In recent decades, an evolution in CMMS (Computerized Maintenance Management Software) has introduced data-driven maintenance capabilities, in commercial real estate operations. CMMS, which was once looked at merely as centralized software to optimize maintenance management, is now on the verge of major tech-driven advances. One could go so far as to say that, when optimally utilized, next-gen CMMS will define the future of property operations and the facility management industry.
In May 2021, Tony Callis, Sales Director (Americas), Facilio, sat down with Jonathan Thomas and Doug Litwiller, from Building Maintenance Optimization Consultants, Inc. (BMOC), as part of an episode in our webinar series. The interaction focused on the power of leveraging contemporary CMMS technology, and the importance of data, in the evolving digital world of building maintenance and operations.
In this blog, we'll dive into some of the key takeaways from the webinar, including some of the challenges and the possibilities that a data-driven approach will enable, to help take building maintenance to the next level in efficiency and impact.
Contemporary CMMS is held back by a lack of interoperability
Tony initiated the discussion by listing the problems that limit existing CMMS. He drew attention to the fact that building owners, and end-users, have been restricted in their options, by using a single software for multiple purposes. He pointed out that such software is designed for use by particular personnel in a building, and not to address the full spectrum of challenges that the maintenance function has to deal with. In effect, these ‘solutions’ add to workloads, instead of reducing the effort required.
In light of these limitations, industry experts have been consistently asking for a streamlined CMMS. The issues are further complicated by the fact that, in the past, two-way communication between equipment systems and CMMS has been virtually non-existent.
Jonathan categorized the major gaps in contemporary CMMS solutions as follows:
- Service and collaboration gaps, between the users of CMMS and the vendors they rely on
- A particularly huge gap that is evident in the area of the new construction, while deploying and maintaining CMMS to enhance operations
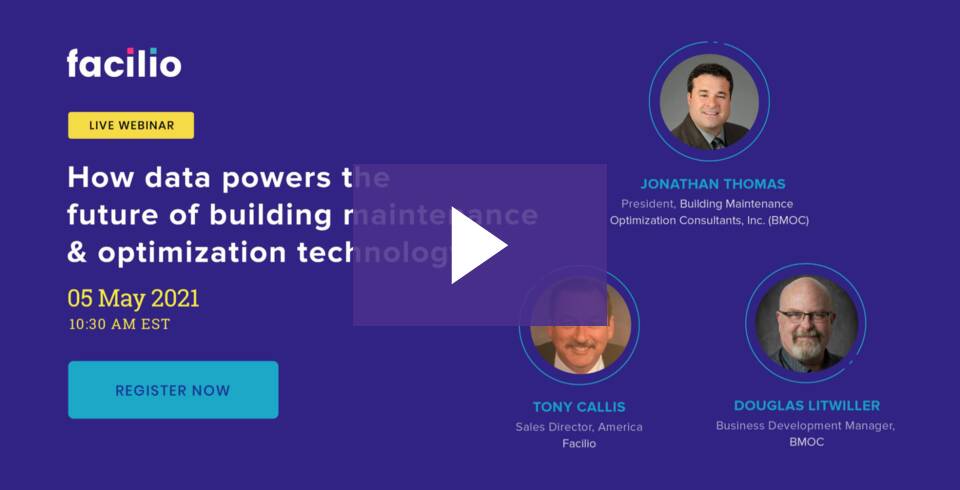
The panelists agreed that continuing issues of inflexibility and rigid structure – in the legacy CMMS solutions deployed in buildings – are phenomenal. However, the three experts also came to the consensus that it is almost impossible to abandon these solutions completely. So what options exist? One way for the industry to adapt is to leverage contemporary CMMS to integrate with existing automation management solutions like FDD (Fault detection & diagnostics) and EMS/EMIS (Energy management systems).
The panel agreed that discontinuity in legacy CMMS has created immense opportunities for growth and development in building operations and maintenance software.
