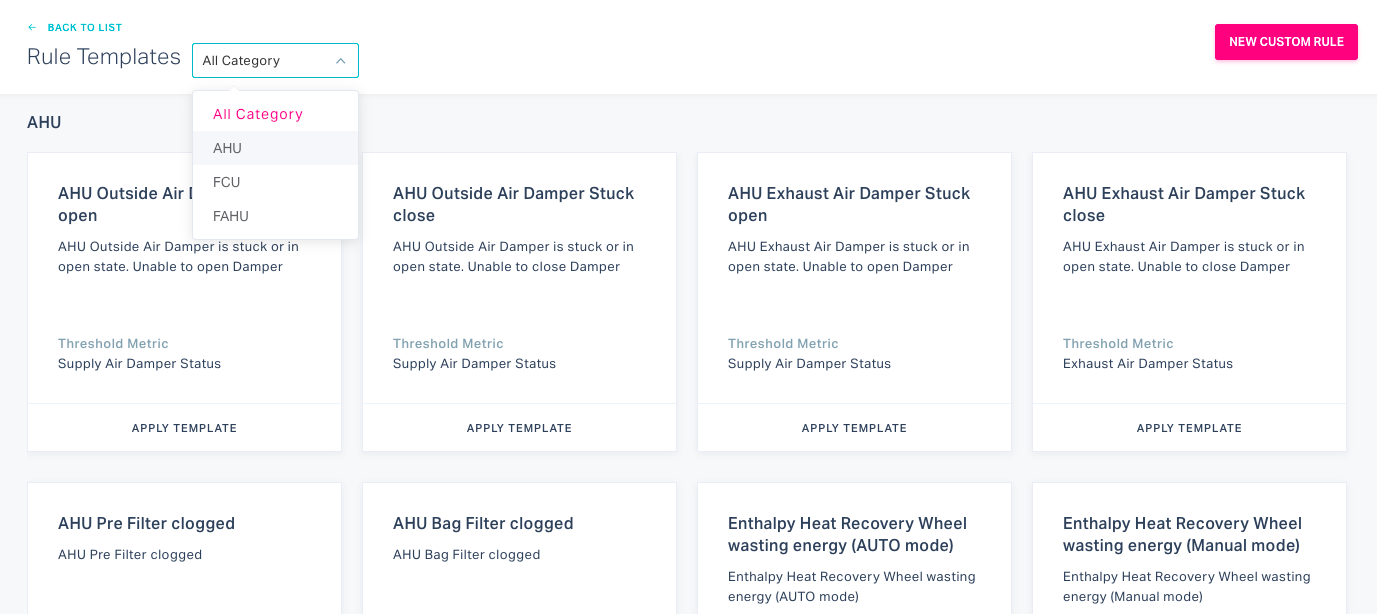
A diverse FDD rule library that allows easy customization means alarm configuration across a portfolio is a breeze.
That clears level-1. What about the next level where you are swarmed by hundreds of alarms, only to discover later that few were false and most were redundant?
Good news! A centralized FDD engine can smartly combine multiple rules, correlate alarms to exact active issues, and discard false positives; so your alarm list summarises only the unique issues.
5. Benchmark equipment performance across buildings
A central unified portfolio-wide view of alerts means you can compare the performance of HVAC or any other equipment category across vendors.
Similarly, you can also benchmark building performance against one another, in terms of any parameter of your choice.
With easy access to maintenance metrics like Mean time between failures(MTBF), Mean time to trigger(MTTR), Mean time to clear(MTTC), Downtime, Average Response time and Resolution time, and more.
You can straightaway tend asset units that need care(Sufficient data to dissect a few AMC contracts, you think?).
Proactive management of your enterprise gets a facelift, thanks to Automated FDD. It is no longer a standalone tech ‘super feature’, but an FM-compatible foreteller you can readily integrate into your operational workflow.
Real-time and centralized nature of FDD eliminates oversight of minor flaws that snowballs into major unplanned maintenance costs.
What’s more, you can concurrently optimize the lifespan of assets at a portfolio level.
Sounds like an apt Fitbit for your building health?