Adapting CMMS, in line with modern enterprise technology
The future of CMMS is proactive and predictive. And with such exponentially widening expectations on the results that CMMS needs to deliver, building maintenance has been shifting towards fault forecasting and solutioning. These necessities are driving rapid innovation in CMMS, across an array of applications, aimed at making it more efficient.
Jonathan recalled his experience with legacy CMMS, sharing his opinion that it needs to be updated with the ability to integrate with modern systems like Building Automation, FDD, Capital Planning, Energy Management, and Asset Maintenance. Jonathan stressed that this significant challenge can only be addressed by enhancing connectivity among systems, as the means to obtain and utilize real-time performance data.
The panelists were unanimous in their belief that the integration of new systems with the current CMMS should be fast-paced and collaborative. This emerging approach needs to position CMMS as the central nervous system of communication, for all the individual applications and systems.
Currently, the FM industry uses CMMS for maintenance management; but the panel was in agreement that a shift to optimizing overall operational performance, using a data-led unified modern CMMS, is the future.
Unilever was one of the earliest companies, globally, to adopt modern CMMS technology, after trying out multiple asset management software. C-suite management to floor level factory workers benefited from intuitively designed CMMS, and the way it facilitated the creation of work orders; storing and accessing data; and generating alerts. The decision to deploy the technology freed thousands of employees from repetitive and cumbersome tasks, in the day-to-day processes that are part of building maintenance and operations.
A Modern Unified O&M platform is the solution
Data is the cornerstone of any structured building operations software. So how can this precious resource – which is currently already being generated by building portfolios, but lying soiled and under-utilized – be leveraged to empower legacy CMMS? The obvious answer is to bring the entire asset under the purview of CMMS, for it to function seamlessly, and extract maximum value for operations.
One major roadblock to such a comprehensive, and data-enriched, model of CMMS is that larger commercial real estate organizations, with multiple stakeholders and assets, have difficulty in driving effective discussion and collaboration between entities. In essence, such organizations are operating in a fragmented fashion, with no consistency in the data being used by diverse teams, decision-makers, and automation.
CMMS can benefit an organization, and unlock its potential to be data-driven, when insights across building conditions, performance, and asset value proposition, is accessible; across the entire portfolio, and every asset category.
If you do not use your CMMS to completely document your data, it is not valuable- Doug
According to Jonathan, the top advantages that clients will experience, by implementing a comprehensively data-driven CMMS are:
- Ease of access to data history of reports, performance, records, and manuals
- Enhanced and accurate training, that leverages collective data
- Drastic improvement in intra-organizational communication, with the entire team gaining granular visibility into data
- Enhanced reliability, because of easily accessible data
- Of course, these advantages also make the strongest case for preferring cloud-based CMMS, over on-premises CMMS
The panel pushed for a focus on innovations that result in robust, scalable, and responsive attributes. The key, according to the three experts, was to enhance current CMMS, by leveraging technology to capture real-time information. And, by common consensus, implementing a centralized data-driven platform was the means the panel agreed on, to enable an optimally efficient CMMS.
On an interesting note, Facilio launched an online poll for the audience, at the beginning of the webinar. Respondents were asked to choose the option that most limits the efficiency of current CMMS, and needs an upgrade. The results are shared below:
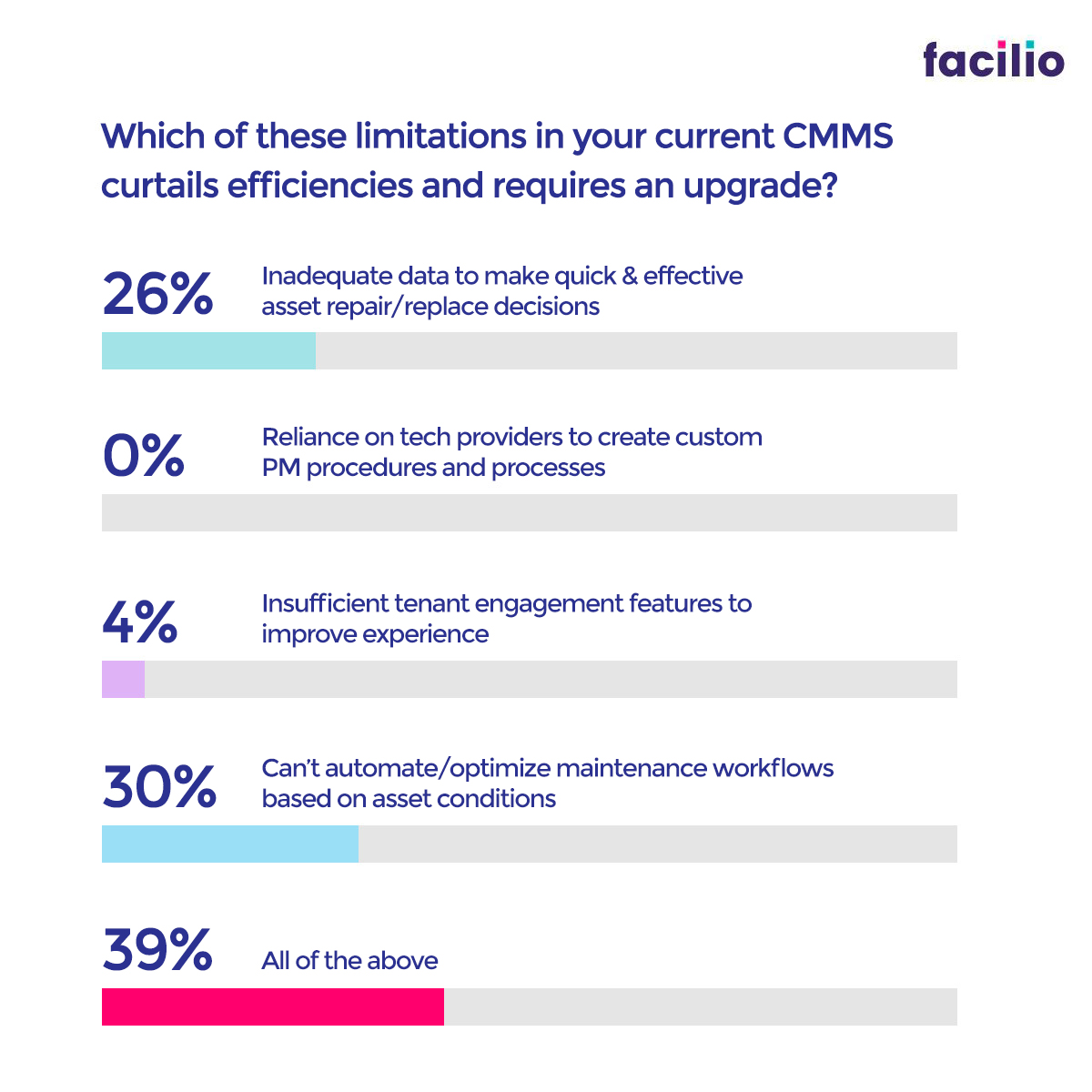
39% of the respondents – the highest number for any of the choices – selected ‘All of the Above’ from the poll options. This, somewhat limited, sample was an indicative snapshot of the front-end and back-end issues faced by the FM industry with the current CMMS.
System scale solutions, like CMMS, need access to rich, real-time data, to be truly effective
All three panelists agreed that CMMS is the primary tool for building operations & maintenance. But they were equally on the same page, in the assertion that its greatest potential will only be unlocked when the data is shared and normalized among all the stakeholders involved.
Several Industry 4.0 use cases have made it evident that adopting IoT + CMMS integrations can have a dramatic and transformational effect, for improved maintenance efficiency across industries. For the commercial real estate industry to achieve these same optimal results, implementing the data-driven and seamlessly connected model of CMMS will be the key enabler.
Want your CMMS to be cost-effective and reduce downtime? Then it is time you consider a changeover in your building maintenance and operations technology strategy.
For insights on CMMS and the technical side of maintenance operations, from our distinguished panel of industry experts, you can listen to the webinar featured in this blog, here.